240sx Cranks But Won't Start: Troubleshooting Guide
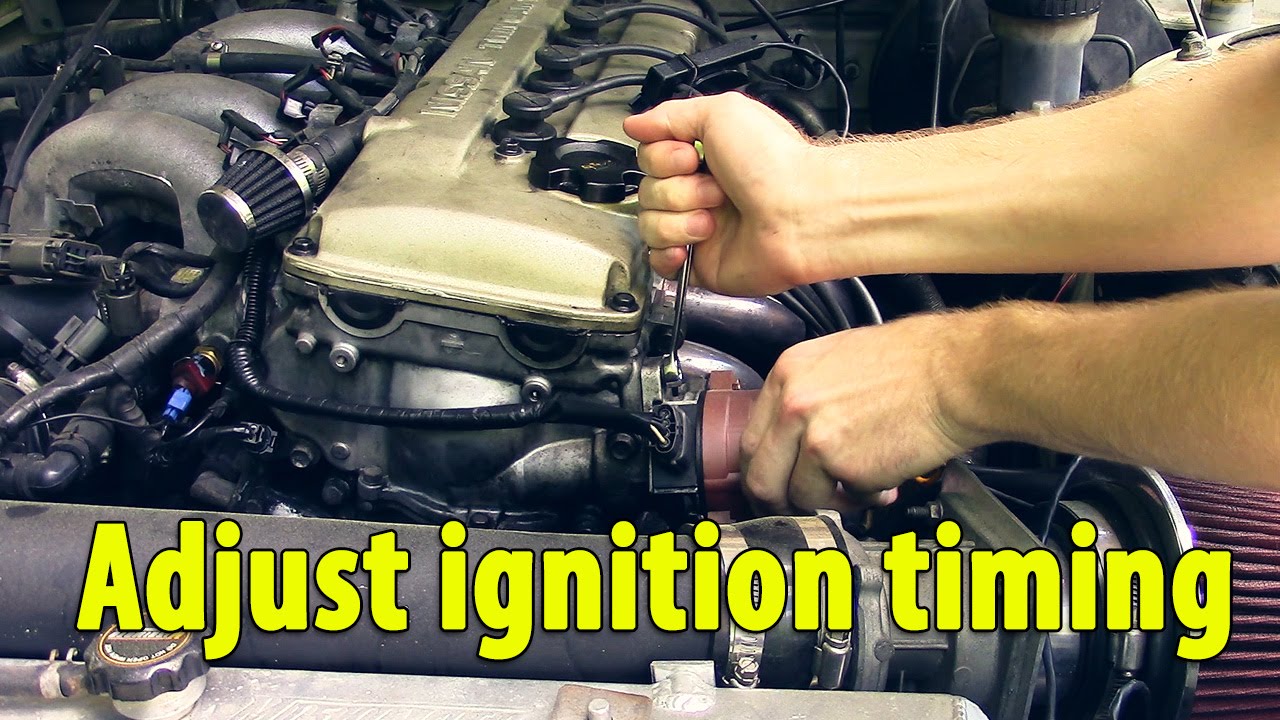
Okay, so your 240SX is cranking but stubbornly refusing to fire up. This is a frustrating situation, but don't panic. This guide will walk you through a logical troubleshooting process to pinpoint the problem. We'll cover the most common causes, focusing on diagnosis and potential solutions. We're assuming you've already checked the obvious – like making sure there's gas in the tank. Let's get started.
Understanding the Basics: What's Needed for Combustion
Before diving into specific components, let's review the fundamental requirements for an internal combustion engine to start. You need the "fire triangle":
- Fuel: A properly mixed air/fuel ratio in the cylinders.
- Spark: A strong spark at the spark plugs to ignite the mixture.
- Compression: Adequate compression in the cylinders to create a high-pressure environment for combustion.
If any of these are missing or insufficient, the engine won't start. We'll systematically examine each.
Fuel System Diagnostics
1. Fuel Pump Check
The fuel pump is responsible for delivering fuel from the tank to the engine. A common failure point in older vehicles. You should check to see if the fuel pump is priming. You can listen by turning the key to the "ON" position (not starting). You should hear a brief whirring sound from the rear of the car for 1-2 seconds. If you hear nothing, the fuel pump might be dead, not getting power, or have a bad ground.
Testing the Fuel Pump Relay: Locate the fuel pump relay (consult your 240SX repair manual for its exact location). You can try swapping it with a known working relay (like the horn relay, often the same type). If the car starts after swapping, the relay was the culprit. You can also use a multimeter to test the relay for continuity and proper operation.
Checking Fuel Pump Voltage: With the key in the "ON" position, use a multimeter to check for voltage at the fuel pump connector. You should see approximately 12V. If there's no voltage, trace the wiring back to the fuel pump relay and ignition switch, looking for breaks or corrosion.
Fuel Pump Continuity Test: Disconnect the fuel pump connector and use a multimeter to measure the resistance across the pump terminals. A reading of very low resistance or zero ohms indicates a shorted pump. An open circuit (infinite resistance) suggests a broken pump. Consult a repair manual for specific resistance values.
2. Fuel Filter Inspection
A clogged fuel filter can restrict fuel flow, preventing the engine from starting. It's a relatively inexpensive part, so consider replacing it as part of regular maintenance, especially if you suspect fuel system issues. Location is usually in the fuel line after the fuel tank and before the fuel rail.
