Repair And Replacement Of The Radiator Core Support On A Nissan 240sx
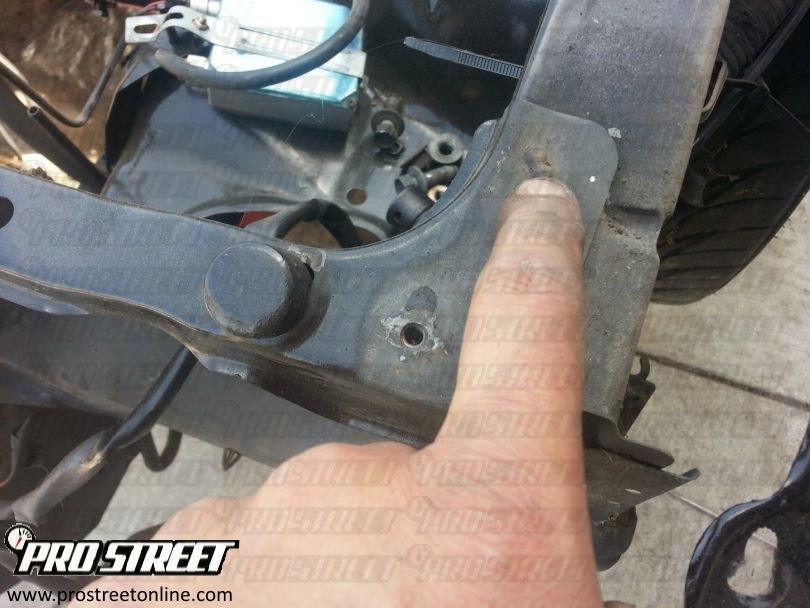
The Nissan 240SX, a darling of the drift and tuner communities, is no stranger to impacts. Whether from track incidents, minor fender benders, or the ravages of time, the radiator core support is a common casualty. This vital structural component, also known as the front panel or header panel, provides the mounting points for the radiator, headlights, hood latch, and other front-end components. Damage to the core support not only compromises the aesthetic appeal of the car, but, more importantly, affects its structural integrity and can lead to cooling system issues.
While a severely damaged core support often necessitates professional repair, a competent DIY enthusiast with the right tools and a methodical approach can tackle the replacement. This guide will provide an in-depth look at the process, covering everything from inspection and preparation to cutting, welding, and finishing. This isn't a simple bolt-on procedure; it demands precision and skill to ensure the structural integrity of the repaired area.
Assessing the Damage and Planning the Repair
Before diving into the repair, a thorough assessment is crucial. Begin by carefully inspecting the extent of the damage. Are there bends, cracks, or outright tears in the metal? Is the surrounding sheet metal also affected? The more extensive the damage, the more complex the repair will be. Pay close attention to the mounting points for the radiator, headlights, and hood latch. Damage to these areas can significantly impact the functionality of the car.
Important Safety Note: If the damage is severe and affects the car's frame rails or crumple zones, it's strongly recommended to consult with a professional body shop. Attempting to repair compromised frame components without the proper equipment and expertise can be extremely dangerous.
Once you've assessed the damage, you need to decide on the repair strategy. The most common approach is to replace the entire core support with a new or used unit. This ensures a proper and structurally sound repair. Alternatively, if the damage is localized, you might consider sectioning – cutting out the damaged area and welding in a replacement piece. This requires even greater precision and skill.
Sourcing a replacement core support is the next step. New aftermarket core supports are readily available for the 240SX. Used core supports can be found from salvage yards or online marketplaces. When purchasing a used unit, carefully inspect it for rust, dents, and previous repairs. Ideally, you want a core support that is in as good condition as possible to minimize additional work.
Tools and Materials Required
Successfully replacing a radiator core support requires a well-equipped workspace and the right tools. Here’s a comprehensive list:
- Safety Gear: Safety glasses, gloves, welding helmet, welding gloves, respirator (for grinding and painting).
- Cutting Tools: Angle grinder with cutting and grinding discs, reciprocating saw (Sawzall), spot weld drill bit.
- Welding Equipment: MIG welder (Metal Inert Gas), welding wire, welding gas (usually a mix of argon and CO2).
- Measuring and Marking Tools: Tape measure, marking pen, straight edge, level.
