Dual Fuel Pump System Design And Installation Guide
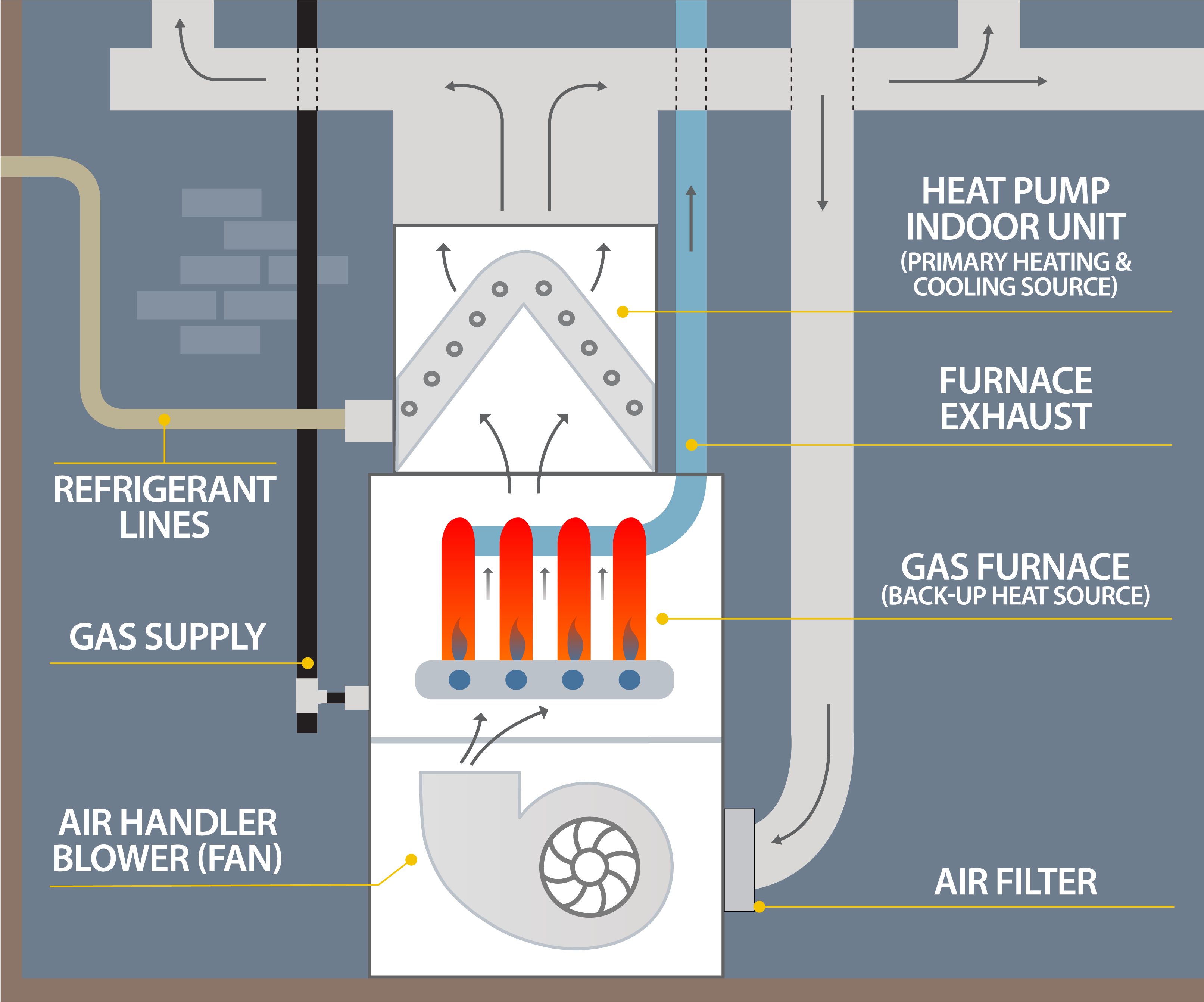
So, you're looking to step up your fuel delivery game with a dual fuel pump system? Excellent choice! This is a common upgrade for high-horsepower builds, especially those running forced induction (turbochargers or superchargers) or nitrous. Before we dive in, let's be clear: this isn't a beginner's project. You'll need solid mechanical skills, a good understanding of automotive electrical systems, and the right tools. But with careful planning and execution, you can successfully install a dual fuel pump system and provide your engine with the fuel it needs to perform.
