Technical Overview Of The Ka24e Sohc Engine In The 1990 Nissan 240sx
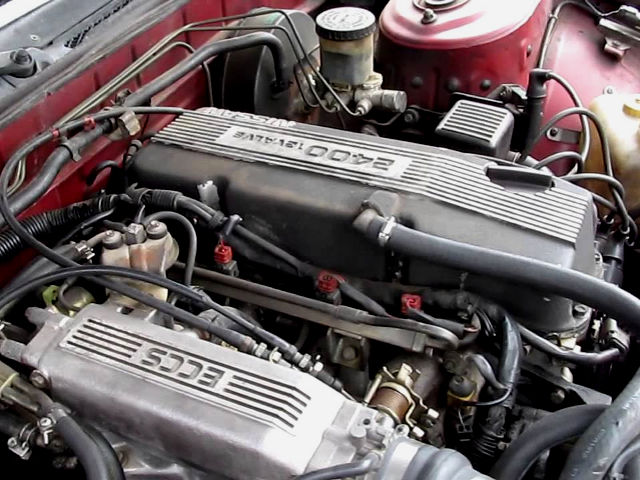
Alright, let's dive deep into the heart of many a 1990 Nissan 240SX: the KA24E engine. This single overhead cam (SOHC) workhorse is known for its reliability, simplicity, and surprising potential, making it a popular choice for both daily drivers and weekend project cars. This breakdown aims to provide a technical overview suitable for the experienced DIYer looking to understand or modify their KA24E.
Engine Block and Rotating Assembly
The KA24E boasts a cast-iron engine block, which contributes significantly to its durability. Iron blocks, while heavier than aluminum alternatives, are incredibly robust and better at dampening vibrations. This inherent strength is one reason why KA24Es can often withstand quite a bit of abuse.
Inside the block, you'll find a forged steel crankshaft. Forged cranks are stronger than cast cranks, capable of handling higher stresses associated with increased horsepower and RPM. The crankshaft connects to the pistons via connecting rods, typically made of forged steel as well. These rods transmit the force of combustion to the crankshaft, converting the linear motion of the pistons into rotational motion.
The pistons themselves are typically cast aluminum alloy. They feature piston rings, which seal the combustion chamber and prevent oil from entering. Good piston ring seal is crucial for maintaining compression and preventing excessive oil consumption.
The cylinder bore dimensions for the KA24E are 89mm (3.50 inches) for the bore and 96mm (3.78 inches) for the stroke, giving it a displacement of 2389cc, or roughly 2.4 liters. This relatively long stroke contributes to the engine's torquey nature, particularly in the lower RPM range.
Cylinder Head and Valvetrain
The cylinder head is made of aluminum alloy, which helps to dissipate heat more effectively than cast iron. This is particularly important around the combustion chambers and exhaust ports. The KA24E utilizes a single overhead cam (SOHC) design. This means there's only one camshaft in the cylinder head, controlling both the intake and exhaust valves.
The valvetrain is relatively simple. The camshaft lobes act directly on rocker arms, which then push down on the valve stems, opening the valves. Valve springs then return the valves to their closed position. This is a simpler system than dual overhead cam (DOHC) designs, making it easier to maintain and understand.
The KA24E features 3 valves per cylinder: two intake valves and one exhaust valve. This configuration provides a decent balance between intake flow and exhaust scavenging. While not as efficient as a four-valve per cylinder design, it’s a cost-effective compromise.
Valve timing is crucial to engine performance. The camshaft is driven by a timing chain, which connects it to the crankshaft. The precise relationship between the camshaft and crankshaft determines when the valves open and close relative to the piston position. Incorrect valve timing can lead to reduced power, poor fuel economy, and even engine damage.
Fuel and Ignition Systems
The KA24E utilizes multi-port fuel injection (MPFI). This means that each cylinder has its own fuel injector, located in the intake manifold near the intake valve. This allows for more precise fuel delivery compared to throttle body injection (TBI).
The fuel injectors are controlled by the engine control unit (ECU), which determines the amount of fuel to inject based on various sensor inputs, such as engine speed (RPM), throttle position, and manifold air pressure (MAP). The ECU aims to maintain the optimal air-fuel ratio (AFR) for efficient combustion.
The ignition system uses a distributor to distribute the spark to the correct cylinder at the correct time. The distributor is driven by the camshaft. Inside the distributor is a rotor that spins and makes contact with terminals connected to each spark plug wire. The spark plugs then ignite the air-fuel mixture in the combustion chamber.
The ignition timing is also controlled by the ECU. The ECU advances or retards the ignition timing based on engine load and speed. Optimal ignition timing is essential for maximizing power and preventing engine knock (detonation).
Intake and Exhaust Systems
The intake manifold is responsible for distributing air to the cylinders. It's designed to provide relatively equal airflow to each cylinder. However, the design of the intake manifold can also affect the engine's powerband. Longer runners tend to improve low-end torque, while shorter runners tend to improve high-end horsepower.
The exhaust manifold collects exhaust gases from the cylinders and directs them to the exhaust system. Factory exhaust manifolds are typically made of cast iron and are designed for cost-effectiveness and durability, rather than optimal flow. Upgrading to an aftermarket header can significantly improve exhaust flow and increase horsepower.
The exhaust system consists of a catalytic converter, which reduces harmful emissions, and a muffler, which reduces noise. Upgrading the exhaust system can also improve exhaust flow and increase horsepower, especially when paired with an aftermarket header.
Lubrication and Cooling Systems
The lubrication system is responsible for providing oil to all moving parts in the engine, reducing friction and wear. The oil pump, driven by the crankshaft, circulates oil through the engine. Oil is filtered to remove contaminants before being distributed to the bearings, pistons, and valvetrain.
The cooling system is responsible for maintaining the engine at a safe operating temperature. The water pump circulates coolant through the engine block, cylinder head, and radiator. The radiator dissipates heat from the coolant. A thermostat regulates the flow of coolant to maintain a consistent engine temperature.
Common KA24E Issues and Modifications
The KA24E is generally a very reliable engine, but like any engine, it has its common issues. One common issue is timing chain wear, especially on higher mileage engines. This can lead to timing issues and reduced performance. It's recommended to replace the timing chain and tensioner as part of a preventative maintenance schedule, typically around 100,000 miles.
Another common issue is distributor failure. The distributor is a mechanical device that can wear out over time. Symptoms of a failing distributor include misfires, rough running, and difficulty starting.
Oil leaks are also common, particularly from the valve cover gasket, oil pan gasket, and front main seal. These leaks are usually easy to fix with replacement gaskets and seals.
As for modifications, the KA24E responds well to basic bolt-on upgrades. A cold air intake, aftermarket header, and cat-back exhaust system can significantly improve horsepower and torque. Upgrading the ECU or using a standalone engine management system can also unlock more power.
For more serious power gains, forced induction (turbocharging or supercharging) is a popular option. The KA24E's robust bottom end can handle a decent amount of boost with proper tuning and supporting modifications. However, it's important to remember that increasing horsepower will also increase stress on the engine, so it's important to build the engine properly to ensure reliability.
Finally, don't underestimate the importance of proper maintenance. Regular oil changes, coolant flushes, and spark plug replacements are crucial for keeping the KA24E running smoothly for years to come. Pay attention to any unusual noises or symptoms, and address them promptly to prevent more serious problems.