Oem Front Bumper Impact Absorption Characteristics
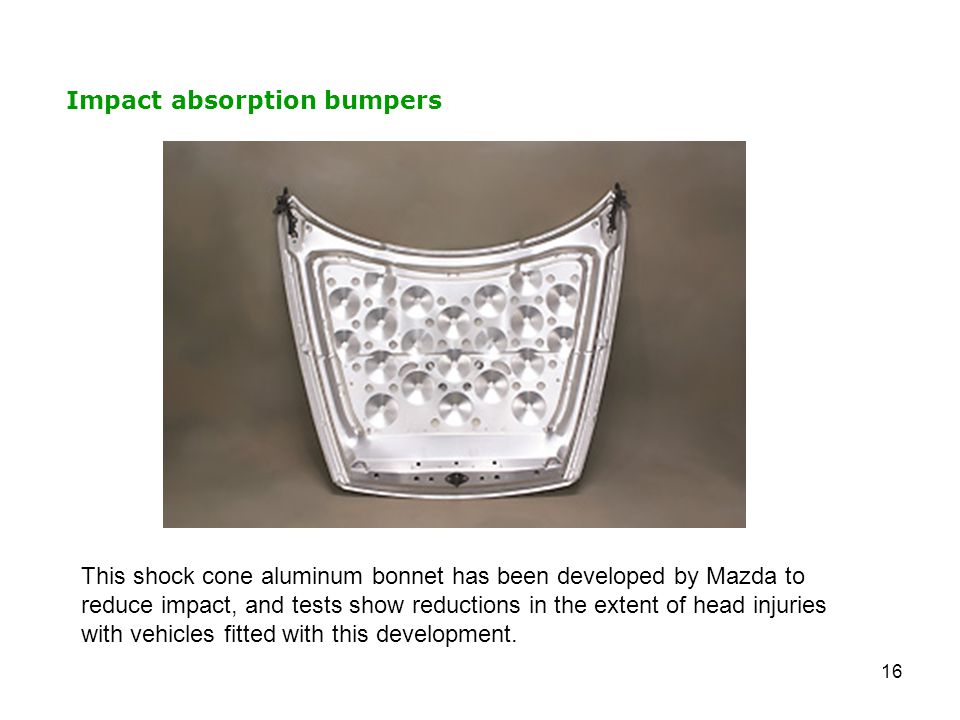
Alright, let's dive deep into the often-overlooked world of OEM (Original Equipment Manufacturer) front bumper impact absorption. You might think it's just a piece of plastic designed to look good, but there's a surprisingly complex engineering effort behind ensuring it protects you and your car in a low-speed collision. We're going to break down the key components, materials, and design principles that contribute to its impact absorption capabilities.
Understanding the System: More Than Just a Bumper Cover
First, it's crucial to understand that the front bumper is rarely, if ever, a single piece doing all the work. It's a system of interconnected components designed to work together to absorb energy and minimize damage during an impact. The visible part, the bumper cover, is often the least critical component in terms of energy absorption. Think of it as the first line of defense, primarily designed for aesthetics and pedestrian safety (more on that later).
Here’s a breakdown of the typical components:
- Bumper Cover: Usually made of a flexible plastic like Polypropylene (PP), Thermoplastic Olefin (TPO), or Acrylonitrile Butadiene Styrene (ABS). Its primary function is to provide the vehicle's styling.
- Energy Absorber: This is the workhorse of the system. Typically made of expanded polypropylene (EPP), expanded polystyrene (EPS), or a similar foam material, its purpose is to crush and deform under impact, dissipating kinetic energy.
- Bumper Reinforcement Bar (or Impact Bar): A rigid structural member, usually made of high-strength steel or aluminum. It's the primary load-bearing component, transferring impact forces to the vehicle's frame.
- Mounting Brackets: Connect the bumper reinforcement bar to the vehicle's frame. These brackets are often designed with specific deformation characteristics to further manage impact forces.
Material Properties and Their Roles
Each material used in the bumper system is selected for specific properties that contribute to its overall performance:
- Plastic Bumper Covers: Need to be flexible to withstand minor impacts without cracking. TPO is often preferred for its excellent impact resistance, even at low temperatures. PP is more common but can become brittle in cold weather. ABS provides a good balance of strength and flexibility but can be more susceptible to UV degradation.
