One-piece Driveshaft Material And Balance Considerations
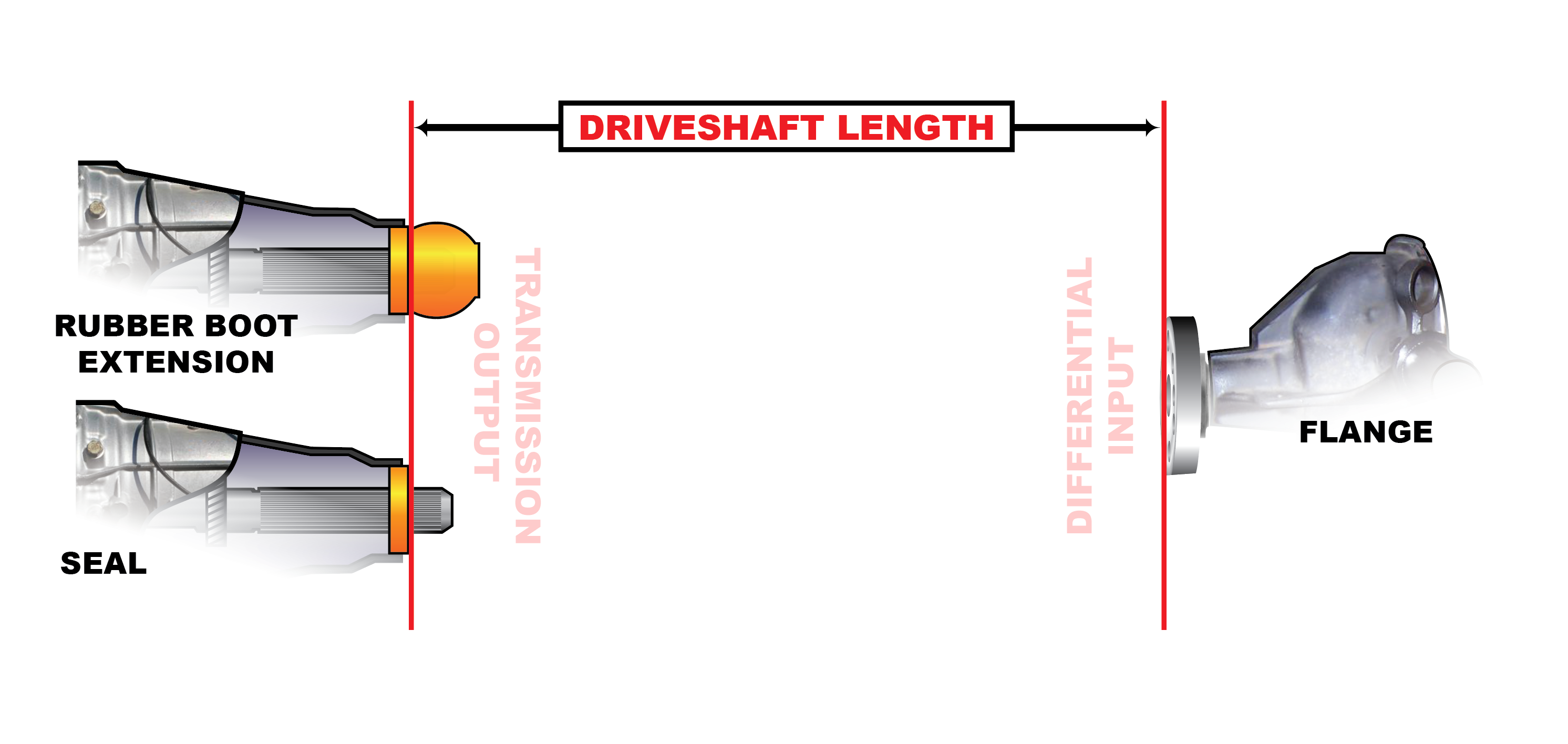
Driveshafts are crucial components in vehicles with rear-wheel drive, four-wheel drive, and all-wheel drive systems. They transmit rotational power from the transmission to the differential, which then powers the wheels. A common type of driveshaft is the one-piece driveshaft, known for its simplicity and often preferred in performance applications. This article will delve into the materials used in one-piece driveshafts and the critical balance considerations that ensure smooth and efficient power transfer.
One-Piece Driveshaft Material Selection
The choice of material for a one-piece driveshaft is paramount, directly impacting its strength, weight, and ability to withstand the stresses of constant rotation and torque transfer. Several materials are commonly employed, each with its own advantages and disadvantages.
Steel Driveshafts
Steel has traditionally been the go-to material for driveshafts due to its robustness and relatively low cost. Steel driveshafts are typically made from high-strength steel alloys designed to resist torsional stress and bending.
Advantages of Steel Driveshafts:
- High Strength: Steel offers excellent tensile and yield strength, making it suitable for high-torque applications.
- Durability: Steel driveshafts are known for their longevity and ability to withstand harsh conditions.
- Cost-Effective: Compared to other materials, steel is generally more affordable.
- Easy to Repair: Welding and other repair techniques are readily applicable to steel.
Disadvantages of Steel Driveshafts:
- Weight: Steel is significantly heavier than aluminum or carbon fiber, which can impact vehicle performance and fuel economy.
