Tubed Front End Chassis Reinforcement Engineering Analysis
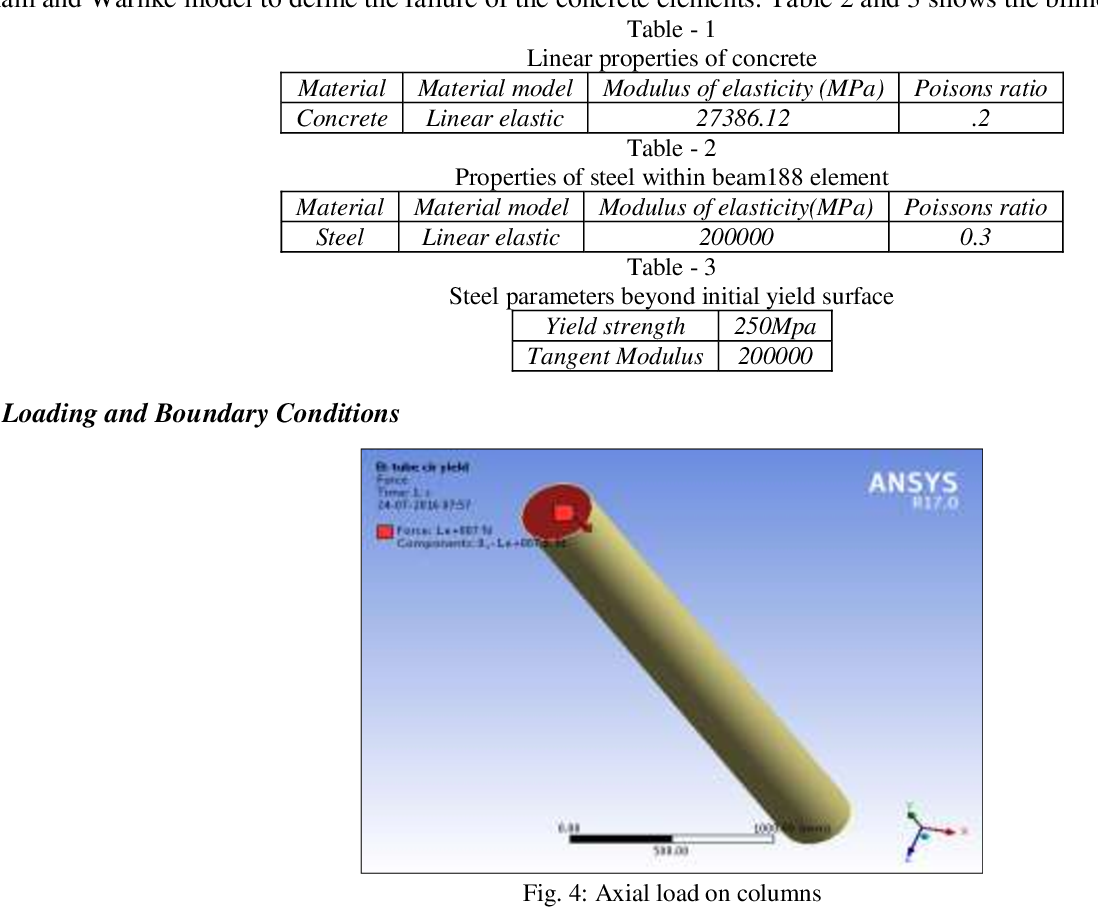
Hey there, fellow car enthusiast! Ever notice your classic muscle car or off-road rig feeling a little... wobbly? Maybe the steering isn't as crisp as it used to be, or you're hearing some unsettling creaks and groans when tackling rough terrain. Chances are, your front end chassis is showing its age, and that's where tubed front end chassis reinforcement comes into play.
The Problem: Front End Flex and Weakness
Let's face it, vehicle chassis, especially on older or heavily used vehicles, are subjected to tremendous stress. Think about it: engine weight, suspension forces, braking loads, and the constant vibrations of driving all conspire to weaken the frame over time. This is especially true for vehicles that see a lot of off-road action, autocross events, or those with significant engine modifications. The original chassis, designed for a specific power output and driving style, can struggle to cope with increased demands.
What happens when the chassis flexes? Several things:
- Poor Handling: Flex in the front end can negatively impact steering response, making the vehicle feel vague and unpredictable. It can also lead to increased body roll in corners.
- Suspension Misalignment: A flexing chassis can throw off suspension geometry, leading to uneven tire wear and reduced handling performance.
- Cracking and Fatigue: Repeated flexing can cause cracks to form in the frame, eventually leading to structural failure. This is a serious safety concern.
- Noise and Vibration: Excessive chassis flex can manifest as annoying squeaks, rattles, and vibrations, making for an unpleasant driving experience.
For off-road vehicles, the problem is often exacerbated by impacts and torsional forces encountered on rough terrain. The stock chassis might simply not be strong enough to withstand the constant abuse.
The Solution: Tubed Front End Chassis Reinforcement
Tubed front end chassis reinforcement involves welding steel tubing to the existing frame to significantly increase its strength and rigidity. Think of it as adding a roll cage to the front of your vehicle, providing a robust framework that can withstand far greater stresses. This isn't just about slapping some tubes on; it's about strategically designing and implementing a system that addresses the specific weaknesses of your chassis.
