2018 Nissan Rogue Steering Wheel Cover
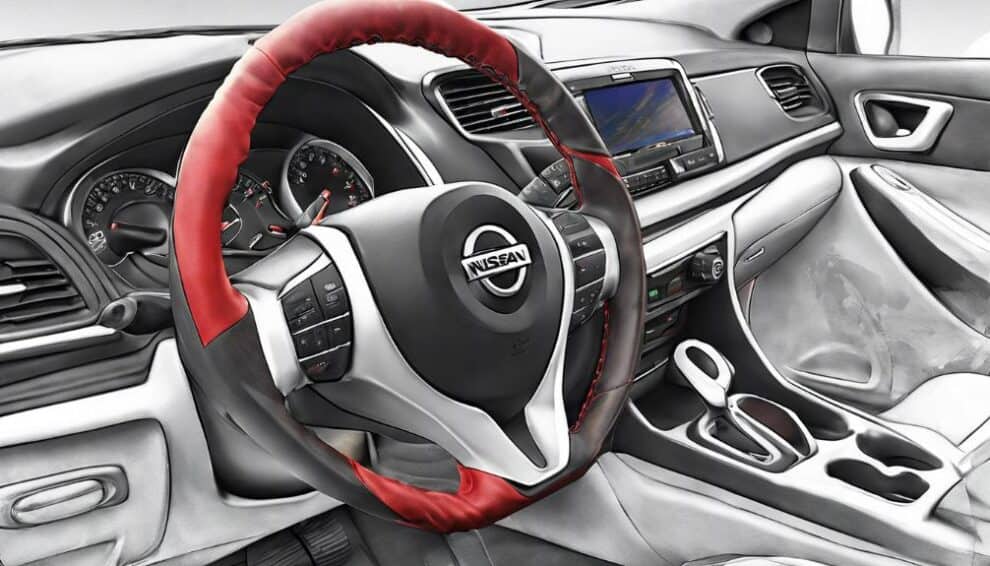
The seemingly simple steering wheel cover on a 2018 Nissan Rogue represents a surprisingly complex intersection of ergonomics, materials science, manufacturing processes, and design aesthetics. While its primary function is to enhance grip and comfort for the driver, the engineering behind its construction goes far beyond a simple slip-on sleeve. This guide delves into the technical aspects of a typical 2018 Rogue steering wheel cover, exploring its construction, materials, and the engineering considerations that influence its design.
Dissecting the Anatomy of a Steering Wheel Cover
To truly understand the engineering, let's break down the typical components of a 2018 Rogue steering wheel cover. While aftermarket options abound, we'll focus on a reasonably high-quality, stitched cover to highlight the key features.
The Core Material: Grip and Feel
The primary material is usually some form of leather or a synthetic alternative like polyurethane (PU) or microfiber leather. Real leather offers a premium feel, superior durability, and breathability, but it also comes with a higher price tag and requires more maintenance. Synthetic alternatives, on the other hand, offer similar tactile properties at a more accessible price point and are often more resistant to wear and tear and UV degradation.
The choice of material is a critical engineering decision. It impacts:
- Coefficient of Friction: This determines the grip available to the driver. Higher friction translates to better control, especially in dynamic driving situations. Manufacturers often use textured surfaces or perforations to further enhance grip.
- Thermal Conductivity: How well the material conducts heat affects comfort. Leather tends to breathe better than synthetic materials, preventing sweaty palms. Conversely, in cold weather, some materials can feel unpleasantly cold to the touch.
- Durability: Resistance to abrasion, cracking, and fading under sunlight and temperature fluctuations is paramount. High-quality materials undergo rigorous testing to ensure they meet specific durability standards.
- Aesthetics: The visual appeal of the material contributes to the overall interior ambiance of the vehicle. The color, grain, and finish are carefully selected to complement the existing design.
The thickness of the material is also a critical design parameter. Too thin, and it won't provide sufficient cushioning or grip. Too thick, and it can feel bulky and diminish the driver's sense of connection with the steering system.
The Substrate: Structural Integrity
Beneath the surface material lies a substrate, often a layer of foam or a similar cushioning material. This layer serves several important purposes:
- Comfort and Vibration Damping: The foam provides a comfortable cushioning effect, reducing fatigue on long drives. It also helps dampen vibrations transmitted from the road through the steering system, improving the overall driving experience.
- Shape Retention: The substrate helps the cover maintain its shape and conform to the contours of the steering wheel. It prevents the cover from sagging or bunching up.
