Digital Speedometer Conversion Wiring And Sensor Integration
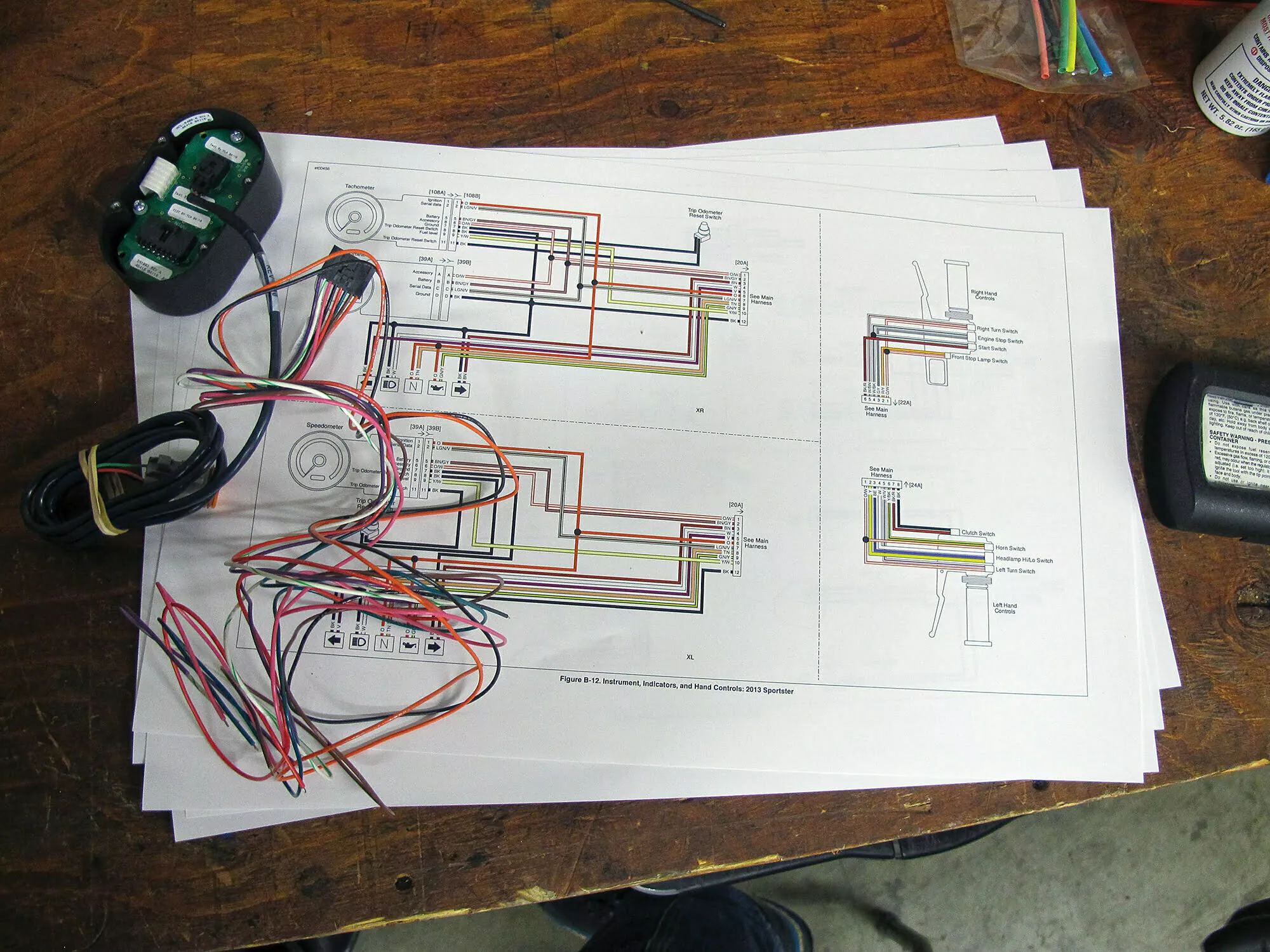
The allure of a digital speedometer is undeniable. Its crisp, easily readable display offers a modern touch to classic cars and provides enhanced functionality in newer vehicles. But retrofitting a digital speedometer often involves more than just swapping out the old analog unit. It requires a solid understanding of wiring, sensor integration, and the underlying principles that translate wheel rotation into a digitally displayed speed. This article provides a technical deep dive into the conversion process, equipping you with the knowledge to tackle this project with confidence.
