When Did Cvt Transmissions Come Out
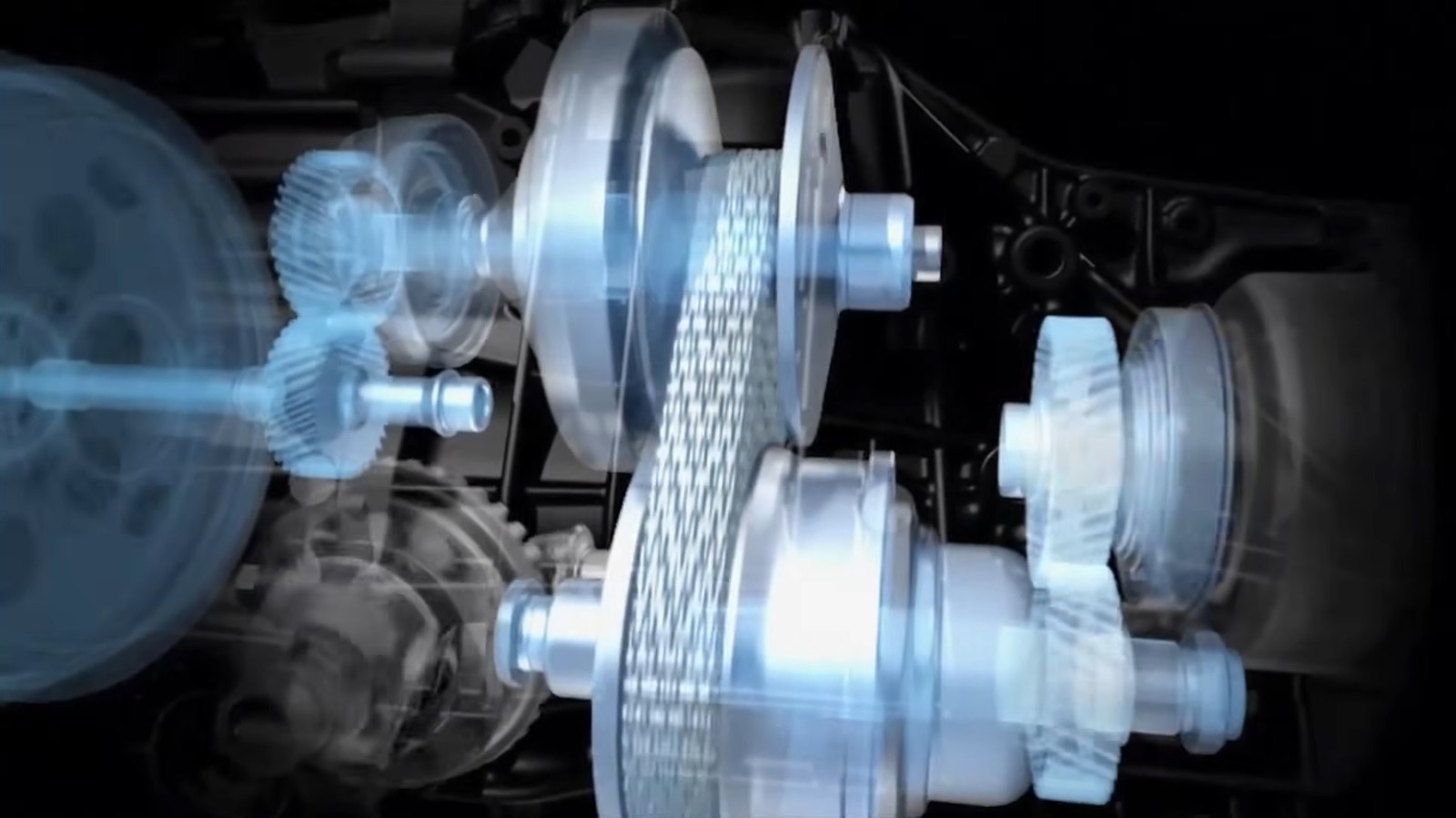
Continuously Variable Transmissions (CVTs) have gained significant traction in the automotive world, offering potential improvements in fuel economy and smoothness compared to traditional automatic transmissions. However, the question of when they first emerged isn't as straightforward as it might seem. While widespread adoption is relatively recent, the core concept has a surprisingly long history. This article delves into the history of CVTs, explaining their operation, common issues, and best practices for maintenance.
Background: A Quest for Efficiency
Before diving into the history of CVTs, it's helpful to understand the motivation behind their development. Traditional automatic transmissions use a set of fixed gear ratios to match the engine's output speed to the vehicle's wheel speed. This means the engine often operates outside its most efficient zone, especially during acceleration or when maintaining a constant speed. The goal of a CVT is to eliminate these fixed ratios and allow the engine to operate at its optimal RPM for any given speed and load.
The dream is a transmission that seamlessly adapts. Think about it: internal combustion engines produce peak power and torque at specific RPM ranges. A traditional transmission forces the engine to jump through gears, often outside this optimal range. A CVT, in theory, allows the engine to stay in that sweet spot, maximizing efficiency and performance.
The CVT Timeline: From Concept to Cars
Early Concepts and Prototypes (1886-1950s)
The earliest conceptual CVT designs date back to Karl Benz in 1886, of Mercedes-Benz fame. He patented a system that used a cone pulley system. This was, of course, in the very infancy of the automobile. While it wasn't particularly practical for production vehicles at the time due to material limitations and other engineering challenges, it demonstrated the core idea of continuously variable ratios.
