Custom Fabrication Techniques For 240sx Components
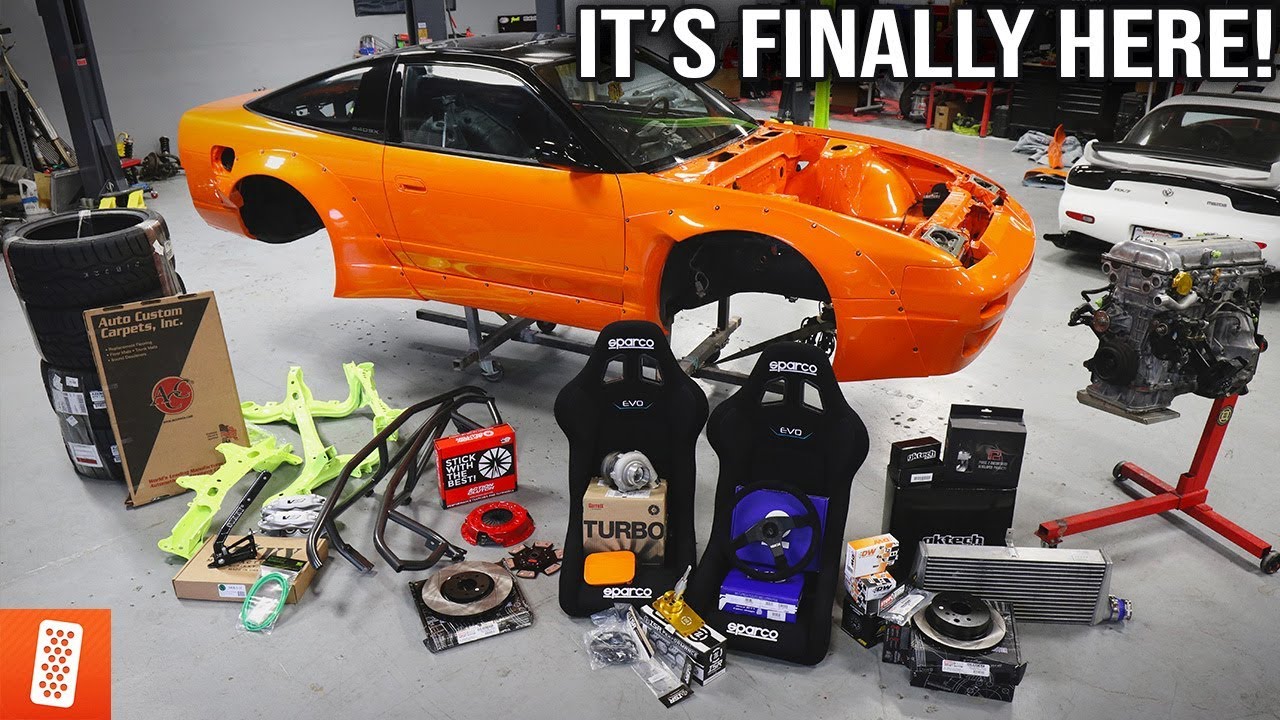
The Nissan 240SX, a beloved platform for drifting, racing, and modification, often benefits from custom fabrication. Whether you're chasing performance gains, addressing rust issues, or simply personalizing your ride, understanding custom fabrication techniques is crucial. This article explores common methods and considerations for creating 240SX components tailored to your specific needs.
Why Consider Custom Fabrication for Your 240SX?
Several reasons drive enthusiasts towards custom fabrication. Here are a few key motivations:
- Performance Enhancement: Off-the-shelf parts might not always provide the optimal solution for your specific setup. Custom fabrication allows for precise adjustments to airflow, suspension geometry, and chassis rigidity.
- Repair and Restoration: The 240SX is aging, and rust is a common enemy. Custom fabrication allows for the creation of replacement panels, floor pans, and other structural components to restore the car to its former glory.
- Unique Aesthetics: Stand out from the crowd with custom body panels, interior modifications, and other unique elements that reflect your personal style.
- Parts Availability: Certain discontinued or rare parts can be replicated or improved upon through custom fabrication.
- Improved Strength & Durability: Fabrication allows you to beef up weak points in the chassis or suspension for increased longevity and performance.
Common Custom Fabrication Techniques
Several techniques are employed in the custom fabrication of 240SX components. Understanding these processes will help you make informed decisions when commissioning or undertaking fabrication work yourself.
Welding
Welding is arguably the most essential skill for any fabricator. It involves joining metal pieces by melting and fusing them together. Common welding processes include:
- MIG (Metal Inert Gas) Welding: A versatile process suitable for various materials and thicknesses. It's relatively easy to learn and ideal for general fabrication work, chassis reinforcement, and sheet metal repair.
- TIG (Tungsten Inert Gas) Welding: Offers greater precision and control, resulting in cleaner, stronger welds. TIG welding is preferred for aluminum, stainless steel, and intricate projects where aesthetics are paramount.
- Stick Welding (SMAW - Shielded Metal Arc Welding): A more robust and portable option, often used for heavier-duty applications and outdoor repairs. However, it requires more skill and practice to master.
Important Note: Proper welding technique is critical for safety and structural integrity. Always wear appropriate safety gear, including a welding helmet, gloves, and protective clothing.
Metal Cutting
Accurate metal cutting is essential for preparing components for welding and assembly. Common cutting methods include:
- Plasma Cutting: A fast and efficient method for cutting various metals, including steel, aluminum, and stainless steel. It uses a high-temperature plasma arc to melt and sever the metal.
