Replacement Dashboard Material Composition And Fitment Analysis
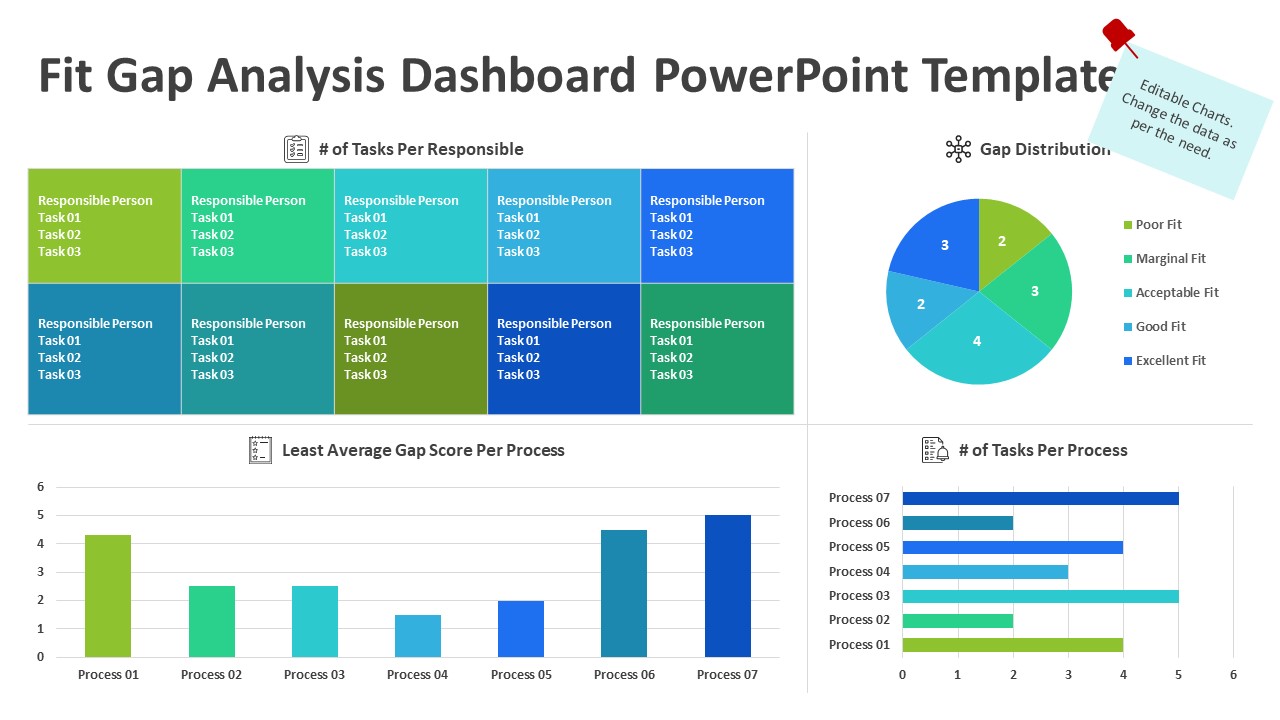
The dashboard, or instrument panel, is more than just a place to house gauges and vents; it's a critical component of a vehicle's interior, contributing significantly to structural integrity, occupant safety, and overall aesthetic appeal. Understanding the composition and fitment of replacement dashboard materials is crucial for anyone undertaking a restoration project, collision repair, or simply seeking to upgrade their vehicle's interior. This guide delves into the technical aspects of dashboard materials and fitment, providing an in-depth analysis relevant to both curious readers and amateur engineers.
Dashboard Material Composition: A Layered Approach
Modern dashboards are rarely constructed from a single material. Instead, they employ a layered approach, each layer contributing specific properties and functionalities. Let's break down the most common layers:
1. Substrate Layer: The Backbone
The substrate layer forms the structural foundation of the dashboard. Common materials used for the substrate include:
- Polypropylene (PP): PP is a widely used thermoplastic polymer known for its high strength-to-weight ratio, excellent chemical resistance, and low cost. It's often reinforced with glass fibers or mineral fillers to further enhance its stiffness and impact resistance. PP dashboards are typically manufactured using injection molding, allowing for complex shapes and intricate details.
- Acrylonitrile Butadiene Styrene (ABS): ABS is another popular thermoplastic polymer prized for its durability, rigidity, and good impact resistance. It's more expensive than PP but offers better dimensional stability and surface finish. ABS is often used in dashboards that require a smoother, more refined appearance.
- Fiberglass Reinforced Plastic (FRP): FRP substrates offer superior strength and stiffness compared to PP and ABS. They are typically used in high-performance vehicles or dashboards that require exceptional structural integrity. FRP dashboards are more complex to manufacture and typically involve a resin transfer molding (RTM) or hand layup process.
The choice of substrate material depends on factors such as cost, weight, performance requirements, and manufacturing complexity.
2. Foam Layer: Impact Absorption and Comfort
The foam layer plays a crucial role in absorbing impact energy during a collision, protecting occupants from injury. It also provides a soft, comfortable surface for occupants to interact with. Common foam materials include:
- Polyurethane (PU) Foam: PU foam is the most widely used foam material in dashboards. It offers a good balance of impact absorption, comfort, and cost. PU foam can be molded to various shapes and densities, allowing for customization of the dashboard's feel and performance.
- Thermoplastic Olefin (TPO) Foam: TPO foam offers superior durability and UV resistance compared to PU foam. It's often used in dashboards that are exposed to direct sunlight or extreme temperatures. TPO foam is also recyclable, making it a more environmentally friendly option.
