2016 Nissan Altima Front Bumper Painted
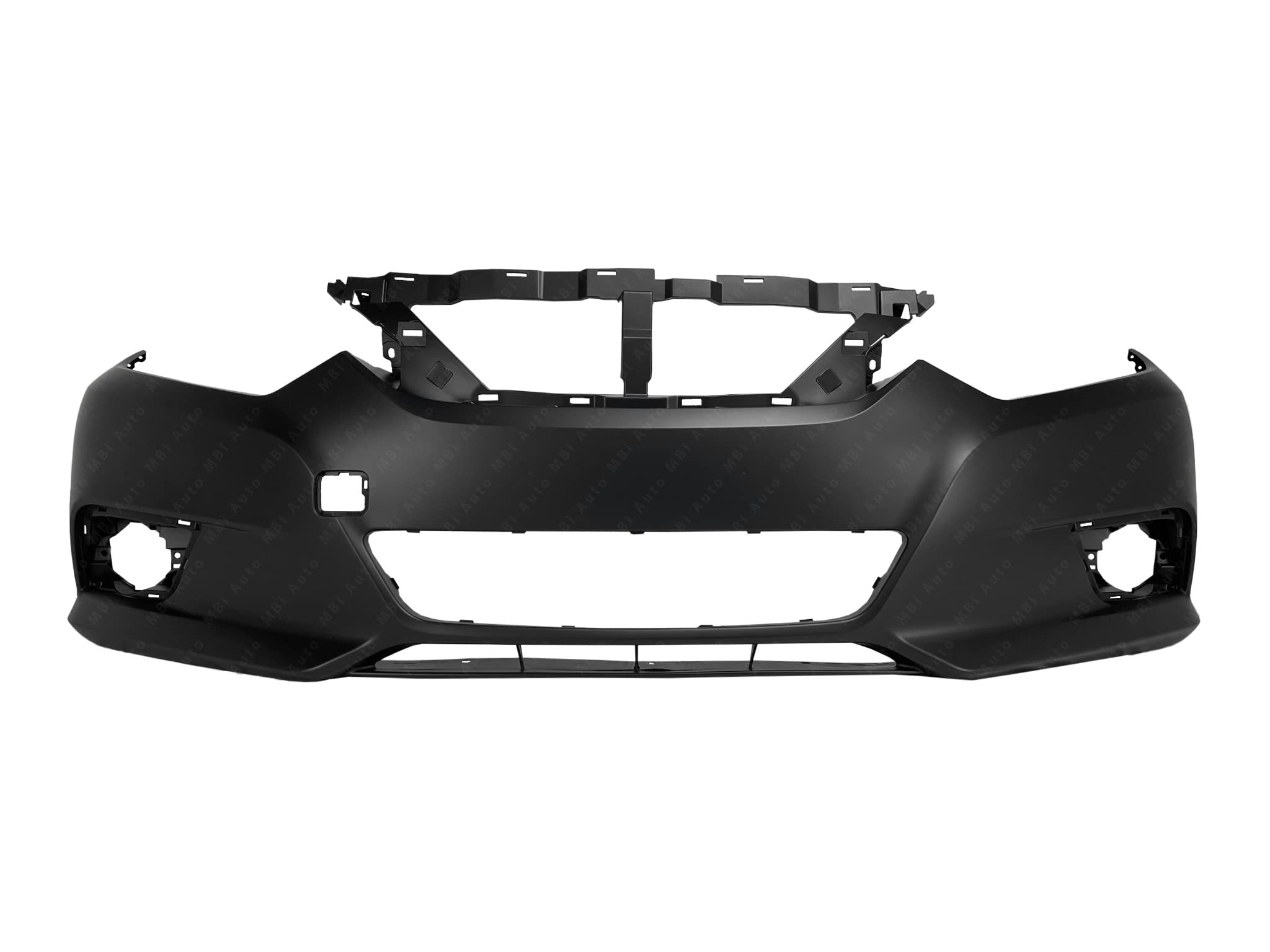
The 2016 Nissan Altima, a mainstay in the mid-size sedan segment, presents a compelling blend of fuel efficiency, comfort, and value. While often overlooked, the front bumper, specifically its painted finish, plays a critical role in both the vehicle's aesthetics and its structural integrity. This analysis delves into the engineering and manufacturing intricacies behind the painted front bumper of the 2016 Altima, offering a detailed exploration for the curious reader and the aspiring automotive engineer.
Material Composition and Design
The foundation of the 2016 Altima's front bumper is typically a polymer-based material, commonly polypropylene (PP) or a similar thermoplastic olefin (TPO). The selection of PP or TPO stems from their favorable properties, including impact resistance, flexibility, and moldability. These materials are relatively lightweight, contributing to overall fuel efficiency. The exact grade of polymer used will be chosen to provide the correct balance of properties, and may include reinforcing additives for increased strength and stiffness.
The design itself is dictated by several factors. Aerodynamic considerations are paramount, as the bumper's shape influences airflow around the vehicle, impacting fuel economy and high-speed stability. The Integrated design of the bumper also involves accommodating various components such as fog lights, parking sensors (if equipped), and the lower grille. The bumper is designed to deform in a controlled manner during low-speed collisions, absorbing energy and minimizing damage to the vehicle's structure and occupants. Finite Element Analysis (FEA) is extensively used during the design phase to simulate impact scenarios and optimize the bumper's geometry for crash performance.