- Oxy-Acetylene Cutting: An older but still useful method for cutting steel. It uses a mixture of oxygen and acetylene gas to create a flame that melts the metal.
- Angle Grinder with Cutting Discs: A versatile tool for cutting, grinding, and shaping metal. Use appropriate cutting discs for different materials.
- Band Saw: Provides precise and clean cuts, particularly useful for cutting tubing and bar stock.
- Laser Cutting & Waterjet Cutting: For complex and highly accurate cuts, outsourcing to a laser or waterjet cutting service may be necessary. These methods offer exceptional precision and are suitable for intricate designs.
Metal Bending
Bending metal into specific shapes is crucial for creating custom brackets, panels, and other components. Common bending methods include:
- Manual Bending: Using hand tools like bending brakes and rollers for simple bends and curves.
- Hydraulic Bending: Utilizes hydraulic power for more complex and precise bends. Hydraulic benders are available in various sizes and capacities.
- Tube Bending: Specialized tube benders are used to create smooth, consistent bends in tubing for roll cages, exhaust systems, and other tubular structures.
Metal Forming
Metal forming encompasses techniques for shaping metal through processes other than cutting and bending. This includes:
- Hammer Forming: Shaping metal by hammering it over a form or anvil. This technique is often used for creating custom body panels and intricate shapes.
- English Wheel: A tool used to create compound curves in sheet metal, often used in automotive restoration and custom bodywork.
- Shrinking and Stretching: Techniques used to manipulate the shape of metal by either shrinking or stretching specific areas. These methods are crucial for creating complex curves and contours.
Surface Finishing
After fabrication, surface finishing is crucial for protection and aesthetics. Common options include:
- Painting: Applying paint to protect the metal from corrosion and enhance its appearance. Choose appropriate paints for the specific material and application.
- Powder Coating: A durable and long-lasting finish that is applied electrostatically and then cured with heat. Powder coating offers excellent resistance to corrosion, scratches, and fading.
- Anodizing: An electrochemical process that creates a protective oxide layer on aluminum. Anodizing enhances corrosion resistance and can be used to add color to aluminum components.
- Polishing: A process that removes imperfections and creates a smooth, shiny surface. Polishing is often used on stainless steel and aluminum components.
Examples of Custom Fabricated 240SX Components
Here are some specific examples of how custom fabrication can be applied to the 240SX:
- Roll Cages: Provide enhanced safety and chassis rigidity for racing and drifting. Custom roll cages are designed to fit the specific dimensions of the 240SX chassis and offer optimal protection.
- Suspension Components: Custom control arms, strut towers, and sway bar mounts can be fabricated to optimize suspension geometry and improve handling.
- Exhaust Systems: Custom exhaust manifolds, downpipes, and cat-back systems can be fabricated to improve exhaust flow and increase horsepower.
- Intercooler Piping: Custom intercooler piping allows for optimized routing and reduced pressure drop in turbocharged applications.
- Body Panels: Custom widebody kits, fender flares, and bumpers can be fabricated to enhance the aesthetics and aerodynamic performance of the 240SX.
- Rust Repair Panels: Replacement floor pans, rocker panels, and quarter panels can be fabricated to address rust issues and restore the structural integrity of the chassis.
- Engine Mounts: For engine swaps, custom engine mounts are often necessary to properly position the new engine in the 240SX chassis.
- Fuel Cells: Custom fuel cells can be fabricated to provide a safer and more reliable fuel supply for racing and high-performance applications.
Considerations Before Starting Your Custom Fabrication Project
Before diving into a custom fabrication project, consider the following:
- Skill Level: Assess your welding, cutting, and fabrication skills honestly. If you're a beginner, start with simpler projects and gradually increase the complexity.
- Tools and Equipment: Ensure you have the necessary tools and equipment for the project, including a welder, cutting tools, bending tools, and safety gear.
- Materials: Choose the appropriate materials for the specific application. Steel, aluminum, and stainless steel are common choices, each with its own properties and advantages.
- Design and Planning: Thorough planning and design are crucial for a successful fabrication project. Create detailed drawings or CAD models before starting the fabrication process.
- Budget: Custom fabrication can be expensive, so establish a budget beforehand and stick to it. Factor in the cost of materials, tools, and potential outsourcing.
- Safety: Prioritize safety at all times. Wear appropriate safety gear and follow safe working practices.
Finding a Professional Fabricator
If you lack the skills, tools, or time to undertake a custom fabrication project yourself, consider hiring a professional fabricator. When choosing a fabricator, consider the following:
- Experience: Look for a fabricator with experience in working with 240SXs or similar vehicles.
- Reputation: Check online reviews and ask for recommendations from other enthusiasts.
- Portfolio: Review the fabricator's portfolio to assess the quality of their work.
- Communication: Ensure the fabricator is responsive and communicates clearly throughout the project.
- Pricing: Obtain quotes from multiple fabricators and compare pricing.
Conclusion
Custom fabrication opens up a world of possibilities for enhancing the performance, aesthetics, and functionality of your 240SX components. Whether you're tackling rust repair, chasing horsepower gains, or simply personalizing your ride, understanding the techniques and considerations outlined in this article will help you achieve your goals. Remember to prioritize safety, plan carefully, and choose the right materials and methods for your specific project. With careful planning and execution, custom fabrication can transform your 240SX into a truly unique and personalized machine.