1997 Nissan Pathfinder Lower Control Arm
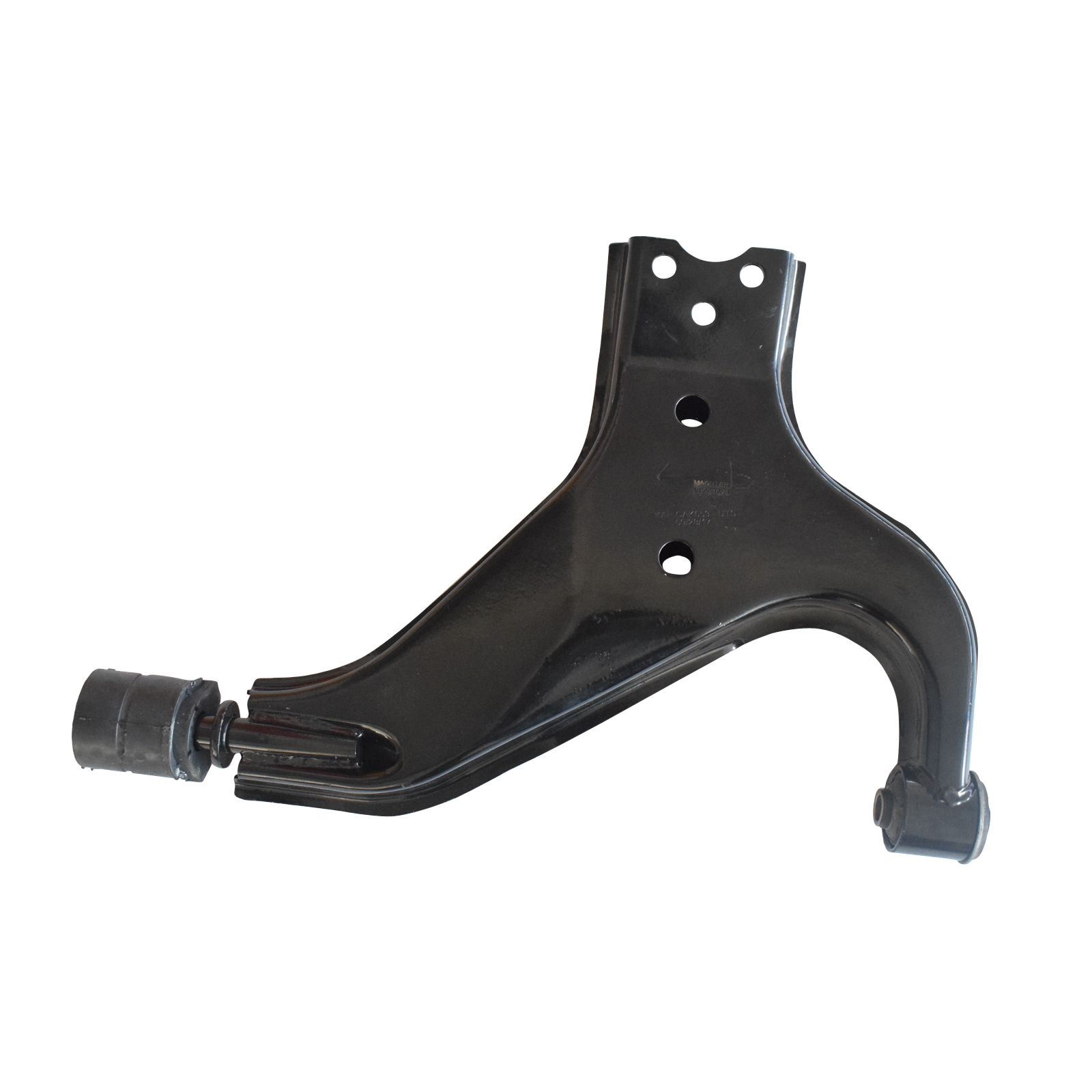
The 1997 Nissan Pathfinder, a staple of the SUV boom era, boasts a robust suspension system designed to handle both on-road comfort and moderate off-road excursions. A critical component of this system is the lower control arm. While often overlooked until a problem arises, the lower control arm plays a vital role in vehicle stability, handling, and overall safety. This article delves into the design, function, and potential failure points of the 1997 Nissan Pathfinder's lower control arm, offering insights for both curious readers and amateur engineers.
Function and Design
At its core, the lower control arm is a suspension link that connects the vehicle's chassis to the wheel hub. In the 1997 Pathfinder, the front suspension utilizes a double-wishbone configuration, meaning there are both upper and lower control arms. The lower control arm, being closer to the ground and bearing a significant portion of the vehicle's weight, is generally the more substantial of the two. Its primary functions are:
- Providing a Pivot Point: The control arm allows the wheel to move up and down in response to road imperfections, facilitating vertical suspension travel.
- Maintaining Wheel Position: It rigidly connects the wheel hub to the chassis, preventing unwanted lateral movement and ensuring proper alignment. This is crucial for steering accuracy and tire wear.
- Transmitting Forces: The control arm transmits braking and acceleration forces from the wheel hub to the chassis.
- Supporting Spring and Damper: The lower control arm often serves as a mounting point for the coil spring and shock absorber, further integrating it into the suspension system.
The typical 1997 Pathfinder lower control arm is a forged or stamped steel component, chosen for its strength and durability. The specific geometry and material composition vary depending on Nissan's design requirements, balancing factors like weight, stiffness, and manufacturing cost. It's not a simple straight bar; instead, it's shaped to provide necessary clearance for other suspension components and to optimize its strength under various load conditions.
