240sx Banjo Bolt Style Braided Brake Lines
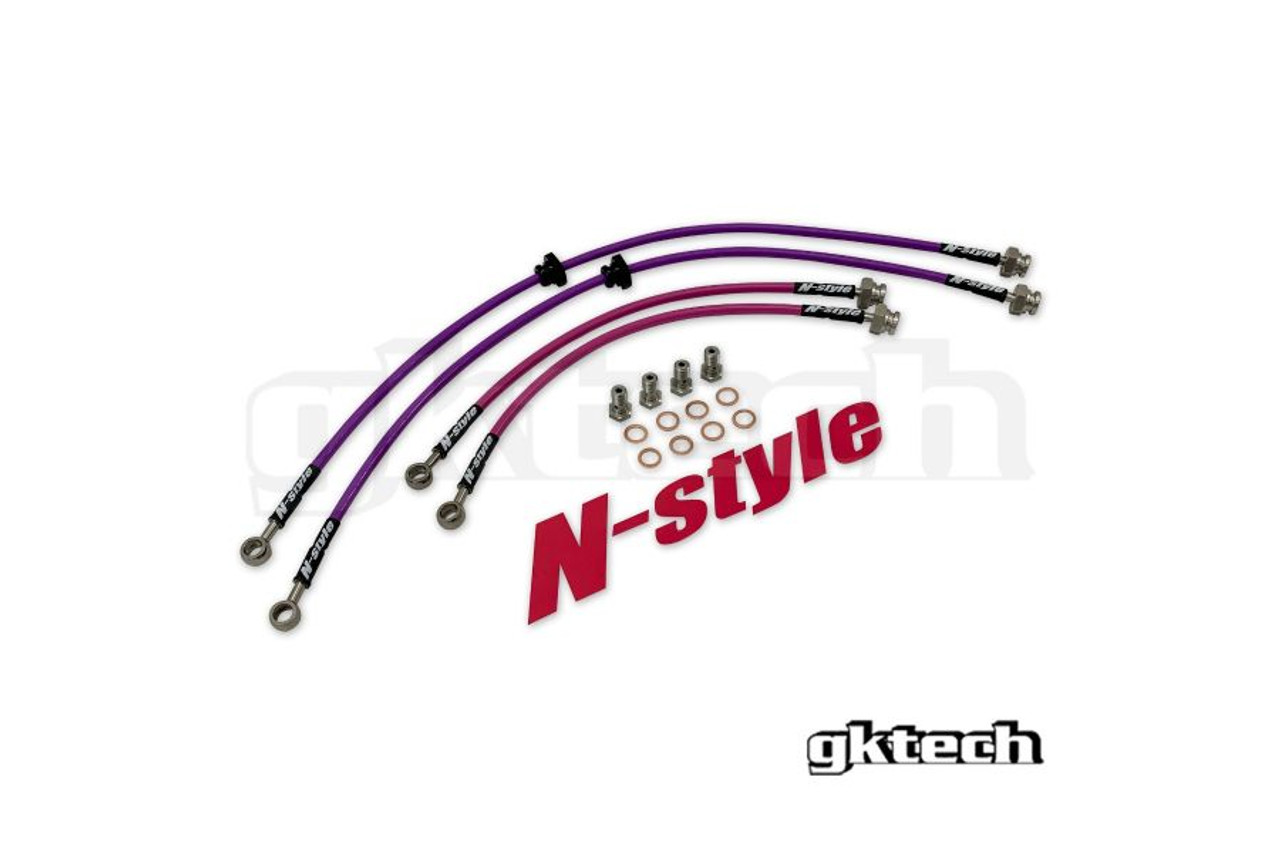
The Nissan 240SX, a darling of the drift and tuner scene, often sees extensive modifications to improve its performance. One crucial upgrade, frequently overlooked until panic sets in at the first corner, is the braking system. While bigger rotors and calipers grab headlines, the unsung heroes of braking efficiency are often the humble braided stainless steel brake lines. This article dives deep into the specifics of 240SX brake line upgrades, focusing particularly on the nuances of banjo bolt style connections.
Understanding Brake Line Dynamics
Before dissecting the banjo bolt configuration, let's establish why upgrading to braided stainless steel lines is beneficial. OEM brake lines are typically constructed from rubber, reinforced with a woven fabric. While cost-effective, rubber is porous and, critically, expands under pressure. When you stomp on the brake pedal, a portion of the hydraulic force is spent inflating the lines, leading to a softer, less responsive pedal feel and a reduction in braking power. This is commonly referred to as "brake fade" due to line expansion.
Braided stainless steel lines, on the other hand, consist of a Teflon or PTFE inner liner (the actual fluid carrier) wrapped in a tightly woven stainless steel braid. This braid provides exceptional strength and, more importantly, prevents expansion under pressure. This translates directly to a firmer, more consistent pedal feel, improved modulation (control over braking force), and shorter stopping distances. The Teflon/PTFE inner liner is also chemically inert and resists degradation from brake fluid, extending the lifespan of the lines.
Banjo Bolt Connections: An In-Depth Look
Now, let's focus on the banjo bolt configuration. This connection style utilizes a circular fitting (the "banjo") with a hole through its center. The banjo fitting sits flush against the caliper or master cylinder, and a hollow bolt (the banjo bolt) passes through the banjo fitting and into the component. This bolt secures the banjo fitting and provides a path for the brake fluid to flow.
