Driveshaft Bolt Torque Specifications And Failure Analysis
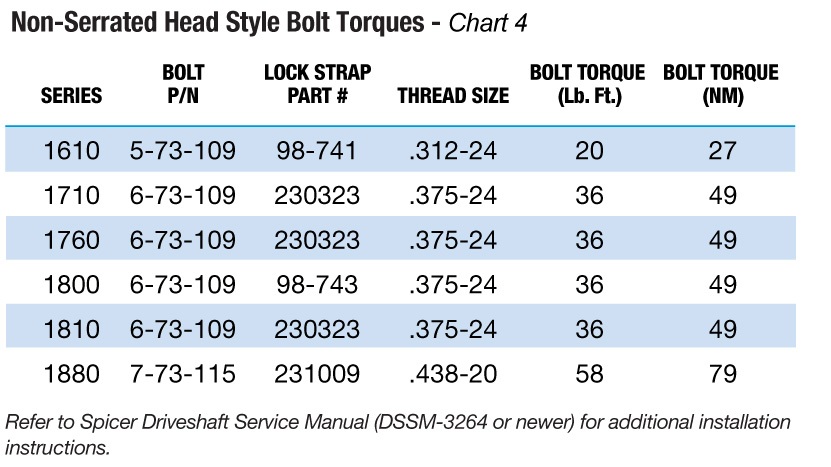
Driveshafts are a critical component in rear-wheel-drive and four-wheel-drive vehicles, responsible for transmitting power from the transmission to the differential and ultimately to the wheels. Ensuring the driveshaft is securely connected is paramount for safety and performance. A crucial aspect of this secure connection is the proper torque applied to the driveshaft bolts. Understanding driveshaft bolt torque specifications and the potential consequences of improper torque is essential for vehicle maintenance and repair.
Driveshaft Bolt Torque Specifications: Why They Matter
Torque is a measure of rotational force, and in the context of driveshaft bolts, it refers to the amount of force applied when tightening the bolts to secure the driveshaft to the transmission or differential flange. Each vehicle manufacturer specifies a precise torque value for these bolts, based on factors such as bolt size, material strength, thread pitch, and the overall design of the driveline. Adhering to these torque specifications is absolutely critical for several reasons:
- Preventing Loosening: Insufficient torque can lead to the bolts gradually loosening over time due to vibrations and stress. Loose bolts can cause driveline vibrations, noise, and, in severe cases, complete driveshaft separation.
- Preventing Bolt Failure: Over-torquing, on the other hand, can stretch or even break the bolts. Stretched bolts lose their clamping force and are prone to fatigue failure. Broken bolts, obviously, result in immediate driveline issues.
- Ensuring Proper Clamp Load: The specified torque value ensures the correct clamping force between the driveshaft flange and the transmission/differential flange. This clamping force is essential for a secure and reliable connection that can withstand the stresses of acceleration, deceleration, and cornering.
- Preserving Component Integrity: Applying the correct torque helps prevent damage to the driveshaft, transmission, and differential flanges. Overtightening can deform or crack these components, leading to costly repairs.
Finding the Correct Torque Specifications
Locating the correct torque specifications for your vehicle is the first step in any driveshaft-related repair or maintenance. The most reliable source is the vehicle's repair manual or service information provided by the manufacturer. These manuals typically include detailed torque specifications for all components, including the driveshaft bolts.
If you don't have access to a repair manual, you can often find torque specifications through online databases that provide technical information for specific vehicle makes and models. Reputable automotive websites and forums dedicated to your vehicle can also be valuable resources. However, always cross-reference information from multiple sources to ensure accuracy.
Important Note: Torque specifications are often given in foot-pounds (ft-lbs) or Newton-meters (Nm). Make sure you are using the correct units when applying torque to the bolts.
Driveshaft Bolt Failure Analysis: Understanding the Causes
Driveshaft bolt failure can manifest in several ways, including:
- Bolt Breakage: Complete fracture of the bolt.
- Bolt Stretching: Permanent elongation of the bolt, resulting in reduced clamping force.
- Thread Stripping: Damage to the threads of the bolt or the mating flange.
- Bolt Loosening: Gradual reduction in torque over time.
Understanding the root cause of the failure is crucial for preventing future occurrences. Here's a breakdown of common causes:
Common Causes of Driveshaft Bolt Failure
- Improper Torque: As discussed earlier, undertorquing and overtorquing are major contributors to bolt failure.
- Incorrect Bolt Type: Using the wrong type of bolt (e.g., incorrect grade or material) can compromise its strength and durability. Always use the OEM-specified bolts.
- Corrosion: Rust and corrosion can weaken the bolts and make them more susceptible to failure. This is especially true in areas where road salt is used.
- Fatigue: Repeated stress and vibration can lead to fatigue failure, even if the bolts were initially torqued correctly.
- Pre-existing Damage: Nicks, scratches, or other damage to the bolts can create stress points that lead to premature failure.
- Improper Installation: Failing to properly clean the threads or using thread lubricant incorrectly can affect the accuracy of the torque reading and lead to failure.
- Driveline Misalignment: Significant driveline misalignment can place excessive stress on the driveshaft bolts, leading to premature failure.
Diagnosing Driveshaft Bolt Failure
Diagnosing driveshaft bolt failure typically involves a visual inspection of the bolts and surrounding components. Look for signs of:
- Missing Bolts: An obvious sign of a problem.
- Loose Bolts: Check the torque of each bolt to see if it is within the specified range.
- Damaged Bolts: Look for signs of stretching, cracking, or thread damage.
- Corrosion: Examine the bolts for rust or other signs of corrosion.
- Driveline Vibrations: Unusual vibrations, especially at higher speeds, can indicate loose or damaged driveshaft bolts.
- Unusual Noises: Clicking, clunking, or grinding noises coming from the driveline area can also be a sign of driveshaft bolt issues.
If you suspect driveshaft bolt failure, it's crucial to address the issue promptly to prevent further damage and ensure your safety. Replace any damaged or missing bolts with new, OEM-specified bolts and torque them to the correct specification using a calibrated torque wrench.
Preventing Driveshaft Bolt Failure
Taking proactive steps can significantly reduce the risk of driveshaft bolt failure:
- Use a Calibrated Torque Wrench: A calibrated torque wrench is essential for accurately applying the specified torque. Periodically calibrate your torque wrench to ensure its accuracy.
- Clean Threads: Clean the bolt threads and mating flange threads before installation to ensure accurate torque readings. Use a wire brush or thread chaser to remove any dirt, debris, or corrosion.
- Use Thread Locker (If Specified): Some manufacturers recommend using a thread locker (e.g., Loctite) on the driveshaft bolts. Follow the manufacturer's instructions regarding the type of thread locker to use and the application procedure. Do not use thread locker unless it's specified.
- Follow Tightening Sequence: If the repair manual specifies a tightening sequence, follow it carefully to ensure even clamping force.
- Inspect Regularly: Periodically inspect the driveshaft bolts for any signs of loosening, damage, or corrosion.
- Address Driveline Issues: Correct any driveline misalignment or other issues that could place excessive stress on the driveshaft bolts.
- Retorque After Initial Run: Some technicians recommend retorquing the driveshaft bolts after a short initial run (e.g., 50-100 miles) to ensure they remain properly tightened.
By understanding the importance of driveshaft bolt torque specifications, identifying potential causes of failure, and implementing preventative measures, you can ensure a safe and reliable driveline for your vehicle. Always consult your vehicle's repair manual or a qualified mechanic for specific torque specifications and repair procedures.