Convertible Model Structural Analysis And Modifications
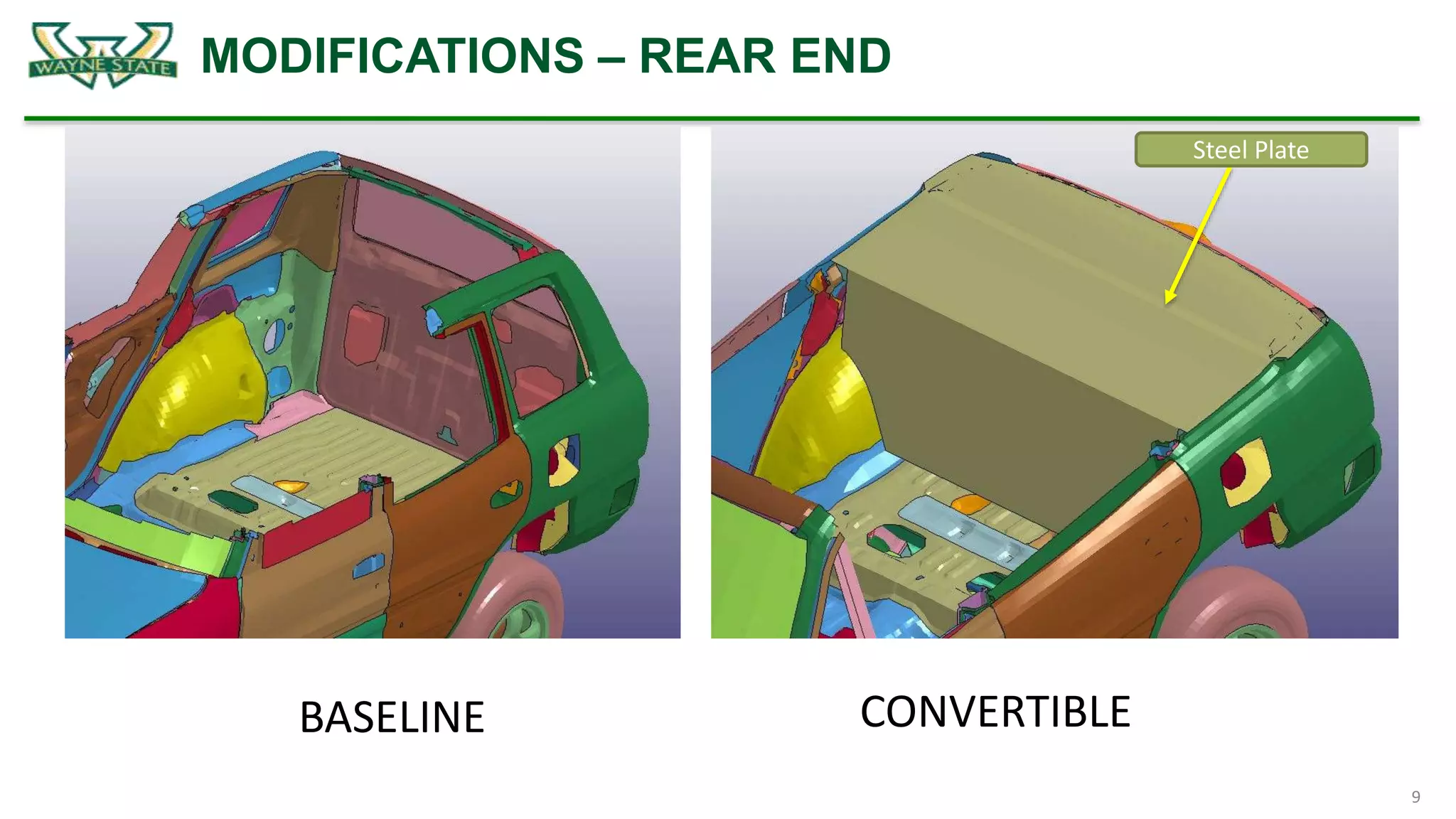
Okay, so you're thinking about modifying a convertible. Awesome! Convertibles are fantastic, but understanding their unique structural challenges is critical before you start chopping, adding, or significantly altering anything. Unlike a hardtop, a convertible lacks a fixed roof, which fundamentally changes how the car handles stress. This article will break down the key structural differences, how to analyze them, and what modifications require extra attention and reinforcement.
The Missing Roof: A Structural Void
The roof of a standard car acts as an integral part of the vehicle's unibody structure. A unibody (or monocoque) design means the body and frame are essentially one piece, distributing loads across the entire structure. The roof contributes significantly to:
- Torsional rigidity: Resisting twisting forces. Think of a shoebox – it's easier to twist open than a closed box. The roof acts like the closed lid.
- Bending stiffness: Resisting bending forces along the length of the car.
- Crashworthiness: Providing structural integrity in the event of a rollover.
A convertible essentially removes a major component contributing to all these areas. To compensate, manufacturers employ various strategies to regain some of that lost stiffness and safety.
Key Structural Differences in Convertibles
Here's where things get interesting. Manufacturers use several techniques to bolster a convertible's structure:
Reinforced Rocker Panels
The rocker panels (the body panels below the doors) are significantly strengthened in convertibles. This is often achieved by:
- Increased steel gauge: Using thicker steel in the rocker panels.
- Internal bracing: Welding in additional bracing and reinforcements within the rocker panel structure.
- Filling with structural foam: Injecting a rigid foam into the rocker panel cavity to add stiffness and absorb energy.
These reinforcements make the rocker panels a primary load-bearing member in a convertible. They resist bending and torsional forces that would otherwise be absorbed by the roof.
