1995 Nissan 240sx Turbocharger System Pressure Ratios And Mapping
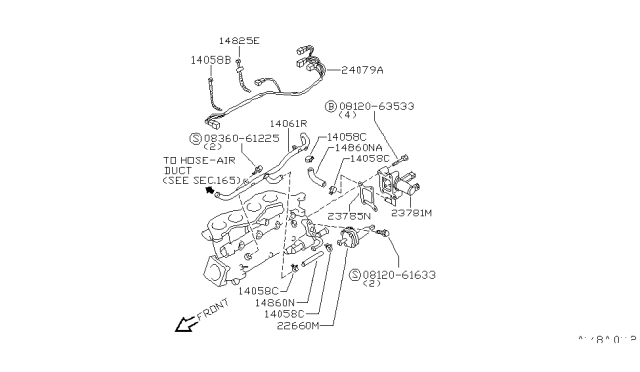
The 1995 Nissan 240SX, a darling of the drift and tuner communities, never came factory-equipped with a turbocharger. However, its robust KA24DE engine and relatively simple design made it a popular platform for aftermarket turbo conversions. Understanding the intricacies of turbocharger system pressure ratios and mapping is crucial for anyone considering or already running a turbocharger on their 240SX. This article delves into these concepts, providing a technical overview relevant to the KA24DE engine and typical turbo setups.
Pressure Ratio: The Core of Turbocharging
The pressure ratio (PR) is arguably the most important parameter in turbocharger selection and operation. It's a simple ratio, but it profoundly affects engine performance and longevity. It's defined as:
PR = (Absolute Pressure at Turbo Outlet) / (Absolute Pressure at Turbo Inlet)
Let's break that down. The "absolute pressure" refers to the total pressure, including atmospheric pressure. So, standard atmospheric pressure at sea level is approximately 14.7 psi (101.3 kPa), or 1 atmosphere (atm). If your turbo is boosting to 14.7 psi (relative to atmospheric, meaning gauge pressure), then the absolute pressure at the turbo outlet is 14.7 psi (boost) + 14.7 psi (atmospheric) = 29.4 psi absolute. Assuming atmospheric pressure at the turbo inlet, your pressure ratio is 29.4 / 14.7 = 2.0.
A pressure ratio of 1.0 means the turbo is doing nothing; the outlet pressure is the same as the inlet pressure. Any value greater than 1.0 indicates the turbo is compressing the intake air.
Impact on Engine Performance
A higher pressure ratio means more air is being forced into the engine's cylinders. This increased air mass allows for more fuel to be burned, resulting in a larger, more powerful combustion event. However, simply increasing the pressure ratio isn't a free lunch. As air is compressed, its temperature rises. This hotter intake charge is less dense and more prone to pre-ignition (knock), reducing power and potentially damaging the engine.
Intercooling: Taming the Heat
This is where the intercooler comes in. An intercooler is a heat exchanger that cools the compressed air after it exits the turbo and before it enters the engine. By reducing the intake air temperature, the intercooler allows for higher boost pressures (and therefore higher pressure ratios) without the risk of excessive knock. The efficiency of the intercooler is critical. A poorly designed or undersized intercooler will negate many of the benefits of a turbocharger.
Turbocharger Mapping: Visualizing Performance
A turbocharger map (also known as a compressor map) is a graphical representation of the turbocharger's performance characteristics. It plots pressure ratio against corrected mass airflow, and overlays efficiency islands. Understanding and interpreting a turbocharger map is vital for selecting the correct turbocharger for your KA24DE and your performance goals.
Key Components of a Turbocharger Map
- Y-axis: Pressure Ratio. As previously discussed, this is the ratio of outlet to inlet pressure.
- X-axis: Corrected Mass Airflow. This represents the amount of air (in lb/min or kg/s) that the turbocharger is moving, corrected for temperature and pressure variations. Correction is necessary because turbocharger maps are generated under specific testing conditions.
