Nissan 240sx Hatchback Structural Rigidity Analysis
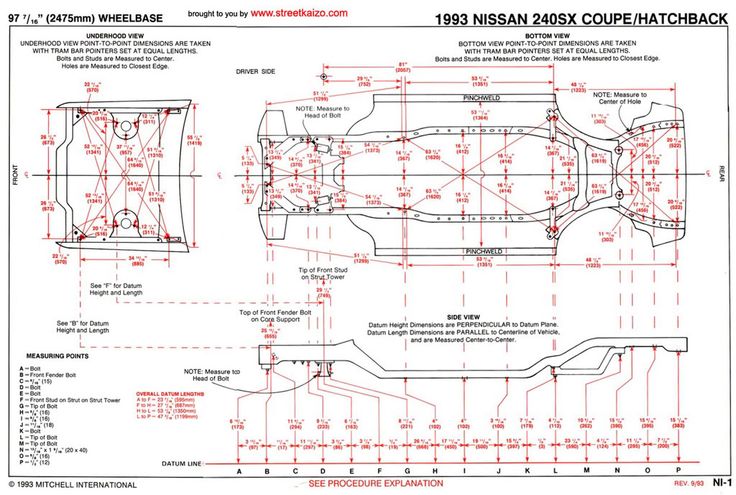
The Nissan 240SX, particularly the hatchback model (often referred to as the "S13" in its first generation and "S14" in its second), enjoys a legendary status in the automotive world. Revered for its affordability, rear-wheel-drive configuration, and inherent tunability, it has become a favorite among drifters, track enthusiasts, and car modification aficionados. However, like any vehicle, understanding its structural strengths and weaknesses is crucial for maximizing its performance and ensuring safety, especially when pushing the limits or undertaking significant modifications. This analysis delves into the structural rigidity of the Nissan 240SX hatchback, exploring its design, vulnerabilities, and common reinforcement methods.
Understanding Structural Rigidity: A Foundation for Performance
Before diving into the specifics of the 240SX, it’s essential to understand what we mean by "structural rigidity." Simply put, it refers to a vehicle's resistance to deformation under stress. A structurally rigid car will flex less, resulting in improved handling, more predictable response to driver inputs, and enhanced safety in the event of a collision. Conversely, a vehicle with poor structural rigidity will exhibit more flex, leading to vague handling, increased tire wear, and potentially compromised safety.
In the context of performance driving, structural rigidity is paramount. When cornering, a car experiences significant lateral forces. If the chassis flexes excessively, the suspension geometry can be compromised, leading to unpredictable handling and reduced grip. Similarly, during braking, torsional forces can twist the chassis, making it difficult to maintain a stable trajectory. A stiffer chassis provides a more stable platform for the suspension to operate, allowing for more precise control and improved overall performance.
The 240SX Hatchback: A Factory Overview
The Nissan 240SX hatchback was designed as an affordable sports coupe. While it offered a compelling driving experience straight from the factory, its primary focus wasn't necessarily extreme rigidity. Its unibody construction, while offering decent strength for everyday driving, has limitations when subjected to the stresses of competitive motorsports or highly modified street cars.
Key Structural Components
Several key components contribute to the overall structural rigidity of the 240SX hatchback:
- Unibody Construction: The 240SX utilizes a unibody construction, where the body and frame are integrated into a single unit. This design is lighter and more efficient to manufacture than a traditional body-on-frame design, but it can be more prone to flex under extreme stress.
- Chassis Rails: These longitudinal beams run along the length of the car and provide the primary structural support. They are crucial for resisting bending forces.
- Strut Towers: These are the mounting points for the front and rear suspension struts. They are subjected to significant loads and are often a point of weakness in unreinforced 240SXs.
- Firewall: The firewall separates the engine compartment from the passenger cabin. It provides structural support and helps to isolate the cabin from noise and heat.
- Floor Pan: The floor pan provides a rigid base for the passenger compartment and contributes to the overall torsional rigidity of the car.
- Hatch Area: The hatchback design, while practical, inherently introduces a potential weak point compared to a coupe or sedan due to the large opening at the rear of the vehicle.
Vulnerabilities and Weak Points
Despite its strengths, the 240SX hatchback has several inherent weaknesses that can become apparent under increased stress, especially with modifications or aging:
- Strut Tower Flex: The strut towers are prone to flexing, especially under hard cornering. This flex can negatively impact handling and tire wear.
