Suspension Component Material Analysis And Durability Testing
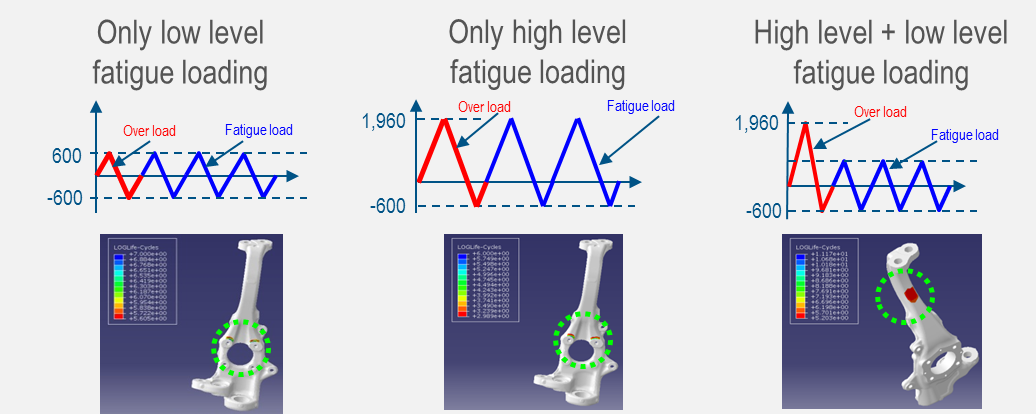
Suspension systems, the unsung heroes of vehicle dynamics, are complex assemblies of interconnected components working in concert to provide ride comfort, handling precision, and overall vehicle stability. But how do engineers ensure these vital components can withstand the immense stresses and strains they're subjected to, day in and day out? The answer lies in a rigorous process of material analysis and durability testing, a blend of scientific inquiry and practical experimentation that separates reliable suspension designs from catastrophic failures. This article delves into the fascinating world of suspension component material analysis and durability testing, offering a glimpse into the techniques and technologies used to build suspensions that can handle the rigors of the road – and beyond.
Material Selection: The Foundation of Durability
The journey to a durable suspension system begins long before any physical testing takes place. It starts with careful material selection, a process guided by a deep understanding of the intended application and the environmental conditions the suspension will face. Consider the forces at play: compression, tension, shear, and torsion, all varying in magnitude and direction depending on driving conditions. The chosen materials must be able to resist these forces without yielding, fracturing, or undergoing excessive deformation.
Common Suspension Materials and Their Properties
Several materials are commonly used in suspension components, each offering a unique combination of properties:
- Steel: A workhorse material, steel alloys offer high strength, stiffness, and fatigue resistance. Different alloying elements, such as chromium, nickel, and molybdenum, can be added to tailor the steel's properties for specific applications. For example, spring steel, typically a high-carbon alloy, is used for coil springs and leaf springs due to its excellent elasticity and ability to return to its original shape after deformation.
- Aluminum: Lighter than steel, aluminum alloys are increasingly used in suspension components like control arms and knuckles to reduce unsprung weight, improving handling and fuel efficiency. However, aluminum typically has a lower yield strength and fatigue resistance than steel, so careful design and alloy selection are crucial.
- Composites: Carbon fiber reinforced polymers (CFRP) offer an exceptional strength-to-weight ratio, making them attractive for high-performance applications. However, composites are generally more expensive and can be susceptible to damage from impacts.
- Elastomers: Rubber and polyurethane are commonly used for bushings and mounts, providing damping and isolation from vibrations and noise. These materials must be chosen for their specific durometer (hardness) and resistance to degradation from exposure to oils, solvents, and temperature extremes.
Material Analysis Techniques
Before a material is chosen for a specific suspension component, it undergoes rigorous analysis to determine its key properties. Some common techniques include:
- Tensile Testing: Measures the material's resistance to being pulled apart. This test provides information about yield strength, ultimate tensile strength, and elongation.
- Hardness Testing: Determines the material's resistance to indentation. Common hardness tests include Rockwell, Vickers, and Brinell.
- Fatigue Testing: Evaluates the material's ability to withstand repeated cycles of stress. This is crucial for suspension components that experience continuous loading and unloading during vehicle operation.
