Nissan 240sx Carbon Fiber Parts
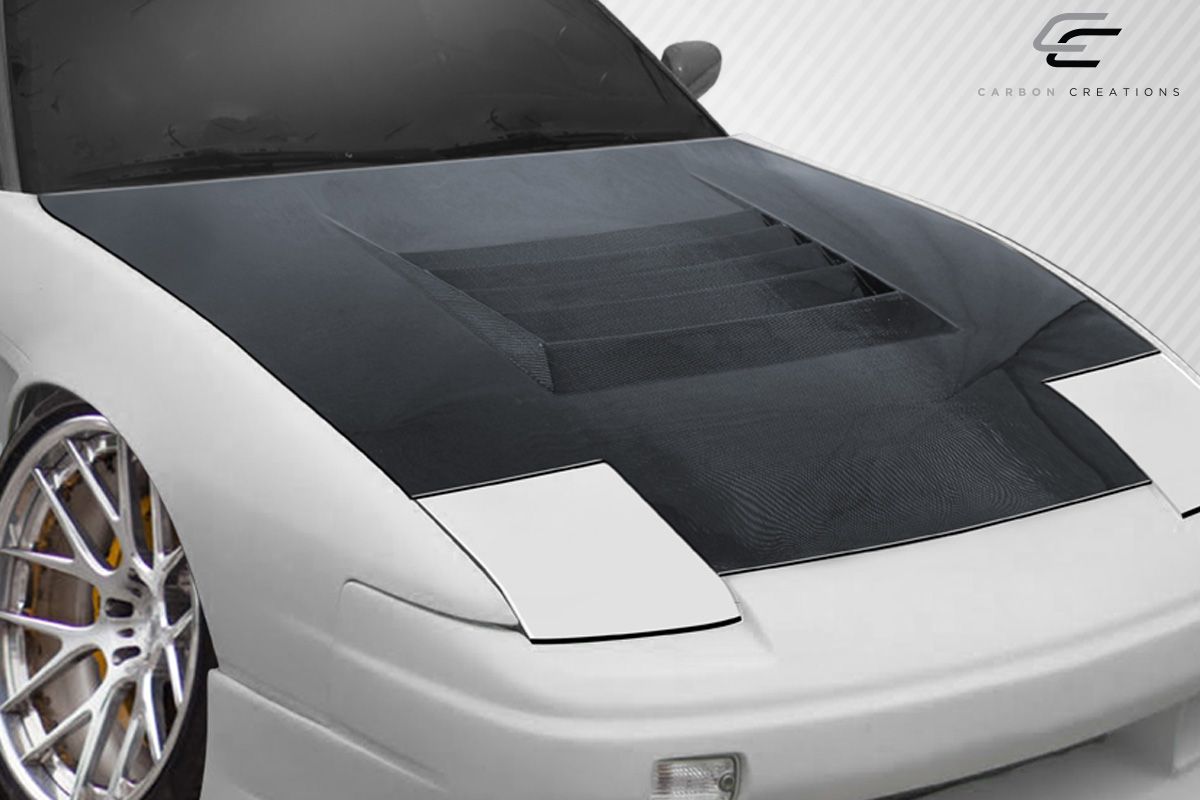
The Nissan 240SX, a darling of the tuning and drifting scenes, has enjoyed a long and fruitful aftermarket life. Among the many modifications available, carbon fiber parts stand out for their potential to improve both performance and aesthetics. But what truly makes carbon fiber a desirable material, and how are these components made specifically for the 240SX? Let's delve into the world of 240SX carbon fiber upgrades.
Understanding Carbon Fiber: More Than Just Looks
Carbon fiber isn't just a fancy texture; it's a high-performance composite material. To understand its advantages, we need to understand its composition. Carbon fiber is typically composed of thousands of tiny strands of carbon, thinner than a human hair. These strands are woven together to create a fabric, and then impregnated with a resin (typically epoxy). The resin hardens, binding the carbon fibers together and providing the structural matrix.
The incredible strength-to-weight ratio of carbon fiber stems from the properties of the carbon filaments themselves. Carbon has a high tensile strength, meaning it can withstand a significant amount of pulling force before breaking. When arranged in a matrix with a strong resin, this tensile strength is leveraged to create a material that is exceptionally strong for its weight.
For 240SX applications, the benefits are numerous:
- Weight Reduction: This is perhaps the most significant advantage. Replacing steel or fiberglass components with carbon fiber equivalents can drastically reduce the overall weight of the car, improving acceleration, braking, and handling.
- Increased Stiffness: Carbon fiber components, especially those designed with strategically oriented fiber layers, can be significantly stiffer than their stock counterparts. This reduces flex and improves handling precision, particularly in areas like hoods, trunks, and body panels.
- Aesthetics: Let's face it, the look of carbon fiber is undeniably appealing. It adds a sporty and high-tech aesthetic to any vehicle.
The Manufacturing Process: From Fabric to Finished Part
Creating carbon fiber parts for the 240SX is a multi-step process that requires precision and attention to detail. Different manufacturing techniques yield different results in terms of cost, strength, and finish. Here's a look at the common methods:
1. Wet Layup: The Budget-Friendly Option
Wet layup is the simplest and most affordable method. It involves manually applying resin to a layer of carbon fiber fabric placed inside a mold. The resin is typically applied with a brush or roller, and air bubbles are worked out to ensure proper adhesion. Once the resin cures, the part is removed from the mold. Wet layup is often used for cosmetic parts like dashboard trim or mirror covers where ultimate strength isn't critical.
