When Manifolds And Headers Are Not In Use
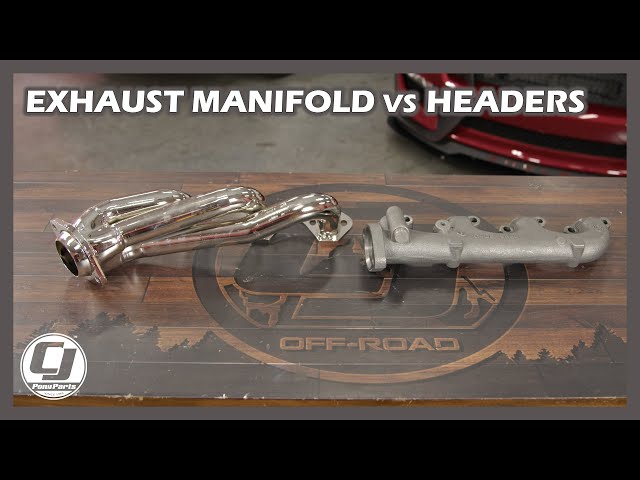
Let's talk about what happens when your intake manifold and exhaust headers aren't actively doing their jobs, or, more accurately, situations that can mimic that scenario. Often, performance problems can be traced back to issues that make it seem like these components aren't performing as designed. Understanding this helps you diagnose problems and improve your engine's efficiency.
Engine Fundamentals: The Breathing Apparatus
Before diving into specifics, let's recap the basic role of these components within an internal combustion engine. The engine operates on a four-stroke cycle: Intake, Compression, Combustion, and Exhaust. The intake manifold and exhaust headers are crucial to the Intake and Exhaust phases, respectively.
Intake Manifold: Delivering the Air-Fuel Mix
The intake manifold is a series of interconnected runners (passageways) that distribute the air-fuel mixture (or just air in a direct injection engine) to each cylinder. It's bolted to the cylinder head and, in essence, is the "breathing apparatus" that draws air into the engine. Its design is critical for engine performance. A well-designed manifold ensures that each cylinder receives an equal and consistent charge of air-fuel mixture. This promotes even combustion, optimal power output, and reduced emissions.
Exhaust Headers: Scavenging Exhaust Gases
The exhaust headers are the first part of the exhaust system directly connected to the cylinder head. Their primary job is to collect exhaust gases from each cylinder and direct them towards the catalytic converter and eventually the muffler. High-performance headers are designed to minimize backpressure and improve the scavenging effect. Scavenging refers to the process where the outgoing exhaust gases help draw in the fresh air-fuel mixture during valve overlap (when both intake and exhaust valves are briefly open). Efficient exhaust flow translates into increased horsepower and torque.
When Performance Falters: Manifold and Header Issues
Now, what are the circumstances when these vital parts aren’t functioning optimally, or what common issues might you encounter?
Vacuum Leaks in the Intake Manifold
One of the most common problems is a vacuum leak. This occurs when air enters the intake manifold after the mass airflow sensor (MAF sensor) or throttle body. The engine control unit (ECU) is expecting a certain amount of air based on the MAF sensor reading. An unmetered air leak throws everything off, leading to a lean air-fuel mixture (too much air, not enough fuel). Symptoms include:
- Rough idling: The engine struggles to maintain a stable idle speed.
- Hesitation during acceleration: The engine might stumble or lag when you press the accelerator.
- Poor fuel economy: The ECU tries to compensate for the lean mixture by adding more fuel.
- Check engine light: Often accompanied by codes related to lean conditions or idle control issues.
Vacuum leaks can occur due to:
- Cracked or brittle vacuum hoses: These are often made of rubber and deteriorate over time.
- Leaking intake manifold gasket: The gasket that seals the manifold to the cylinder head can fail.
- Loose or damaged fittings: Any connections on the intake manifold can become loose or damaged.
Diagnosing vacuum leaks can be done with a smoke test, where smoke is introduced into the intake system and you look for escaping smoke, or using carburetor cleaner/starting fluid sprayed carefully around suspect areas. A change in engine idle indicates a leak.
