Isr Mbse Exhaust System Flow Characteristics And Db Levels
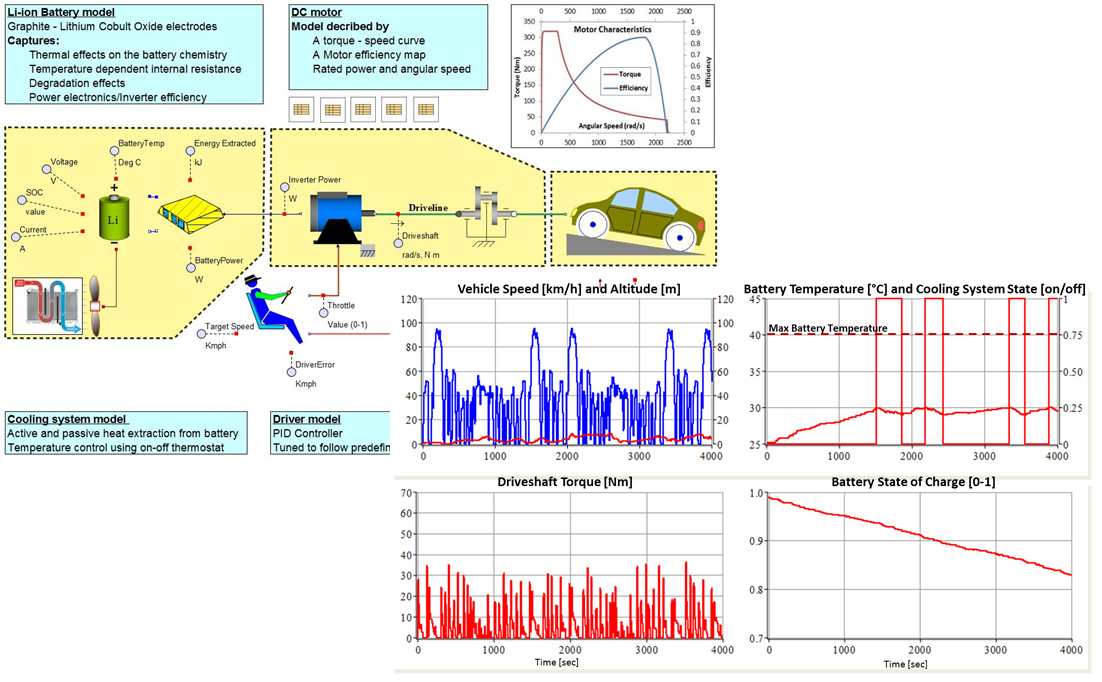
Alright, let's talk about exhaust systems. Not just the pretty chrome tips you see sticking out, but the whole flow-dynamics and sound pressure level (DB) aspects of them. We're going to dive into how integrated system representation (ISR), specifically when implemented within a model-based systems engineering (MBSE) framework, can help us understand and optimize these crucial characteristics. Think of this as leveling up your understanding beyond just bolting on a new muffler.
What is ISR and MBSE, and Why Should I Care?
Let's break down these acronyms. MBSE (Model-Based Systems Engineering) is, at its core, a formalized methodology that focuses on creating and using domain models to represent a system throughout its development lifecycle. Instead of relying solely on documents and drawings, MBSE uses interconnected models – think simulations, flow charts, equations – to describe the system's behavior, structure, and requirements. This allows for early detection of potential issues, improved communication between teams, and better overall system design.
ISR (Integrated System Representation) is a key component within MBSE. It's the way we *visually* and *mathematically* represent how the different components of a system relate to each other. Imagine a flowchart, but instead of just drawing arrows, we're plugging in real-world data, equations, and simulations to predict the performance of the entire exhaust system before we even build a prototype. This is incredibly powerful for optimization.