Furthermore, pedestrian safety is a critical design constraint. Modern bumper designs incorporate features that reduce the severity of injuries to pedestrians in the event of a collision. This might involve incorporating energy-absorbing foams or carefully shaped surfaces to distribute impact forces.
Manufacturing Process
The manufacturing of the bumper involves several key steps:
Injection Molding
The primary method for producing the bumper's core structure is injection molding. Molten polymer is injected under high pressure into a mold cavity that defines the bumper's shape. The mold is typically made of steel or aluminum and is precisely machined to ensure dimensional accuracy. After the polymer cools and solidifies, the mold opens, and the bumper is ejected.
The injection molding process requires precise control of temperature, pressure, and cycle time to ensure a consistent and high-quality product. Any variations in these parameters can lead to defects such as warping, sink marks, or short shots (incomplete filling of the mold cavity).
Surface Preparation
Before painting, the molded bumper undergoes a series of surface preparation steps. This is critical to ensure proper paint adhesion and a durable finish. The process typically involves:
- Cleaning: Removing any residual mold release agents, oils, or contaminants from the bumper's surface. This is often achieved using specialized detergents or solvents.
- Sanding/Abrasive Blasting: Creating a slightly roughened surface to promote mechanical adhesion of the primer. The grade of abrasive used is carefully selected to avoid damaging the plastic.
- Degreasing: Removing any remaining traces of grease or oil after sanding.
- Antistatic treatment: Removing any static electricity from the part, which will attract contaminants.
Priming
A primer coat is applied to the prepared bumper surface. The primer serves several important functions:
- Adhesion Promotion: Creating a strong bond between the plastic substrate and the subsequent paint layers.
- Surface Smoothing: Filling in minor imperfections and creating a uniform surface for painting.
- Corrosion Protection (in some cases): Providing a barrier against moisture and other environmental factors that could degrade the plastic.
The primer is typically applied using spray painting techniques, ensuring even coverage and consistent film thickness. After application, the primer is cured using heat or ultraviolet (UV) light to create a durable and chemically resistant layer. The type of primer used is specifically formulated for plastic substrates and must be compatible with the topcoat paint system.
Painting
The painting process is where the bumper receives its final color and appearance. This typically involves multiple layers of paint, each serving a specific purpose. A common approach is a three-coat system:
- Basecoat: Provides the color and metallic or pearl effect (if desired). Basecoats are usually solvent-based and require careful application to achieve a uniform color match with the rest of the vehicle.
- Midcoat (optional): Some paint systems use a midcoat to enhance the color depth or create special effects.
- Clearcoat: Provides a protective layer that resists scratches, UV damage, and chemical attack. The clearcoat is responsible for the gloss and overall durability of the finish.
Paint is applied using automated spray painting robots in controlled environments to ensure consistent quality and minimize overspray. Electrostatic painting is often employed, where the bumper is given an electrical charge, attracting the paint particles and improving transfer efficiency.
The color matching process is absolutely critical. Automakers use sophisticated spectrophotometers to measure the color of existing body panels and formulate paints that provide a near-perfect match. Variations in color can occur due to factors such as batch-to-batch differences in paint pigments, variations in application techniques, and the age of the paint. Therefore, skilled paint technicians are essential for achieving a seamless finish.
Curing
After each paint layer is applied, the bumper is cured in ovens at elevated temperatures. Curing promotes cross-linking within the paint film, resulting in a hardened, durable, and chemically resistant finish. The curing temperature and duration are carefully controlled to optimize the paint's properties without damaging the plastic substrate. UV curing is also a common alternative, particularly for clearcoats. UV curing offers advantages such as faster curing times and lower energy consumption.
Quality Control
Throughout the manufacturing process, rigorous quality control checks are performed to ensure that the bumper meets the required specifications. These checks include visual inspections for defects such as runs, sags, orange peel, and color mismatches. Film thickness measurements are taken to ensure that the paint layers are within the specified tolerances. Adhesion tests are performed to verify that the paint is properly bonded to the substrate. Impact resistance tests are conducted to assess the bumper's ability to withstand impacts without cracking or chipping.
Challenges and Future Trends
Several challenges are associated with painting plastic bumpers. One significant challenge is the difference in thermal expansion coefficients between plastic and paint. This can lead to cracking or delamination of the paint film under extreme temperature variations. Another challenge is achieving a durable and scratch-resistant finish that can withstand the rigors of everyday driving. Environmental regulations are also driving the development of more environmentally friendly paint systems, such as waterborne paints and powder coatings, which have lower VOC (volatile organic compound) emissions.
Future trends in bumper painting include the use of self-healing coatings, which can repair minor scratches and abrasions. Nanotechnology is also being explored to create coatings with enhanced scratch resistance, UV protection, and self-cleaning properties. Furthermore, advancements in additive manufacturing (3D printing) are enabling the creation of complex bumper designs with integrated features and improved aerodynamic performance.
In conclusion, the painted front bumper of the 2016 Nissan Altima represents a sophisticated blend of materials science, engineering design, and manufacturing processes. From the selection of polymers to the meticulous painting and curing steps, every aspect of the bumper's creation is carefully controlled to ensure that it meets the stringent requirements for aesthetics, durability, and safety. Understanding these intricacies provides a deeper appreciation for the engineering behind this often-overlooked component of the modern automobile.