Technical Specifications And Airflow Analysis Of The Oem Intake System
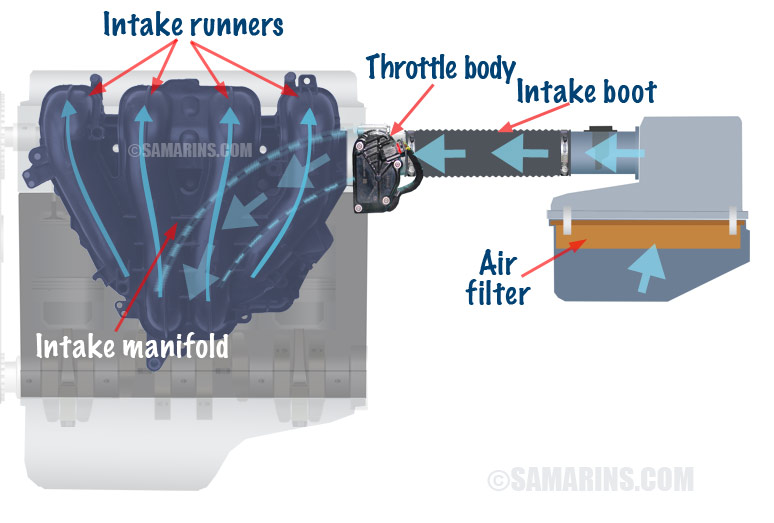
Let's delve into the often-overlooked yet crucial component of any internal combustion engine: the OEM (Original Equipment Manufacturer) intake system. This guide will provide a detailed technical analysis of its specifications and, most importantly, the airflow dynamics that govern its performance. Understanding the intricacies of the intake system is paramount to grasping the overall efficiency and power output of an engine.
Defining the OEM Intake System
The OEM intake system encompasses all components responsible for drawing air into the engine's cylinders. This usually includes, but is not limited to:
- Air filter and airbox assembly
- Intake piping (often plastic or rubber)
- Throttle body
- Intake manifold (plenum and runners)
Each component plays a specific role, and their interaction determines the overall airflow characteristics. OEM systems are designed with a primary focus on reliability, cost-effectiveness, noise reduction, and meeting stringent emissions regulations. This often means compromises are made in terms of outright performance when compared to aftermarket alternatives.
Technical Specifications: A Component-by-Component Breakdown
Air Filter and Airbox
The air filter's primary function is to remove particulate matter from the incoming air, preventing damage to sensitive engine components. OEM filters are typically made of pleated paper, offering a balance between filtration efficiency and airflow restriction. Key specifications include:
- Filtration Efficiency: Measured as the percentage of particles of a certain size that are captured. OEM filters usually aim for a high efficiency, typically above 95% for particles larger than a few microns.
- Airflow Restriction: Measured in inches of water column (inH2O) at a specific flow rate. This indicates how much the filter impedes airflow. Lower values are generally better for performance, but can compromise filtration.
- Surface Area: A larger surface area allows for greater airflow and a longer service life before clogging.
- Material: Pleated paper is the most common, but some OEMs use oiled cotton gauze or synthetic materials in certain applications.
The airbox serves as a housing for the air filter and helps to manage airflow. Its design influences the velocity and direction of air entering the intake piping. Features like resonators are often integrated into the airbox to reduce intake noise.
Intake Piping
The intake piping connects the airbox to the throttle body. Its design is crucial for minimizing flow losses and maintaining consistent airflow. Key specifications include:
- Diameter: Affects the airflow capacity. A larger diameter generally allows for higher flow rates, but can reduce air velocity.
- Material: Typically plastic or rubber, chosen for their flexibility, cost-effectiveness, and noise damping properties. Smooth internal surfaces are desirable to minimize friction.
- Bends and Transitions: Sharp bends and abrupt changes in diameter can create turbulence and flow restrictions. OEM systems often incorporate gradual curves to minimize these losses.
Throttle Body
The throttle body controls the amount of air entering the intake manifold. Its design directly impacts throttle response and overall engine performance. Key specifications include:
- Bore Diameter: Determines the maximum airflow capacity. Larger bores generally improve high-RPM performance, but can negatively affect low-end torque and drivability.