Key Components of the Lower Control Arm Assembly
The lower control arm itself isn't a standalone part; it's an assembly consisting of several key components:
- The Arm Body: This is the main structural component, the forged or stamped steel piece.
- Ball Joint: Located at the outboard end of the control arm, the ball joint connects the control arm to the steering knuckle (wheel hub). It allows for pivoting movement in multiple planes, enabling the wheel to steer and move vertically. The ball joint is typically a sealed unit containing a ball stud, socket, and grease for lubrication.
- Bushings: Located at the inboard end of the control arm, where it connects to the vehicle's frame, bushings are typically made of rubber or polyurethane. They act as vibration dampeners, reducing noise and harshness transmitted from the road to the chassis. Bushings also allow for some controlled movement and articulation of the control arm.
- Mounting Points: These are the reinforced areas on the control arm where it bolts to the frame and to the steering knuckle. They must be robust to withstand high stresses.
- Coil Spring Seat (If Applicable): Depending on the Pathfinder's specific suspension configuration, the lower control arm might include a seat or platform to support the coil spring.
Forces and Stresses
The lower control arm is subjected to a complex array of forces during vehicle operation. Understanding these forces is crucial for appreciating the design and potential failure modes of the component. Key forces include:
- Vertical Load: This is the weight of the vehicle, passengers, and cargo, acting downwards on the control arm. This is a primarily compressive force.
- Longitudinal Forces: These are forces generated during acceleration and braking, acting along the length of the vehicle. These forces can be tensile (pulling) or compressive (pushing).
- Lateral Forces: These are forces generated during cornering, acting perpendicular to the length of the vehicle. These forces cause the control arm to flex and twist.
- Torsional Forces: These are twisting forces generated by uneven road surfaces or impacts.
The magnitude and direction of these forces vary constantly depending on driving conditions. The control arm is designed to withstand these forces within specified limits. However, exceeding those limits, through extreme off-roading or impacts, can lead to damage or failure.
Common Failure Points and Symptoms
Despite being a robust component, the lower control arm is susceptible to wear and damage over time. Common failure points include:
- Ball Joint Failure: The ball joint is a wear item that can loosen or fail due to contamination, lack of lubrication, or excessive wear. Symptoms include:
- Clunking or popping noises, especially when turning or going over bumps.
- Loose or wandering steering.
- Uneven tire wear.
- Play in the ball joint when inspected.
- Bushing Failure: Bushings can crack, tear, or become excessively soft over time, leading to:
- Vibration or shaking in the steering wheel.
- Poor handling and stability.
- Squeaking or groaning noises.
- Visible cracks or deterioration in the bushing material.
- Control Arm Bending or Cracking: This is less common but can occur due to severe impacts, corrosion, or material fatigue. Symptoms include:
- Visible damage to the control arm.
- Misalignment of the suspension.
- Difficulty maintaining vehicle alignment.
- Corrosion: Especially in regions with harsh winters and road salt, corrosion can weaken the control arm, eventually leading to failure. Regular inspection and rust prevention measures are crucial.
It's important to note that symptoms of a worn or damaged lower control arm can sometimes mimic those of other suspension or steering components. Therefore, a thorough inspection by a qualified mechanic is essential for accurate diagnosis.
Material Science and Manufacturing
The choice of materials and manufacturing processes for the lower control arm is critical to its performance and longevity. High-strength steel is typically used, often with specific alloys added to enhance properties like yield strength, tensile strength, and corrosion resistance. Two primary manufacturing methods are commonly employed:
- Forging: This process involves shaping heated metal using compressive forces. Forging produces parts with excellent strength and fatigue resistance due to the aligned grain structure of the metal.
- Stamping: This process involves shaping sheet metal using dies and presses. Stamping is a more cost-effective method for producing complex shapes, but the resulting parts may not be as strong as forged parts.
Regardless of the manufacturing method, heat treatment processes are often applied to further enhance the strength and durability of the control arm. These processes involve heating and cooling the metal in a controlled manner to alter its microstructure.
Inspection and Maintenance
Regular inspection of the lower control arm is crucial for identifying potential problems before they lead to catastrophic failure. Inspections should include:
- Visual Inspection: Look for cracks, bends, corrosion, and damage to the ball joint and bushings.
- Ball Joint Play Check: Use a pry bar or specialized tool to check for excessive play in the ball joint.
- Bushing Condition: Visually inspect the bushings for cracks, tears, or excessive softness. Also, try to move the control arm by hand to check for excessive play in the bushings.
- Listen for Noises: Pay attention to any unusual noises, such as clunking, popping, squeaking, or groaning, coming from the suspension.
While some maintenance tasks, such as lubricating the ball joint (if equipped with a grease fitting), can be performed by DIYers, more complex repairs, such as replacing the ball joint or bushings, typically require specialized tools and expertise. Replacing the entire lower control arm assembly is often the preferred solution, especially if the arm itself is damaged or corroded.
Conclusion
The lower control arm is an unsung hero of the 1997 Nissan Pathfinder's suspension system. Its robust design and crucial function contribute significantly to the vehicle's handling, stability, and safety. Understanding its operation, potential failure points, and maintenance requirements allows owners and enthusiasts to ensure the continued performance and reliability of their Pathfinder's suspension system. By paying attention to the symptoms of wear and damage and performing regular inspections, you can keep your Pathfinder running smoothly and safely for years to come. Ignoring these components can lead to dangerous driving conditions. Always consult a qualified mechanic for proper diagnosis and repair.