Nissan Rogue License Plate Screws Stuck
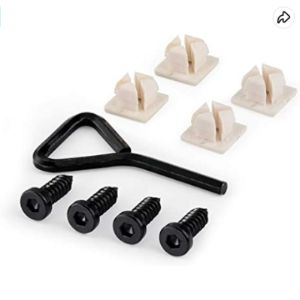
The humble license plate screw. It seems innocuous enough, a simple fastener holding your vehicle's identification tag in place. But anyone who's wrenched on cars for any length of time knows that these little buggers can become a major headache. The Nissan Rogue, in particular, seems prone to the dreaded phenomenon of stuck license plate screws. This article delves into the technical reasons why this happens and explores various methods for freeing those stubbornly seized fasteners.
The Culprits: Corrosion and Dissimilar Metals
At the heart of most stuck license plate screw problems lies corrosion. But it's not just any corrosion; it's often a specific type called galvanic corrosion. To understand this, we need to consider the materials involved.
Galvanic Corrosion Explained
Galvanic corrosion occurs when two dissimilar metals are in electrical contact in the presence of an electrolyte. In the case of a Nissan Rogue license plate, the steel screws often thread into a steel (or sometimes aluminum) bracket attached to the vehicle's body. While steel-on-steel might seem less problematic, the different grades of steel, manufacturing processes, and even surface treatments can create a potential difference. Rainwater, road salt, and other contaminants act as the electrolyte, facilitating the flow of electrons between the metals. This electron flow causes one metal (the anode) to corrode at an accelerated rate, while the other (the cathode) is protected.
In this scenario, the screw often acts as the anode and corrodes, forming rust and corrosion products within the threads. This effectively welds the screw to the bracket, making removal extremely difficult.
Rust and Thread Lock: Further Complications
Even without dissimilar metal issues, simple rust can seize the screws. The constant exposure to the elements, especially in regions with harsh winters and salted roads, accelerates the rusting process. Additionally, some owners or dealerships might apply thread-locking compounds like Loctite during installation. While intended to prevent screws from loosening due to vibration, these compounds can harden over time and contribute to the seizure problem.
Diagnosis: Is it Really Stuck?
Before resorting to drastic measures, it's essential to properly diagnose the issue. Sometimes, a screw that appears stuck is simply being attacked with the wrong tool or insufficient force. Here's a simple checklist:
- Verify the Screwdriver Type: Are you using a Phillips head screwdriver? Ensure it's the correct size (usually #2) for the screw. Using an incorrect size will strip the screw head.
- Apply Downward Pressure: A common mistake is simply twisting the screwdriver without applying sufficient downward pressure. This causes the screwdriver to slip and round out the screw head. Apply firm, consistent downward pressure while turning.
- Check for Stripped Heads: If the screwdriver slips easily, the screw head might already be stripped. In this case, you'll need to employ specialized techniques (discussed later).
- Inspect for Visible Corrosion: Examine the screw head and the surrounding area for signs of rust or corrosion. This will give you a clue about the severity of the problem.
Removal Techniques: A Step-by-Step Guide
Once you've confirmed that the screws are genuinely stuck, it's time to employ some problem-solving techniques. Start with the least aggressive methods and gradually escalate as needed.
1. Penetrating Oil: The First Line of Defense
Penetrating oil is your best friend when dealing with corroded fasteners. Products like PB Blaster, Liquid Wrench, and Kroil are designed to seep into the threads and break down rust and corrosion.
- Application: Generously spray the penetrating oil around the screw head and where the screw enters the bracket.
- Soaking Time: Allow the oil to soak for at least 15-30 minutes. For severely corroded screws, let it soak overnight. Reapply the oil periodically to keep the area saturated.
- Tapping: After soaking, gently tap the screw head with a hammer. This vibration can help the oil penetrate further and loosen the corrosion.
- Attempt Removal: Use a properly sized Phillips head screwdriver with firm downward pressure to attempt to remove the screw.
2. Impact Driver: Adding Some Force
An impact driver delivers both rotational force and downward force, making it significantly more effective than a standard screwdriver. This tool is especially useful for breaking loose stubborn screws.
