A Guide To The Fabrication And Sourcing Of Custom Parts For The Nissan 240sx
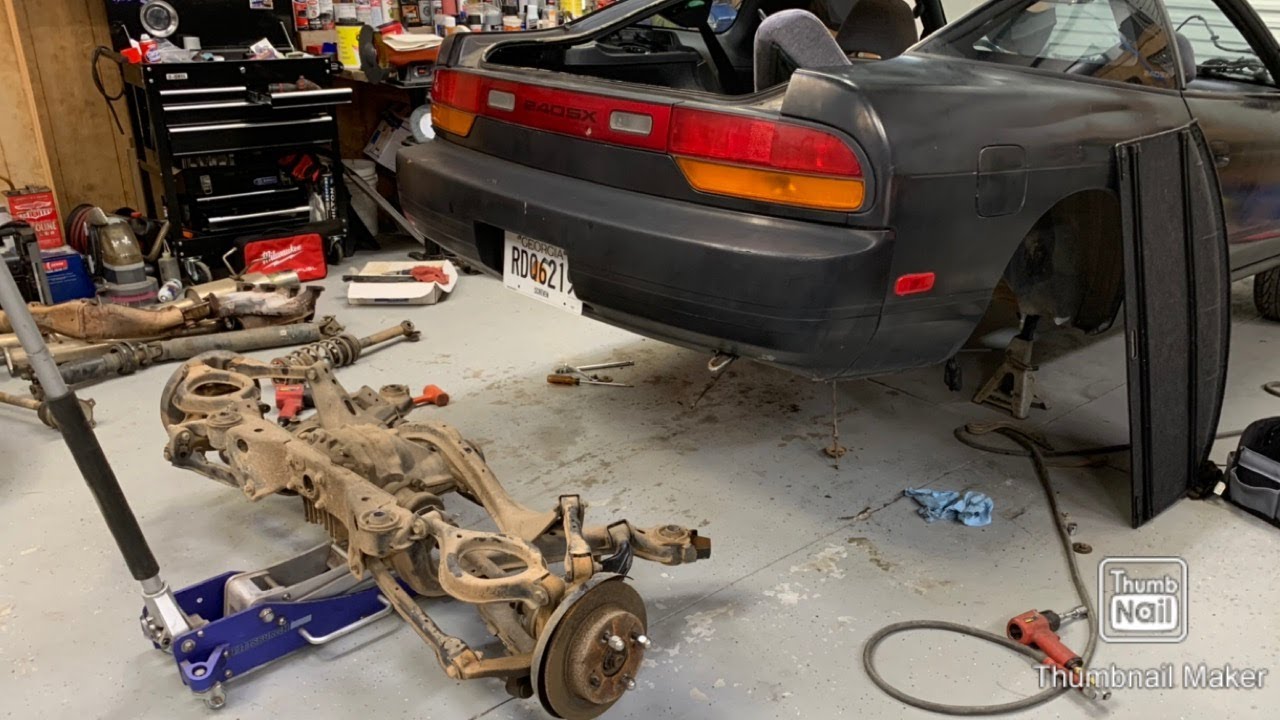
So, you're looking to tackle some custom work on your Nissan 240SX? Excellent choice! These cars are fantastic platforms for modification and personalization. But let's be honest, sometimes the parts you need just aren't readily available. Whether you're chasing a specific aesthetic, improving performance, or replacing something NLA (No Longer Available), custom fabrication and sourcing become essential skills. This guide will walk you through some common challenges and offer practical solutions to get you closer to your 240SX dream.
Problem: Finding Discontinued or NLA Parts
The 240SX is a classic, but its age means some parts are becoming increasingly difficult, if not impossible, to find through traditional channels. Common culprits include body panels, interior trim pieces, and specific engine components. This is a problem faced by almost every 240SX enthusiast sooner or later.
Solution 1: Exploring the Aftermarket and Salvage Yards
Before diving into custom fabrication, exhaust your readily available options. The aftermarket for the 240SX is still surprisingly robust, with many companies reproducing or offering improved versions of original parts. Websites like Enjuku Racing, FR Sport, and even eBay can be treasure troves. Don't overlook specialty forums dedicated to the 240SX, as members often sell used or surplus parts.
Speaking of used parts, salvage yards (aka junkyards) can be a goldmine. Use online databases like Car-Part.com to search for yards near you and inventory. Pro Tip: Call ahead and confirm the part's availability and condition before making the trip. Be prepared to do some digging and possibly some disassembly yourself.
