Computational Fluid Dynamics Of 240sx Rear Diffuser Designs
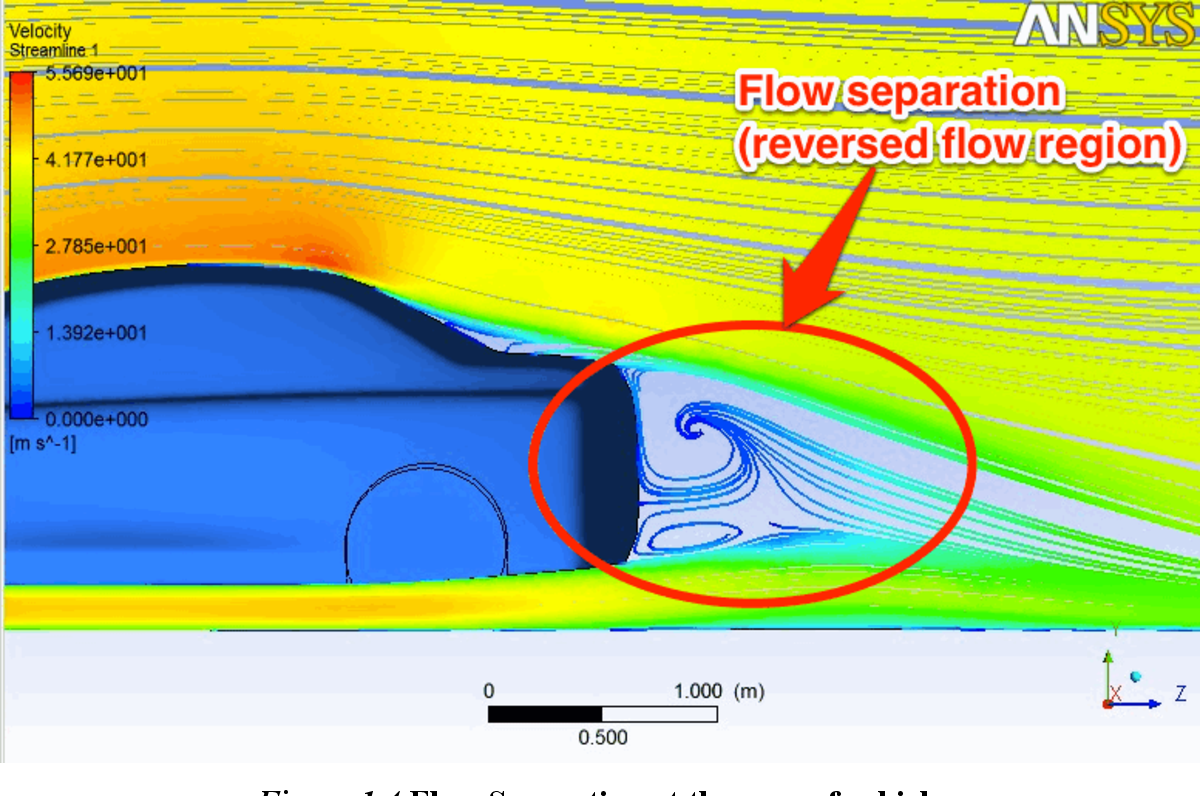
The Nissan 240SX, a beloved platform for drifting and performance enthusiasts, offers ample opportunities for aerodynamic enhancement. Among these, the rear diffuser stands out as a crucial component for optimizing airflow and increasing downforce. While off-the-shelf diffusers are readily available, understanding the underlying principles through Computational Fluid Dynamics (CFD) can lead to a more informed purchase or even inspire custom designs tailored to specific driving needs. This article explores the application of CFD in analyzing and optimizing 240SX rear diffuser designs.
Understanding Rear Diffusers and Their Importance
A rear diffuser is a carefully shaped aerodynamic device located at the rear of a vehicle, typically underneath the bumper. Its primary function is to manage the airflow exiting the underbody. As air flows underneath a car, it accelerates, creating a low-pressure area. The diffuser gradually expands this flow, reducing its velocity and increasing pressure. This controlled expansion is key to several benefits:
- Reduced Pressure Drag: By smoothly transitioning the underbody airflow back to ambient pressure, the diffuser minimizes the pressure difference between the bottom and top of the car, reducing drag.
- Increased Downforce: The diffuser effectively 'sucks' the car towards the ground. The low pressure generated under the car contributes to increased downforce, improving grip and stability, especially at higher speeds.
- Improved Airflow Management: A well-designed diffuser directs airflow away from the rear wheels and suspension components, further reducing turbulence and drag.
For 240SX owners, especially those involved in drifting or track racing, these benefits translate to improved handling, increased cornering speeds, and enhanced overall performance. However, not all diffusers are created equal. The effectiveness of a diffuser depends heavily on its design, which is where CFD comes into play.
Computational Fluid Dynamics (CFD): A Virtual Wind Tunnel
CFD is a powerful simulation technique used to analyze and predict fluid flow behavior. It involves dividing the space around an object (in this case, a 240SX with a diffuser) into a vast number of small cells, creating a computational mesh. Sophisticated mathematical equations, such as the Navier-Stokes equations, are then applied to these cells to calculate the velocity, pressure, and temperature of the fluid (air) flowing through them.
