Exhaust Manifold Design For A Turbocharged Ls-swapped Nissan 240sx
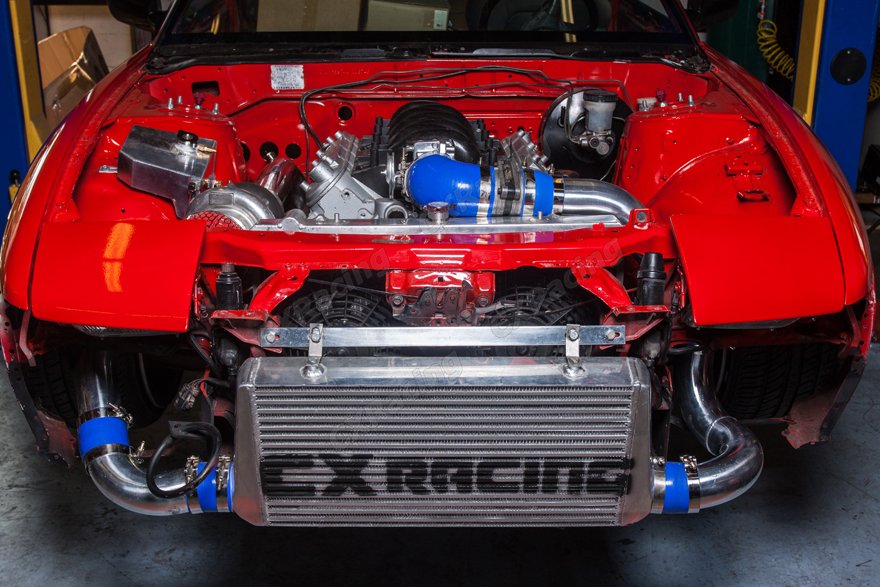
The LS swap into a Nissan 240SX is a popular modification, offering a significant power upgrade while maintaining a relatively lightweight chassis. When adding a turbocharger to this already potent combination, careful consideration must be given to the exhaust manifold design. The manifold plays a crucial role in efficiently channeling exhaust gases from the engine to the turbocharger, impacting performance, responsiveness, and overall reliability. Choosing the wrong manifold can lead to significant performance bottlenecks or even engine damage. This article will explore the key considerations for exhaust manifold design in a turbocharged LS-swapped Nissan 240SX, aiming to provide a comprehensive guide for enthusiasts and professionals alike.
Understanding the Importance of Exhaust Manifold Design
The exhaust manifold serves as the initial pathway for exhaust gases leaving the engine. In a naturally aspirated engine, its primary function is to efficiently evacuate these gases to the exhaust system. However, in a turbocharged application, the manifold's role is amplified. It must effectively collect and direct exhaust flow to the turbocharger's turbine, maximizing energy transfer for optimal boost production. A poorly designed manifold can result in:
- Reduced turbo spool-up: Laggy response due to insufficient exhaust gas velocity reaching the turbine.
- Increased backpressure: Hindering engine performance and potentially causing damage.
- Uneven cylinder firing: Leading to inconsistent performance and potential engine issues.
- Hot spots: Concentrated heat can damage the manifold or surrounding components.
Therefore, selecting the right manifold or designing a custom one is paramount for achieving the desired performance goals from your turbocharged LS-swapped Nissan 240SX.
Key Considerations for Manifold Design
Several factors influence the effectiveness of an exhaust manifold design for a turbocharged LS swap. These include:
Material Selection
The material used for the manifold is critical due to the high temperatures and stresses involved. Common materials include:
- Cast Iron: A durable and cost-effective option, but heavy and prone to cracking under extreme conditions. Usually only found on OEM setups and generally not recommended for high-performance turbocharged applications.
- Mild Steel: A popular choice for custom manifolds, offering good weldability and strength. Requires proper coating or wrapping to prevent rust.
- Stainless Steel: Provides excellent corrosion resistance and heat tolerance but can be more challenging to weld. Often considered the best option for performance applications where budget allows. Different grades of stainless steel exist, so ensure you're selecting one appropriate for high-temperature exhaust applications (e.g., 304 or 321).
- Inconel: The ultimate material for extreme heat and stress applications. Inconel is incredibly strong and heat resistant, but also very expensive and requires specialized welding techniques. Often used in professional motorsports.
For most turbocharged LS-swapped Nissan 240SX builds, stainless steel offers a good balance of performance, durability, and cost.
Runner Length and Diameter
The length and diameter of the individual runners connecting each exhaust port to the collector significantly impact exhaust gas velocity and scavenging effects.