- Inertia: The higher mass contributes to greater rotational inertia, potentially affecting acceleration and deceleration.
Aluminum Driveshafts
Aluminum is a lighter alternative to steel, offering a better strength-to-weight ratio. Aluminum driveshafts are usually made from high-grade aluminum alloys.
Advantages of Aluminum Driveshafts:
- Lighter Weight: Significantly reduces weight compared to steel, improving acceleration, braking, and fuel efficiency.
- Reduced Inertia: Lower rotational inertia allows for quicker engine response and improved handling.
- Corrosion Resistance: Aluminum naturally resists corrosion, extending the driveshaft's lifespan.
Disadvantages of Aluminum Driveshafts:
- Lower Strength: While strong for its weight, aluminum is generally less strong than steel. This can limit its application in very high-torque environments.
- Higher Cost: Aluminum driveshafts are typically more expensive than steel driveshafts.
- More Susceptible to Damage: Aluminum can be more easily damaged by impacts or debris.
Carbon Fiber Driveshafts
Carbon fiber represents the cutting edge in driveshaft technology. Carbon fiber composites offer an unparalleled strength-to-weight ratio, making them ideal for performance vehicles and racing applications.
Advantages of Carbon Fiber Driveshafts:
- Extremely Lightweight: Carbon fiber offers the greatest weight reduction, maximizing performance benefits.
- Superior Strength: Provides exceptional strength and stiffness, capable of handling very high torque loads.
- Dampening Properties: Carbon fiber can dampen vibrations, leading to a smoother and quieter ride.
- Corrosion Resistance: Carbon fiber is highly resistant to corrosion.
Disadvantages of Carbon Fiber Driveshafts:
- High Cost: Carbon fiber driveshafts are the most expensive option due to the complex manufacturing process.
- Vulnerability to Impact Damage: While strong in tension and bending, carbon fiber can be susceptible to damage from sharp impacts.
- Repair Complexity: Repairing carbon fiber driveshafts requires specialized skills and equipment.
Balance Considerations for One-Piece Driveshafts
Regardless of the material, proper balancing is absolutely critical for a one-piece driveshaft. An imbalanced driveshaft can lead to vibrations, noise, and premature wear on driveline components, including the transmission, differential, and bearings. Balancing ensures that the mass of the driveshaft is evenly distributed around its axis of rotation.
Importance of Driveshaft Balancing
An unbalanced driveshaft creates a centrifugal force that increases with speed. This force causes the driveshaft to vibrate, which can transmit through the vehicle, creating discomfort for the driver and passengers. More importantly, these vibrations put undue stress on the driveshaft's U-joints, slip yoke, and other components, leading to premature failure. Proper balancing extends the lifespan of the driveshaft and other driveline components.
The Balancing Process
Driveshaft balancing is typically performed on a specialized machine that rotates the driveshaft at high speeds. Sensors detect any imbalance, and weights are then added to or removed from the driveshaft to correct the imbalance.
Here's a simplified breakdown of the process:
- Mounting: The driveshaft is carefully mounted on the balancing machine.
- Spinning: The machine spins the driveshaft at various speeds, simulating real-world operating conditions.
- Measurement: Sensors detect the magnitude and location of any imbalance.
- Correction: Weights are precisely added to or removed from specific points on the driveshaft to counteract the imbalance. This may involve welding small weights to the driveshaft or grinding away material in specific areas.
- Verification: The driveshaft is re-spun to verify that the imbalance has been corrected to within acceptable tolerances.
Factors Affecting Driveshaft Balance
Several factors can influence the balance of a driveshaft:
- Manufacturing Tolerances: Imperfections in the manufacturing process can lead to slight imbalances.
- Welding: Welding U-joints or other components can introduce imbalances if not done carefully.
- Damage: Dents, bends, or other damage can throw the driveshaft out of balance.
- Wear and Tear: Over time, wear on U-joints or other components can affect the balance.
- Incorrect Installation: Improper installation, such as misalignment, can also contribute to vibrations.
When to Balance a Driveshaft
It's generally recommended to balance a driveshaft in the following situations:
- New Driveshaft Installation: Even new driveshafts should be balanced to ensure optimal performance.
- After Repairs: If the driveshaft has been repaired, such as welding U-joints or straightening a bend, it should be re-balanced.
- Experiencing Vibrations: If you're experiencing vibrations, especially at higher speeds, balancing the driveshaft is a good place to start troubleshooting.
- Performance Upgrades: When upgrading to a different type of driveshaft, such as switching from steel to aluminum or carbon fiber, balancing is essential.
Finding a Reputable Balancing Service
When choosing a driveshaft balancing service, look for a shop with:
- Experienced Technicians: Technicians should have experience balancing a variety of driveshafts.
- Modern Equipment: The shop should use a well-maintained balancing machine.
- Good Reputation: Check online reviews and ask for recommendations.
- Clear Pricing: Get a clear quote before authorizing any work.
Conclusion
Choosing the right material and ensuring proper balance are both crucial for a one-piece driveshaft to perform reliably and efficiently. Understanding the pros and cons of steel, aluminum, and carbon fiber allows you to select the material that best suits your needs and budget. Regular inspection and balancing, especially after repairs or modifications, will help prevent vibrations and extend the life of your driveline. By paying attention to these considerations, you can ensure a smooth and enjoyable driving experience.