Throughout the early 20th century, various inventors and engineers experimented with different CVT designs. Notably, several agricultural and industrial applications utilized early CVT implementations. These early CVTs primarily relied on friction drives and were often plagued by issues such as slippage, wear, and limited power handling capabilities. Friction drives use contact and friction between two wheels to transfer power. However, these materials degrade and can cause issues.
The DAF Variomatic (1958)
The first commercially successful CVT for automotive use was the DAF Variomatic, introduced in 1958 in the DAF 600, a small Dutch passenger car. This system used a belt-and-pulley design, a configuration that remains the most common type of CVT today. The Variomatic employed two pulleys connected by a rubber belt. By varying the effective diameter of the pulleys, the transmission ratio could be continuously adjusted. While innovative, the early Variomatic systems were relatively weak and prone to belt failure, especially under high-stress conditions.
Further Development and Refinement (1960s-1990s)
Despite the DAF's pioneering effort, CVTs remained relatively obscure for several decades. Improvements in materials and control systems were needed to make them reliable and robust enough for widespread automotive use. Japanese manufacturers, particularly Subaru and Nissan, began experimenting with and refining CVT technology in the 1980s and 1990s. These companies introduced CVTs in select models, focusing on improving their durability and performance.
Key advancements during this period included the development of stronger belts (moving from rubber to metal-based designs) and more sophisticated electronic control systems. These electronic systems allowed for precise adjustment of the transmission ratio based on factors like engine load, vehicle speed, and driver input.
Modern CVTs: Widespread Adoption (2000s-Present)
The 21st century has witnessed a significant increase in the adoption of CVTs across a wide range of vehicles. This is largely driven by the increasing demand for fuel efficiency and reduced emissions. Modern CVTs are significantly more reliable and efficient than their predecessors. They are also often paired with advanced control algorithms that mimic the behavior of a traditional automatic transmission, mitigating the "rubber band" feel that some drivers find disconcerting.
Technical Breakdown: How a CVT Works
The most common type of CVT uses a belt-and-pulley system. Here's a simplified explanation:
- Two Pulleys: The system has two variable-diameter pulleys, one connected to the engine (the driving pulley) and the other to the wheels (the driven pulley).
- V-Belt: A strong, flexible belt (typically made of steel or a composite material) connects the two pulleys.
- Hydraulic Control: Hydraulic cylinders control the effective diameter of each pulley. As one pulley's diameter increases, the other's decreases, and vice versa.
- Ratio Adjustment: By continuously adjusting the pulley diameters, the CVT can provide an infinite number of gear ratios within a specific range. This allows the engine to operate at its optimal RPM, regardless of vehicle speed.
The Transmission Control Module (TCM) is the brain of the CVT system. It monitors various sensors, including engine speed, throttle position, vehicle speed, and driver input, to determine the optimal transmission ratio. The TCM then sends signals to the hydraulic control system to adjust the pulley diameters accordingly.
Common Issues and Maintenance Concerns
While modern CVTs are more reliable than their early counterparts, they are not without their potential issues:
- Belt Slippage: Excessive wear or contamination of the belt can lead to slippage, resulting in reduced performance and potential damage to the transmission.
- Pulley Wear: The pulleys themselves can wear over time, especially if the CVT is subjected to high loads or improper maintenance.
- Fluid Degradation: CVT fluid is crucial for lubricating the internal components and maintaining proper belt grip. Using the wrong type of fluid or failing to change it regularly can lead to premature wear and failure.
- "Rubber Band" Effect: Some drivers dislike the feeling of constant engine RPM during acceleration, which is characteristic of CVTs. This can feel like the engine is revving without a corresponding increase in speed.
- Overheating: CVTs can overheat under strenuous conditions, especially when towing or driving in hot climates. This can damage the internal components and shorten the transmission's lifespan.
Maintenance is key to extending the life of a CVT. Regular fluid changes, using the correct type of fluid (specified by the manufacturer), are essential. It's also important to avoid subjecting the CVT to excessive stress, such as frequent hard acceleration or towing heavy loads. Listen for any unusual noises or vibrations, which could indicate a problem.
Do's and Don'ts / Best Practices
- DO: Follow the manufacturer's recommended maintenance schedule for CVT fluid changes. Use ONLY the specified fluid type. Incorrect fluid can cause significant damage.
- DO: Allow the vehicle to warm up properly before driving, especially in cold weather.
- DO: Drive smoothly and avoid abrupt acceleration or deceleration.
- DO: Monitor the CVT's operating temperature, especially when towing or driving in hot conditions.
- DON'T: Tow loads that exceed the vehicle's rated towing capacity.
- DON'T: Perform "neutral drops" or other abusive driving maneuvers.
- DON'T: Ignore warning signs, such as unusual noises, vibrations, or slipping. Get the CVT inspected by a qualified technician promptly.
Conclusion
While the concept of a CVT dates back to the late 19th century, its widespread adoption is a relatively recent phenomenon. The DAF Variomatic in 1958 represented a significant milestone, but it wasn't until the late 20th and early 21st centuries that advancements in materials, electronics, and control systems made CVTs a viable option for a broad range of vehicles. They offer potential benefits in terms of fuel efficiency and smoothness, but they also require proper maintenance and care. If you own a vehicle with a CVT, it's crucial to understand its operating principles and follow the manufacturer's recommendations to ensure its longevity. While CVTs have improved considerably, staying proactive with maintenance will help avoid costly repairs in the long run. Therefore, prioritize proper maintenance and be mindful of driving habits to maximize the lifespan and performance of your CVT.