Braided Brake Line Material And Fitting Specifications
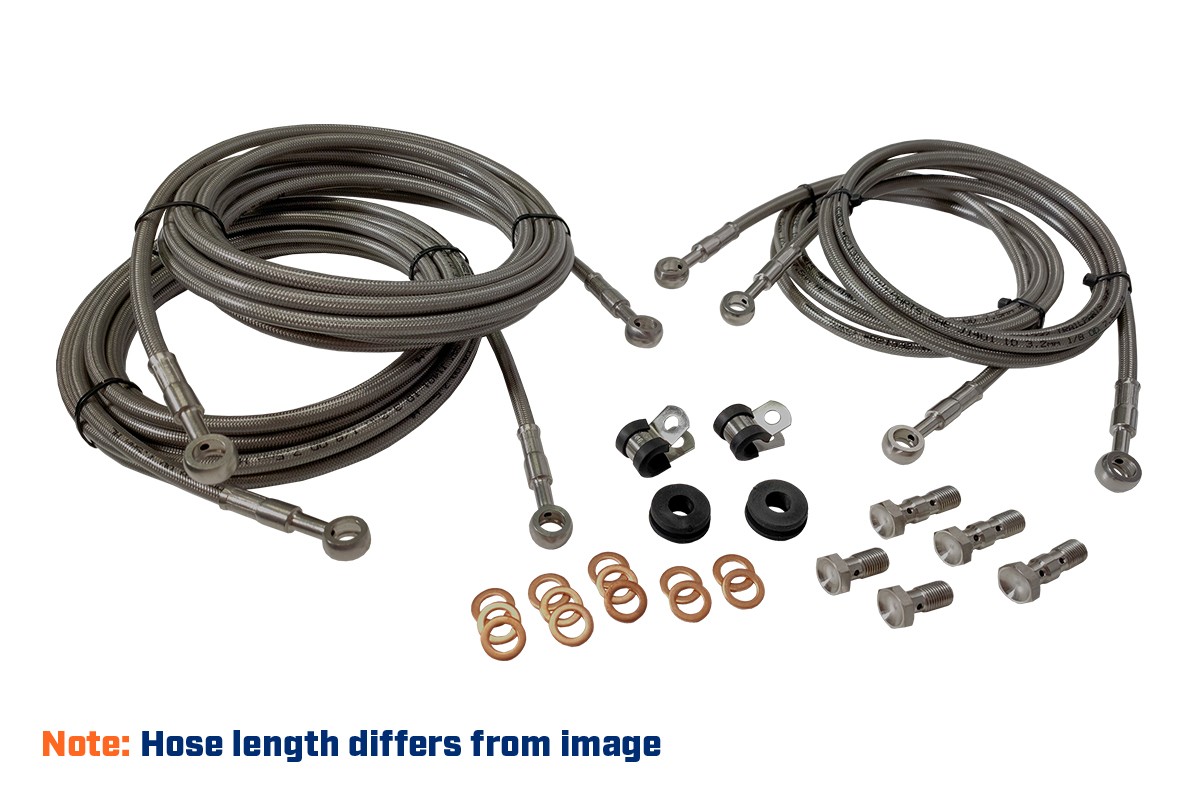
Braided stainless steel brake lines are a popular upgrade for many vehicles, from daily drivers to high-performance machines. They offer a firmer pedal feel and more consistent braking performance compared to traditional rubber hoses, especially under hard braking conditions. However, like any automotive component, they can sometimes experience issues. This article aims to provide a practical guide to understanding braided brake line materials, fitting specifications, common problems, and effective solutions.
Understanding Braided Brake Line Materials
The core of a braided brake line typically consists of a Teflon (PTFE) or a similar low-friction polymer inner hose. This material is highly resistant to brake fluid, high temperatures, and pressure. Surrounding this inner hose is a stainless steel braid, which is the signature feature of these lines. The braid provides significant reinforcement, preventing the hose from expanding under pressure. This is where the performance benefit comes from – reduced expansion translates directly to a firmer, more responsive brake pedal.
Inner Hose Materials: PTFE vs. Other Polymers
While PTFE (Teflon) is the most common, some braided lines utilize alternative polymers. PTFE boasts excellent chemical resistance and a wide operating temperature range. However, other materials may offer slightly improved flexibility or abrasion resistance, depending on the manufacturer and intended application. Always check the manufacturer's specifications to understand the exact material used in your brake lines.
Stainless Steel Braid: Grades and Construction
The quality of the stainless steel braid is crucial. Higher-grade stainless steel offers better corrosion resistance and durability. The braid's construction also matters – a tighter weave generally provides greater strength and resistance to expansion. Inspect the braid for any signs of damage, such as fraying or corrosion. Any damage to the braid can compromise the line's integrity.
Brake Line Fitting Specifications and Identification
Fittings are the connection points between the brake lines, calipers, and master cylinder. Proper fitting selection and installation are critical for leak-free and safe braking.
