448 Tolland Turnpike Manchester Ct 06042
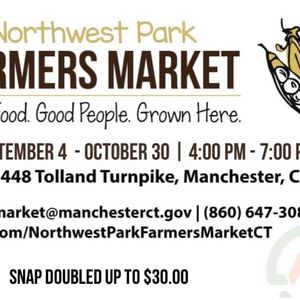
Let's embark on a hypothetical exploration, a deep dive into the operational characteristics of a facility located at 448 Tolland Turnpike, Manchester, CT 06042. While this analysis will be purely speculative, we can use publicly available information, industry best practices, and engineering principles to paint a plausible picture of the processes, systems, and considerations that might be in play at such a location. For the purposes of this exercise, we will assume the property houses a mid-sized light manufacturing facility focusing on precision components.
Facility Overview: A Hypothetical Manufacturing Plant
Imagine a single-story structure of approximately 50,000 square feet. The building's core is likely constructed of pre-engineered steel framing, chosen for its cost-effectiveness and rapid construction. The exterior walls might be precast concrete panels or insulated metal panels, providing thermal efficiency and fire resistance. The roof would be a flat or slightly sloped built-up roofing system, designed for durability and weather protection. Landscaping around the perimeter will likely include grass, shrubs and trees to improve aesthetics and help manage storm water runoff.
Internally, the facility can be divided into several distinct zones:
- Manufacturing Floor: The largest area, dedicated to the machining, assembly, and testing of components.
- Warehouse: For storage of raw materials, work-in-progress, and finished goods.
- Quality Control Laboratory: Equipped with precision measurement instruments for dimensional and material analysis.
- Engineering and Design Office: A space for engineers to design, prototype, and refine manufacturing processes.
- Administrative Offices: Housing management, sales, and support staff.
- Maintenance Area: A dedicated area for equipment repairs and preventative maintenance.
- Shipping and Receiving Dock: An area for the loading and unloading of trucks.
Manufacturing Processes: Precision Machining
Assuming our hypothetical plant manufactures precision components, the manufacturing floor would be populated with a variety of sophisticated equipment. Computer Numerical Control (CNC) machines would be central to the process. These machines, including lathes, milling machines, and grinders, use computer-controlled cutting tools to shape raw materials into finished parts. The CNC machines are likely networked together, allowing for centralized programming and monitoring. Common materials being machined could include aluminum alloys, stainless steel, and various engineering plastics.
The manufacturing process likely follows these steps:
- Material Procurement: Raw materials are sourced from suppliers and delivered to the warehouse.
- Cutting and Machining: Materials are cut and shaped using CNC machines, following detailed engineering drawings.
- Deburring and Finishing: Parts are deburred to remove sharp edges and may undergo surface finishing processes like anodizing or powder coating.
- Quality Inspection: Parts are inspected for dimensional accuracy, surface finish, and material properties. This is a critical step.
- Assembly: Components are assembled into sub-assemblies or finished products.
- Testing: Finished products are tested to ensure they meet performance specifications.
- Packaging and Shipping: Products are packaged and shipped to customers.
CNC Machine Technology
A closer look at the CNC machining process reveals a complex interplay of software, electronics, and mechanics. CNC machines use G-code, a programming language that instructs the machine on the precise movements of the cutting tool. The machine's control system interprets the G-code and translates it into electrical signals that drive servo motors. These motors, in turn, control the position and speed of the cutting tool. The accuracy of the machining process depends on the precision of the servo motors, the rigidity of the machine frame, and the quality of the cutting tools. The importance of regular calibration and maintenance cannot be overstated. Modern CNC machines often incorporate sensors and feedback systems that monitor the cutting process and adjust parameters in real time to optimize performance and prevent errors. This is particularly important when working with tight tolerances or complex geometries.
Environmental Considerations: Sustainability and Compliance
Even in a hypothetical scenario, environmental responsibility is paramount. The facility would need to comply with all applicable federal, state, and local environmental regulations. This includes managing waste streams, controlling air emissions, and minimizing water consumption.
