Newton Nissan Of Gallatin Service Center
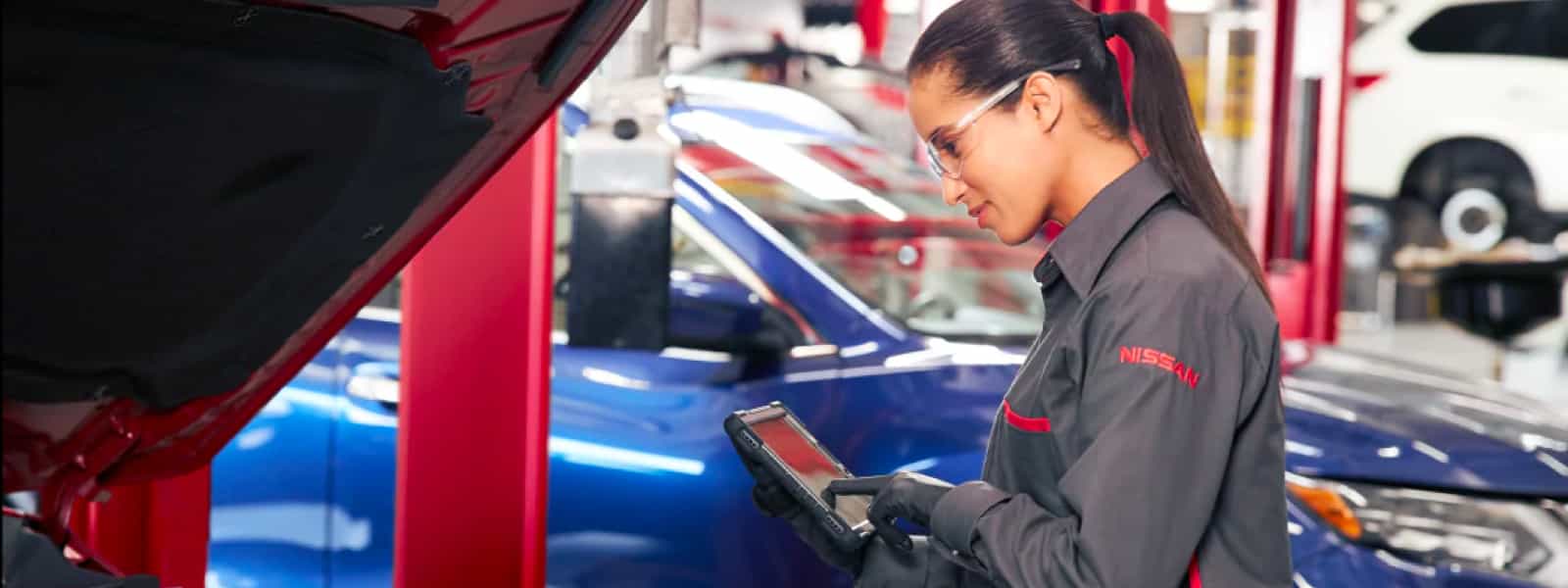
Newton Nissan of Gallatin's service center represents a modern approach to vehicle maintenance and repair, blending diagnostic technology with skilled technicians to keep a diverse array of Nissan models performing optimally. This isn't just about oil changes; it's about a comprehensive system designed for efficiency, accuracy, and customer satisfaction. Let's delve into the intricacies of what makes this service center tick.
Diagnostic Technologies: The Heart of Accurate Repairs
The cornerstone of any effective modern service center is its diagnostic capability. At Newton Nissan of Gallatin, this starts with a suite of advanced diagnostic tools provided by Nissan and other aftermarket vendors. These tools connect directly to a vehicle's onboard diagnostic (OBD) system, accessing a wealth of information about the engine, transmission, braking system, and other critical components.
Decoding the Data Stream
The OBD system, mandated in most vehicles since the mid-1990s, continuously monitors various sensors and actuators. When a problem arises, it stores a Diagnostic Trouble Code (DTC) in the vehicle's computer. The diagnostic tool retrieves these DTCs, providing technicians with an initial indication of the fault. However, the DTC is only the starting point. A code indicating a misfire in cylinder one, for example, doesn't automatically mean a faulty spark plug. It could be a bad ignition coil, a clogged fuel injector, a vacuum leak, or even a compression issue. The technician must then use their knowledge and experience, along with further diagnostic tests, to pinpoint the root cause.
Beyond the Basics: Oscilloscopes and Multimeters
While DTCs provide a starting point, more complex issues require the use of advanced diagnostic equipment. An oscilloscope, for example, allows technicians to visualize electrical signals within the vehicle. This is particularly useful for diagnosing intermittent problems or issues with sensors that are not reporting obvious errors. By observing the waveform of a sensor signal, technicians can identify irregularities like noise, dropouts, or incorrect voltage levels that would be missed by simply reading the sensor's numerical output.