So, why should you, as a car enthusiast or DIY mechanic, care about this? Because it allows you to move beyond guesswork and into data-driven decision making. Want to know if that header swap will *really* give you the horsepower you’re looking for? MBSE, using an ISR, can give you a much better estimate than just reading online forums. Want to understand how that new muffler will affect your car's DB levels at different RPMs? MBSE can help with that too!
Exhaust System Flow Characteristics: The Basics
Before we dive into the modeling aspect, let's recap the fundamentals of exhaust flow. The primary goal of an exhaust system is to efficiently remove burnt gases from the engine cylinders. This seemingly simple task has a huge impact on engine performance, fuel efficiency, and emissions. Key flow characteristics to consider include:
- Backpressure: This is the pressure exerted *against* the piston as it tries to expel exhaust gases. High backpressure reduces engine efficiency and power output. Generally, lower backpressure is desirable for performance, but *zero* backpressure isn't the goal either.
- Flow Velocity: How fast the gases are moving. Too slow, and the exhaust gases don’t scavenge efficiently. Too fast, and you introduce frictional losses and potentially create unwanted noise.
- Scavenging: The process of using the exhaust pulse from one cylinder to help pull exhaust gases from another cylinder. This is especially important in multi-cylinder engines and can significantly improve volumetric efficiency.
- Temperature: Exhaust gas temperature (EGT) affects gas density and velocity. Higher EGT generally leads to faster flow, but also increased stress on components.
- Turbulence: Smooth, laminar flow is ideal. Turbulence creates resistance and reduces flow efficiency. Sharp bends, poorly designed collectors, and internal obstructions all contribute to turbulence.
Each of these characteristics is interconnected. For example, reducing backpressure might increase flow velocity, which in turn could impact scavenging. MBSE helps us understand these complex interactions.
Modeling Exhaust Flow with MBSE and ISR
Now, let's see how we can use MBSE to model these flow characteristics. We'll build a simplified example to illustrate the process. First, we need to define the system components. For a basic exhaust system, these might include:
- Exhaust Manifold/Headers: Collect exhaust gases from the cylinders.
- Catalytic Converter: Reduces emissions.
- Resonator (Optional): Reduces noise.
- Muffler: Further reduces noise.
- Piping: Connects the components.
Each of these components can be represented as a block in our ISR model. Each block has specific properties, such as:
- Dimensions: Length, diameter, cross-sectional area.
- Material Properties: Thermal conductivity, roughness.
- Flow Resistance: A measure of how much the component restricts flow. This can be represented as a pressure drop equation or a computational fluid dynamics (CFD) simulation.
- Temperature Drop: The amount of heat lost as gases flow through the component.
- Acoustic Properties: How much noise the component attenuates.
The ISR connects these blocks using relationships that represent the flow of exhaust gases. These relationships are not just visual connections; they represent mathematical equations that describe the mass flow rate, pressure, temperature, and other relevant parameters. For example, the flow rate through the catalytic converter depends on the pressure difference across it, the temperature of the exhaust gas, and the converter's internal geometry.
We can use software like Modelica or Simulink to build and simulate this model. We would input engine parameters (RPM, air-fuel ratio, exhaust gas temperature) and then run the simulation to predict the exhaust flow characteristics at different operating conditions. The software will solve the system of equations and give us values for backpressure, flow velocity, temperature, and other parameters at various points in the exhaust system.
This model can be further refined by incorporating CFD simulations of individual components. For example, we can simulate the flow through a specific header design to determine its flow resistance and identify areas of turbulence. This data can then be used to update the header block in our MBSE model.
Example: Modeling Backpressure
Let's say we want to model the backpressure created by a specific muffler. We can represent the muffler as a block with a flow resistance parameter. This parameter can be determined experimentally (by measuring the pressure drop across the muffler at different flow rates) or through CFD simulation. Once we have the flow resistance, we can plug it into our overall exhaust system model and simulate the backpressure at different engine speeds. This allows us to compare different mufflers and see how they affect engine performance.