Restricted Exhaust Flow: Header Problems and Blockages
On the exhaust side, restrictions can significantly hinder engine performance. Issues arise from:
- Collapsed or damaged exhaust pipes: Physical damage to the exhaust system restricts flow.
- Clogged catalytic converter: Over time, the catalytic converter can become clogged with contaminants, restricting exhaust flow and creating backpressure.
- Internal damage to headers: Though rare, headers can develop cracks or internal blockages, especially in extreme conditions.
- Poorly designed or installed headers: Headers not optimized for your engine's specifications can actually hurt performance.
The effects of restricted exhaust flow include:
- Reduced power and torque: The engine struggles to expel exhaust gases efficiently.
- Poor fuel economy: The engine has to work harder to overcome the restriction.
- Overheating: Increased backpressure can lead to higher engine temperatures.
- Check engine light: Often accompanied by codes related to catalytic converter efficiency or oxygen sensor readings.
Diagnosing exhaust restrictions can involve a backpressure test using a gauge installed in place of an oxygen sensor or visual inspection of the exhaust system for damage.
Fuel Delivery Problems: Starving the Manifold
While the intake manifold itself might be in good condition, fuel delivery problems can make it seem like it's not working. This usually stems from:
- Clogged fuel injectors: Dirty injectors don't deliver the correct amount of fuel.
- Weak fuel pump: A failing fuel pump can't maintain adequate fuel pressure.
- Faulty fuel pressure regulator: The regulator controls the fuel pressure in the system.
- Restricted fuel filter: A clogged fuel filter restricts fuel flow to the engine.
Symptoms of fuel delivery problems often mimic vacuum leak symptoms, including:
- Rough idling
- Hesitation during acceleration
- Poor fuel economy
- Check engine light
Fuel delivery issues require a different diagnostic approach, involving fuel pressure testing, injector testing, and fuel filter inspection.
Sensor Issues: Misinformation to the ECU
Problems with sensors that provide data to the ECU can also lead to performance issues that seem like manifold or header problems. The MAF sensor, oxygen sensors, and throttle position sensor (TPS) all play a crucial role in engine management. Faulty readings from these sensors can cause the ECU to make incorrect adjustments to the air-fuel mixture and ignition timing.
Do's and Don'ts / Best Practices
- DO perform regular maintenance: Replacing air filters, fuel filters, and spark plugs helps keep the engine running smoothly.
- DO inspect vacuum hoses regularly: Look for cracks, brittleness, or loose connections.
- DO use quality replacement parts: Cheap aftermarket parts can often cause more problems than they solve.
- DO properly torque all bolts: Especially when installing intake manifolds and exhaust headers. Incorrect torque can lead to leaks or damage.
- DON'T ignore warning signs: Hesitation, rough idling, and poor fuel economy are often early indicators of a problem.
- DON'T overtighten bolts: This can strip threads or damage the components.
- DON'T use excessive sealant: A thin, even coat is all that's needed. Too much sealant can cause blockages.
- Best Practice: When replacing an intake manifold or exhaust header, always replace the gaskets.
- Best Practice: Consider upgrading to performance headers and intake manifolds only after understanding your engine's current capabilities and desired performance goals. A mismatched or poorly chosen upgrade can decrease overall performance.
Conclusion
Understanding the intricate relationship between your engine's intake manifold, exhaust headers, and supporting systems is crucial for effective troubleshooting and performance tuning. While problems with the manifolds and headers themselves can certainly occur, often the symptoms you observe stem from related issues like vacuum leaks, exhaust restrictions, fuel delivery problems, or faulty sensors. By adopting a systematic approach to diagnosis and adhering to best practices for maintenance and upgrades, you can keep your engine breathing easy and performing at its best. Prioritize regular maintenance and a thorough understanding of your engine's operating parameters. This will save you time, money, and frustration in the long run. If you are unsure, consult a professional mechanic.