Procedure For Relocating And Tucking The Engine Bay Wiring Harness
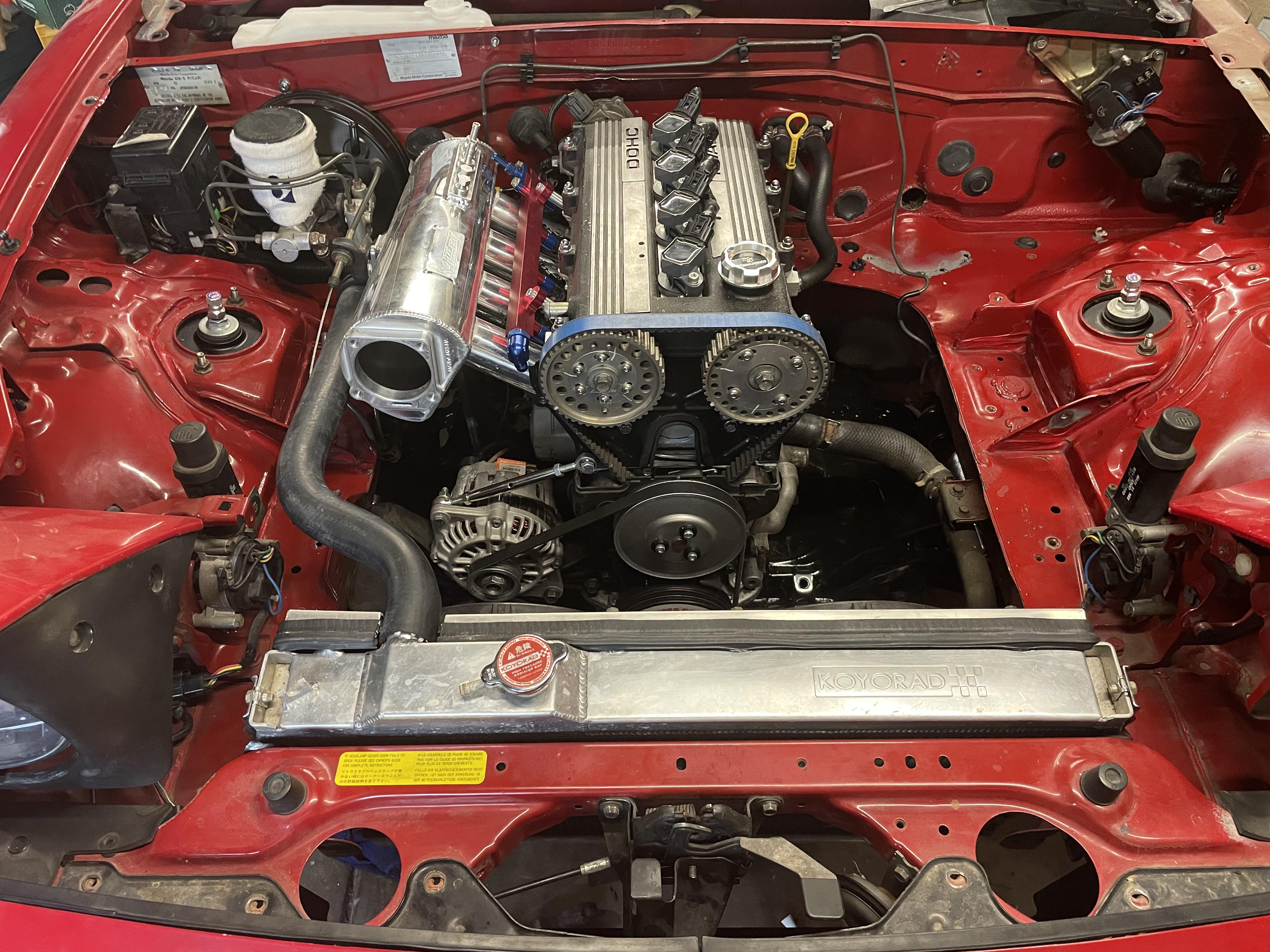
Alright folks, so you're looking to clean up that engine bay, huh? A wiring harness relocation, often referred to as "tucking," is a fantastic way to achieve a sleek, minimalist look. It involves moving the factory wiring harness from its stock location to a less visible area, usually inside the fender wells, under the dashboard, or even routing it through the frame rails. This isn't a quick weekend project; it demands patience, meticulous planning, and a solid understanding of your vehicle's electrical system. However, with the right approach, it's a very rewarding modification.
Before we dive in, let's be clear: this is an advanced DIY project. Messing with your car's wiring can lead to serious electrical problems, damage to components, and even safety hazards. If you're not comfortable with diagnosing electrical issues, soldering, or reading wiring diagrams, I strongly recommend consulting a professional.
Preparation is Key
The success of a wiring harness tuck hinges on careful planning and preparation. Don't just start ripping wires out; that's a recipe for disaster.
1. Research and Planning
This is the most crucial step. You need to understand your car's electrical system inside and out. Acquire a detailed wiring diagram for your specific make, model, and year. These diagrams are your roadmap; they show you the function of each wire, its color code, and where it connects. Look for online forums dedicated to your car model; chances are someone else has already tucked the harness and can offer valuable insights and lessons learned.
Consider where you want to relocate the harness. Popular choices include inside the fender wells, under the dashboard, or even through the frame rails. Each location has its pros and cons. Fender wells offer relatively easy access, but expose the harness to moisture and debris. The dashboard keeps it protected but requires significant interior disassembly. Frame rails offer maximum concealment but can be difficult to access and require drilling and welding.
2. Gather Your Tools and Supplies
You'll need a comprehensive toolkit. Here’s a rundown of essential items:
- Wiring Diagram: Absolutely essential.