The density and thickness of the foam layer are carefully engineered to meet specific safety standards and performance requirements.
3. Skin Layer: Aesthetics and Tactile Feel
The skin layer is the outermost layer of the dashboard, providing the final aesthetic appeal and tactile feel. Common skin materials include:
- Polyvinyl Chloride (PVC): PVC is a durable and versatile thermoplastic polymer that can be textured and colored to mimic various materials, such as leather or fabric. It's a cost-effective option for dashboards that require a high-quality appearance. However, PVC can release harmful chemicals when exposed to high temperatures.
- Thermoplastic Polyolefin (TPO): TPO is a more environmentally friendly alternative to PVC. It offers good durability, UV resistance, and a wide range of textures and colors. TPO is also recyclable, making it a sustainable choice.
- Leather: Leather provides a luxurious and premium feel to the dashboard. It's a durable and long-lasting material that ages gracefully. However, leather is expensive and requires special care and maintenance.
- Alcantara: Alcantara is a synthetic suede-like material that offers a soft, tactile feel and a high-end appearance. It's resistant to fading, staining, and wear. Alcantara is often used in high-performance vehicles and luxury cars.
The skin layer is typically bonded to the foam layer using adhesives or heat welding.
4. Decorative Trim and Inserts: Visual Accents
Decorative trim and inserts, such as chrome accents, wood veneer, or carbon fiber panels, are often added to the dashboard to enhance its visual appeal. These elements are typically attached to the skin layer using clips, screws, or adhesives.
Fitment Analysis: Achieving a Seamless Integration
Proper fitment of a replacement dashboard is critical for ensuring structural integrity, safety, and aesthetic appeal. A poorly fitted dashboard can lead to squeaks, rattles, air leaks, and even compromise the vehicle's safety systems. Here's a detailed look at the key aspects of fitment analysis:
1. Dimensional Accuracy: Matching the Original
The replacement dashboard must precisely match the dimensions of the original dashboard. This includes overall length, width, height, and the location of mounting points, cutouts for gauges and vents, and provisions for wiring harnesses. Deviations from the original dimensions can lead to fitment issues and require modifications to the dashboard or the vehicle's structure.
Key Measurement Points: Pay close attention to the distance between mounting points, the diameter of gauge cutouts, and the alignment of vent openings.
2. Mounting Point Alignment: Securing the Dashboard
The mounting points on the replacement dashboard must align perfectly with the corresponding mounting points on the vehicle's structure. This ensures that the dashboard is securely attached and can withstand the forces generated during a collision. Misaligned mounting points can lead to stress concentrations and premature failure of the dashboard or the vehicle's structure.
Common Mounting Methods: Screws, bolts, clips, and rivets are commonly used to secure the dashboard to the vehicle's structure. Ensure that the replacement dashboard includes all necessary mounting hardware and that the hardware is compatible with the vehicle's structure.
3. Clearance: Avoiding Interference
The replacement dashboard must provide adequate clearance for all surrounding components, such as the steering column, pedals, wiring harnesses, and air conditioning ducts. Interference with these components can lead to functional problems and safety hazards. Check for sufficient clearance between the dashboard and the steering column throughout its range of motion. Ensure that wiring harnesses are routed correctly and are not pinched or stressed.
Critical Clearance Areas: Pay attention to the area around the steering column, the pedal box, and the air conditioning ducts.
4. Sealing: Preventing Air Leaks
The replacement dashboard must properly seal against the windshield, side pillars, and other interior panels to prevent air leaks. Air leaks can lead to drafts, noise, and reduced heating and cooling efficiency. Use appropriate weather stripping and sealant to ensure a tight seal between the dashboard and the surrounding components. A proper seal also helps prevent water intrusion, which can damage electrical components and lead to corrosion.
Sealant Types: Silicone sealant, butyl tape, and foam weather stripping are commonly used to seal dashboards. Choose a sealant that is compatible with the dashboard material and the surrounding components.
5. Aesthetic Integration: Maintaining a Consistent Look
The replacement dashboard should seamlessly integrate with the existing interior trim and components to maintain a consistent aesthetic appearance. This includes matching the color, texture, and grain of the dashboard to the surrounding panels. Pay attention to the gaps and seams between the dashboard and the surrounding components. Uneven gaps or misaligned seams can detract from the overall appearance of the interior.
Color Matching: Obtain a color sample of the original dashboard and compare it to the replacement dashboard. Use a color matching system to ensure an accurate match.
Tools and Techniques for Fitment Analysis
Proper fitment analysis requires a combination of tools and techniques. Here are some essential tools:
- Tape Measure: Used to measure the overall dimensions of the dashboard and the location of mounting points.
- Calipers: Used to measure the diameter of gauge cutouts and the thickness of the dashboard material.
- Level: Used to ensure that the dashboard is level and aligned properly.
- Straightedge: Used to check for straightness and flatness of the dashboard surface.
- Feeler Gauges: Used to measure the gaps and clearances between the dashboard and surrounding components.
- Torque Wrench: Used to tighten fasteners to the correct torque specifications.
Fitment Techniques: Dry fit the dashboard before permanently installing it. Check for interference with surrounding components. Adjust the mounting points as needed to achieve a proper fit. Use shims or spacers to correct minor misalignments. Take your time and be patient. Proper fitment is essential for ensuring the long-term performance and safety of the dashboard.
Conclusion
Understanding the material composition and fitment requirements of replacement dashboards is essential for achieving a successful restoration, repair, or upgrade project. By carefully analyzing the materials and dimensions of the dashboard, and by employing proper fitment techniques, you can ensure that the replacement dashboard provides the same level of performance, safety, and aesthetic appeal as the original.