- Microscopy: Allows for the examination of the material's microstructure, revealing potential flaws or weaknesses. Scanning electron microscopy (SEM) and transmission electron microscopy (TEM) are powerful tools for analyzing material composition and structure at the microscopic level.
- Chemical Analysis: Determines the elemental composition of the material, ensuring that it meets specifications and that no harmful impurities are present.
Durability Testing: Simulating the Real World
Once the materials are selected, the next step is to validate the design through durability testing. This involves subjecting the suspension components to simulated real-world conditions to identify potential weaknesses and ensure they can withstand the expected lifespan of the vehicle. Durability testing can range from simple component-level tests to complex full-vehicle simulations.
Types of Durability Tests
Several types of durability tests are commonly used for suspension components:
- Fatigue Testing: As mentioned earlier, fatigue testing is crucial for evaluating the component's ability to withstand repeated stress cycles. This can be done on individual components or on entire suspension assemblies. Different loading profiles can be used to simulate various driving conditions, such as smooth highway driving, rough off-road driving, or aggressive cornering.
- Impact Testing: Simulates the effects of impacts, such as hitting a pothole or curb. This test evaluates the component's ability to withstand sudden, high-energy loads without fracturing or deforming.
- Environmental Testing: Exposes the components to extreme temperatures, humidity, salt spray, and UV radiation to assess their resistance to corrosion, degradation, and other environmental factors.
- Component-Level Testing: Involves testing individual suspension components, such as control arms, springs, dampers, and bushings, under controlled conditions. This allows engineers to isolate specific weaknesses and optimize the design of each component.
- Full-Vehicle Testing: Subjects the entire vehicle to simulated real-world driving conditions on a test track or in a laboratory using specialized equipment, such as a four-poster shaker. This allows engineers to evaluate the overall performance and durability of the suspension system under realistic conditions.
Testing Equipment and Techniques
Durability testing relies on sophisticated equipment and techniques to accurately simulate real-world conditions and measure the performance of the suspension components. Some common tools include:
- Servo-Hydraulic Actuators: These powerful actuators are used to apply controlled forces and displacements to the suspension components, simulating the loads experienced during driving.
- Data Acquisition Systems: These systems collect data from various sensors, such as strain gauges, accelerometers, and displacement transducers, providing real-time measurements of stress, strain, acceleration, and displacement.
- Finite Element Analysis (FEA): A computer-aided engineering (CAE) tool that allows engineers to simulate the behavior of the suspension components under various loading conditions. FEA can be used to identify areas of high stress concentration and optimize the design for improved durability.
- Accelerated Testing: Techniques used to accelerate the fatigue process, such as increasing the frequency or amplitude of the applied loads. This allows engineers to obtain durability data in a shorter amount of time. However, it's important to ensure that the accelerated testing methods accurately reflect the real-world failure mechanisms.
Interpreting the Results and Improving the Design
The data collected during durability testing is carefully analyzed to identify potential weaknesses in the suspension design. This analysis may involve:
- Identifying failure modes: Determining the specific mechanisms by which the components fail, such as fatigue cracking, yielding, or fracture.
- Analyzing stress and strain distributions: Identifying areas of high stress concentration that are prone to failure.
- Comparing performance to target values: Assessing whether the suspension system meets the required performance criteria, such as ride comfort, handling precision, and durability.
Based on the analysis of the test results, engineers can make design modifications to improve the durability of the suspension system. This may involve changing the material, geometry, or manufacturing process of the components. The modified design is then subjected to further testing to validate the improvements. This iterative process of testing, analysis, and design refinement continues until the suspension system meets all the required performance and durability criteria. This comprehensive approach to material analysis and durability testing ensures that suspension systems are not only capable of providing a comfortable and controlled ride, but also of withstanding the demanding conditions of real-world driving for the entire lifespan of the vehicle.
In conclusion, the seemingly simple act of driving over a bump relies on a monumental effort of engineering and testing. From the careful selection of high-strength steels to the intricate simulations performed in virtual environments, every component of a vehicle's suspension is designed and tested to ensure it can withstand the rigors of the road. This rigorous process, often unseen, is what separates a comfortable and reliable driving experience from a jarring and potentially dangerous one.
Understanding the science behind suspension systems allows us to appreciate the complexity and ingenuity involved in creating vehicles that can handle the diverse challenges of the modern world.