240sx Carbon Fiber Door Panels
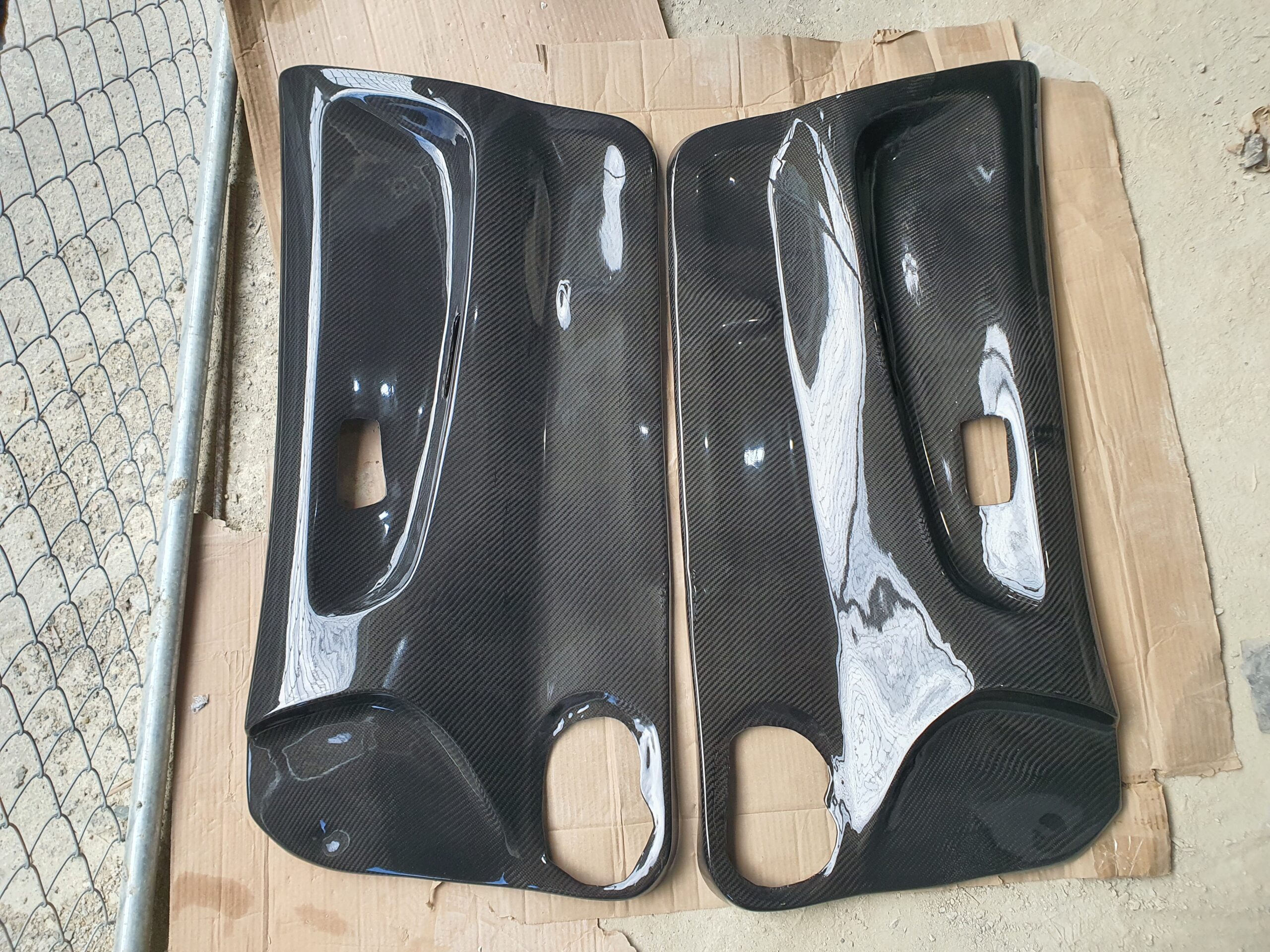
The 240SX, a beloved chassis in the drift and JDM tuning communities, often sees extensive modifications to improve performance and aesthetics. Among these, carbon fiber door panels are a popular upgrade, offering weight reduction, enhanced stiffness, and a distinct visual appeal. This article delves into the construction, benefits, and technical considerations surrounding carbon fiber door panels for the 240SX.