Understanding the Need for Dual Fuel Pumps
Why bother with two fuel pumps instead of just one bigger one? Several reasons:
- Fuel Demand: High-performance engines, especially when boosted, consume significantly more fuel than stock engines. A single stock pump simply can't keep up with the demand at higher RPMs and boost levels, leading to fuel starvation and potential engine damage.
- Fuel Pressure Drop: As fuel demand increases, the pressure in the fuel system can drop. This can cause the fuel injectors to not atomize fuel properly, leading to poor combustion and reduced power. Dual pumps help maintain consistent fuel pressure.
- Redundancy: In some configurations, the second pump acts as a backup. If one pump fails, the other can continue to supply fuel (though at a reduced rate), preventing a complete engine shutdown. This is especially important for racing applications.
- Pump Life: Sharing the workload between two pumps can extend the lifespan of each individual pump, compared to a single pump working at its maximum capacity all the time.
Planning Your Dual Fuel Pump System
Before you start tearing into your car, a thorough planning phase is crucial. This involves determining your fuel needs, selecting the right components, and designing the system layout.
1. Calculating Fuel Requirements
The first step is to estimate how much fuel your engine will require at its maximum horsepower output. There are online calculators and formulas that can help with this. You'll need to know your target horsepower and Brake Specific Fuel Consumption (BSFC). BSFC is a measure of how efficiently an engine uses fuel; a typical value for a boosted gasoline engine is around 0.6-0.7 lbs/hp/hr.
Formula: Fuel Flow (lbs/hr) = Horsepower x BSFC
Once you have the fuel flow in lbs/hr, you can convert it to gallons per hour (GPH) or liters per hour (LPH). Knowing your fuel flow requirement is crucial for selecting appropriately sized fuel pumps.
2. Choosing the Right Fuel Pumps
Select fuel pumps that, combined, can deliver significantly more fuel than your calculated requirement. It's always better to have some headroom. Look for pumps with specifications that include fuel flow (LPH or GPH) at various pressures (PSI). Consider these factors:
- Fuel Type: Are you running gasoline, E85, or methanol? Choose pumps that are compatible with your fuel type. E85 and methanol are corrosive and require specialized pumps.
- Pump Type: In-tank or external? In-tank pumps are generally quieter and run cooler, but can be more difficult to install. External pumps are easier to access but can be noisy.
- Flow Rate: As mentioned above, the pumps must be able to supply enough fuel at your desired fuel pressure.
- Voltage: Make sure the pumps operate at your vehicle's voltage (usually 12V or 14V).
Popular fuel pump brands include Aeromotive, AEM, Walbro, and DeatschWerks. Read reviews and compare specifications before making a decision.
3. Selecting Supporting Components
A dual fuel pump system requires more than just the pumps themselves. You'll also need:
- Fuel Lines: Upgrade your fuel lines to larger diameter lines to handle the increased fuel flow. Use AN fittings and braided stainless steel lines for durability and leak prevention. The size depends on the flow rate, -6AN or -8AN are common.
- Fuel Pressure Regulator (FPR): A high-quality adjustable FPR is essential for maintaining consistent fuel pressure.
- Fuel Filter: Use a high-flow fuel filter to protect your fuel injectors from debris.
- Fuel Rails: Upgraded fuel rails with larger bores can improve fuel distribution to the injectors.
- Y-Block or Manifold: These split the fuel supply from the tank into two lines, one for each pump.
- Wiring Harness: A dedicated wiring harness with relays and fuses is critical for safe and reliable operation. Using a "boost-a-pump" can help supply the needed voltage, especially at high loads.
- Relays: These are switches controlled by a low-current circuit that can handle the high current required by the fuel pumps.
- Fuses: Protect the wiring and pumps from overcurrent.
- Fuel Level Sender Modification: If using an in-tank setup, you may need to modify the fuel level sender to accommodate the additional pump and pickup.
