Rear Big Brake Kit Caliper Mounting And Rotor Specifications
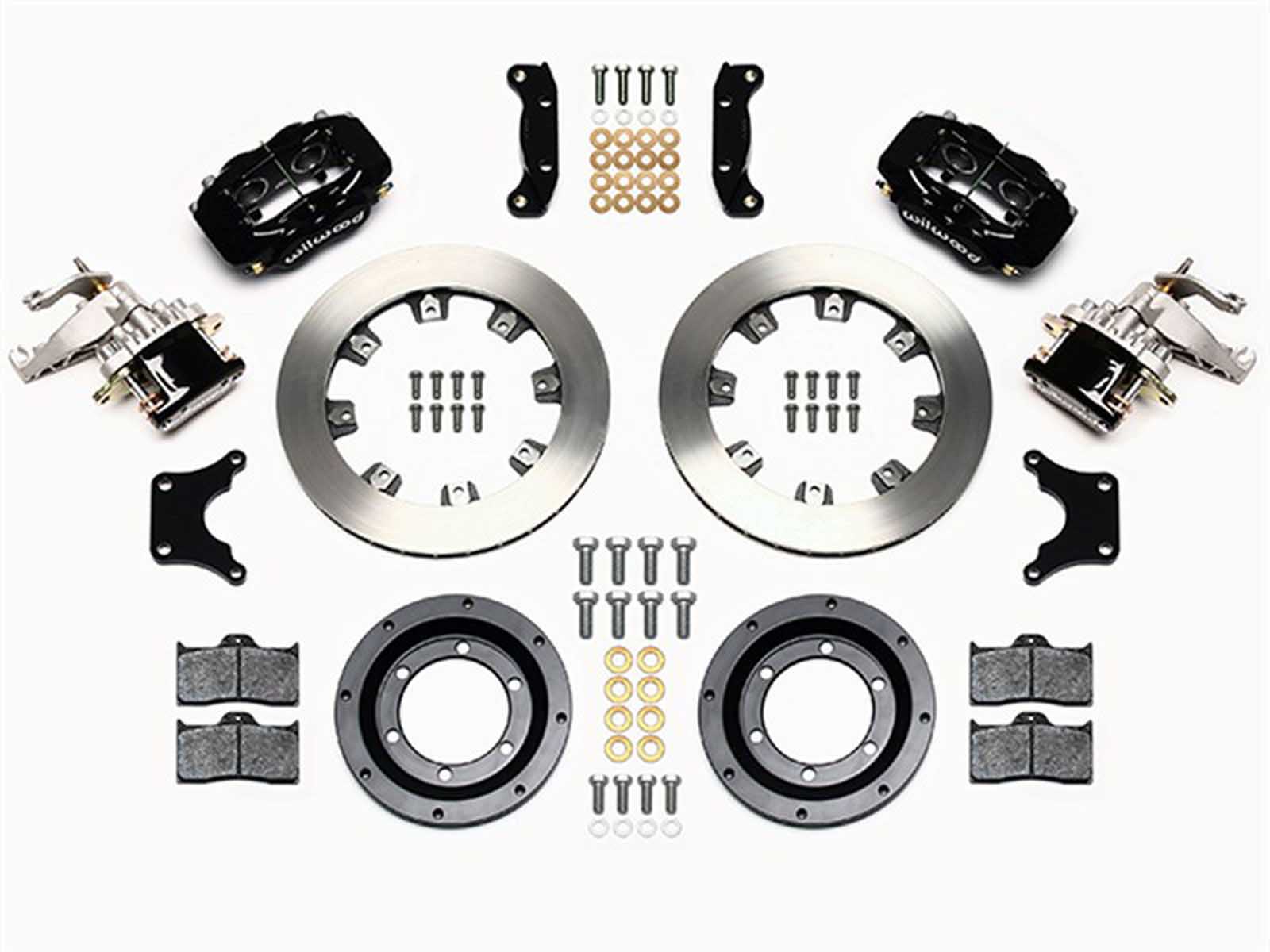
Upgrading to a rear big brake kit (BBK) is a popular modification for enthusiasts seeking improved stopping power, reduced brake fade, and enhanced aesthetics. While the front brakes typically handle the majority of the braking force, upgrading the rear brakes provides a more balanced and effective braking system. This guide dives deep into the technical aspects of rear BBK caliper mounting and rotor specifications, providing a comprehensive understanding for those looking to undertake this upgrade or simply expand their automotive knowledge.
Understanding the Fundamentals
Before diving into the specifics, it's crucial to understand the basic principles behind brake system operation. When the brake pedal is pressed, hydraulic pressure is generated by the master cylinder. This pressure is then transmitted to the calipers, which in turn clamp the brake pads against the rotors. The friction between the pads and rotors slows the vehicle down, converting kinetic energy into heat. A BBK increases the surface area and thermal capacity of the braking system, allowing it to absorb and dissipate more heat, resulting in improved braking performance.
Caliper Mounting: Precision and Compatibility
Caliper Brackets: The Foundation of the Upgrade
The core of any rear BBK installation lies in the caliper mounting brackets. These brackets are specifically designed to adapt the new, larger calipers to the existing mounting points on the vehicle's rear knuckle or spindle. The bracket design is critical for several reasons:
- Ensuring Correct Caliper Position: The bracket must position the caliper so that the brake pads correctly align with the rotor's friction surface. Improper alignment can lead to uneven pad wear, reduced braking efficiency, and even damage to the rotor.