Strengthened A-Pillars
The A-pillars (the pillars that frame the windshield) are also beefed up, particularly in terms of rollover protection. This often involves:
- High-strength steel: Using higher grades of steel with greater tensile strength.
- Increased diameter: Making the A-pillars physically larger.
- Internal reinforcement: Adding internal plates or tubes to increase their resistance to bending and crushing.
Reinforced Floor Pan
The floor pan is another critical area. Manufacturers often add:
- Cross-bracing: Welding in additional cross-members to connect the rocker panels and transmission tunnel, increasing torsional rigidity.
- Reinforced transmission tunnel: Making the tunnel stronger to resist twisting forces.
Roll Hoops (or Roll Bars)
Some convertibles, especially older models, rely heavily on roll hoops (or roll bars) located behind the seats. These are designed to protect the occupants in a rollover accident. They are usually welded directly to the chassis or reinforced sections of the floor pan.
It's important to note that these reinforcements add weight. Convertibles are often heavier than their hardtop counterparts due to these structural modifications.
Structural Analysis: Knowing What You're Working With
Before you start modifying, you need to understand the existing structure. Here's how you can analyze it:
Visual Inspection
Start with a thorough visual inspection. Look for:
- Welded seams: Identify where reinforcements have been added. Look for telltale signs of thicker welds or multiple weld passes.
- Changes in panel thickness: Compare the thickness of the rocker panels and A-pillars to those of a comparable hardtop model (if available).
- Rust and corrosion: Rust weakens the structure significantly. Pay particular attention to the rocker panels, floor pan, and areas around welded seams. Address any rust issues before proceeding with modifications.
Manufacturer's Data
Accessing the manufacturer's technical specifications can provide valuable information about:
- Steel grades: Knowing the type of steel used in different areas can help you choose appropriate materials for modifications.
- Section moduli: This indicates the resistance of a structural member to bending. Higher section moduli mean greater strength.
- Exploded diagrams: These diagrams can show the location of internal bracing and reinforcements.
Finding this data can be challenging, but service manuals, online forums, and even contacting the manufacturer directly can be helpful.
Finite Element Analysis (FEA) - The Advanced Option
For complex modifications, Finite Element Analysis (FEA) can be invaluable. FEA is a computer simulation technique that allows you to predict how a structure will respond to different loads and stresses. This can help you identify potential weak points and optimize your modifications for maximum strength and safety. While FEA software can be expensive and requires specialized knowledge, online services and engineering consultants offer FEA services for a fee.
Modifications and Reinforcements: Proceed with Caution
Now let's talk about specific modifications and the reinforcements they may require:
Suspension Modifications (Lowering, Stiffer Springs/Shocks)
Stiffer suspension components increase the stress on the chassis. On a convertible, this can exacerbate existing weaknesses. Consider:
- Strut tower braces: These connect the strut towers (the mounting points for the front suspension) to improve torsional rigidity. They are particularly beneficial on convertibles.
- Subframe connectors: These connect the front and rear subframes to the rocker panels, further stiffening the chassis.
- Reinforced sway bar mounts: Stiffer sway bars can put extra stress on the mounting points. Reinforce these areas as needed.
Engine Swaps and Power Adders (Turbochargers, Superchargers)
Increased power puts more stress on the entire drivetrain and chassis. You'll need to consider:
- Reinforced engine mounts: Prevent excessive engine movement, which can strain the chassis.
- Stronger drivetrain components: Upgrade the transmission, axles, and differential to handle the increased power.
- Chassis stiffening: Consider adding a roll cage or extensive subframe connectors to improve torsional rigidity and prevent chassis flex.
Body Modifications (Widebody Kits, Custom Fabrication)
Any significant changes to the body can impact the structural integrity. Pay close attention to:
- Maintaining structural continuity: When cutting or welding body panels, ensure that you maintain a continuous load path. Avoid creating stress risers (sharp corners or abrupt changes in geometry).
- Reinforcing welded seams: Properly weld all seams with sufficient penetration and add additional bracing as needed.
- Rollover protection: If removing or modifying the A-pillars, you must install a properly engineered roll cage to maintain adequate rollover protection. This is non-negotiable for safety reasons.
Adding Weight (Audio Systems, Custom Interiors)
Even seemingly minor additions can affect the car's handling and stress on the chassis. Consider:
- Weight distribution: Try to distribute weight evenly to avoid upsetting the car's balance.
- Suspension adjustments: Adjust the suspension to compensate for the added weight.
- Chassis stiffening (if necessary): If adding a significant amount of weight, consider adding subframe connectors or other chassis reinforcements.
Welding: The Heart of Reinforcement
Welding is often necessary for reinforcing a convertible's structure. MIG (Metal Inert Gas) welding is generally preferred for automotive applications due to its ease of use and ability to weld a wide range of materials. Ensure you have proper welding skills and equipment, and always use appropriate safety gear (welding helmet, gloves, etc.). Key considerations include:
- Material compatibility: Use welding wire that is compatible with the type of steel you are welding.
- Proper penetration: Ensure that the weld penetrates deeply into the base metal for a strong bond.
- Cleanliness: Thoroughly clean the metal before welding to remove rust, paint, and other contaminants.
- Avoiding distortion: Use appropriate welding techniques to minimize distortion of the metal. Spot welding or stitch welding can help prevent warping.
Safety First
Modifying a convertible's structure is not something to take lightly. Safety should always be your top priority. If you are unsure about any aspect of the modification process, consult with a qualified automotive engineer or experienced fabricator. A poorly executed modification can compromise the vehicle's structural integrity and put you and others at risk.
Remember, a convertible's strength lies in its compensated design. Undoing or altering that compensation without proper reinforcement can lead to dangerous consequences. Plan carefully, analyze thoroughly, and reinforce intelligently. Happy modifying!