Think of CFD as a virtual wind tunnel. Instead of physically building and testing different diffuser designs, engineers can simulate their performance using software. This allows for rapid prototyping, cost savings, and a deeper understanding of the airflow dynamics.
How CFD is Used to Analyze 240SX Diffusers
The CFD process for analyzing a 240SX diffuser typically involves these steps:
- Geometry Creation: A 3D model of the 240SX, including the proposed diffuser design, is created. This model needs to be highly accurate to ensure reliable simulation results.
- Mesh Generation: The space around the car and diffuser is divided into a computational mesh, a grid of cells where the calculations will be performed. The finer the mesh, the more accurate the results, but also the greater the computational cost.
- Setup and Boundary Conditions: This involves defining the properties of the air (density, viscosity), setting the inlet velocity (simulating the car's speed), and defining boundary conditions, such as the ground and the edges of the computational domain.
- Simulation: The CFD software solves the governing equations iteratively until a stable solution is reached. This can take hours or even days, depending on the complexity of the model and the computational resources available.
- Post-Processing and Analysis: The results of the simulation are visualized and analyzed. This includes examining pressure distributions, velocity vectors, streamlines, and downforce values.
By analyzing these results, engineers can identify areas of improvement in the diffuser design. For example, they might look for:
- Flow separation: This occurs when the airflow detaches from the diffuser surface, reducing its effectiveness.
- Regions of high turbulence: Turbulence increases drag and reduces downforce.
- Pressure gradients: Analyzing pressure differences can help optimize the diffuser shape for maximum downforce generation.
Key Design Parameters for 240SX Rear Diffusers
CFD simulations can help optimize various design parameters of a 240SX rear diffuser. Some of the most important include:
- Diffuser Angle: The angle at which the diffuser expands is critical. Too small an angle, and the diffuser will be ineffective. Too large an angle, and the flow will likely separate. CFD can help determine the optimal angle for a given 240SX configuration.
- Diffuser Length: A longer diffuser generally provides more time for the airflow to expand, but it also increases drag. CFD can help balance these competing factors.
- Number of Strakes/Vanes: Strakes are vertical fins that run along the length of the diffuser. They help to channel the airflow and prevent it from spilling out to the sides. CFD can be used to optimize the number, shape, and placement of strakes.
- Height of the Diffuser: The height of the diffuser affects the volume of air that can flow through it. CFD can help determine the optimal height for maximizing downforce without significantly increasing drag.
- Transition to Upward Angle: Many diffusers incorporate an upward angle as they near the rear bumper. CFD analysis here ensures proper airflow transition to minimize pressure drag, and also help manage flow around the rear bumper and exhaust.
Optimizing these parameters through trial and error in the real world would be extremely time-consuming and expensive. CFD provides a much more efficient and cost-effective way to explore different design options.
Benefits of Using CFD for 240SX Diffuser Design
The use of CFD offers several significant advantages for 240SX rear diffuser design:
- Reduced Development Time: CFD allows for rapid prototyping and testing of different designs, significantly reducing the time required to develop an optimized diffuser.
- Cost Savings: Eliminating the need for physical prototypes and wind tunnel testing results in significant cost savings.
- Improved Performance: CFD allows for a more thorough understanding of the airflow dynamics, leading to improved diffuser performance in terms of downforce, drag reduction, and overall handling.
- Customization: CFD enables the design of custom diffusers tailored to specific 240SX configurations and driving needs. For example, a diffuser designed for drifting might prioritize different parameters than one designed for track racing.
- Detailed Data Analysis: CFD provides a wealth of data about the airflow around the diffuser, allowing for a more in-depth understanding of its performance. This data can be used to further refine the design and identify areas for improvement.
Limitations of CFD
While CFD is a powerful tool, it is important to be aware of its limitations:
- Computational Cost: Running complex CFD simulations can require significant computational resources and time.
- Accuracy: The accuracy of the CFD results depends on the quality of the 3D model, the mesh, and the simulation parameters. Simplifications and assumptions may be necessary, which can affect the accuracy of the results.
- Expertise Required: Performing CFD simulations and interpreting the results requires specialized knowledge and expertise.
- Validation: CFD results should ideally be validated with experimental data, such as wind tunnel testing or on-track measurements, to ensure their accuracy.
It's important to remember that CFD is a tool, and the quality of the results depends on the skill and experience of the user.
Conclusion: Enhancing Your 240SX with Informed Aerodynamics
CFD is a valuable tool for analyzing and optimizing 240SX rear diffuser designs. By simulating airflow behavior, engineers can gain a deeper understanding of how different design parameters affect performance. This knowledge can be used to develop diffusers that provide increased downforce, reduced drag, and improved handling, ultimately enhancing the driving experience. While CFD has its limitations, it offers significant advantages over traditional design methods, making it an essential tool for performance enthusiasts and automotive engineers alike. Whether you're looking to purchase an off-the-shelf diffuser or design your own custom solution, understanding the principles of CFD can empower you to make more informed decisions and unlock the full aerodynamic potential of your 240SX. Investing the time and resources into understanding and potentially utilizing CFD ensures that any aerodynamic modification is beneficial and specifically targeted towards desired handling characteristics.