Tension Rod Installation And Alignment Considerations
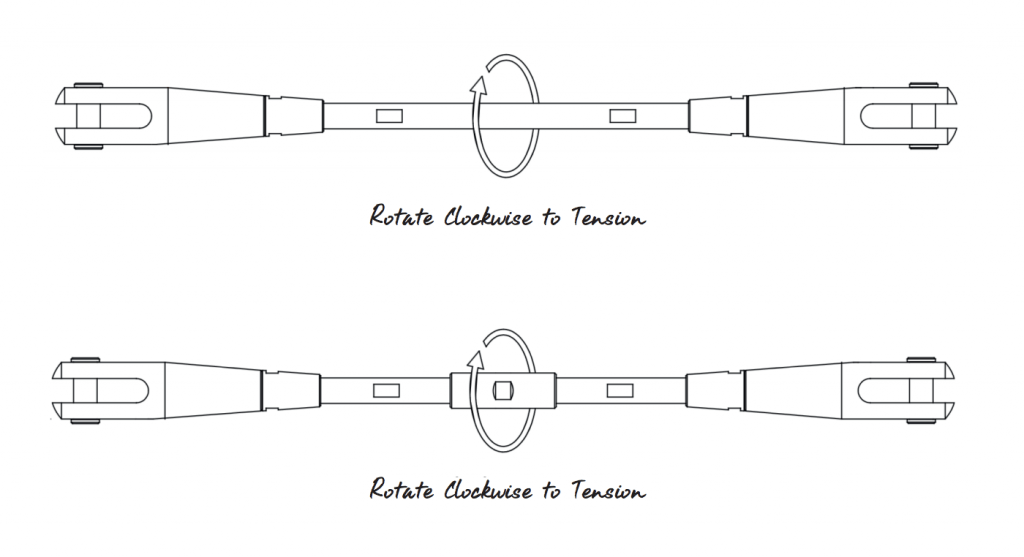
So, you're looking to upgrade or replace your tension rods? Excellent choice! Tension rods, sometimes called radius rods or compression rods, play a crucial role in your vehicle's suspension system. They primarily control fore-and-aft movement of the lower control arm, maintaining proper wheel alignment and contributing to overall handling. Incorrect installation or misalignment can lead to a host of problems, including premature tire wear, unstable braking, and even damage to other suspension components. This article will guide you through the installation and alignment considerations necessary for a successful tension rod project.
Understanding Tension Rod Function and Failure
Before diving into the installation, let's quickly recap the purpose of tension rods. Imagine your lower control arm trying to move forward under braking or acceleration. Without a tension rod, it would be free to do so, significantly altering your vehicle's caster angle. Caster is the angle of the steering pivot axis as viewed from the side of the vehicle. A positive caster angle (top of the strut leaning rearward) helps with straight-line stability. Excessive movement due to worn or missing tension rods disrupts this, leading to wandering, pulling, and a generally unpleasant driving experience.
Common symptoms of tension rod failure include:
- Clunking or knocking noises, especially during braking or acceleration.
- Vague or wandering steering.
- Excessive tire wear, often on the inside or outside edges.
- Unstable braking, particularly under hard braking.
These issues usually stem from worn-out bushings or, in more extreme cases, a bent or broken rod. Bushings are typically made of rubber or polyurethane and provide a compliant connection between the tension rod and the chassis and lower control arm. Over time, they can degrade, crack, and allow excessive movement.
Preparation is Key: Tools and Components
Proper preparation is crucial for any automotive job, and tension rod installation is no exception. Here’s a list of essential tools and materials:
- Jack and Jack Stands: Safety first! Always support your vehicle with jack stands before working underneath it.
- Wheel Chocks: Further safety to prevent rolling.
- Socket Set and Wrenches: Metric or SAE, depending on your vehicle. Make sure you have a range of sizes.
- Torque Wrench: Essential for tightening fasteners to the correct specifications.
- Ball Joint Separator (Pickle Fork or Press-Type): You might need to disconnect the lower control arm from the spindle.
- Penetrating Oil: For loosening stubborn bolts.
- Hammer: For gentle persuasion.
- New Tension Rods (with bushings): Ensure they're the correct part for your vehicle.
- New Hardware (bolts, nuts, washers): Highly recommended, as old hardware can be corroded or stretched.
- Alignment Tools (Optional): A camber/caster gauge or angle finder can be helpful for preliminary alignment adjustments.
- Safety Glasses and Gloves: Protect yourself!
- Service Manual: Crucial for torque specifications and specific instructions for your vehicle.
Before you even touch your vehicle, carefully inspect the new tension rods and bushings. Make sure they're free of defects and that the bushings are properly seated. If you opted for polyurethane bushings, consider lubricating them with a silicone-based grease to prevent squeaking.
Step-by-Step Installation Procedure
While the specific steps may vary slightly depending on your vehicle model, the general procedure for tension rod installation is as follows:
- Loosen Lug Nuts: Before lifting the vehicle, loosen the lug nuts on the wheel you'll be working on.