Sound Pressure Levels (DB) and MBSE
Exhaust sound is a complex phenomenon influenced by many factors, including engine firing order, exhaust gas pulsations, and the geometry of the exhaust system. Controlling and predicting sound levels is essential for compliance with noise regulations and, let's be honest, achieving the desired sound profile.
MBSE can also be used to model the acoustic properties of an exhaust system. This involves incorporating acoustic models into the ISR. These models can predict the sound pressure level (SPL) at different frequencies based on the exhaust gas flow characteristics and the acoustic properties of the components.
Key acoustic parameters include:
- Transmission Loss: The amount of sound energy that is attenuated as it passes through a component. Mufflers are designed to have high transmission loss at specific frequencies.
- Insertion Loss: The difference in sound pressure level with and without a specific component in the system.
- Resonance Frequencies: Frequencies at which the exhaust system resonates, creating peaks in the sound spectrum.
These parameters can be determined through acoustic testing or simulation. For example, we can use finite element analysis (FEA) to simulate the acoustic behavior of a muffler and predict its transmission loss at different frequencies. This data can then be used to update the muffler block in our MBSE model.
By combining flow and acoustic models, we can predict the overall sound pressure level of the exhaust system at different engine speeds and loads. This allows us to optimize the exhaust system design to achieve the desired sound profile while meeting noise regulations. Remember, DB is measured on a logarithmic scale; a 3dB increase represents a doubling of sound intensity, and a 10dB increase is perceived as twice as loud!
Example: Predicting DB Levels
Imagine you want to add a high-flow catalytic converter but are concerned about increasing the exhaust noise. You can use MBSE to model the acoustic effect of the new converter. You would measure (or simulate) the insertion loss of the new converter and compare it to the insertion loss of the original converter. By plugging these values into your overall exhaust system model, you can predict the change in sound pressure level at different frequencies. This will help you determine if the new converter will significantly increase the exhaust noise.
Putting it All Together: A DIY Example
Let's say you're planning to upgrade your headers. Here's how you could use an MBSE approach, even without sophisticated software (although access to CFD software would be ideal):
- Research: Find flow data (CFM ratings, pressure drop) for different header designs. Look for dyno tests that show before-and-after performance changes. This is your initial data gathering for populating your "header" block.
- Simplify: Create a simplified model in a spreadsheet. Estimate the flow resistance of your existing exhaust system (catalytic converter, muffler, piping). This might involve looking up typical values for these components.
- Calculate: Use basic fluid dynamics equations (available online) to estimate the backpressure with your existing setup and then with the new headers. This will give you a rough idea of the performance improvement you can expect.
- Acoustic Considerations: Research whether the new headers are known to increase exhaust noise. Look for reviews or sound clips.
- Iterate: If the predicted performance improvement is marginal or the potential noise increase is unacceptable, consider a different header design or other exhaust modifications.
While this is a simplified approach, it demonstrates the core principles of MBSE: using models to predict system behavior and make informed decisions.
Limitations and Considerations
MBSE is a powerful tool, but it's not a magic bullet. The accuracy of the model depends on the quality of the input data and the assumptions made. It's crucial to remember these limitations:
- Model Simplification: All models are simplifications of reality. We have to make assumptions and approximations to make the model manageable.
- Data Accuracy: The accuracy of the model depends on the accuracy of the input data. Garbage in, garbage out!
- Computational Complexity: Complex models can require significant computational resources and expertise to develop and run.
- Validation: It's essential to validate the model against experimental data to ensure that it accurately predicts system behavior.
Furthermore, remember that MBSE is a *process*, not a product. It's about thinking systematically and using models to support decision-making throughout the design process. Embrace the iterative nature of modeling and be prepared to refine your models as you gain more information.
By understanding the principles of ISR and MBSE, you can take a more data-driven approach to exhaust system design and optimization. This will allow you to make informed decisions and achieve your desired performance and sound characteristics with greater confidence. Good luck, and happy wrenching!