Fuel Pump Flow Rate Requirements And Wiring Specifications
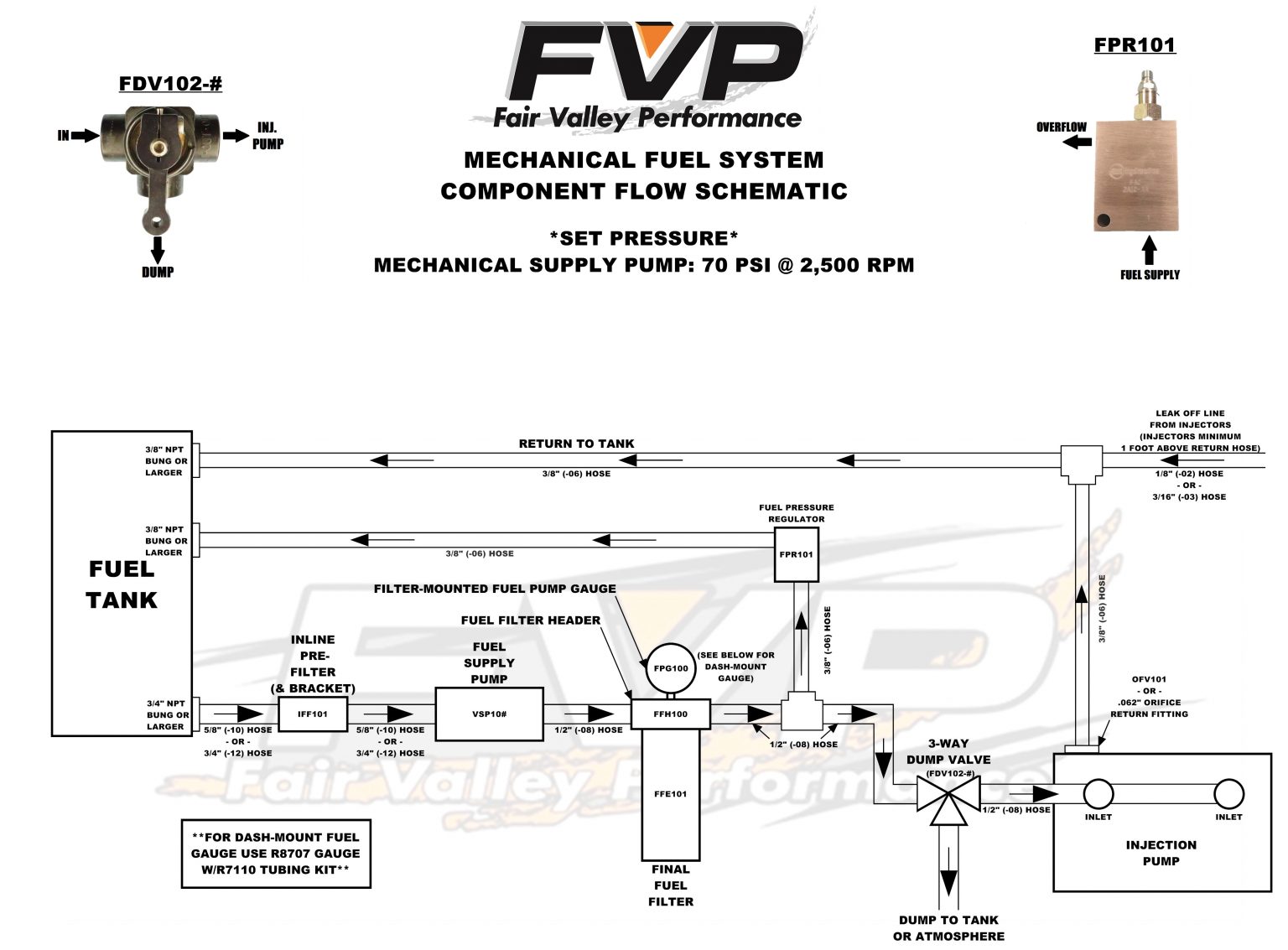
Alright, let's talk fuel pumps. Specifically, how to figure out what flow rate you need, and how to wire them up properly. This is a critical area – undersized pumps starve your engine, especially when boosting, and incorrect wiring can fry components or even cause a fire. I'm assuming you have some basic electrical and mechanical knowledge. If you're unsure, always consult a professional. This isn't something to guess at.
Fuel Pump Flow Rate: Getting It Right
The flow rate of a fuel pump, measured in liters per hour (LPH) or gallons per hour (GPH), is the amount of fuel it can deliver under specific conditions. Getting the right flow rate is paramount for ensuring your engine receives adequate fuel, particularly under high-demand scenarios like wide-open throttle or when running forced induction (turbocharger or supercharger).
Estimating Your Fuel Needs
The first step is estimating your engine's maximum fuel consumption. We'll use horsepower as the primary metric. There are a few different rules of thumb, but let's break them down:
- Naturally Aspirated (NA) Engines: A common estimate is 0.5 pounds of fuel per horsepower per hour (lb/hp/hr). This is also sometimes expressed as a Brake Specific Fuel Consumption (BSFC) of 0.5.
- Forced Induction Engines: These engines need significantly more fuel. A typical BSFC for a boosted engine is 0.6-0.65 lb/hp/hr. For E85, this number can climb to 0.8-0.85 lb/hp/hr or even higher.