A multimeter, a staple in any automotive technician's toolkit, is used to measure voltage, current, and resistance. It's invaluable for checking the integrity of wiring harnesses, identifying short circuits, and verifying the functionality of electrical components. Proper use of a multimeter requires a thorough understanding of electrical circuits and the ability to interpret the readings obtained.
Proprietary Software and Databases
Newton Nissan of Gallatin utilizes Nissan's proprietary software and databases, which provide access to service manuals, technical service bulletins (TSBs), and wiring diagrams. TSBs are crucial, as they often describe known issues with specific models and provide the recommended repair procedures. These databases are constantly updated, ensuring that technicians have the most current information available.
The Service Bay: Efficiency and Specialization
The layout of the service bay at Newton Nissan of Gallatin is carefully designed for efficiency and workflow. Each service bay is equipped with the necessary tools and equipment to perform a wide range of tasks. Furthermore, the service center often employs a team of technicians with varying levels of expertise and specialization.
Specialized Technicians
Some technicians may specialize in specific areas, such as engine repair, transmission repair, or electrical systems. This specialization allows them to develop a deeper understanding of these systems and to become more proficient at diagnosing and repairing them. For example, a technician specializing in transmission repair will have extensive experience with rebuilding transmissions and will be familiar with the common failure points of various transmission models.
The service advisor plays a critical role in the service process. They are the point of contact for the customer and are responsible for communicating the customer's concerns to the technicians. The service advisor also provides updates to the customer on the progress of the repairs and explains the recommended repairs. A good service advisor will have a strong understanding of automotive systems and the repair process.
Tools and Equipment
Beyond basic hand tools, the service bay is equipped with specialized equipment such as:
- Lift systems: Allowing technicians to safely raise vehicles to access the undercarriage.
- Tire changers and balancers: For tire maintenance and replacement.
- Alignment machines: To ensure proper wheel alignment, maximizing tire life and handling.
- Fluid exchange machines: For efficient and clean fluid changes, such as coolant, transmission fluid, and brake fluid.
Parts and Inventory Management
A well-stocked parts department is essential for minimizing downtime and ensuring that repairs can be completed quickly. Newton Nissan of Gallatin maintains an inventory of commonly used parts, such as filters, brake pads, and spark plugs. They also have access to a larger network of parts suppliers, allowing them to quickly obtain less common parts. Efficient inventory management is crucial for minimizing costs and maximizing customer satisfaction. A computerized inventory system tracks parts usage and automatically reorders parts as needed.
Genuine Nissan Parts vs. Aftermarket Parts
Newton Nissan of Gallatin typically uses genuine Nissan parts, which are designed specifically for Nissan vehicles and are backed by a warranty. While aftermarket parts may be less expensive, they may not meet the same quality standards as genuine parts. Using genuine parts helps to ensure that the vehicle performs as intended and that the repairs are long-lasting.
The Service Process: A Step-by-Step Approach
The service process at Newton Nissan of Gallatin typically follows these steps:
- Customer Check-in: The customer meets with a service advisor, who gathers information about the vehicle's problems and the customer's concerns.
- Vehicle Inspection: A technician performs a thorough inspection of the vehicle to identify any potential problems. This may include a visual inspection, as well as diagnostic testing.
- Diagnosis: Based on the inspection and diagnostic testing, the technician determines the root cause of the problem.
- Repair Recommendation: The service advisor explains the recommended repairs to the customer, including the cost and estimated time to completion.
- Repair Execution: The technician performs the necessary repairs, using high-quality parts and following proper procedures.
- Quality Control: After the repairs are completed, the technician performs a quality control check to ensure that the repairs were done correctly and that the vehicle is operating properly.
- Customer Check-out: The service advisor reviews the repairs with the customer and answers any questions. The customer then pays for the services and receives their vehicle.
Training and Certification
The technicians at Newton Nissan of Gallatin are required to undergo ongoing training and certification to stay up-to-date on the latest technologies and repair procedures. Nissan offers a comprehensive training program for its technicians, which includes both classroom instruction and hands-on training. Certification programs, such as those offered by the National Institute for Automotive Service Excellence (ASE), provide independent validation of a technician's skills and knowledge. Continuous learning is crucial in the ever-evolving automotive industry.
The Future of Automotive Service
The automotive industry is undergoing rapid change, with the introduction of electric vehicles, autonomous driving systems, and connected car technologies. These advancements will require technicians to develop new skills and expertise. Newton Nissan of Gallatin is committed to investing in the training and equipment necessary to stay ahead of the curve and provide its customers with the highest quality service. The service center of the future will be even more data-driven, relying on real-time vehicle data and predictive analytics to proactively identify and address potential problems before they occur.
The blend of human expertise and technological advancement is the key to ensuring the continued reliability and performance of modern vehicles.