When Did Nissan Open Us Assembly Plants
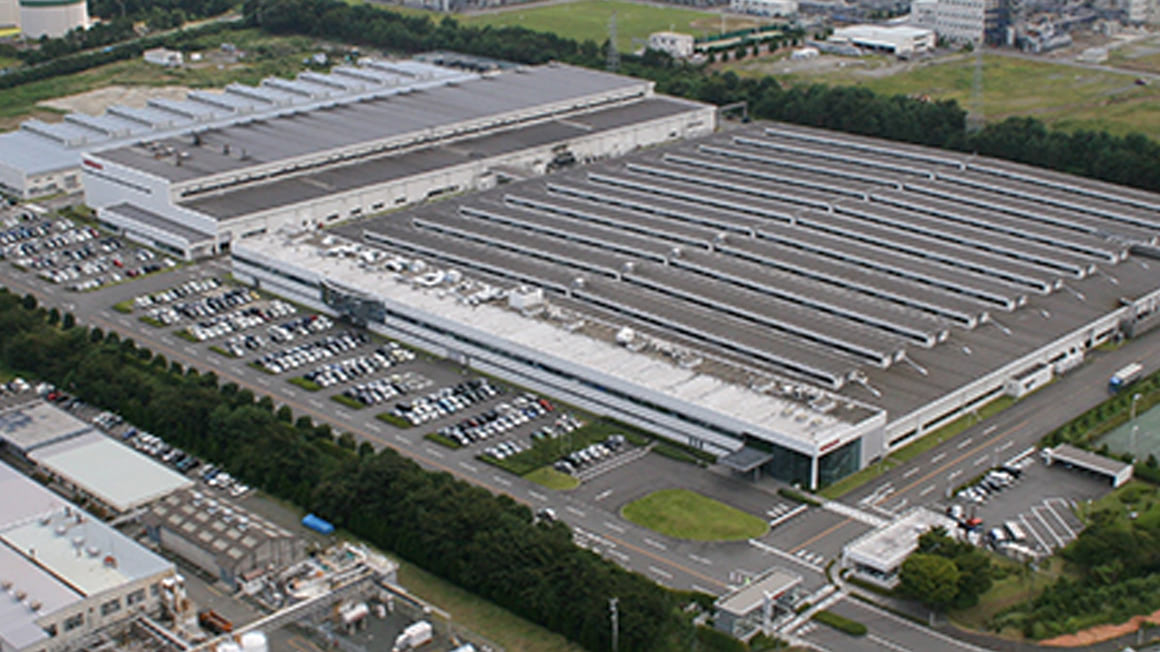
For Nissan enthusiasts in the US, a key piece of the puzzle is understanding where those beloved cars and trucks were actually assembled. While Nissan's roots are firmly in Japan, their commitment to the American market led to the establishment of US-based assembly plants. Knowing when these plants opened, what models they produced, and even the specific manufacturing processes used gives you, the dedicated DIYer or modifier, a deeper appreciation for your vehicle. It can also provide valuable clues when diagnosing issues or sourcing parts.
A Brief History: Nissan's Expansion into the US Market
Before diving into the specifics of the US assembly plants, a quick recap of Nissan's US market entry is helpful. Initially, Nissan vehicles were imported and sold under the Datsun brand. The shift to the Nissan brand, combined with increasing market share, spurred the need for local production to reduce import costs and respond more quickly to local demand.
The Smyrna, Tennessee Pioneer: 1983
The watershed moment was the opening of the Smyrna, Tennessee plant in 1983. This was Nissan's first major foray into US vehicle manufacturing. While several Japanese manufacturers had assembly facilities in the US before, Nissan's Smyrna plant was a major commitment and represented a significant investment.
This plant wasn't just an assembly line; it was a full-fledged manufacturing complex encompassing stamping, welding, painting, and final assembly. This vertical integration meant that Nissan had significant control over the entire production process. The initial focus was on the Datsun/Nissan pickup truck (later the Nissan Truck) and the Sentra, both popular models at the time.
How Smyrna Operates: A Glimpse Inside the Assembly Line
Let's break down a simplified version of the assembly process. The process involves many stages which include Stamping, Body Assembly (Welding), Painting, Trim, Chassis and Final Assembly.
- Stamping: Large metal sheets are fed into massive presses, creating the body panels. These presses can exert thousands of tons of force to shape the steel with incredible precision.
- Body Assembly (Welding): Robots play a crucial role in welding the stamped panels together to form the vehicle's body shell (also referred to as the body-in-white or BIW). Automated welding ensures consistent and high-quality welds. Spot welding is the most common technique here, where two pieces of metal are joined by applying pressure and electric current to create a localized weld. Laser welding is also used in some areas for tighter, more precise seams.
- Painting: The BIW goes through an elaborate painting process to protect it from corrosion and give it its color. This includes cleaning, applying primer, multiple coats of paint, and a clear coat. Electrodeposition, or e-coating, is a common process used to apply the primer coat. This involves submerging the body in a conductive paint bath and applying an electrical charge, which causes the paint to deposit evenly onto the metal surface.