Let's work through an example. Say you have a naturally aspirated engine targeting 300 horsepower. Your estimated fuel consumption is 300 hp * 0.5 lb/hp/hr = 150 lbs/hr. Now, we need to convert this to a flow rate. Gasoline weighs roughly 6.1 lbs per gallon. Therefore, 150 lbs/hr / 6.1 lbs/gallon = 24.6 GPH.
To convert GPH to LPH, multiply by 3.785. So, 24.6 GPH * 3.785 = 93.1 LPH. Therefore, you need a pump capable of delivering at least 93.1 LPH. However, that's the bare minimum. We need to factor in a safety margin.
Accounting for Safety Margins and Fuel Pressure
It's crucial to select a pump that exceeds your calculated fuel needs by a significant margin, typically 20-30%. This buffer accounts for variations in fuel density, aging of the pump, voltage drops, and potential future modifications. Let's use 20% for our example. 93.1 LPH * 1.2 = 111.72 LPH. You should select a pump rated for at least 112 LPH.
Another crucial factor is fuel pressure. Pump flow rates are usually specified at a particular pressure. A common spec is at 43.5 PSI (3 bar), which is close to a standard fuel pressure for many fuel injected systems. If you're running higher fuel pressure (e.g., with a boost-referenced fuel pressure regulator), the pump has to work harder, and its effective flow rate will decrease. Always check the fuel pump's flow chart at your intended fuel pressure. These charts show the relationship between pressure and flow. You may need a pump with a significantly higher advertised flow rate to meet your needs at higher pressure.
Think of it like this: a water pump can move more water easily at low pressure. As you increase the pressure it needs to push against, the amount of water it can move decreases. Fuel pumps are the same way.
Considering Fuel Type
The type of fuel you use significantly impacts fuel pump requirements. As mentioned earlier, Ethanol fuels like E85 require considerably more fuel than gasoline due to their lower energy density. If you're switching to E85, increase your calculated fuel flow requirement significantly – up to 40% or more depending on the ethanol content.
Also, some fuel pumps are not compatible with ethanol-based fuels. Always check the manufacturer's specifications to ensure compatibility to avoid premature pump failure.
Fuel Pump Wiring: Ensuring Reliable Power Delivery
An often overlooked aspect of fuel pump installation is the wiring. Insufficient wiring can lead to voltage drop, which significantly reduces the pump's performance. It can also cause the wiring to overheat, creating a fire hazard.
Understanding Voltage Drop
Voltage drop occurs when the voltage at the fuel pump is less than the voltage at the battery. This is due to the resistance of the wiring. Longer wires and smaller wire gauges result in greater voltage drop. A 1-volt drop can significantly reduce fuel pump flow, especially at higher fuel pressures.
Wire Gauge Selection
Choosing the correct wire gauge is essential. Refer to an automotive wiring chart that considers amperage and wire length to minimize voltage drop. Here's a simplified guideline, but always consult a proper chart for your specific application:
- Up to 10 Amps: 16 AWG wire
- 10-15 Amps: 14 AWG wire
- 15-20 Amps: 12 AWG wire
- 20-30 Amps: 10 AWG wire
- 30+ Amps: 8 AWG wire or larger
Measure the distance from your battery to the fuel pump (and back to ground) to determine the total wire length. Consult a voltage drop calculator online, entering your expected amperage, wire length, and target voltage drop (aim for less than 0.5 volts) to determine the appropriate wire gauge.
Using a Fuel Pump Relay
Always use a relay to power your fuel pump. The fuel pump draws a significant amount of current, and running that current through the ignition switch or ECU can damage those components. A relay allows you to use a small signal from the ignition or ECU to switch a high-current circuit directly from the battery to the fuel pump.
A typical fuel pump relay wiring diagram looks like this:
- Pin 30: Connect to the battery positive terminal through a fuse. Choose a fuse rating slightly higher than the pump's maximum current draw.
- Pin 87: Connect to the positive terminal of the fuel pump.
- Pin 85: Connect to ground.
- Pin 86: Connect to a switched 12V source (e.g., from the ignition switch or ECU fuel pump control wire).
When the ignition is turned on (or the ECU activates the fuel pump), pin 86 receives 12V, energizing the relay. This closes the circuit between pin 30 and pin 87, sending power to the fuel pump.
Dedicated Ground
Provide a dedicated ground wire for the fuel pump. Do not rely on grounding through the fuel tank or chassis. Run a wire of the same gauge as your positive wire directly from the fuel pump's ground terminal to a clean, solid ground point on the chassis, preferably near the battery.
Wiring Connectors and Terminals
Use high-quality connectors and terminals designed for automotive use. Crimp connectors securely using a proper crimping tool. Soldering the connections after crimping can provide an even more reliable connection, but ensure the solder doesn't wick up the wire excessively, making it brittle. Protect all connections with heat shrink tubing to prevent corrosion and short circuits. Avoid using wire taps, as these are prone to failure.
Checking Your Work
After wiring the fuel pump, double-check all connections to ensure they are secure and properly insulated. Use a multimeter to verify the voltage at the fuel pump with the engine running. It should be close to the battery voltage. If you're seeing significant voltage drop, re-examine your wiring and connections.
Important Safety Notes:
- Always disconnect the battery before working on the fuel system or electrical system.
- Work in a well-ventilated area to avoid inhaling fuel vapors.
- Have a fire extinguisher readily available.
- If you are not comfortable working on the fuel system or electrical system, consult a qualified mechanic.
Upgrading your fuel pump correctly involves careful calculations and precise wiring. Taking the time to do it right will ensure your engine gets the fuel it needs, reliably and safely. Good luck!