- Runner Length: Equal-length runners are generally preferred in turbocharged applications. They ensure that exhaust pulses from each cylinder arrive at the turbine with similar timing and energy. This promotes a more stable and consistent boost response. Short runners typically improve spool-up at the expense of top-end power, while longer runners can favor top-end power but potentially increase lag. However, due to space constraints in the 240SX engine bay, achieving true equal-length runners can be challenging.
- Runner Diameter: The diameter must be carefully selected to maintain adequate exhaust gas velocity without causing excessive backpressure. Too small of a diameter will choke the engine, while too large can reduce velocity and negatively impact turbo spool. A common starting point for runner diameter is around 1.75" to 2" for moderate power goals (500-700hp). Higher power applications may benefit from larger diameters.
Collector Design
The collector is the point where the individual runners merge into a single outlet to the turbocharger. Its design significantly influences exhaust flow efficiency.
- Merge Collector: A well-designed merge collector gradually combines the runners into a single outlet, minimizing turbulence and maximizing exhaust gas velocity. A smooth transition is crucial.
- Turbine Inlet Flange: The flange that connects the collector to the turbocharger should match the turbocharger's inlet flange size. Common options include T3, T4, and V-band. V-band connections are often preferred for their ease of installation and improved sealing.
Turbocharger Placement
The location of the turbocharger in relation to the engine and exhaust manifold impacts manifold design. Common configurations include:
- Forward Facing: This places the turbocharger towards the front of the engine bay. It often requires a custom manifold design and may necessitate modifications to the radiator support or other components.
- Rear Mounted (Remote Mount): Positions the turbocharger towards the rear of the vehicle. While this can simplify manifold design and potentially improve cooling, it often results in increased turbo lag due to the longer exhaust piping. It's generally not recommended for performance-oriented applications.
- Top Mount: This positions the turbo above the engine. While sometimes aesthetically pleasing, it can create challenges with hood clearance and heat management.
For most LS-swapped 240SX builds, a forward-facing manifold is the most common and often the most effective for maximizing performance within the limited engine bay space. The turbo placement should be dictated by engine bay space and the desired power goals. Higher horsepower applications may warrant the compromises associated with a top mount to accommodate larger frame turbos.
Flange Thickness and Quality
Using thick, high-quality flanges is crucial to prevent warping and leaks. Thicker flanges offer better resistance to heat-induced distortion. Ensure the flanges are properly machined for a tight seal against the cylinder head and turbocharger.
Wastegate Placement
An external wastegate is essential for controlling boost pressure. The placement of the wastegate on the manifold significantly affects its effectiveness. Ideally, the wastegate should be positioned as close to the turbocharger inlet as possible and at an angle that allows it to effectively divert exhaust gases away from the turbine. Poor wastegate placement can lead to boost creep or overboost issues.
Prefabricated vs. Custom Manifolds
When selecting a manifold, you have two primary options: prefabricated (off-the-shelf) or custom-built.
Prefabricated Manifolds
Prefabricated manifolds offer a convenient and often more affordable solution. Several manufacturers produce manifolds specifically designed for LS-swapped 240SX applications. These manifolds are typically designed to fit within the engine bay constraints and provide a reasonable performance upgrade. However, they may not be optimized for your specific turbocharger or power goals.
Custom Manifolds
A custom-built manifold allows for complete control over the design and offers the potential for maximum performance. A skilled fabricator can tailor the manifold to your specific turbocharger, engine specifications, and desired power goals. Custom manifolds are generally more expensive than prefabricated options but can provide significant performance benefits. If your power goals are very high, or you have specific fitment requirements, a custom manifold may be the best option.
Wrapping or Coating Manifolds
Regardless of whether you choose a prefabricated or custom manifold, wrapping or coating the manifold is highly recommended. This helps to reduce radiant heat, improving engine bay temperatures and protecting nearby components. Ceramic coatings offer excellent thermal barrier properties and corrosion resistance. Exhaust wrap is another effective option, but it can trap moisture and potentially accelerate corrosion if not properly applied.
Conclusion
Designing or selecting the right exhaust manifold for a turbocharged LS-swapped Nissan 240SX is a critical step in achieving optimal performance and reliability. By carefully considering the factors discussed in this article – material selection, runner length and diameter, collector design, turbocharger placement, wastegate placement, and the advantages and disadvantages of prefabricated versus custom manifolds – you can make an informed decision that aligns with your specific goals and budget. A well-designed manifold will not only unlock the full potential of your LS swap but also contribute to a more enjoyable and reliable driving experience. Remember to consult with experienced fabricators or performance specialists to ensure your chosen manifold is properly installed and optimized for your application. Ignoring these details can lead to costly repairs and a significant decrease in performance. Invest the time and resources to get it right, and you'll be rewarded with a powerful and responsive turbocharged LS-swapped Nissan 240SX.