4. Designing the System Layout
Plan the physical layout of the system carefully. Consider the location of the pumps, fuel lines, FPR, and wiring. Ensure that the fuel lines are routed safely away from heat sources and moving parts. Think about accessibility for maintenance and future upgrades.
Installation Process
Now for the hands-on part. Remember to disconnect the negative battery terminal before starting any electrical work.
1. Fuel Tank Preparation (In-Tank Systems)
If you're installing in-tank pumps, you'll need to remove the fuel tank. Drain the fuel completely before starting. Safety First! Work in a well-ventilated area and avoid open flames.
Once the tank is removed, carefully disassemble the stock fuel pump assembly. You'll likely need to modify the assembly to accommodate the new pumps. This might involve cutting, drilling, or fabricating brackets. Use appropriate tools and take your time.
Install the new pumps into the modified assembly. Ensure that the pump inlets are positioned to draw fuel from the bottom of the tank. Connect the fuel lines to the pumps using appropriate fittings.
Reinstall the modified assembly into the fuel tank, making sure everything is secure and properly sealed. Reinstall the fuel tank into the vehicle.
2. Pump Mounting (External Systems)
For external pumps, choose a suitable mounting location that is protected from the elements and easily accessible. Ensure that the pumps are mounted securely and are not subject to excessive vibration.
Consider mounting the pumps close to the fuel tank to minimize the length of the suction lines. Use vibration dampening mounts to reduce noise and extend pump life.
3. Plumbing the Fuel Lines
Connect the fuel lines from the fuel tank to the pumps, and then from the pumps to the fuel rails. Use AN fittings and braided stainless steel lines. Ensure that all connections are tight and leak-free. Proper torque is crucial for AN fittings.
Route the fuel lines carefully, avoiding sharp bends and potential sources of abrasion. Use fuel line clamps to secure the lines to the chassis.
Install the fuel pressure regulator (FPR) in the return line. Connect the return line from the FPR back to the fuel tank.
4. Wiring the Pumps
This is a critical step. A properly wired fuel pump system is essential for safety and reliability.
- Dedicated Wiring Harness: Use a dedicated wiring harness designed for dual fuel pumps. This will include relays, fuses, and properly sized wiring.
- Relays: Use relays to switch the pumps on and off. The relays should be triggered by the ignition switch or a dedicated fuel pump controller.
- Fuses: Use appropriately sized fuses to protect the wiring and pumps from overcurrent.
- Grounding: Ensure that the pumps are properly grounded to the chassis.
- Boost-a-Pump (Optional): Consider using a boost-a-pump to increase the voltage to the fuel pumps at higher boost levels. This can help maintain consistent fuel pressure.
Many people wire the second pump to activate with a Hobbs switch or the ECU based on boost level. This means the second pump only kicks in when needed, reducing wear and tear.
5. Testing and Tuning
Before starting the engine, check all fuel line connections for leaks. Cycle the ignition switch to prime the fuel system. Look for any signs of fuel leakage.
Start the engine and monitor the fuel pressure. Adjust the fuel pressure regulator (FPR) to the desired pressure. Use a fuel pressure gauge to ensure accurate readings.
It's highly recommended to have your car professionally tuned after installing a dual fuel pump system. A tuner can adjust the fuel maps in the engine control unit (ECU) to optimize performance and ensure that the engine is running safely.
Troubleshooting Common Issues
- Fuel Leaks: Check all fuel line connections and fittings. Tighten as necessary. Replace any damaged lines or fittings.
- Low Fuel Pressure: Check the fuel filter for clogs. Verify that the fuel pumps are operating correctly. Inspect the FPR for damage or malfunction.
- High Fuel Pressure: Adjust the FPR to the desired pressure. Verify that the return line is not blocked.
- Pump Noise: External pumps can be noisy. Use vibration dampening mounts to reduce noise. Excessive noise could indicate a problem with the pump.
- Electrical Problems: Check the wiring harness, relays, and fuses. Ensure that all connections are secure and properly grounded.
Installing a dual fuel pump system is a significant undertaking, but with careful planning, the right components, and attention to detail, you can successfully upgrade your fuel delivery and support your high-performance engine. Always prioritize safety and consult with a professional if you have any doubts.