Solution 2: 3D Printing as a Viable Option
For smaller, non-structural components, 3D printing is becoming an increasingly viable option. Interior trim pieces, custom gauge pods, or even small brackets can be designed and printed relatively inexpensively. Services like Shapeways and Treatstock allow you to upload your own designs or choose from existing models.
Tools/Materials Needed:
- Digital Calipers (for accurate measurements)
- CAD Software (like Fusion 360 - often available with hobbyist licenses)
- 3D Printing Service (or access to a 3D printer)
Solution 3: Custom Fabrication - Welding, Machining, and More
Sometimes, there's just no way around it: you need to fabricate a part from scratch. This is where things get interesting (and potentially expensive!). This usually involves welding, machining, or a combination of both. The best approach depends on the part's complexity, materials, and required precision.
Problem: Adapting Parts from Other Vehicles
Another common challenge is adapting parts from other vehicles to fit your 240SX. This might be necessary for brake upgrades, suspension modifications, or engine swaps. While often cost-effective, it requires careful planning and execution.
Solution 1: Research and Community Knowledge
Before attempting any adaptation, thoroughly research what others have done. 240SX forums are filled with build threads and guides detailing successful swaps and modifications. Learn from their experiences – the pitfalls to avoid, the necessary parts, and the potential challenges.
Solution 2: Accurate Measurements and CAD Modeling
Accurate measurements are crucial for any successful adaptation. Invest in a good set of digital calipers and measuring tools. If the adaptation is complex, consider creating a CAD model of the original and adapted parts to ensure proper fitment. This will help identify potential interference issues early on.
Tools/Materials Needed:
- Digital Calipers
- Measuring Tape
- CAD Software (optional, but highly recommended)
- Welder (if modifications require welding)
- Grinder with cutting and grinding discs
Solution 3: Professional Fabrication Assistance
For complex adaptations, don't hesitate to seek professional help from a fabrication shop. They have the expertise and equipment to perform precision welding, machining, and other fabrication tasks. Discuss your project in detail, provide accurate measurements and drawings, and get a clear understanding of the cost involved. A reputable shop can save you time, money, and frustration in the long run.
Problem: Achieving the Desired Aesthetic
Custom fabrication isn't just about functionality; it's also about aesthetics. Maybe you want a custom widebody kit, a unique spoiler, or a flush-mounted fuel filler. Achieving the desired look requires skill and attention to detail.
Solution 1: Sketching and Design Mockups
Before cutting or welding anything, create detailed sketches and design mockups of your desired aesthetic. Use Photoshop or other image editing software to visualize how the custom parts will look on your car. This will help refine your design and identify potential issues before they become costly mistakes.
Solution 2: Working with Fiberglass or Carbon Fiber
Fiberglass and carbon fiber are popular materials for creating custom body panels and aerodynamic components. They offer a good balance of strength, weight, and moldability. However, working with these materials requires specialized skills and equipment. Consider taking a workshop or seeking guidance from experienced fabricators.
Tools/Materials Needed (for Fiberglass):
- Fiberglass Cloth
- Resin and Hardener
- Mixing Cups and Stir Sticks
- Brushes and Rollers
- Mold Release Agent
- Sandpaper (various grits)
- Respirator and Gloves
Solution 3: Attention to Detail and Finishing
The key to a successful custom aesthetic is attention to detail and proper finishing. Ensure all surfaces are smooth, free of imperfections, and properly prepped before painting. Use high-quality paints and clear coats for a durable and professional finish. Consider hiring a professional painter for best results. Cost estimates: A professional paint job can range from $500 to $5000+ depending on the complexity and quality of the materials used.
Sourcing Considerations and Final Thoughts
When sourcing parts for your custom project, consider the following:
- Material Selection: Choose materials that are appropriate for the application and environment. Consider factors like strength, weight, corrosion resistance, and cost.
- Tolerances and Precision: Specify the required tolerances and precision for any machined or fabricated parts. This is crucial for proper fitment and functionality.
- Vendor Reputation: Research the reputation of any vendors or fabricators you're considering. Look for reviews, testimonials, and examples of their previous work.
- Budget: Custom fabrication can be expensive. Set a realistic budget and be prepared to adjust it as needed. Factor in the cost of materials, labor, and any necessary tools or equipment.
Working on a 240SX offers a unique opportunity to express your creativity and personalize your ride. While sourcing and fabricating custom parts can be challenging, the rewards are well worth the effort. With careful planning, research, and execution, you can create a truly one-of-a-kind 240SX that reflects your individual style and preferences. Don't be afraid to ask for help from the 240SX community – we're all in this together! Good luck, and happy wrenching!