- Throttle Plate Design: The shape and angle of the throttle plate influence airflow characteristics and throttle sensitivity.
- Throttle Actuation: Modern vehicles use electronic throttle control (ETC), also known as drive-by-wire, which allows the ECU (Engine Control Unit) to precisely control the throttle opening.
Intake Manifold
The intake manifold distributes air evenly to each cylinder. It typically consists of a plenum (a large chamber that collects air from the throttle body) and runners (individual pipes that lead to each intake port on the cylinder head). The intake manifold design is a critical factor in determining engine power and torque characteristics. Key specifications include:
- Plenum Volume: A larger plenum volume can improve high-RPM performance by providing a larger reservoir of air, but can reduce throttle response.
- Runner Length and Diameter: Runner length and diameter are carefully tuned to take advantage of intake resonance. Longer runners generally improve low-end torque, while shorter runners favor high-RPM power. The diameter influences the flow velocity and capacity.
- Runner Shape and Taper: Tapered runners can help to maintain consistent air velocity and improve cylinder filling.
- Material: Typically aluminum or plastic, chosen for their heat transfer properties and weight.
Airflow Analysis: Understanding the Dynamics
Analyzing airflow through the OEM intake system involves understanding the principles of fluid dynamics, including pressure, velocity, and turbulence. The goal is to minimize flow restrictions and ensure that each cylinder receives an adequate and consistent supply of air.
Volumetric Efficiency
Volumetric efficiency is a key metric for evaluating the performance of an intake system. It represents the ratio of the actual volume of air drawn into the cylinder during the intake stroke to the cylinder's swept volume. A higher volumetric efficiency indicates that the engine is effectively filling the cylinders with air, which translates to more power. OEM systems often have relatively lower volumetric efficiency compared to performance-oriented aftermarket systems, due to the design constraints mentioned earlier.
Pressure Drop
Pressure drop refers to the reduction in air pressure as it flows through the intake system. Each component, from the air filter to the intake manifold, contributes to the overall pressure drop. Excessive pressure drop restricts airflow and reduces volumetric efficiency. Engineers use computational fluid dynamics (CFD) software to simulate airflow and identify areas of high pressure drop, allowing them to optimize the intake system design.
Resonance Tuning
Intake resonance is a phenomenon where pressure waves are created within the intake manifold. These pressure waves can be tuned to increase cylinder filling at specific engine speeds. By carefully selecting the runner length and diameter, engineers can create a positive pressure wave that arrives at the intake valve just as it opens, effectively "ramming" more air into the cylinder. This is known as Helmholtz resonance. OEM intake manifolds are often designed to provide a broad torque curve by utilizing resonance tuning at multiple engine speeds.
Turbulence
Turbulence is chaotic airflow that can reduce volumetric efficiency and combustion quality. While some level of turbulence is desirable for mixing air and fuel, excessive turbulence can create flow restrictions and increase pressure drop. Smooth internal surfaces and gradual transitions in the intake piping and manifold help to minimize turbulence. Swirl and tumble are specific types of controlled turbulence that can enhance combustion efficiency. Some OEM intake systems incorporate features to promote swirl or tumble in the cylinders.
Limitations of OEM Systems
OEM intake systems, while carefully engineered, are often subject to certain limitations. These limitations typically stem from the need to balance performance with cost, reliability, noise reduction, and emissions compliance. For example, OEM air filters may prioritize filtration efficiency over airflow, while intake manifolds may be designed for a broad torque curve rather than peak horsepower. Materials choices also play a role; cost-effective plastics might be favored over lighter and more thermally efficient materials like carbon fiber. These constraints often leave room for improvement through aftermarket upgrades.
Conclusion
The OEM intake system is a complex and carefully designed component that plays a critical role in engine performance. Understanding its technical specifications and airflow dynamics is essential for appreciating its contribution to overall engine efficiency and power output. By analyzing factors such as filtration efficiency, pressure drop, resonance tuning, and turbulence, we can gain valuable insights into how OEM intake systems work and identify potential areas for improvement. While aftermarket solutions can offer performance gains, it's crucial to acknowledge the compromises and engineering considerations that go into the design of the original equipment. The next time you consider upgrading your intake, remember the intricate balance of factors that the OEM system strives to achieve.