Understanding Carbon Fiber Composition and Manufacturing
Carbon fiber isn't just a single material; it's a composite, meaning it's made up of two or more constituent materials with significantly different physical or chemical properties that, when combined, produce a material with characteristics different from the individual components. In this case, the two primary components are carbon fibers and a resin matrix. The carbon fibers provide the strength and stiffness, while the resin holds the fibers together and distributes the load.
Carbon Fiber Strands and Weaves
Carbon fiber itself is created by heating strands of a precursor material, often polyacrylonitrile (PAN), pitch, or rayon, in an oxygen-free environment. This process carbonizes the material, leaving behind long, thin strands of nearly pure carbon. These strands are then bundled together into tows, which are rated by the number of filaments they contain (e.g., 3K, 6K, 12K). For automotive applications, 3K and 6K tows are common due to their balance of strength, flexibility, and aesthetic appeal.
These tows are then woven into various patterns, with the most common being plain weave, twill weave, and satin weave. The weave pattern significantly impacts the material's properties and appearance.
- Plain Weave: A simple over-under pattern, offering good stability and crimp. It is commonly used in applications needing equal strength in warp and weft direction.
- Twill Weave: Characterized by a diagonal rib pattern, twill weave offers better drapeability than plain weave, making it easier to conform to complex shapes. It also has a distinctive aesthetic.
- Satin Weave: Satin weaves have fewer interlacings, resulting in a smoother surface and better drapeability than twill. However, they can be more prone to distortion.
Resin Systems: The Binding Agent
The resin system is crucial for transferring stress between the carbon fibers and protecting them from environmental damage. Common resin systems include epoxy, polyester, and vinyl ester. Epoxy is generally preferred for high-performance applications due to its superior strength, stiffness, and temperature resistance. The resin is applied either before or during the manufacturing process to saturate the carbon fiber layers.
Manufacturing Processes: From Raw Materials to Finished Product
Several manufacturing processes are used to create carbon fiber door panels, each with its own advantages and disadvantages. The most common methods include:
- Wet Layup: This is the simplest and most affordable method. Carbon fiber fabric is laid into a mold and then saturated with resin by hand. It's suitable for low-volume production and complex shapes but can result in lower fiber volume fraction and higher void content compared to other methods.
- Vacuum Bagging: A vacuum bag is placed over the layup, and a vacuum is drawn to compress the layers and remove excess resin and air. This results in a higher fiber volume fraction, reduced void content, and improved part quality compared to wet layup.
- Vacuum Infusion: Dry carbon fiber fabric is placed in a mold, covered with a vacuum bag, and resin is drawn through the fabric using vacuum pressure. This method offers excellent fiber volume fraction and reduced void content, producing lightweight and strong parts. It also minimizes resin waste.
- Prepreg: Pre-impregnated carbon fiber (prepreg) fabric is used, which already contains a controlled amount of resin. The prepreg is laid into a mold and cured under heat and pressure, resulting in very high fiber volume fraction and minimal void content. Prepreg is the most expensive method but produces the highest quality parts.
Benefits of Carbon Fiber Door Panels on a 240SX
Replacing the OEM steel door panels with carbon fiber counterparts offers several advantages, primarily focused on weight reduction and performance enhancement.
Weight Reduction: A Significant Advantage
The most significant benefit is weight reduction. Steel door panels are relatively heavy, contributing to the overall vehicle weight and negatively impacting handling, acceleration, and braking. Carbon fiber is significantly lighter than steel, typically offering a 50-70% weight reduction. This translates to improved performance characteristics:
- Improved Acceleration: Less weight means the engine has less mass to accelerate, resulting in quicker acceleration times.