- Waste Management: The facility would generate various waste streams, including metal shavings, cutting fluids, and packaging materials. These wastes would need to be properly sorted, stored, and disposed of in accordance with environmental regulations. Recycling programs would be implemented to reduce the amount of waste sent to landfills.
- Air Emissions: Machining processes can generate air emissions, such as volatile organic compounds (VOCs) from cutting fluids and particulate matter from grinding operations. The facility would need to implement measures to control these emissions, such as using enclosed machining systems, installing air filtration equipment, and monitoring air quality.
- Water Consumption: Machining processes often require the use of water for cooling and cleaning. The facility would need to implement water conservation measures, such as using recirculating water systems and minimizing water waste. Stormwater runoff would also need to be managed to prevent pollution.
- Energy Efficiency: Energy consumption is a significant operating cost for any manufacturing facility. The facility would implement energy efficiency measures, such as using high-efficiency lighting, installing energy-efficient HVAC systems, and optimizing manufacturing processes to reduce energy consumption.
The facility might also consider implementing sustainable manufacturing practices, such as using recycled materials, reducing waste generation, and minimizing energy consumption. These practices can not only reduce the facility's environmental footprint but also improve its bottom line.
Building Systems: HVAC, Electrical, and Plumbing
The facility would rely on a number of critical building systems to ensure a safe, comfortable, and productive work environment.
- HVAC System: A heating, ventilation, and air conditioning (HVAC) system would be essential for maintaining a comfortable temperature and air quality throughout the facility. The system would likely include rooftop units for cooling and heating, as well as air handlers and ductwork for distributing conditioned air. The system would need to be properly sized to meet the heating and cooling demands of the facility, and it would need to be regularly maintained to ensure optimal performance. Considerations for the machining area include proper ventilation to remove fumes and maintain a consistent temperature for machine accuracy.
- Electrical System: The facility would require a robust electrical system to power the machinery, lighting, and other equipment. The system would include a main electrical panel, distribution panels, and branch circuits. The system would need to be properly sized to meet the electrical demands of the facility, and it would need to be regularly inspected and maintained to ensure safety. Backup power, such as a generator, may be installed for critical equipment in case of power outages.
- Plumbing System: The facility would require a plumbing system to provide potable water for drinking, sanitation, and process use. The system would include water supply lines, drainage lines, and plumbing fixtures. The system would need to be properly sized to meet the water demands of the facility, and it would need to be regularly inspected and maintained to prevent leaks and other problems.
Fire Suppression System
A critical safety feature is the fire suppression system. This would likely consist of a sprinkler system throughout the building, supplemented by fire extinguishers and fire alarms. The sprinkler system would be designed to automatically suppress fires, protecting the building and its occupants. The fire alarm system would alert occupants to the presence of a fire, allowing them to evacuate safely. The system will be compliant with local fire codes, which would dictate system specifics.
Security System: Protecting Assets and Personnel
Security is a major concern for any manufacturing facility. The facility at 448 Tolland Turnpike would need to implement a comprehensive security system to protect its assets and personnel.
- Perimeter Security: The facility would be surrounded by a fence or other barrier to prevent unauthorized access. Security cameras would be installed around the perimeter to monitor activity and deter intruders.
- Access Control: Access to the facility would be controlled through a card access system or biometric scanner. This would ensure that only authorized personnel are allowed to enter the building.
- Intrusion Detection: An intrusion detection system would be installed to detect unauthorized entry into the building. The system would include door and window sensors, motion detectors, and other sensors.
- Surveillance System: A network of security cameras would be installed throughout the facility to monitor activity and record evidence in case of a security breach.
- Alarm System: An alarm system would be installed to alert security personnel to any security breaches. The system would include audible and visual alarms.
"The overall design and operation of a facility like this hinges on a delicate balance of productivity, efficiency, safety, and environmental responsibility."
In conclusion, while this analysis is speculative, it provides a plausible overview of the systems and considerations that might be in play at a light manufacturing facility located at 448 Tolland Turnpike, Manchester, CT 06042. It showcases the complexity of modern manufacturing and highlights the importance of careful planning, engineering, and maintenance.