- Secure Fit: The substrate can incorporate features like elastic bands or gripping surfaces to ensure a snug and secure fit on the steering wheel. This prevents the cover from slipping or rotating during use, which could compromise driver control.
The density and composition of the foam are carefully chosen to achieve the desired balance of comfort, support, and durability. Closed-cell foams are often preferred because they are resistant to moisture absorption and provide better long-term performance.
The Stitching: Art and Engineering
The stitching is not merely a decorative element; it plays a crucial role in the structural integrity and overall performance of the steering wheel cover. The type of stitch used, the thread material, and the stitch density all contribute to the cover's strength and durability.
- Stitch Type: Common stitch types include the saddle stitch, the baseball stitch, and the overlock stitch. Each stitch has its own unique characteristics in terms of strength, flexibility, and appearance. The saddle stitch, for example, is known for its durability and its ability to resist unraveling.
- Thread Material: High-strength nylon or polyester thread is typically used to ensure that the stitches can withstand the stresses of everyday use. The thread is often UV-resistant to prevent fading and degradation under sunlight.
- Stitch Density: The number of stitches per inch (SPI) is a measure of stitch density. Higher SPI generally results in a stronger and more durable seam. However, too high an SPI can weaken the material by creating too many perforations.
The pattern of the stitching is also carefully designed to provide reinforcement in areas that are subjected to high stress, such as the grip zones. Some covers incorporate features like reinforced stitching or double stitching in these areas to further enhance durability.
Underlying Frame/Structure (If Applicable)
Some steering wheel covers, especially those designed for a very specific fit, might incorporate a semi-rigid plastic or composite frame. This frame provides additional structural support and helps the cover maintain its shape even under extreme temperatures or prolonged use. This is more common in covers that are designed to be "permanently" installed and mimic the appearance of a factory-installed leather steering wheel.
Manufacturing and Assembly
The manufacturing process involves several key steps, each requiring precision and attention to detail:
- Material Cutting: The leather or synthetic material is precisely cut to the required shape using automated cutting machines or traditional cutting techniques.
- Substrate Lamination: The foam or other cushioning material is laminated to the back of the leather or synthetic material. This process involves applying an adhesive and bonding the two layers together under pressure.
- Stitching: The various pieces of the cover are stitched together using automated sewing machines or hand-stitching techniques.
- Finishing: The cover is inspected for any defects and finished with treatments to protect the material and enhance its appearance.
- Inspection and Quality Control: Rigorous quality control measures are implemented throughout the manufacturing process to ensure that the finished product meets the required standards for fit, finish, and durability.
Engineering Considerations: A Deeper Dive
Beyond the basic components, a host of engineering considerations influence the design and performance of a steering wheel cover:
- Ergonomics: The shape and thickness of the cover are carefully designed to provide a comfortable and secure grip for a wide range of hand sizes. Contoured designs and strategically placed padding can help reduce hand fatigue and improve driver comfort.
- Safety: The cover must not interfere with the operation of any of the vehicle's safety systems, such as the airbag. The design must ensure that the airbag can deploy properly in the event of a collision.
- Environmental Considerations: Manufacturers are increasingly focused on using environmentally friendly materials and manufacturing processes. This includes using recycled materials, reducing waste, and minimizing the use of harmful chemicals.
- Cost Optimization: Balancing performance, durability, and cost is a constant challenge. Engineers must carefully select materials and manufacturing processes that provide the best value for the customer.
- UV Resistance: The cover must be resistant to degradation from ultraviolet (UV) radiation from sunlight. UV stabilizers are often added to the materials to protect them from fading and cracking.
The fit of the steering wheel cover is also critical. A poorly fitting cover can slip or bunch up, compromising driver control and safety. Therefore, precise measurements and careful attention to detail are required to ensure a snug and secure fit.
The selection of materials and manufacturing processes is heavily influenced by testing. Covers are subjected to rigorous tests to evaluate their resistance to abrasion, UV degradation, temperature fluctuations, and other environmental factors. These tests help engineers identify potential weaknesses and optimize the design for long-term durability.
Understanding the complexities involved in designing and manufacturing a steering wheel cover underscores the importance of even seemingly simple automotive components. A well-engineered steering wheel cover not only enhances comfort and grip but also contributes to overall driving safety and the longevity of the vehicle's interior.
In conclusion, the 2018 Nissan Rogue steering wheel cover is more than just an accessory. It's a carefully engineered component that reflects a balance between ergonomics, materials science, and manufacturing precision. By understanding the underlying principles, we can appreciate the engineering efforts that go into creating a product that enhances the driving experience.