- Body Work Tools: Hammer and dolly set, pry bar, body filler, sanding block, various grades of sandpaper.
- Drilling Tools: Drill, drill bits.
- Fasteners: New bolts, nuts, and washers as needed.
- Rust Prevention: Rust converter, primer, paint.
- Specialized Tools: Spot weld cutter.
Removing the Old Core Support
Before you begin cutting, disconnect the battery and drain the radiator. Remove all components attached to the core support, including the radiator, headlights, hood latch, and any associated wiring harnesses. Label all wires and connectors to avoid confusion during reassembly. Take plenty of pictures for reference.
The old core support is typically attached to the car with a combination of spot welds and seam welds. The first step is to locate and remove the spot welds. A spot weld drill bit is specifically designed for this purpose. It cuts through the outer layer of metal without damaging the underlying panel. Carefully drill out each spot weld, taking care not to drill too deep.
Next, use an angle grinder or reciprocating saw to cut through the seam welds. These welds are typically located along the edges of the core support, where it is joined to the inner fenders and frame rails. Be careful not to cut into the surrounding sheet metal. A cutting disc on an angle grinder is effective for this task, but a reciprocating saw offers better control in tight spaces.
Once all the welds are removed, the old core support should be free. You may need to use a pry bar to gently separate it from the car. Be careful not to damage the surrounding sheet metal.
Preparing the New Core Support and the Car
Before installing the new core support, thoroughly clean and inspect the area where it will be attached. Remove any rust, dirt, or debris. Use a wire brush or abrasive pad to clean the metal surface. Apply a rust converter to any areas of surface rust to prevent further corrosion.
Test fit the new core support to ensure proper alignment. You may need to make minor adjustments to the shape or position of the core support to achieve a perfect fit. Use clamps to hold the core support in place during the test fit.
Once you are satisfied with the fit, prepare the surfaces for welding. Clean the metal to bare steel. Use an angle grinder or sanding disc to remove any paint, primer, or rust from the welding areas. This will ensure a strong and clean weld. Coat all interior surfaces and seams with a weld-through primer. This helps to prevent rust from forming between the panels after welding.
Welding the New Core Support
Welding is the most critical step in the core support replacement process. It requires a steady hand, proper welding technique, and a good understanding of metallurgy. If you are not experienced in welding, it is highly recommended to seek professional assistance. Poor welds can compromise the structural integrity of the repair and create a safety hazard.
MIG welding is the preferred method for welding sheet metal. It is relatively easy to learn and produces strong, clean welds. Start by tack welding the core support in place at several points around the perimeter. This will hold it in position while you complete the welding process.
When welding sheet metal, it is important to use a low heat setting to prevent warping. Weld in short bursts, allowing the metal to cool between welds. Overheating the metal can cause it to buckle and distort. Use a stitch welding technique, creating a series of short welds along the seam. This will help to distribute the heat evenly and prevent warping.
Pay close attention to the alignment of the core support while welding. Check frequently to ensure that it is still in the correct position. Use clamps to hold the core support in place if necessary.
After welding, grind down the welds to create a smooth and even surface. Use a grinding disc on an angle grinder to remove any excess weld material. Be careful not to grind too deep, as this can weaken the weld. Inspect the welds for any cracks or pinholes. If you find any defects, re-weld the area.
Finishing and Reassembly
Once the welding and grinding are complete, it’s time to finish the repair. Apply body filler to any imperfections in the surface. Sand the filler smooth, using progressively finer grades of sandpaper. Prime the entire area with a rust-resistant primer. This will protect the metal from corrosion.
Paint the core support to match the color of the car. Apply several coats of paint, allowing each coat to dry completely before applying the next. After the paint is dry, apply a clear coat to protect the paint and give it a glossy finish.
Reinstall all the components that you removed earlier, including the radiator, headlights, hood latch, and wiring harnesses. Make sure that everything is properly connected and secured. Double-check all your work before starting the car.
Finally, adjust the headlights and hood latch to ensure proper alignment. Check the cooling system for leaks. Take the car for a test drive to verify that everything is working correctly.
Replacing a radiator core support is a challenging but rewarding project. By following these steps and taking your time, you can restore the structural integrity and appearance of your Nissan 240SX. Remember to prioritize safety and seek professional assistance if you are not comfortable with any aspect of the repair.