Tension Rod Bushing Material Properties Comparison
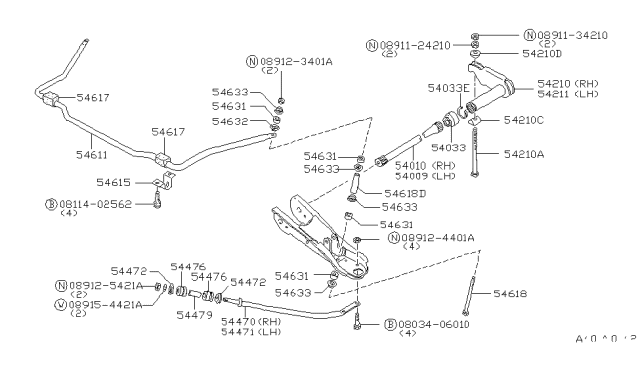
When maintaining a vehicle, understanding the properties of different components is crucial. One such component, often overlooked, is the tension rod bushing. These small but vital parts play a significant role in suspension and steering stability. Choosing the right bushing material can dramatically impact performance, longevity, and overall driving experience. This article provides a comparison of common tension rod bushing materials, helping you make an informed decision when replacing or upgrading them.
What is a Tension Rod Bushing?
Before diving into material comparisons, let's clarify what a tension rod bushing actually is and what it does. The tension rod, sometimes referred to as a radius rod, connects the vehicle's chassis to the suspension components, typically near the lower control arm. The tension rod bushing acts as an interface between the tension rod and the chassis. Its primary function is to absorb vibrations, reduce noise, and allow controlled movement of the suspension. By cushioning the connection, these bushings prevent metal-on-metal contact, minimizing wear and tear and contributing to a smoother ride.
A worn or damaged tension rod bushing can lead to several issues, including:
- Poor Handling: Reduced steering precision and increased body roll.
- Increased Noise: Clunking or rattling sounds, especially when going over bumps.
- Vibration: Noticeable vibrations felt through the steering wheel or chassis.
- Premature Tire Wear: Uneven wear patterns due to improper alignment.
- Alignment Problems: Difficulty maintaining proper wheel alignment.
Therefore, selecting the right material for your tension rod bushing is essential for optimal vehicle performance and safety.
Common Tension Rod Bushing Materials: A Comparison
Several materials are used in the manufacturing of tension rod bushings, each with its own set of advantages and disadvantages. The most common include rubber, polyurethane, and, less frequently, other specialized compounds. Let's explore the properties of each in detail:
Rubber Bushings
Rubber bushings are the most common type found in original equipment (OE) applications. They are typically made from natural or synthetic rubber compounds.
Pros:
- Excellent Vibration Damping: Rubber excels at absorbing vibrations and road noise, providing a comfortable and quiet ride.
- Cost-Effective: Rubber bushings are relatively inexpensive to manufacture, making them a budget-friendly option.
- Good Ride Quality: The compliant nature of rubber contributes to a smooth and comfortable driving experience.
- OEM Standard: Vehicles are designed with rubber bushings in mind; changing to harder materials may adversely affect ride quality if not carefully considered.
Cons:
- Lower Durability: Rubber is susceptible to degradation from heat, ozone, and petroleum products. This leads to cracking, hardening, and eventual failure.
- Less Precise Handling: The flexibility of rubber can result in some degree of play in the suspension, leading to less precise handling and responsiveness.
- Higher Deflection Under Load: Under heavy loads, rubber bushings tend to deflect more than other materials, potentially affecting alignment.
Summary: Rubber bushings are a good choice for drivers prioritizing comfort and noise reduction, and who are looking for a direct replacement for OEM parts. However, they may not be the best option for performance-oriented applications or vehicles that experience harsh conditions.
Polyurethane Bushings
Polyurethane (PU) bushings are a popular upgrade option for those seeking improved performance and durability. They are made from a synthetic polymer that offers a blend of flexibility and stiffness.
Pros:
- Higher Durability: Polyurethane is significantly more resistant to wear, tear, and degradation from environmental factors compared to rubber.
- Improved Handling: Polyurethane bushings offer less deflection under load, resulting in more precise handling and a more responsive feel.
- Greater Resistance to Chemicals: Polyurethane is less susceptible to damage from oil, grease, and other chemicals.
- Customizable Hardness: Polyurethane can be formulated in various durometers (hardness levels), allowing for tailored performance characteristics.
Cons:
- Reduced Vibration Damping: Polyurethane bushings transmit more vibration and noise compared to rubber, potentially leading to a harsher ride.
- Higher Cost: Polyurethane bushings are generally more expensive than rubber bushings.
- Potential for Squeaking: Polyurethane bushings can sometimes squeak if not properly lubricated. Special greases are often required.
- Installation Challenges: Polyurethane bushings may require specialized tools and techniques for installation.
Summary: Polyurethane bushings are a good choice for drivers who prioritize handling and durability over comfort. They are popular among enthusiasts who are willing to trade some ride quality for improved performance. They are ideal for performance applications, racing, or vehicles subject to heavy use.
Other Specialized Materials
While rubber and polyurethane are the most common, other specialized materials are sometimes used in tension rod bushings, particularly in high-performance or specialized applications. These materials might include:
- Delrin (Acetal): Offers high stiffness and low friction, often used in racing applications for minimal deflection.
- Nylon: Provides a balance of stiffness, wear resistance, and cost-effectiveness.
- Specialized Rubber Compounds: Some manufacturers use advanced rubber compounds that offer improved durability and performance compared to standard rubber.
These specialized materials offer unique properties tailored to specific needs. They are generally more expensive and require careful consideration of their specific characteristics before use.
Factors to Consider When Choosing a Tension Rod Bushing Material
Selecting the right tension rod bushing material depends on several factors, including:
- Driving Style: Aggressive driving and performance applications benefit from stiffer materials like polyurethane.
- Road Conditions: Rough roads and frequent off-road driving can accelerate wear on rubber bushings.
- Budget: Rubber bushings are the most cost-effective option, while polyurethane and specialized materials are more expensive.
- Desired Ride Quality: Rubber bushings provide a smoother, quieter ride, while polyurethane bushings offer a firmer, more responsive feel.
- Vehicle Use: Daily drivers may prioritize comfort and noise reduction, while track cars may prioritize handling and durability.
Installation Tips
Regardless of the material you choose, proper installation is crucial for optimal performance and longevity. Here are some general tips:
- Use the Correct Tools: Specific tools, such as a ball joint press or bushing removal tool, may be required for proper installation.
- Lubricate the Bushings: Apply a silicone-based grease or lubricant to the bushing surfaces to prevent squeaking and reduce friction. Never use petroleum-based lubricants on rubber or polyurethane bushings.
- Follow the Manufacturer's Instructions: Always refer to the manufacturer's instructions for specific installation procedures.
- Properly Torque Fasteners: Use a torque wrench to tighten all fasteners to the specified torque values.
- Consider Professional Installation: If you are not comfortable performing the installation yourself, consider having a qualified mechanic do the work.
Conclusion
Choosing the right tension rod bushing material is a critical step in maintaining your vehicle's suspension and steering performance. By understanding the properties of different materials, such as rubber and polyurethane, and considering your specific needs and driving conditions, you can make an informed decision that will improve your driving experience and extend the life of your vehicle's suspension components. Whether you prioritize comfort, performance, or durability, there's a tension rod bushing material that's right for you. Always research thoroughly and consult with a qualified mechanic if you have any questions.