- Maintaining Proper Offset: Offset refers to the distance between the mounting surface of the rotor and the centerline of the caliper. The bracket must ensure this offset is correct to prevent binding or interference.
- Structural Integrity: Braking forces are significant. The bracket must be robust enough to withstand these forces without bending, flexing, or fracturing. High-quality brackets are typically machined from billet aluminum or steel for maximum strength and durability.
The design of the caliper bracket depends heavily on the vehicle's suspension geometry and the chosen caliper. Each bracket is CAD designed and FEA (Finite Element Analysis) tested to ensure structural integrity and proper fitment. High-strength bolts are essential for securing the bracket to the knuckle and the caliper to the bracket. Torque specifications provided by the BBK manufacturer must be strictly adhered to.
Mounting Types and Considerations
There are generally two types of caliper mounting configurations:
- Radial Mount: The caliper is mounted to the bracket using bolts that are perpendicular to the rotor surface. This is a common and generally simpler mounting method.
- Lug Mount: The caliper bolts through the bracket into the original mounting points on the spindle or knuckle. These brackets are commonly steel construction and are designed to mount to the existing OEM caliper mounting points.
When installing the caliper bracket, it's crucial to:
- Clean the Mounting Surfaces: Ensure that the mounting surfaces on the knuckle and bracket are clean and free of any debris or corrosion. This will ensure proper contact and prevent loosening over time.
- Use Thread Locker: Applying a thread locker, such as Loctite, to the bolt threads will help prevent them from loosening due to vibration.
- Torque to Specification: Use a torque wrench to tighten the bolts to the manufacturer's specified torque value. Over-tightening can damage the threads or the bracket, while under-tightening can lead to loosening.
Incorrect installation of the caliper bracket can have severe consequences, including brake failure. If you are not comfortable performing this task, it's best to have it done by a qualified mechanic.
Rotor Specifications: Size, Material, and Design
Rotor Diameter and Thickness: The Key to Performance
The size of the rotor is a critical factor in determining the braking performance of a BBK. Larger rotors have several advantages:
- Increased Surface Area: A larger rotor provides a larger friction surface for the brake pads to engage with. This translates to greater stopping power.
- Improved Heat Dissipation: Larger rotors have a greater thermal mass, allowing them to absorb more heat before reaching their maximum operating temperature. This helps prevent brake fade.
- Increased Leverage: A larger rotor effectively increases the leverage of the caliper, requiring less force to achieve the same braking torque.
Rotor thickness is also important. A thicker rotor can absorb more heat and is less prone to warping under extreme conditions. However, excessively thick rotors can add weight and increase the overall size of the brake system, potentially creating clearance issues.
When selecting a rear BBK, it's important to consider the rotor diameter and thickness in relation to the vehicle's weight, power output, and intended use. A larger rotor is generally better for high-performance applications, while a smaller rotor may be sufficient for street use.
Rotor Material: Balancing Performance and Cost
Most aftermarket rotors are made from cast iron, although different grades of cast iron are used. The specific alloy composition affects the rotor's strength, heat resistance, and wear characteristics. High-carbon cast iron rotors are a popular choice for BBKs due to their improved thermal capacity and reduced tendency to warp.
More exotic materials, such as carbon ceramic, are sometimes used in high-end BBKs. Carbon ceramic rotors offer exceptional performance, including very high heat resistance and low weight. However, they are significantly more expensive than cast iron rotors and are typically reserved for specialized applications.
Rotor Design: Optimizing Cooling and Performance
The design of the rotor plays a significant role in its cooling efficiency and overall performance. Common rotor designs include:
- Solid Rotors: These are the simplest type of rotor and are typically used on vehicles with lower performance requirements. They offer adequate cooling for normal driving conditions but can overheat under heavy braking.
- Vented Rotors: Vented rotors have internal vanes that allow air to flow through the rotor, improving heat dissipation. There are different types of vent designs, including straight vanes, curved vanes, and pillar vanes. Curved vanes are generally more efficient at pumping air through the rotor.
- Drilled Rotors: Drilled rotors have holes drilled through the friction surface. These holes help to vent gases and debris that can accumulate between the pad and rotor, improving braking performance. However, drilled rotors can be more prone to cracking under extreme heat.
- Slotted Rotors: Slotted rotors have grooves cut into the friction surface. These slots help to remove debris and improve pad bite, similar to drilled rotors. Slotted rotors are generally less prone to cracking than drilled rotors.
Many BBKs use a combination of vented, drilled, and slotted rotors to optimize cooling and performance. The choice of rotor design depends on the specific application and the desired performance characteristics.
Matching Components: A System Approach
It's crucial to remember that a BBK is a system, and all components must be carefully matched to ensure optimal performance. The caliper, rotor, brake pads, and master cylinder must all work together in harmony. When selecting a BBK, it's best to choose a kit that has been specifically designed for your vehicle and intended use.
Furthermore, consider the brake bias. The brake bias describes how much braking force is being applied to the front versus the rear wheels. Modifying the front or rear brakes can impact the brake bias, potentially leading to instability or reduced braking performance. It’s important that the front and rear systems are compatible with each other to maintain proper brake bias and stability. Some vehicles may require proportioning valves to fine-tune the brake bias after installing a BBK.
In conclusion, upgrading to a rear big brake kit involves careful consideration of caliper mounting and rotor specifications. Understanding the technical aspects of these components is essential for ensuring a safe and effective installation. By paying attention to the details and selecting high-quality components, you can significantly improve your vehicle's braking performance and enjoy a more confident driving experience.