Fuel Pressure Test: This is a more advanced test requiring a fuel pressure gauge. Connect the gauge to the Schrader valve (test port) on the fuel rail (usually located on the engine near the injectors). With the fuel pump running (you may need to bypass the relay or use a scan tool to activate the pump), check the fuel pressure. Consult your service manual for the correct pressure specifications. Low fuel pressure indicates a problem with the fuel pump, fuel filter, fuel pressure regulator, or a fuel line restriction.
3. Fuel Injector Functionality
The fuel injectors spray fuel into the intake manifold or directly into the cylinders (depending on the 240SX model). If they're clogged or not firing correctly, the engine won't start.
Injector Pulse Test: Use a noid light to check if the injectors are receiving a signal from the ECU (Engine Control Unit). Disconnect an injector connector and plug in the noid light. Crank the engine. The noid light should flash if the ECU is sending a pulse to the injector. If the light doesn't flash, there's a problem with the wiring to the injectors, the ECU, or the crank/camshaft position sensors (which provide the timing signal for the injectors).
Injector Resistance Test: Use a multimeter to measure the resistance across the injector terminals. This test verifies the integrity of the injector's internal coil. Compare the readings to the specifications in your repair manual. Out-of-range resistance values indicate a faulty injector.
Injector Cleaning: If the injectors are suspected of being clogged, they can be professionally cleaned using ultrasonic cleaning equipment. You can also try using fuel injector cleaner additives, but they're often not as effective for severe clogs.
Ignition System Troubleshooting
1. Spark Plug Inspection
Remove the spark plugs and inspect them for wear, damage, or fouling. Look for signs of oil fouling (wet and black), carbon fouling (dry and black), or excessive wear on the electrodes. A healthy spark plug should have a light tan or gray color. If the plugs are heavily fouled, clean or replace them.
Testing Spark: Remove a spark plug, connect it to the spark plug wire, and ground the spark plug body against the engine block. Have someone crank the engine while you observe the spark plug. A strong, blue spark is desirable. A weak, yellow spark, or no spark at all, indicates an ignition system problem.
2. Distributor (If Equipped) and Ignition Coil
Some older 240SX models use a distributor, while newer models have coil-on-plug (COP) ignition. For distributor-equipped models, check the distributor cap and rotor for cracks, corrosion, or damage. Replace them if necessary.
Ignition Coil Testing: Use a multimeter to measure the primary and secondary resistance of the ignition coil. Compare the readings to the specifications in your repair manual. An out-of-range resistance value indicates a faulty coil. If you have COP, test each coil individually.
3. Crankshaft and Camshaft Position Sensors
These sensors provide the ECU with information about the engine's position and speed. If these sensors fail, the ECU won't know when to fire the injectors or spark plugs. A scan tool is invaluable for diagnosing these sensors. OBDII scanners can read codes from the Engine Control Unit (ECU) that can tell you what is happening in the system.
Sensor Testing: Use a multimeter to check the resistance and output voltage of the crankshaft and camshaft position sensors. Refer to your repair manual for specific testing procedures and values. Erratic or absent signals indicate a faulty sensor.
Compression Check
While less likely to cause a no-start condition *unless* there's catastrophic engine damage, low compression can make it difficult for the engine to fire. If you've exhausted the fuel and ignition system checks, a compression test is a worthwhile step.
Performing a Compression Test: Remove all spark plugs. Disable the fuel injection system (remove the fuel pump relay). Insert a compression tester into each spark plug hole, one at a time. Crank the engine for several seconds while observing the pressure reading on the tester. Repeat for each cylinder. Compare the readings to the specifications in your repair manual. Low compression in one or more cylinders indicates a problem with the piston rings, valves, or cylinder head gasket.
Other Potential Causes
1. Immobilizer System
Some 240SX models have an immobilizer system that prevents the engine from starting if the correct key is not used. If the immobilizer is malfunctioning, it can prevent the engine from starting. Consult your owner's manual or a qualified technician for immobilizer troubleshooting.
2. ECU Malfunction
Although rare, the ECU can fail, preventing the engine from starting. If you've checked everything else and still can't find the problem, consider having the ECU tested by a professional.
3. Wiring and Connectors
Carefully inspect all wiring and connectors in the fuel and ignition systems for damage, corrosion, or loose connections. Clean and tighten any suspect connections. Use a wiring diagram to trace circuits and identify potential problem areas.
Grounding Issues: Pay special attention to engine and chassis ground connections. A poor ground connection can cause a variety of electrical problems, including a no-start condition. Clean and tighten all ground connections.
Using a Scan Tool (OBDII)
A scan tool is an invaluable tool for diagnosing engine problems. Connect a scan tool to the OBDII port (usually located under the dashboard). Read the Diagnostic Trouble Codes (DTCs). These codes can provide valuable clues about the cause of the no-start condition. Research the codes and follow the recommended troubleshooting procedures.
Live Data Monitoring: Scan tools can also display live data from the engine sensors. This can help you identify sensors that are not functioning correctly. For example, you can monitor the crankshaft position sensor signal, the fuel injector pulse width, and the air/fuel ratio. Knowing to use OBDII live data will help you troubleshoot this situation.
Final Thoughts
Troubleshooting a no-start condition can be challenging, but by following a systematic approach and using the appropriate tools, you can usually pinpoint the problem. Remember to consult your 240SX repair manual for specific procedures and specifications. If you're not comfortable performing any of these tests, it's best to consult a qualified mechanic. Good luck!