Advantages of Banjo Bolt Style
Banjo bolts offer several advantages, particularly in tight spaces:
- Compact Design: They require less space than traditional threaded fittings, making them ideal for applications where clearance is limited. This is often a significant factor in the 240SX engine bay or around the calipers.
- Rotational Freedom: The banjo fitting can be rotated around the bolt, allowing for flexible line routing. This is crucial when dealing with aftermarket suspension components, engine swaps, or other modifications that might interfere with brake line placement.
- Ease of Installation: While proper torque is essential (more on that later), banjo bolts are relatively straightforward to install and remove.
Disadvantages and Considerations
Despite their advantages, banjo bolt connections also have potential drawbacks:
- Potential for Leaks: If not properly installed or if the sealing washers are damaged, banjo bolts are prone to leaks. This is the most common issue encountered with this type of connection.
- Specific Torque Requirements: Over-tightening or under-tightening a banjo bolt can lead to leaks or even damage to the caliper or master cylinder. Adhering to the manufacturer's specified torque value is absolutely critical.
- Washer Compatibility: Using the correct type and size of sealing washer is essential. Copper or aluminum crush washers are typically used. These washers deform slightly under pressure to create a tight seal. Reusing old washers is strongly discouraged as they will likely be compressed and unable to seal effectively.
Selecting the Right Banjo Bolt Brake Lines for your 240SX
Choosing the right brake lines involves several considerations:
- Line Length: Measure your existing lines or consult a reputable supplier for recommended lengths based on your suspension setup. Too short, and the lines will be under tension and prone to damage. Too long, and they can rub against other components, leading to wear.
- Fitting Material: Stainless steel fittings are generally preferred for their durability and corrosion resistance. Avoid fittings made from cheaper materials that may corrode or fail over time.
- Hose Construction: Ensure the lines use a high-quality Teflon/PTFE inner liner and a tightly woven stainless steel braid. The braid should be free of defects or fraying.
- DOT Compliance: Look for brake lines that meet Department of Transportation (DOT) standards. This ensures they have been tested and certified for use on public roads. While the 240SX is often used for track applications, DOT compliance indicates a certain level of quality and safety.
- Banjo Bolt Size and Thread Pitch: The 240SX typically uses specific banjo bolt sizes and thread pitches for the calipers and master cylinder. Verify compatibility before purchasing. Refer to your vehicle's service manual or consult a knowledgeable parts supplier.
Installation Procedure: A Step-by-Step Guide
Always exercise extreme caution when working with brake systems. Improper installation can lead to brake failure and serious injury or death. If you are not comfortable performing this procedure, seek the assistance of a qualified mechanic.
- Preparation: Gather all necessary tools, including a flare nut wrench (to avoid rounding off the fittings on the hard lines), new sealing washers (copper or aluminum), a torque wrench, brake fluid (DOT 3 or DOT 4, depending on your vehicle's specifications), and a catch pan.
- Fluid Removal: Start by removing the brake fluid reservoir cap and using a syringe or turkey baster to remove as much fluid as possible. This minimizes spillage during the line replacement.
- Line Disconnection: Working on one corner at a time, loosen the fitting connecting the rubber brake line to the hard line on the chassis. Use a flare nut wrench to prevent damaging the fitting. Be prepared for brake fluid to spill.
- Caliper End Disconnection: Disconnect the banjo bolt from the caliper. Catch any remaining fluid in the catch pan. Remove the old sealing washers.
- Line Installation: Install the new braided brake line, using new sealing washers on both sides of the banjo fitting at the caliper. Ensure the banjo fitting is properly seated against the caliper.
- Banjo Bolt Torque: Tighten the banjo bolt to the manufacturer's specified torque value. This is critical. Consult your vehicle's service manual or the brake line manufacturer's instructions. Typically, this is between 12-18 ft-lbs, but always verify.
- Hard Line Connection: Connect the other end of the braided line to the hard line on the chassis. Ensure the fitting is properly tightened to prevent leaks.
- Repeat: Repeat steps 3-7 for the remaining brake lines.
- Bleeding the Brakes: This is the most crucial step. After installing the new lines, you must bleed the brake system to remove any air that may have entered. Start with the caliper furthest from the master cylinder and work your way closer. Use a pressure bleeder or the traditional two-person method. Bleed each caliper until clear, bubble-free fluid flows out.
- Final Inspection: After bleeding the brakes, carefully inspect all connections for leaks. Top off the brake fluid reservoir to the appropriate level. Pump the brake pedal several times to check for a firm pedal feel.
- Test Drive: Perform a test drive in a safe environment to ensure the brakes are functioning properly. Pay attention to the pedal feel and stopping distance. If you notice any abnormalities, such as a soft pedal or increased stopping distance, re-inspect the brake system immediately.
Troubleshooting Common Issues
- Leaks: The most common problem is leaks around the banjo bolt connections. This is usually due to damaged or improperly installed sealing washers, or incorrect torque. Replace the washers and ensure the bolt is torqued to the correct specification.
- Soft Pedal: A soft pedal indicates air in the brake lines. Re-bleed the brakes thoroughly. If the problem persists, check for leaks or a faulty master cylinder.
- Uneven Braking: Uneven braking can be caused by contaminated brake pads, a faulty caliper, or air in only one brake line. Inspect the pads and calipers and bleed the brakes.
Upgrading to banjo bolt style braided brake lines is a worthwhile investment for any 240SX owner looking to improve their braking performance. By understanding the principles behind these upgrades and following proper installation procedures, you can significantly enhance your car's stopping power and overall driving experience. Remember to always prioritize safety and consult a qualified mechanic if you have any doubts or concerns. Good luck!