Here's why it's such an effective solution:
- Increased Strength: The added tubing creates a significantly stronger and more rigid frame, reducing flex and improving overall handling.
- Improved Handling: A stiffer chassis allows the suspension to work more effectively, resulting in sharper steering response, reduced body roll, and better overall control.
- Enhanced Durability: Reinforcement can prevent cracks and fatigue from forming, extending the lifespan of your chassis.
- Customization: Tubing can be tailored to your specific needs and driving style, whether you're building a dedicated off-road machine or a high-performance street car.
Engineering Analysis: The Key to Success
Before you start welding tubes to your frame, it's crucial to understand where and how to reinforce it. This is where engineering analysis comes in. A proper analysis will identify the areas of the chassis that are most prone to flexing and stress, allowing you to target your reinforcement efforts effectively.
Here are some common methods used in engineering analysis for chassis reinforcement:
- Finite Element Analysis (FEA): FEA uses computer simulations to model the stress and strain distribution within the chassis under various load conditions. This allows engineers to identify weak points and optimize the reinforcement design.
- Strain Gauge Testing: Strain gauges are small sensors that measure the amount of deformation in a material under load. By attaching strain gauges to the chassis and subjecting it to real-world driving conditions, engineers can gather valuable data on stress levels.
- Experienced Intuition (with caution): While not a substitute for proper analysis, an experienced fabricator or chassis builder can often identify common weak points based on their knowledge and past projects. However, relying solely on intuition can lead to suboptimal or even detrimental reinforcement.
The results of the engineering analysis will inform the design of the tubing structure, including the diameter, wall thickness, and placement of the tubes. It will also help determine the best welding techniques and materials to use.
The Process: A Step-by-Step Overview
While the specific steps involved will vary depending on the vehicle and the complexity of the reinforcement, here's a general overview of the process:
- Assessment and Planning: Thoroughly inspect the existing chassis for any signs of damage or weakness. Determine the goals of the reinforcement and the desired performance characteristics.
- Engineering Analysis (Highly Recommended): Conduct FEA or strain gauge testing to identify areas of high stress and determine the optimal reinforcement design.
- Design and Fabrication: Design the tubing structure based on the results of the engineering analysis. Cut, bend, and notch the tubing to the required dimensions.
- Welding: Carefully weld the tubing to the existing frame using appropriate techniques and materials. Ensure proper penetration and weld quality to avoid stress concentrations.
- Finishing: Grind and smooth the welds, and apply a protective coating to prevent rust and corrosion.
- Alignment: After welding, it's critical to check the chassis alignment and correct any deviations. Welding can introduce significant stresses that distort the frame.
- Testing and Refinement: Test the reinforced chassis under real-world driving conditions and make any necessary adjustments.
Tools and Equipment
To tackle a project like this, you'll need a range of tools and equipment, including:
- Welding Machine: MIG or TIG welder, depending on the type of steel and the desired weld quality.
- Metal Cutting Tools: Chop saw, angle grinder, plasma cutter.
- Tube Bender: Hydraulic or manual tube bender for creating smooth, precise bends.
- Tube Notcher: For creating accurate notches in the tubing to ensure proper fitment.
- Measuring Tools: Tape measure, square, angle finder, levels.
- Safety Equipment: Welding helmet, gloves, safety glasses, ear protection.
- Alignment Tools: Frame measuring system, levels, plumb bobs.
Approximate Costs
The cost of tubed front end chassis reinforcement can vary widely depending on several factors, including:
- Complexity of the Design: A simple reinforcement will be less expensive than a complex one.
- Materials Used: The type and amount of steel tubing will affect the cost.
- Labor Costs: Hiring a professional fabricator will add to the overall cost.
- Engineering Analysis: If you opt for FEA or strain gauge testing, expect to pay for the engineering services.
As a rough estimate, a basic tubed front end reinforcement could cost anywhere from $500 to $2000 if you do the work yourself. Hiring a professional could easily double or triple that cost, especially if extensive engineering analysis is involved. Remember to factor in the cost of materials, tools, and any necessary alignment work.
Is it Right for You?
Tubed front end chassis reinforcement is a significant undertaking, and it's not for everyone. Here are some questions to ask yourself to determine if it's the right solution for your needs:
- Are you experiencing significant chassis flex or weakness?
- Are you planning to push your vehicle to its limits in off-road or high-performance applications?
- Are you comfortable with welding and fabrication, or are you willing to hire a professional?
- Are you prepared to invest the time and money required for a proper reinforcement?
If you answered yes to most of these questions, then tubed front end chassis reinforcement could be a worthwhile investment. However, it's important to do your research, plan carefully, and seek professional advice when needed. Don't hesitate to consult with experienced fabricators or chassis builders to discuss your specific needs and get their recommendations.
Ultimately, a well-engineered and properly executed tubed front end chassis reinforcement can transform your vehicle's handling, durability, and overall performance. It's an investment that can pay off handsomely in terms of increased driving enjoyment and peace of mind.
Drive safe and happy wrenching!