- Chassis Flex: The unibody construction can exhibit noticeable flex, particularly in the floor pan and along the chassis rails. This flex can lead to vague handling and reduced predictability.
- Hatch Opening: The large opening for the hatch significantly reduces the torsional rigidity of the rear of the car. This can be particularly noticeable under hard acceleration or braking.
- Corrosion: Rust can significantly weaken the structural integrity of the 240SX, particularly in areas prone to moisture accumulation, such as the floor pan, chassis rails, and strut towers. Cars that have lived in areas with harsh winters or coastal environments are especially susceptible. Regular inspection and rust prevention are crucial for maintaining structural integrity.
- Weld Fatigue: Over time, the factory welds can weaken due to repeated stress and vibration. This can lead to cracks and reduced rigidity.
Reinforcement Methods: Strengthening the 240SX Hatchback
Fortunately, several methods can be used to reinforce the 240SX hatchback and improve its structural rigidity. These modifications range from simple bolt-on parts to more complex welding and fabrication techniques.
Bolt-On Reinforcements
These are generally the easiest and most affordable methods to implement:
- Strut Tower Braces: These braces connect the strut towers to each other, reducing flex and improving handling. They are available for both the front and rear of the car. A high-quality strut tower brace can make a noticeable difference.
- Lower Tie Bars: These bars connect the lower suspension arms, further reducing flex and improving handling.
- Sway Bars (Anti-Roll Bars): While primarily for suspension tuning, stiffer sway bars can help distribute load and reduce body roll, indirectly improving the perceived rigidity of the car.
- Subframe Collars: These collars fill the gaps between the subframe and the chassis, reducing subframe movement and improving handling.
Welded Reinforcements
These modifications require welding and are generally more involved but offer a more significant improvement in structural rigidity:
- Seam Welding: This involves welding along the factory seams of the unibody structure to increase its strength and rigidity. Seam welding is a common and effective method.
- Roll Cage/Roll Bar: A roll cage or roll bar is a significant structural addition that provides a dramatic improvement in rigidity and, more importantly, enhances safety in the event of a rollover. They tie multiple points of the chassis together, creating a rigid structure.
- Chassis Reinforcement Plates: These plates can be welded to areas prone to stress, such as the strut towers, chassis rails, and floor pan, to reinforce them and prevent cracking.
- Custom Reinforcement: Fabricating and welding custom reinforcement bars or plates can address specific areas of weakness based on the intended use of the car.
Material Selection and Preparation
When undertaking any reinforcement project, material selection and preparation are critical. Using high-quality steel and proper welding techniques is essential to ensure the longevity and effectiveness of the modifications. Always consult with a qualified welder or fabricator.
Furthermore, thoroughly cleaning and preparing the metal surfaces before welding is crucial for achieving strong and durable welds. Removing any rust, paint, or other contaminants will ensure proper adhesion and prevent premature failure.
Considerations and Cautions
Before undertaking any structural reinforcement project, it's important to consider the following:
- Intended Use: The type and extent of reinforcement required will depend on the intended use of the car. A daily driver will require less reinforcement than a dedicated drift car.
- Budget: Structural reinforcement can be expensive, especially if welding and fabrication are involved. Plan your budget accordingly.
- Expertise: Welding and fabrication require specialized skills and equipment. Unless you have the necessary experience, it's best to leave these tasks to a qualified professional.
- Weight: Adding reinforcement can increase the weight of the car, which can negatively impact performance. It's important to strike a balance between rigidity and weight.
- Legality: Some modifications may not be legal in all jurisdictions. Check your local laws before undertaking any modifications.
- Hidden Rust: The biggest factor you can't often see is hidden rust. Rust compromises the entire integrity of any reinforcement. Always inspect suspect areas thoroughly before welding.
Conclusion
The Nissan 240SX hatchback is a fantastic platform for modification and performance driving. However, understanding its structural limitations is crucial for maximizing its potential and ensuring safety. By addressing its inherent weaknesses through appropriate reinforcement methods, you can significantly improve its handling, predictability, and overall performance. Whether you're building a dedicated track car or simply want to improve the handling of your daily driver, reinforcing the chassis of your 240SX is a worthwhile investment. Remember to carefully consider your needs, budget, and expertise before undertaking any modifications, and always prioritize safety and quality workmanship. Investing in the structural integrity of your 240SX will undoubtedly translate to a more enjoyable and rewarding driving experience. And, perhaps most importantly, consulting with experienced 240SX owners and qualified professionals is invaluable in making informed decisions and achieving optimal results.