1993 Custom Build Technical Specifications
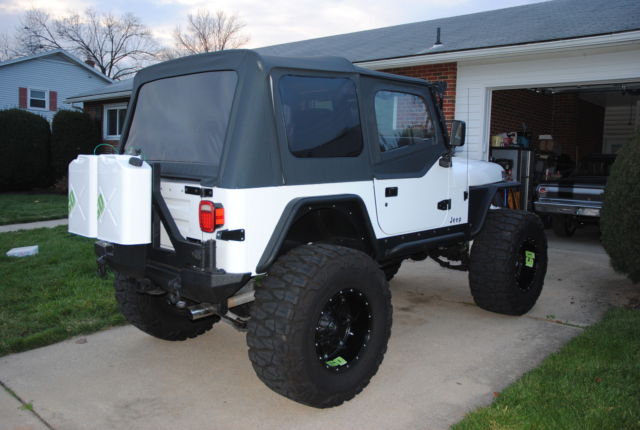
Alright, let's dive into the technical specifications of this 1993 custom build. We're not just talking about a paint job and some fancy wheels here; this is a ground-up transformation, so we'll be covering everything from the engine and drivetrain to the suspension and electronics. This guide assumes you have a reasonable understanding of automotive mechanics, but I'll try to explain everything as clearly as possible, like I'm talking to a fellow gearhead in the shop.
Engine and Drivetrain
The heart of any build is, of course, the engine. In this case, we swapped out the original powerplant for a fully rebuilt LS3 6.2L V8. This wasn't a straight drop-in, so let's break down the specifics.
Engine Block and Internals
The LS3 block itself is a Gen IV small-block, known for its robust design and relatively light weight. We opted for a seasoned block, meaning one that's been run before and has had the initial stresses worked out of it. This helps minimize the risk of future cracking or warping. The block was professionally cleaned, inspected for any damage, and then honed to the correct cylinder bore size. Inside, we went with forged internals for increased strength and durability, especially considering the power we were aiming for. This included:
- Forged Pistons: These are significantly stronger than cast pistons and can withstand much higher compression ratios and combustion pressures. We chose pistons with a slight dome to bump the compression ratio to around 11:1, which is ideal for performance on pump gas.
- Forged Connecting Rods: Again, a strength upgrade. These are typically H-beam or I-beam designs, offering superior resistance to bending and breaking under high loads. We went with H-beam rods for their combination of strength and weight.
- Forged Crankshaft: The crankshaft is the backbone of the engine, and a forged crank is essential for handling the increased power. We opted for a 4340 chromoly steel crankshaft, known for its exceptional strength and resistance to torsional stress.
Cylinder Heads and Valvetrain
The cylinder heads are crucial for airflow and combustion efficiency. We used a set of aftermarket aluminum cylinder heads with CNC-ported runners. CNC porting ensures consistent and optimized airflow compared to hand porting. These heads featured:
- 2.165" Intake Valves and 1.60" Exhaust Valves: These larger valves allow for increased airflow into and out of the cylinders.
- High-Performance Valve Springs: Stiffer valve springs are necessary to control the valves at higher RPMs and prevent valve float. We used dual valve springs with titanium retainers for added durability and reduced weight.
- Roller Rocker Arms: These reduce friction and improve valve train stability. We chose full roller rocker arms with a 1.7:1 ratio for increased valve lift.
The camshaft is the brain of the valvetrain, dictating the timing and duration of valve opening and closing. We selected a custom-ground hydraulic roller camshaft with the following approximate specifications:
- Duration @ 0.050": 230° Intake / 240° Exhaust
- Lift: 0.600" Intake / 0.600" Exhaust
- Lobe Separation Angle (LSA): 112°
This cam provides a good balance of streetability and performance, offering a noticeable increase in power throughout the RPM range without sacrificing idle quality too much.
Fuel and Induction
To feed this beast, we upgraded the fuel system with:
- High-Flow Fuel Injectors: 60 lb/hr injectors were chosen to provide adequate fuel delivery for the increased horsepower.
- Aftermarket Fuel Rails: These rails provide a larger capacity and more consistent fuel pressure to the injectors.
- High-Flow Fuel Pump: A Walbro 450 LPH fuel pump was installed to ensure a constant supply of fuel, even under heavy load.
For induction, we opted for a FAST LSXR intake manifold paired with a 92mm throttle body. This combination provides excellent airflow and throttle response. The air intake system was a custom-fabricated cold air intake with a large conical air filter positioned away from the engine's heat.
Engine Management
Engine management is handled by a standalone Holley EFI system. This allows for complete control over fuel delivery, ignition timing, and other engine parameters. We used a wideband oxygen sensor to monitor the air/fuel ratio and fine-tune the engine for optimal performance and fuel efficiency. The Holley system also provides data logging capabilities, which are invaluable for troubleshooting and optimizing performance.
Drivetrain
To handle the increased power, the original transmission was replaced with a Tremec T56 Magnum 6-speed manual transmission. This transmission is significantly stronger than the stock unit and offers a wider range of gear ratios. We also installed a heavy-duty clutch and flywheel to handle the added torque. The rear end was upgraded to a Ford 9-inch axle with a limited-slip differential and 3.73:1 gears. This provides excellent traction and acceleration. The driveshaft was custom-made to the correct length and balanced for smooth operation.
Suspension and Brakes
Power is useless without control. The suspension was completely overhauled to improve handling and ride quality.
Suspension Components
We installed a full coilover suspension system with adjustable ride height and damping. This allows for fine-tuning of the suspension to suit different driving conditions. We also replaced the original control arms with tubular control arms for increased strength and reduced weight. The sway bars were upgraded to larger diameter units to reduce body roll during cornering. Polyurethane bushings were used throughout the suspension for increased stiffness and responsiveness.
Braking System
The braking system was upgraded with Wilwood 6-piston calipers and 14-inch rotors at the front and 4-piston calipers and 13-inch rotors at the rear. This provides significantly improved braking performance compared to the stock brakes. A Wilwood master cylinder and proportioning valve were also installed to ensure proper brake balance.
Electronics
Beyond the engine management, several other electronic upgrades were implemented.
Gauges and Instrumentation
The original gauges were replaced with aftermarket digital gauges that provide more accurate and detailed information about the engine's performance. We installed gauges for oil pressure, water temperature, fuel pressure, voltage, and air/fuel ratio. A GPS speedometer was used to eliminate the need for a mechanical speedometer cable.
Wiring Harness
The entire wiring harness was replaced with a custom-built harness using high-quality wiring and connectors. This ensures reliable electrical connections and eliminates the risk of shorts or other electrical problems. All wiring was neatly routed and properly grounded.
Lighting
The headlights were upgraded to LED headlights for improved visibility. LED taillights and turn signals were also installed for increased brightness and safety.
This 1993 custom build represents a significant investment of time, money, and expertise. The combination of a powerful engine, upgraded drivetrain, and improved suspension and brakes results in a car that is both exhilarating to drive and reliable for years to come. Remember, this is a highly customized build, and the specific components and specifications may vary depending on the individual preferences and goals of the builder. Always consult with experienced professionals when undertaking such a project to ensure safety and proper execution.