- Energy Absorbers (Foams): The key property here is controlled crushability. EPP and EPS are designed to deform in a predictable manner, absorbing energy as they compress. The density of the foam determines its stiffness and energy absorption capacity. Higher density foams are stiffer and can absorb more energy but also transmit more force to the vehicle frame. The design often incorporates crush initiators – strategically placed grooves or perforations – that dictate how and where the foam will collapse.
- Reinforcement Bars: Must be strong enough to resist bending and transmit impact forces to the frame rails. High-strength steel is a common and cost-effective choice. Aluminum offers a weight savings but can be more expensive and may require different joining techniques. The shape and thickness of the reinforcement bar are carefully calculated to optimize its strength and stiffness.
Impact Absorption: How It Works
The sequence of events during a low-speed impact (typically up to 5 mph, the standard for bumper testing in many regions) is as follows:
- Initial Contact: The bumper cover makes initial contact with the object. Its flexibility allows it to deform without significant damage, absorbing a small amount of energy.
- Energy Absorber Engagement: As the impact force increases, the bumper cover transmits the load to the energy absorber. The foam begins to crush and deform, absorbing the majority of the kinetic energy. This crushing process converts the kinetic energy of the impact into heat and deformation work.
- Reinforcement Bar Activation: If the impact force exceeds the capacity of the energy absorber, the reinforcement bar comes into play. It distributes the remaining force across the vehicle's frame, preventing or minimizing damage to more critical components like the radiator, engine, and chassis.
- Bracket Deformation (If Applicable): The mounting brackets may be designed to deform in a controlled manner, acting as a final safety net to absorb any remaining energy and prevent damage to the frame rails.
Key Design Considerations
OEM bumper systems are carefully engineered to meet specific performance requirements. Here are some critical design considerations:
- Impact Speed: The system is designed to absorb energy effectively within a specific range of impact speeds. Exceeding this range can lead to component failure and increased damage.
- Impact Angle: The angle of impact can significantly affect the performance of the system. OEM designs are typically optimized for frontal impacts, but they also provide some protection in angled impacts.
- Pedestrian Safety: Modern bumper designs increasingly incorporate features to mitigate pedestrian injuries in the event of a collision. This includes using softer materials in the lower part of the bumper to reduce leg injuries and shaping the bumper to help lift the pedestrian onto the hood rather than under the vehicle.
- Vehicle Weight and Frame Stiffness: The bumper system must be compatible with the vehicle's weight and frame stiffness. A heavier vehicle requires a more robust bumper system to absorb the same amount of energy.
- Manufacturing Cost and Complexity: OEMs must balance performance requirements with cost considerations. The design should be relatively simple to manufacture and assemble, using readily available materials.
The Role of Finite Element Analysis (FEA)
Modern automotive engineers heavily rely on Finite Element Analysis (FEA) software to simulate and optimize bumper system performance. FEA allows them to model the behavior of the system under various impact scenarios, predict stress and strain distributions, and identify potential weaknesses in the design. This helps them to refine the design before building physical prototypes, saving time and money.
Using FEA, engineers can virtually test different materials, shapes, and configurations to achieve the desired impact absorption characteristics. This allows for a more efficient and data-driven design process.
Modifying Your Bumper: Proceed with Caution
While aftermarket bumpers can enhance the appearance of your vehicle, it's crucial to understand that they may not offer the same level of impact protection as the OEM bumper system. Many aftermarket bumpers are designed primarily for aesthetics and off-road use and may not have been subjected to the same rigorous testing and engineering as OEM bumpers.
If you're considering replacing your OEM bumper, ask yourself these questions:
- Is the aftermarket bumper certified to meet relevant safety standards? Look for certifications from organizations like the Insurance Institute for Highway Safety (IIHS) or the National Highway Traffic Safety Administration (NHTSA).
- What materials are used in the bumper's construction? Ensure that the materials are of high quality and suitable for impact absorption.
- Does the bumper have an integrated energy absorber? A proper energy absorber is essential for mitigating low-speed impact damage.
- How does the bumper attach to the vehicle's frame? Ensure that the mounting brackets are robust and securely attached to the frame.
Replacing or modifying your bumper can have implications for your vehicle's safety rating and insurance coverage. Always consult with a qualified mechanic or automotive engineer before making any significant modifications.
In conclusion, the OEM front bumper is a carefully engineered system designed to protect your vehicle and its occupants in low-speed collisions. Understanding its components, materials, and design principles can help you make informed decisions about modifications and ensure that your vehicle remains safe and compliant with regulations. Remember, safety should always be your top priority.