While cost-effective, wet layup parts tend to be heavier and less strong than those produced using more advanced methods due to inconsistencies in resin application and the presence of air pockets.
2. Vacuum Bagging: Improving Resin Infusion
Vacuum bagging builds upon the wet layup process by adding a vacuum to the equation. After the resin is applied, the part is sealed in a vacuum bag. The vacuum pressure forces excess resin out of the fabric and compacts the carbon fibers, resulting in a stronger and lighter part with fewer voids. Vacuum bagging is commonly used for hoods, spoilers, and other moderate-strength components.
3. Resin Infusion: Precise Control of Resin Distribution
Resin infusion, also known as vacuum infusion, takes vacuum bagging a step further. Instead of applying resin directly to the fabric, the dry carbon fiber is placed in the mold, and then a vacuum is applied. Resin is then drawn into the fabric through strategically placed inlet ports. This ensures a more uniform resin distribution and minimizes the risk of air pockets. Resin infusion is suitable for larger and more complex parts like doors and fenders.
4. Pre-Preg: The Pinnacle of Performance
Pre-preg (pre-impregnated) carbon fiber involves using carbon fiber fabric that has already been impregnated with resin by the manufacturer. This ensures a precise resin-to-fiber ratio and minimizes the risk of voids. Pre-preg parts are typically cured in an autoclave, a pressurized oven that provides uniform heat and pressure, resulting in exceptionally strong and lightweight components. This method is expensive and typically reserved for high-performance applications like race car body panels.
The Mold: The Key to Consistency Regardless of the manufacturing method, the mold plays a crucial role in the final product. Molds are typically made from fiberglass, aluminum, or steel and must be precisely shaped to match the desired dimensions of the 240SX part. The mold's surface finish also affects the appearance of the carbon fiber part.
240SX Carbon Fiber Parts: Common Applications
The 240SX aftermarket offers a wide range of carbon fiber components. Here are some of the most popular applications:
- Hoods: Carbon fiber hoods are a common upgrade, offering significant weight savings over the stock steel hood. They can also improve engine bay cooling with strategically placed vents.
- Trunk Lids: Similar to hoods, carbon fiber trunk lids reduce weight and improve the car's rearward weight distribution.
- Doors: Replacing steel doors with carbon fiber doors can drastically reduce weight, but this is typically done for dedicated track cars due to safety considerations regarding side impact protection.
- Fenders: Carbon fiber fenders can widen the car's stance and allow for wider wheels and tires. They also contribute to weight reduction.
- Spoilers and Wings: Carbon fiber spoilers and wings enhance the car's aerodynamics, improving downforce and stability at high speeds.
- Interior Trim: Carbon fiber trim pieces, such as dashboard inserts and door panels, add a touch of sporty elegance to the interior.
Considerations When Choosing Carbon Fiber Parts
Not all carbon fiber parts are created equal. When shopping for 240SX carbon fiber upgrades, consider the following factors:
- Manufacturing Method: As discussed earlier, the manufacturing method significantly impacts the strength, weight, and cost of the part. Choose a method appropriate for your needs and budget.
- Resin Type: Epoxy resin is the most common type, offering good strength and heat resistance. However, other resins like vinyl ester are also used.
- Fiber Orientation: The way the carbon fiber fabric is layered can affect the part's strength and stiffness. Look for parts with strategically oriented fiber layers to maximize performance.
- Finish: Carbon fiber parts can be finished with a clear coat to protect the carbon fiber and enhance its appearance. Check for a smooth, even finish without any blemishes.
- Fitment: Ensure that the part is designed specifically for your 240SX model year. Poor fitment can lead to installation headaches and potential damage to the car.
- Reputation of the Manufacturer: Buy from reputable manufacturers with a track record of producing high-quality carbon fiber parts. Read reviews and do your research before making a purchase.
Installation and Maintenance
Installing carbon fiber parts typically requires some mechanical skill. Depending on the part, you may need to remove existing components, drill holes, and attach the new part using bolts, screws, or adhesive. It's always a good idea to consult with a professional if you're unsure about the installation process.
Maintaining carbon fiber parts is relatively simple. Clean them regularly with a mild soap and water solution. Avoid using abrasive cleaners, as they can damage the clear coat. For parts exposed to sunlight, consider applying a UV protectant to prevent fading and discoloration.
Conclusion: A Powerful Upgrade
Carbon fiber parts offer a compelling combination of performance benefits and aesthetic appeal for the Nissan 240SX. By understanding the manufacturing process, material properties, and key considerations, you can make informed decisions and choose the right carbon fiber upgrades to enhance your car's performance and style. While the initial investment can be higher than traditional materials, the weight savings, increased stiffness, and undeniably cool look make carbon fiber a worthwhile upgrade for many 240SX enthusiasts. Remember to prioritize quality and proper installation to ensure long-lasting performance and enjoyment. Good luck and happy tuning!