- Multimeter: For testing voltage, continuity, and resistance. A must-have for troubleshooting.
- Wire Strippers/Crimpers: Invest in a quality set that can handle various wire gauges.
- Soldering Iron and Solder: Soldering provides the most reliable and durable connections.
- Heat Shrink Tubing: To insulate and protect your solder joints. Different sizes are needed.
- Electrical Tape: Use high-quality electrical tape designed for automotive applications.
- Wire Loom and Conduit: To protect and organize the relocated harness.
- Terminal Connectors: Various types and sizes to match your car's connectors.
- Zip Ties: For securing the harness in its new location.
- Label Maker or Wire Labels: Absolutely critical for identifying wires after you've extended them.
- Pen and Paper: For taking notes and documenting your progress.
- Digital Camera: To take pictures of the harness before you start, for reference.
3. Disconnect the Battery
Before you touch anything electrical, disconnect the negative terminal of your battery. This is a non-negotiable safety precaution to prevent accidental shorts and electrical shocks.
The Relocation Process
Now comes the heart of the project. Remember to work methodically and document everything. Take your time; rushing will only lead to mistakes.
1. Accessing and Evaluating the Harness
Locate the main engine bay wiring harness. This is usually a large bundle of wires running along the firewall or inner fenders. Carefully remove any clips, brackets, or retainers holding the harness in place. Evaluate the length of each wire run. You'll likely need to extend many of the wires to reach their new destinations. Note which connectors need to be depinned and which can be left intact.
2. Depinning Connectors (If Necessary)
Some connectors may need to be depinned (removing the individual wires from the connector housing) to route the harness through tight spaces. A depinning tool is designed to release the retaining tabs inside the connector. Never force the wires out; you could damage the connector or the terminals. If you don't have the specific depinning tool for your connector type, you can often use a small pick or a thin screwdriver to carefully release the tabs.
Important: Before depinning anything, take detailed pictures and make notes of the wire order in each connector. You must know which wire goes where!
3. Extending Wires
This is where the majority of the work lies. Each wire that needs to be extended should be done individually. Here's the proper procedure:
- Cut the Wire: Cut the wire cleanly at the point where it needs to be extended. Leave enough slack on both ends for soldering.
- Strip the Insulation: Strip a small amount of insulation (about ¼ inch) from both ends of the cut wire and from both ends of the new wire extension.
- Solder the Connection: Twist the bare wires together to form a mechanical connection. Apply a small amount of flux to the joint and then carefully solder it, ensuring a strong, clean connection. Allow the solder to cool completely.
- Insulate the Joint: Slide a piece of heat shrink tubing over the soldered joint. Position the tubing so it covers the entire joint and a small portion of the insulation on either side. Use a heat gun to shrink the tubing, creating a waterproof and durable seal. You can also use high-quality electrical tape, but heat shrink tubing is far superior.
- Label the Wire: Immediately label the wire with its function and destination. Use a label maker or write clearly on wire labels. This is critical for preventing confusion later on.
Pro Tip: Use the same gauge wire as the original wire for your extensions. Using a smaller gauge wire can restrict current flow and cause problems. Also, stagger your solder joints along the harness. This prevents a large bulge in one spot, making it easier to route the harness.
4. Routing and Securing the Harness
Once all the wires have been extended, it's time to route the harness to its new location. Use wire loom or conduit to protect the wires from abrasion and the elements. Secure the harness with zip ties or cable clamps, making sure it's not rubbing against any sharp edges or moving parts. Leave some slack in the harness to allow for engine movement and chassis flex.
Important: Avoid routing the harness near heat sources, such as the exhaust manifold or turbocharger. High temperatures can damage the wiring and cause it to fail.
5. Reconnecting Connectors
If you depinned any connectors, carefully reinsert the wires in the correct order, referring to your notes and pictures. Ensure that each wire is securely locked in place.
6. Testing and Verification
Before you declare victory, thoroughly test the entire electrical system. Reconnect the battery and check all the circuits that are affected by the harness relocation. Use your multimeter to verify that all the wires are receiving the correct voltage and that there are no shorts or open circuits. Start the engine and check all the sensors, actuators, and other components that are connected to the harness. If you find any problems, use your wiring diagram to troubleshoot the issue. Don’t just guess; diagnose the problem systematically.
Final Touches
Once you're satisfied that everything is working correctly, take some time to clean up the engine bay. Secure any loose wires, replace any missing clips or retainers, and double-check all your connections. Step back and admire your work. You've just transformed the look of your engine bay with a professional-looking wiring harness tuck.
Troubleshooting Tips
Even with careful planning and execution, problems can sometimes arise. Here are some common issues and how to address them:
- Engine Won't Start: Check the main power and ground connections to the engine. Verify that the ECU is receiving power.
- Sensor Malfunctions: Check the wiring to the affected sensor. Use a multimeter to verify that the sensor is receiving power and that the signal is being transmitted to the ECU.
- Short Circuits: Use a multimeter to check for shorts between wires and ground. Carefully inspect the harness for any damaged insulation or exposed wires.
- Intermittent Problems: These can be the most difficult to diagnose. Check all your connections and look for any loose or corroded terminals. Flex the harness while the engine is running to see if you can induce the problem.
Remember, patience and a systematic approach are key to troubleshooting electrical problems. Don't be afraid to ask for help from other enthusiasts or consult a professional if you get stuck.
This project is not for the faint of heart. It requires dedication, meticulousness, and a solid understanding of automotive electrical systems. But with careful planning, proper execution, and a little bit of elbow grease, you can achieve a stunning engine bay transformation with a professionally tucked wiring harness. Good luck!