- Efficiency Islands: These are elliptical or oval-shaped contours on the map. Each contour represents a specific turbocharger efficiency percentage. The closer you are to the center of the highest efficiency island, the more efficiently the turbo is operating. Efficiency is important because an inefficient turbo generates more heat, reducing overall performance and increasing the risk of knock.
- Surge Line: This is a line on the left side of the map. Operating to the left of the surge line can cause compressor surge, a damaging phenomenon characterized by reversed airflow through the turbocharger. This sounds like a "barking" or "fluttering" noise and can rapidly damage the turbo.
- Choke Line: This is a line on the right side of the map. Operating to the right of the choke line means the turbocharger is reaching its maximum airflow capacity. Boosting beyond this point will likely result in minimal power gains and significantly increased exhaust backpressure.
Mapping the KA24DE's Airflow Requirements
To effectively use a turbocharger map, you need to estimate the KA24DE's airflow requirements at various RPMs and boost levels. This requires some calculation. The ideal gas law (PV=nRT) and volumetric efficiency come into play here, but simplified estimations are possible.
First, calculate the engine's theoretical maximum airflow. For a 2.4-liter (2400cc) engine, the volumetric displacement per revolution is 2400cc / 2 = 1200cc (since it's a four-stroke engine, it takes two revolutions to complete a combustion cycle). Convert this to cubic feet per minute (CFM) at a given RPM:
CFM = (Engine Displacement in Liters * RPM * Volumetric Efficiency) / 28.317
Volumetric efficiency is a measure of how well the engine fills its cylinders with air. A naturally aspirated KA24DE might have a volumetric efficiency of around 85%. A turbocharged engine, especially with proper tuning, can exceed 100% VE.
Let's assume a target RPM of 6000 and a VE of 90%:
CFM = (2.4 * 6000 * 0.9) / 28.317 = 456.3 CFM
This is the approximate airflow requirement at atmospheric pressure. Now, account for boost. If you're targeting a pressure ratio of 2.0 (14.7 psi boost), you need to multiply the CFM by the pressure ratio:
Boosted CFM = 456.3 CFM * 2.0 = 912.6 CFM
Finally, convert CFM to lbs/min. At standard temperature and pressure (STP), 1 lb/min of air is approximately 14.26 CFM:
lbs/min = 912.6 CFM / 14.26 = 64 lbs/min (approximately)
Therefore, at 6000 RPM and 14.7 psi of boost, the KA24DE will require approximately 64 lbs/min of airflow. This point can then be plotted on the turbocharger map, along with similar calculations for other RPMs and boost levels. The goal is to select a turbocharger where these operating points fall within the high-efficiency islands of the map.
Choosing the Right Turbocharger
By plotting the engine's airflow requirements on several turbocharger maps, you can identify which turbocharger is best suited for your desired performance. Considerations include:
- Desired Power Output: Higher power levels require more airflow and therefore a larger turbo.
- Spool-Up Time: Smaller turbos spool up faster, providing quicker boost response. Larger turbos take longer to spool but can provide higher peak power.
- Engine Management System: A capable engine management system (EMS) is essential for properly tuning a turbocharged KA24DE. The EMS controls fuel delivery, ignition timing, and boost, ensuring optimal performance and engine safety.
- Budget: Turbochargers vary greatly in price. Consider the cost of the turbocharger itself, as well as supporting modifications like injectors, fuel pump, intercooler, and EMS.
Conclusion
Understanding pressure ratios and turbocharger mapping is essential for anyone modifying a 1995 Nissan 240SX (or any engine) with a turbocharger. By carefully analyzing these parameters and selecting the appropriate components, you can achieve significant performance gains while maintaining engine reliability. While the calculations and map reading might seem complex initially, the effort invested in understanding these concepts will pay off with a well-tuned, powerful, and reliable turbocharged KA24DE.