Common Fitting Types: AN, SAE, and Metric
Brake line fittings typically adhere to one of three standards: AN (Army-Navy), SAE (Society of Automotive Engineers), or Metric. AN fittings are commonly used in racing and high-performance applications. SAE fittings are prevalent in American-made vehicles, while Metric fittings are common in European and Japanese cars. It's crucial to correctly identify the fitting type to ensure compatibility. Using the wrong fitting can lead to leaks or even catastrophic brake failure.
Flare Types: Inverted Flare vs. Bubble Flare
Within each standard, different flare types exist. Inverted flare fittings create a metal-to-metal seal within the fitting. Bubble flare fittings (also known as ISO flare) create a seal on the outside of the fitting. Mixing flare types will result in leaks. Always use the correct flare type for your application.
Identifying Fitting Sizes and Threads
Accurately determining the fitting size and thread is essential for replacement or modification. Use a thread gauge and a caliper to measure the thread pitch and diameter. It is better to purchase a fitting identification kit that contains the different sizes and thread types that may be encountered. This ensures you get the right components. Never force a fitting – if it doesn't thread smoothly, you likely have the wrong size or thread pitch.
Common Problems and Solutions with Braided Brake Lines
While braided brake lines offer numerous advantages, they are not immune to problems. Here are some typical issues and how to address them.
Leakage at Fittings
Problem: Brake fluid leaking from the fittings is a common issue. This can be due to loose fittings, damaged flares, incorrect fitting types, or contaminated sealing surfaces.
Solution: First, try tightening the fitting to the manufacturer's specified torque (if available). Be careful not to overtighten, as this can damage the fitting or the flare. If tightening doesn't solve the problem, inspect the flare for damage. Replace the brake line if the flare is damaged. Ensure you're using the correct fitting type for your application. Clean the sealing surfaces with a clean, lint-free cloth and brake cleaner before reassembling. If using AN fittings, consider replacing the sealing washers. Copper washers are single-use only.
Damaged Braid
Problem: The stainless steel braid can become damaged due to abrasion, impacts, or corrosion.
Solution: If the braid is severely damaged (e.g., frayed or significantly corroded), the brake line must be replaced. Minor surface corrosion can sometimes be addressed with a wire brush and a rust inhibitor, but this is only a temporary fix and does not guarantee the integrity of the brake line. Safety should be a top priority, and compromising on brake lines is never advisable.
Inner Hose Degradation
Problem: Over time, the inner hose can degrade due to exposure to brake fluid and heat. This can lead to swelling, cracking, or even complete failure.
Solution: Regularly inspect the brake lines for signs of degradation. If you notice any swelling, cracking, or leaking, replace the brake line immediately. The lifespan of braided brake lines can vary depending on the quality of the materials and the operating conditions, but a general rule of thumb is to replace them every 5-7 years, or sooner if you notice any signs of wear.
Incorrect Length or Routing
Problem: Using brake lines that are too short can strain the fittings and lead to leaks or failure. Improper routing can cause the lines to rub against other components, leading to abrasion and damage.
Solution: Ensure you're using the correct length brake lines for your application. When installing the lines, carefully route them to avoid contact with other components. Use clamps or brackets to secure the lines and prevent them from rubbing or chafing. Be sure to check the range of motion for the suspension and steering to prevent stretching or kinking during operation.
Tools and Approximate Repair Costs
Working on brake lines requires specific tools and knowledge. If you're not comfortable working on your brakes, it's best to consult a qualified mechanic.
Essential Tools
- Flare nut wrenches: These are specifically designed to grip brake line fittings without rounding them off.
- Torque wrench: Essential for tightening fittings to the correct torque specification.
- Thread gauge and caliper: For identifying fitting sizes and thread pitches.
- Brake line flaring tool: For creating new flares on brake lines (if necessary).
- Brake bleeder: For bleeding the brake system after replacing brake lines.
- Brake fluid: Use the correct type of brake fluid specified for your vehicle.
- Safety glasses and gloves: Always wear safety glasses and gloves when working on brake systems.
Approximate Repair Costs
The cost of replacing braided brake lines can vary depending on the make and model of your vehicle, the quality of the brake lines, and the labor rates in your area. As a general estimate:
- Braided brake line set (front and rear): $100 - $400
- Labor (installation and bleeding): $150 - $400
Therefore, you can expect to pay approximately $250 - $800 for a complete braided brake line replacement. Keep in mind that these are just estimates, and the actual cost may vary. Always get a quote from a reputable mechanic before proceeding with any repairs.
Preventative Maintenance Tips
Following these tips can help extend the life of your braided brake lines and prevent problems:
- Regularly inspect your brake lines for signs of damage, corrosion, or leaks.
- Flush your brake fluid every 2-3 years to remove contaminants and moisture.
- Avoid using harsh chemicals or abrasive cleaners on your brake lines.
- Ensure your brake lines are properly routed and secured to prevent rubbing or chafing.
- Replace your brake lines if you notice any signs of wear or degradation.
By understanding the materials, fittings, and potential issues associated with braided brake lines, you can keep your braking system in top condition and enjoy enhanced performance and safety. Remember, brakes are a critical safety component, so never compromise on quality or maintenance. If in doubt, consult a qualified mechanic.