- Select the Bit: Choose a Phillips head bit that fits the screw snugly.
- Insert and Position: Insert the bit into the impact driver and position it firmly on the screw head, ensuring the bit is fully seated.
- Apply Force: Hold the impact driver firmly against the screw and strike the back of the driver with a hammer. The impact will both rotate and push the bit into the screw, helping to break it free.
- Repeat as Needed: Repeat the process several times, rotating the screw slightly with each impact.
Caution: Use an impact driver carefully. Excessive force can strip the screw head or even damage the surrounding bracket.
3. Heat: Expanding the Metal
Applying heat can help to break the bond between the screw and the bracket. Heat causes the metal to expand, potentially creating small gaps that allow penetrating oil to work its way in. A heat gun or a small butane torch can be used for this purpose.
- Apply Heat: Carefully heat the screw head and the surrounding bracket for a few seconds. Avoid overheating, which can damage the paint or surrounding plastic components.
- Penetrating Oil: Immediately after heating, apply penetrating oil to the area. The heat will help the oil to wick into the threads.
- Attempt Removal: Use a screwdriver or impact driver to attempt to remove the screw.
Safety Note: Exercise extreme caution when using heat near a vehicle. Keep a fire extinguisher nearby and avoid heating flammable materials.
4. Screw Extractor: A Last Resort
If the screw head is stripped or other methods have failed, a screw extractor might be necessary. Screw extractors are specialized tools designed to grip the inside of a damaged screw head and allow you to turn it out. There are different types of screw extractors available, including tapered extractors and fluted extractors.
- Prepare the Screw: Use a center punch to create a small indentation in the center of the screw head. This will help to guide the drill bit.
- Drill a Pilot Hole: Using a drill bit slightly smaller than the diameter of the screw extractor, drill a pilot hole into the screw head.
- Insert the Extractor: Insert the screw extractor into the pilot hole.
- Turn the Extractor: Use a wrench or socket to turn the screw extractor counterclockwise. As you turn, the extractor will bite into the screw head and allow you to unscrew it.
Important: Use caution when using a screw extractor. If the extractor breaks off inside the screw, it can be very difficult to remove. Use a high-quality extractor and apply steady, even pressure.
5. Drilling Out the Screw: When All Else Fails
As a very last resort, you can drill out the screw completely. This method destroys the screw but leaves the bracket intact.
- Center Punch: Center punch the screw head.
- Drill with Increasing Sizes: Start with a small drill bit and gradually increase the size until you've removed the head of the screw. Be extremely careful not to damage the threads in the bracket.
- Remove the Remaining Shank: Once the head is removed, the remaining shank of the screw may be easy to remove with pliers, or you can try carefully drilling it out.
- Thread Repair (If Necessary): If the threads in the bracket are damaged, you may need to use a thread repair kit (e.g., Heli-Coil) to restore them.
Caveat: Drilling is risky. It's easy to damage the bracket and even the vehicle's body. Proceed with extreme caution and patience.
Prevention: Avoiding Stuck Screws in the Future
Prevention is always better than cure. Here's how to minimize the risk of stuck license plate screws on your Nissan Rogue:
- Use Stainless Steel Screws: Stainless steel is highly resistant to corrosion and is an excellent choice for license plate screws.
- Apply Anti-Seize Compound: Apply a thin layer of anti-seize compound to the threads of the screws before installing them. This will prevent corrosion and make removal much easier in the future.
- Isolate Dissimilar Metals: If possible, use nylon washers between the screw and the bracket to isolate dissimilar metals and prevent galvanic corrosion.
- Regular Inspection: Periodically inspect the license plate screws for signs of corrosion. If you notice any rust or corrosion, remove the screws, clean the threads, and apply fresh anti-seize compound.
Conclusion
Dealing with stuck license plate screws on a Nissan Rogue can be frustrating, but by understanding the underlying causes and employing the appropriate removal techniques, you can successfully overcome this common automotive annoyance. Remember to start with the least aggressive methods and gradually escalate as needed, and always prioritize safety and caution.