- Raise and Support the Vehicle: Use a jack to lift the vehicle and securely support it with jack stands. Ensure the jack stands are placed on a solid, designated jacking point.
- Remove the Wheel: Take the wheel off the hub.
- Disconnect Sway Bar Link (If Necessary): In some cases, the sway bar link might be attached to the lower control arm. Disconnect it to allow for greater range of motion.
- Disconnect Brake Caliper (If Necessary): If the brake caliper is in the way, carefully remove it. Important: Support the caliper with a wire or bungee cord so it doesn't hang by the brake line.
- Disconnect ABS Sensor (If Necessary): Disconnect the ABS sensor wire from its mounting points on the suspension components.
- Loosen Tension Rod Bolts: Locate the tension rod bolts at both the chassis and lower control arm. Apply penetrating oil and let it soak in for a few minutes. Loosen these bolts, but don't remove them completely yet.
- Separate Ball Joint (If Necessary): If the lower control arm needs to be completely removed or dropped significantly for tension rod access, you may need to separate the ball joint. Use a ball joint separator tool (pickle fork or press-type) to do this. Be extremely careful not to damage the ball joint boot.
- Remove the Old Tension Rod: Now, fully remove the tension rod bolts and carefully remove the old tension rod. Note the orientation of the rod and any washers or spacers.
- Install the New Tension Rod: Position the new tension rod in the same orientation as the old one. Install the bolts, washers, and spacers.
- Torque the Bolts: Consult your service manual for the correct torque specifications for the tension rod bolts. Critical: Torque these bolts to the specified value. Over-tightening can damage the bushings or hardware, while under-tightening can lead to loosening and movement.
- Reassemble the Suspension: Reconnect the ball joint (if disconnected), sway bar link, brake caliper, and ABS sensor wire.
- Install the Wheel: Put the wheel back on and tighten the lug nuts hand-tight.
- Lower the Vehicle: Carefully lower the vehicle back to the ground.
- Torque Lug Nuts: Torque the lug nuts to the specified value using a torque wrench.
- Repeat on the Other Side: If you're replacing both tension rods, repeat the process on the other side of the vehicle.
Alignment Considerations: Getting it Right
Replacing tension rods often affects your vehicle's alignment, particularly the caster angle. While a full professional alignment is highly recommended after this type of work, here are some important alignment considerations:
Caster Adjustment
Some vehicles have adjustable tension rods, allowing for caster adjustment. This is typically done via shims or an eccentric bolt at the chassis mount. If your vehicle has this feature, pay close attention to the initial caster setting before removing the old tension rods. You can use a camber/caster gauge or an angle finder to measure the initial angle. When installing the new tension rods, try to replicate the original caster setting as closely as possible. However, remember that this is just a starting point. A professional alignment is still necessary to ensure proper handling and tire wear.
If your vehicle doesn't have adjustable tension rods, the caster angle is generally fixed. In this case, ensuring the tension rods are installed correctly and torqued to the proper specifications is even more important. Any variation in the tension rod length or mounting position can affect the caster angle.
The Importance of a Professional Alignment
While you might be tempted to skip the professional alignment, it's a crucial step after replacing tension rods. A qualified alignment technician will use specialized equipment to precisely measure and adjust all alignment angles, including caster, camber, and toe. This ensures optimal handling, tire wear, and overall vehicle stability.
Here’s why a professional alignment is so important:
- Precise Measurements: Alignment machines provide highly accurate measurements of all alignment angles.
- Comprehensive Adjustments: Technicians can adjust all relevant alignment angles to meet factory specifications or your desired performance setup.
- Expertise: Alignment technicians have the knowledge and experience to diagnose and correct alignment issues that you might miss.
- Long-Term Savings: A proper alignment can significantly extend tire life and prevent costly suspension repairs.
Don't underestimate the importance of a professional alignment. It's an investment that will pay off in the long run.
Troubleshooting Common Issues
Even with careful installation, you might encounter some issues. Here are a few common problems and how to address them:
- Squeaking Noises: This is often caused by polyurethane bushings that haven't been properly lubricated. Apply a silicone-based grease to the bushings.
- Clunking Noises: This could indicate loose bolts or worn bushings. Double-check the torque of all bolts and inspect the bushings for damage.
- Pulling to One Side: This is a sign that the alignment is off. Get a professional alignment as soon as possible.
- Difficulty Loosening Bolts: Use penetrating oil and a breaker bar to loosen stubborn bolts. If necessary, apply heat with a torch (exercise extreme caution!).
- Stripped Threads: If you strip the threads on a bolt or in the chassis, you'll need to repair them. Use a thread repair kit (e.g., Heli-Coil) or replace the damaged component.
By following these guidelines and paying close attention to detail, you can successfully install your tension rods and restore your vehicle's handling and stability. Remember safety first, and don't hesitate to seek professional help if you're unsure about any aspect of the installation or alignment process. Good luck!