- Shorter Braking Distances: Reduced weight allows the brakes to stop the car more effectively, leading to shorter braking distances.
- Enhanced Handling: Lighter weight improves the car's responsiveness to steering inputs and reduces body roll, resulting in better handling.
- Improved Fuel Efficiency: Although the impact may be small, reduced weight can contribute to slightly improved fuel efficiency.
Increased Stiffness and Rigidity
Carbon fiber is not only lightweight but also incredibly strong and rigid. Replacing steel door panels with carbon fiber can increase the overall rigidity of the chassis, which can improve handling and responsiveness. While door panels don't contribute significantly to overall chassis stiffness compared to components like roll cages or strut tower bars, the added rigidity can be noticeable, especially in a car with a relatively flexible chassis like the 240SX.
Aesthetics: A Motorsport-Inspired Look
Beyond the performance benefits, carbon fiber door panels offer a distinct aesthetic upgrade. The exposed carbon fiber weave provides a motorsport-inspired look that is both visually appealing and indicative of the car's performance focus. They contribute to a more aggressive and track-ready appearance.
Technical Considerations and Challenges
While carbon fiber door panels offer numerous benefits, there are also several technical considerations and potential challenges to keep in mind.
Fitment and Installation
Proper fitment is crucial for both aesthetic and functional reasons. Aftermarket carbon fiber parts can sometimes have fitment issues, requiring modifications for proper installation. It's important to choose reputable manufacturers known for producing high-quality parts with accurate dimensions. The installation process may involve transferring hardware from the OEM door panels, such as hinges, latches, and window regulators. Careful attention to detail and proper alignment are essential for a successful installation.
Durability and Impact Resistance
While carbon fiber is strong in tension and bending, it can be brittle and susceptible to impact damage. Unlike steel, which can deform and absorb impact energy, carbon fiber can crack or shatter upon impact. This is particularly important to consider in a car that is driven aggressively or used for motorsports. Some manufacturers reinforce their door panels with Kevlar or other impact-resistant materials to improve durability. However, even reinforced carbon fiber is generally less impact-resistant than steel.
UV Resistance and Environmental Degradation
Epoxy resin, which is commonly used in carbon fiber composites, can be susceptible to degradation from ultraviolet (UV) radiation. Prolonged exposure to sunlight can cause the resin to yellow, crack, and lose its structural integrity. To mitigate this, carbon fiber parts are typically coated with a UV-resistant clear coat. However, even with a clear coat, regular maintenance and protection from direct sunlight are recommended to prolong the lifespan of the carbon fiber.
Cost and Value
Carbon fiber door panels are generally more expensive than OEM steel door panels or fiberglass alternatives. The higher cost reflects the expensive materials, complex manufacturing processes, and skilled labor required to produce high-quality carbon fiber parts. When considering the cost, it's important to weigh the benefits of weight reduction, stiffness, and aesthetics against the potential drawbacks of impact resistance and UV degradation. The value proposition ultimately depends on the individual's priorities and budget.
Integration with Safety Systems
OEM door panels often incorporate side impact beams and other safety features designed to protect occupants in the event of a collision. It's crucial to ensure that the carbon fiber door panels either retain these safety features or offer comparable protection. Some aftermarket manufacturers may not prioritize safety to the same extent as OEM manufacturers, so it's important to research and choose products that have been properly tested and engineered for safety. Simply replacing the door skin might compromise the energy absorbing capabilities of the door.
In conclusion, carbon fiber door panels represent a significant upgrade for the 240SX, offering weight reduction, enhanced stiffness, and a distinctive aesthetic. However, it's essential to carefully consider the technical aspects, potential challenges, and cost before making the investment. Choosing reputable manufacturers, ensuring proper fitment, and maintaining the parts properly are crucial for maximizing the benefits and ensuring long-term satisfaction.