Design And Fabrication Of A Full Tubular Space Frame Chassis For A 240sx
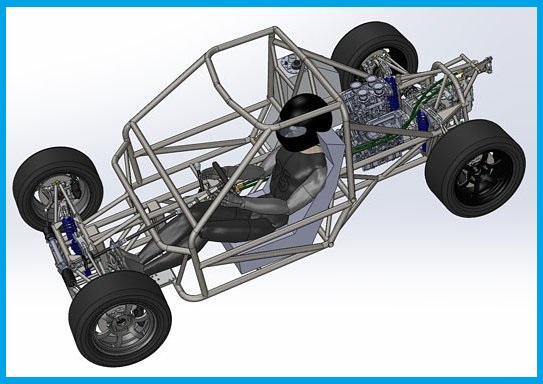
For automotive enthusiasts seeking ultimate performance and chassis rigidity, a full tubular space frame chassis represents the pinnacle of engineering. This article explores the design and fabrication process of a full tubular space frame chassis specifically for a Nissan 240SX (S13/S14), covering key considerations, benefits, and potential challenges involved in such an ambitious project. This guide is intended for educational purposes and should not be taken as a replacement for professional advice. Building a space frame chassis requires significant expertise and resources.
Why a Tubular Space Frame for a 240SX?
The factory chassis of the 240SX, while capable for street use, can exhibit flex under the extreme stresses of racing or high-performance applications. A tubular space frame offers several crucial advantages:
- Superior Rigidity: Significantly reduces chassis flex, improving handling, suspension response, and overall vehicle stability.
- Weight Reduction: With careful design and material selection, a space frame can be lighter than the original unibody structure, leading to improved acceleration, braking, and fuel efficiency.
- Customization: Provides unparalleled freedom to optimize suspension geometry, engine placement, and driver ergonomics.
- Enhanced Safety: When designed and fabricated correctly, a space frame can offer superior crash protection compared to the stock chassis.
Design Considerations for a 240SX Space Frame
Designing a space frame is a complex undertaking that requires a deep understanding of structural engineering principles, CAD software, and finite element analysis (FEA). Here are some key considerations:
1. Defining the Vehicle's Intended Use
The design process begins with a clear understanding of the vehicle's intended application. Will it be used for drifting, circuit racing, drag racing, or a combination of disciplines? This will dictate the load cases the chassis needs to withstand, influencing tube diameters, wall thicknesses, and overall structural layout.
2. Suspension Geometry
One of the biggest advantages of a space frame is the freedom to optimize suspension geometry. Consider factors like:
- Roll Center Height: Influences body roll and handling characteristics.
- Instant Center Location: Affects weight transfer and traction.
- Anti-Squat and Anti-Dive: Determines suspension behavior during acceleration and braking.
- Camber and Caster Curves: Optimizing these parameters is crucial for maximizing tire contact patch throughout suspension travel.
3. Engine and Drivetrain Placement
The space frame design must accommodate the engine, transmission, differential, and all associated components. Consider:
- Engine Mounting Points: Ensure robust and vibration-dampening mounts.
- Driveshaft Angle: Minimize vibration and stress on the drivetrain.
- Exhaust Routing: Plan for adequate clearance and heat shielding.
4. Safety Cage Integration
A properly integrated safety cage is essential for driver protection. The space frame design should incorporate the cage as an integral part of the structure, maximizing its effectiveness in a crash.
5. Material Selection
The most common materials for space frame construction are:
- Mild Steel (DOM): Affordable and easy to weld, but heavier than other options. DOM (Drawn Over Mandrel) tubing is generally preferred over ERW (Electric Resistance Welded) tubing due to its superior strength and consistency.
- Chromoly (4130): Offers significantly higher strength-to-weight ratio compared to mild steel, but requires specialized welding techniques. Chromoly is the popular choice for high-performance applications.
6. CAD Modeling and FEA
Sophisticated CAD software is essential for creating a detailed 3D model of the space frame. Once the model is complete, FEA can be used to simulate various load cases and identify areas of high stress. This allows for optimization of tube placement and material selection to achieve the desired strength and stiffness while minimizing weight. Failure to properly utilize FEA can result in a chassis that is either unnecessarily heavy or structurally inadequate.
Fabrication Process
Fabricating a space frame requires a high degree of skill and precision. Here's a general overview of the process:
1. Tube Cutting and Notching
Accurate tube cutting and notching are critical for achieving a strong and precisely fitting frame. A variety of tools can be used, including:
- Tube Notcher: Creates precise notches for joining tubes at various angles.
- Chop Saw: For straight cuts.
- Band Saw: For angled cuts and more intricate shapes.
2. Jigging and Fixturing
A robust jig or fixture is essential for holding the tubes in the correct position during welding. This ensures that the frame is straight, square, and dimensionally accurate. A well-designed jig is an invaluable asset during the fabrication process.
3. Welding
Welding is arguably the most critical aspect of space frame fabrication. The choice of welding process depends on the material being used:
- MIG (Gas Metal Arc Welding): Suitable for mild steel, but not ideal for chromoly.
- TIG (Gas Tungsten Arc Welding): The preferred method for welding chromoly, as it provides greater control and produces stronger, more ductile welds. TIG welding requires considerable skill and experience.
Proper welding technique is paramount. This includes using the correct amperage, voltage, and travel speed, as well as ensuring proper gas shielding to prevent contamination. Incomplete or improperly executed welds can significantly compromise the strength and integrity of the frame.
4. Post-Weld Inspection
After welding, the frame should be thoroughly inspected for any defects, such as cracks, porosity, or undercut. Non-destructive testing methods like dye penetrant inspection or ultrasonic testing can be used to detect subsurface flaws.
5. Final Assembly and Finishing
Once the frame has been inspected and approved, it can be prepared for final assembly. This may involve:
- Adding Mounting Points: For suspension components, engine, transmission, fuel tank, and other accessories.
- Powder Coating or Painting: To protect the frame from corrosion.
Challenges and Considerations
Building a space frame chassis is a significant undertaking that presents several challenges:
- Cost: The cost of materials, tools, and labor can be substantial.
- Time: The fabrication process can take several weeks or even months, depending on the complexity of the design.
- Expertise: Requires a high level of skill in design, fabrication, and welding.
- Legal Considerations: Modifying the chassis of a vehicle may be subject to regulatory restrictions. Check local laws and regulations before undertaking such a project.
Conclusion
A full tubular space frame chassis offers significant performance advantages for a 240SX, but it is a complex and demanding project. Careful planning, meticulous execution, and a thorough understanding of structural engineering principles are essential for success. If you're considering building a space frame, it's crucial to partner with experienced professionals who can provide guidance and support throughout the process. This project is not for beginners and should be approached with realistic expectations and a commitment to quality and safety. Remember to prioritize safety above all else throughout the entire design and fabrication process. Always consult with qualified professionals to ensure compliance with all applicable regulations. Building a full tubular space frame 240SX is an extremely challenging and costly project, but it also offers a unique opportunity to create a truly high-performance and personalized vehicle. Before embarking on such a project, carefully weigh the costs and benefits and ensure that you have the necessary skills, resources, and expertise to complete it successfully.