Understanding the Analog Legacy
Before diving into digital conversions, it's crucial to understand how traditional analog speedometers function. These rely on a mechanical cable connected to the transmission. As the transmission output shaft rotates, so does the cable, spinning a magnet inside the speedometer head. This rotating magnet induces eddy currents in a metal cup attached to the needle. The interaction between the magnetic field and the eddy currents creates a torque that deflects the needle against the resistance of a hairspring. The faster the cable spins, the stronger the magnetic field, and the further the needle deflects, indicating speed on the gauge.
The beauty of this system lies in its simplicity, but its accuracy can degrade over time due to cable wear, speedometer head aging, and changes in tire size or final drive ratio. Digital speedometers offer improved accuracy and features like trip odometers, average speed calculations, and programmable alerts.
The Digital Advantage: Sensors and Signals
Digital speedometers leverage electronic sensors to measure wheel speed. The most common type is the vehicle speed sensor (VSS), often located on the transmission or, increasingly, integrated into the wheel hub as part of the ABS (Anti-lock Braking System) or traction control system. These sensors typically operate on one of two principles:
Reluctor Wheel Sensors (Variable Reluctance)
Reluctor wheel sensors are passive devices. They consist of a coil of wire wrapped around a magnetic core, positioned near a toothed wheel (the reluctor wheel) attached to a rotating shaft. As the teeth of the reluctor wheel pass the sensor, they alter the magnetic flux in the core. This change in flux induces a small AC voltage in the coil. The frequency of this AC signal is directly proportional to the rotational speed of the wheel. The higher the frequency, the faster the vehicle is traveling. The amplitude of the signal also increases with speed, but it’s the frequency that is primarily used for speed determination.
Important Note: Reluctor wheel sensors are polarity independent. Reversing the wires won't affect their functionality.
Hall Effect Sensors
Hall effect sensors are active devices, meaning they require a power supply. They utilize the Hall effect, which states that when a current-carrying conductor is placed in a magnetic field, a voltage (the Hall voltage) is generated perpendicular to both the current and the magnetic field. In a VSS application, a small magnet is embedded within the sensor, and a rotating toothed or slotted wheel (or a magnetic encoder ring) passes in front of the sensor. Each time a tooth (or a magnetic pole) passes, it alters the magnetic field sensed by the Hall effect sensor, causing the Hall voltage to switch between two distinct levels (high and low). This creates a square wave signal whose frequency is proportional to the rotational speed. Compared to reluctor sensors, Hall effect sensors generally provide a cleaner, more robust signal, especially at low speeds.
Important Note: Hall effect sensors require a specific polarity for their power supply and signal connections. Incorrect wiring can damage the sensor.
Wiring the Digital Speedometer
The wiring process is the critical link between the sensor and the speedometer display. Here's a general overview of the connections:
- Power Supply: The digital speedometer requires a stable 12V DC power supply. This should be sourced from a fused, switched power source in the vehicle, meaning it's only powered when the ignition is on. Grounding is equally crucial. Ensure a secure, clean connection to the vehicle's chassis.
- Ground: As mention above, a proper ground connection is essential for correct operation. Connect the speedometer's ground wire to a reliable chassis ground point.
- VSS Signal: This is the core connection. Connect the VSS output wire (either from the transmission sensor or a wheel speed sensor) to the speedometer's signal input. The polarity of this connection is critical for Hall effect sensors and less important for reluctor sensors. Consult the speedometer and sensor documentation for proper wiring instructions.