- Trim: This stage involves installing interior components, such as the dashboard, seats, carpets, and headliner. Wiring harnesses are also routed and connected.
- Chassis: Simultaneously, the chassis is being assembled. This involves installing the engine, transmission, suspension, brakes, and wheels. The engine is typically mounted on a subframe, which is then bolted to the chassis.
- Final Assembly: The body and chassis are joined together. This is a critical step where all the electrical and mechanical connections are completed. Quality checks are performed throughout the entire process, but final assembly includes a rigorous inspection to ensure everything is functioning correctly. The vehicle undergoes a road test to check for any performance issues.
The Canton, Mississippi Expansion: 2003
Nissan expanded its US manufacturing footprint with the opening of a second assembly plant in Canton, Mississippi in 2003. This plant was designed to produce a wider range of vehicles, including SUVs and full-size trucks. Models like the Titan, Armada, Altima, Frontier, and NV vans have all been produced in Canton.
The Canton plant incorporated advanced manufacturing technologies, including more sophisticated robotics and automation. It also emphasized lean manufacturing principles to minimize waste and improve efficiency.
Canton Operations: Differences and Similarities to Smyrna
While the basic principles of automotive assembly remain the same in both plants, Canton benefited from advancements in technology and manufacturing techniques that weren't available when Smyrna was established. For instance, the Canton plant likely utilizes more advanced robotic welding systems, improved paint application processes (including water-based paints to reduce emissions), and more sophisticated quality control systems.
However, the fundamental processes are similar. Stamping, welding, painting, trim, chassis assembly, and final assembly are all still essential steps in building a vehicle. The key difference lies in the level of automation, precision, and material handling.
Common Issues and Maintenance Concerns Related to US-Assembled Vehicles
While the location of assembly doesn't directly cause specific mechanical issues, it can influence certain aspects of vehicle maintenance and repair. For example:
- Parts Availability: Understanding where your vehicle was assembled can help you source parts. While Nissan parts are generally readily available, knowing the assembly location can be useful when searching for specific components or trim pieces unique to certain production runs.
- Paint Codes: Paint codes can vary slightly depending on the assembly plant and the year of production. Using the correct paint code is crucial for a seamless color match during body repairs.
- Recall Information: Recalls are often specific to certain production dates or VIN ranges. Knowing the assembly plant can help you quickly determine if your vehicle is affected by a particular recall.
- Fit and Finish Variations: Minor variations in fit and finish can sometimes occur between different assembly plants. These variations are usually subtle but can be noticeable to a trained eye.
Common Issues to consider:
- Rust: While not directly related to US assembly, certain climates and road conditions can accelerate rust formation. Regularly inspecting your vehicle for rust, especially in areas prone to corrosion (such as wheel wells and undercarriage), is essential.
- Electrical Issues: Electrical issues can arise from faulty wiring or corroded connectors. Properly maintaining your vehicle's electrical system, including regularly checking battery terminals and grounds, can help prevent these issues.
- Suspension Wear: Suspension components can wear out over time, especially on vehicles driven on rough roads. Regularly inspecting your suspension system for worn bushings, ball joints, and shocks is crucial for maintaining proper handling and ride quality.
Do's and Don'ts / Best Practices for Owners of US-Assembled Nissans
Here are some practical tips for keeping your US-assembled Nissan in top condition:
- Do regularly check your vehicle's fluid levels (oil, coolant, brake fluid, power steering fluid, transmission fluid).
- Do follow the recommended maintenance schedule outlined in your owner's manual.
- Do use genuine Nissan parts or high-quality aftermarket parts when performing repairs.
- Do properly torque all fasteners to the correct specifications. A torque wrench is your friend!
- Do thoroughly inspect your vehicle for rust, especially in areas prone to corrosion.
- Don't ignore warning lights or unusual noises. Address potential problems promptly.
- Don't neglect the electrical system. Keep battery terminals clean and connections tight.
- Don't overload your vehicle beyond its rated capacity.
- Don't use harsh chemicals or abrasive cleaners on your vehicle's paint.
- Do keep detailed records of all maintenance and repairs.
Understanding VIN and assembly locations
Your vehicle identification number, or VIN, carries key information regarding place of manufacture and build date. Look at the first character of the VIN: it tells you where it was manufactured. if it starts with a "1", "4", or "5" it was built in the United States. If it starts with a "J", it was built in Japan.
Conclusion: Appreciating the American-Made Nissan
Nissan's commitment to US manufacturing, starting with the Smyrna plant in 1983 and continuing with the Canton plant in 2003, has had a significant impact on the American automotive landscape. Understanding when and where your Nissan was assembled can provide valuable insights into its production history, potential maintenance considerations, and even its value as a collectible. While the location of assembly doesn't magically imbue a vehicle with superior qualities, it adds another layer to the story of your Nissan. By following the recommended maintenance practices and being mindful of potential issues, you can ensure that your US-assembled Nissan continues to provide reliable and enjoyable service for years to come. Always prioritize preventative maintenance, and don't hesitate to consult a qualified mechanic when needed. Happy wrenching!