- Illumination: Most digital speedometers offer a dimming function connected to the vehicle's lighting circuit. This reduces the display brightness at night.
- Optional Connections: Some speedometers may offer additional inputs for features like gear position indication, shift lights, or programmable alarms.
Sensor Integration Strategies
Integrating a VSS into a vehicle that wasn't originally equipped with one requires careful planning and potentially some fabrication.
Using Existing ABS Sensors
Modern vehicles often use ABS wheel speed sensors. These can be a valuable source of speed information for your digital speedometer. However, the signal from ABS sensors is usually processed by the ABS control module before being outputted on the CAN (Controller Area Network) bus. Accessing this data requires a CAN bus interface and decoding the specific message containing the wheel speed information. This approach is more complex but offers the advantage of using existing hardware. Warning: Tapping directly into an ABS sensor line can disrupt the ABS system. This is not recommended.
Aftermarket VSS Installation
If your vehicle lacks a suitable sensor, you'll need to install an aftermarket VSS. Options include:
- Transmission-Mounted VSS: These sensors replace the original speedometer cable drive with an electronic sensor. They are a direct bolt-on solution for many older vehicles.
- Driveshaft-Mounted VSS: These sensors attach to the driveshaft and use a magnetic pickup to detect the rotation of the shaft. They require careful alignment and mounting.
- Wheel Hub-Mounted VSS: Similar to ABS sensors, these mount on the wheel hub and measure wheel speed directly. They require more extensive fabrication and may be difficult to adapt to older vehicles.
Calibration: Fine-Tuning Accuracy
Once the wiring and sensor integration are complete, the speedometer needs to be calibrated to ensure accurate speed readings. This is typically done through a calibration menu within the speedometer itself. The process usually involves entering a pulses per mile (PPM) or pulses per kilometer (PPK) value. This value represents the number of signal pulses generated by the VSS for each mile or kilometer traveled.
Determining the PPM/PPK Value:
- Manufacturer Specifications: If available, the sensor manufacturer's datasheet will provide the PPM/PPK value.
- Calculation: You can calculate the PPM/PPK value based on the number of teeth on the reluctor wheel or magnetic encoder ring, the final drive ratio, and the tire circumference.
- GPS Calibration: Use a GPS device to compare the speedometer reading to the actual speed. Adjust the PPM/PPK value until the speedometer reading matches the GPS reading. This is typically the most accurate method.
Iterative Adjustment: Calibrating the speedometer is often an iterative process. Drive the vehicle at a known speed (e.g., using a GPS or another vehicle's speedometer) and compare the displayed speed on the digital speedometer. If the speedometer reads too high, increase the PPM/PPK value. If it reads too low, decrease the PPM/PPK value. Repeat this process until the speedometer reading is accurate across the desired speed range.
Troubleshooting Tips
Digital speedometer conversions can sometimes present challenges. Here are some troubleshooting tips:
- No Reading: Check the power and ground connections. Verify that the VSS is properly wired and functioning. Use a multimeter to check for a signal from the VSS when the wheels are rotating.
- Erratic Reading: Check for loose connections or damaged wiring. Ensure that the VSS is securely mounted and properly aligned. Electromagnetic interference (EMI) from other vehicle components can also cause erratic readings. Try shielding the VSS signal wire or rerouting it away from potential sources of EMI.
- Inaccurate Reading: Double-check the PPM/PPK value and recalibrate the speedometer. Verify that the tire size and final drive ratio are correctly accounted for in the calculations.
Conclusion
Converting to a digital speedometer involves a multifaceted approach that combines electrical wiring, sensor integration, and calibration techniques. While it may seem daunting initially, a systematic approach and a thorough understanding of the underlying principles will lead to a successful conversion. By carefully considering the wiring, sensor options, and calibration procedures outlined in this guide, you can transform your vehicle with a modern and accurate digital speed display. Remember to always consult the manufacturer's documentation for both the speedometer and the sensor for specific instructions and wiring diagrams. Safety first!