Tubed Front End Kit Structural Integrity Assessment
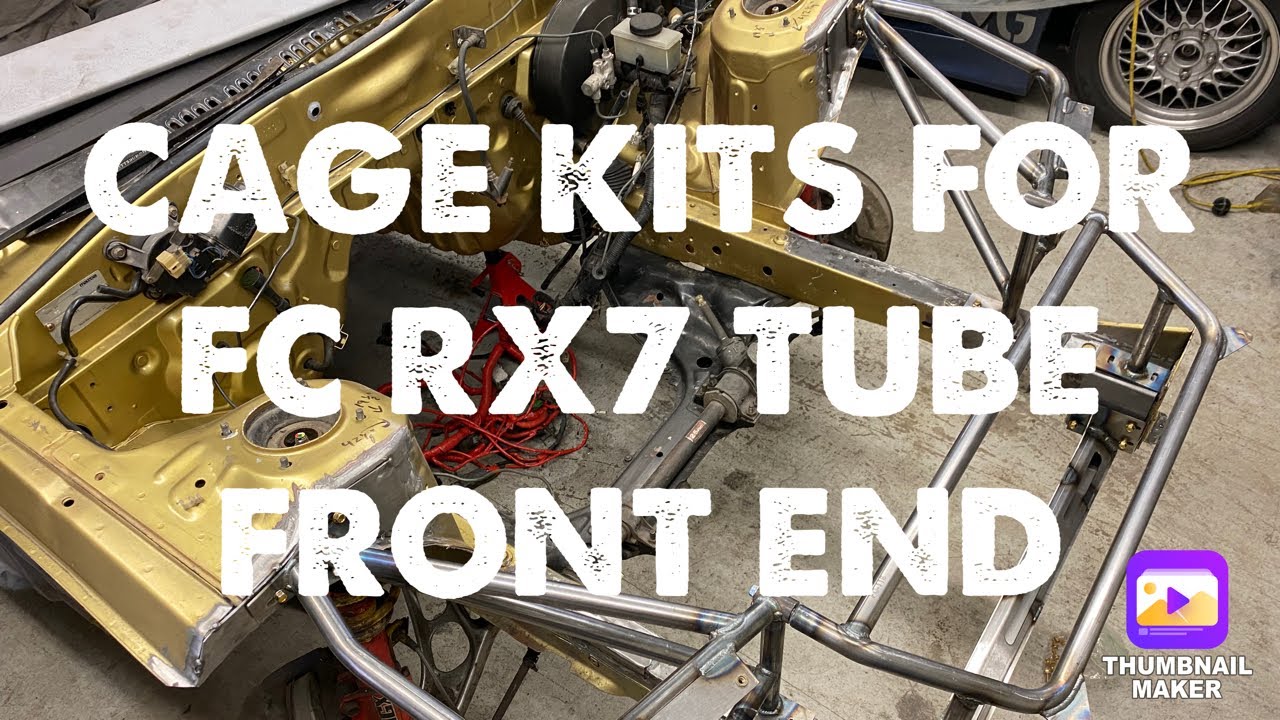
Replacing the stock front end of a vehicle with a tubed front end kit is a modification often undertaken for improved handling, weight reduction, or aesthetics, particularly in performance and off-road applications. However, the structural integrity of a tubed front end kit is paramount for safety and performance. This article delves into assessing the structural integrity of these kits, offering valuable insights for both seasoned mechanics and those new to vehicle modifications.
Understanding Tubed Front End Kits
Before assessing structural integrity, it's important to understand what a tubed front end kit is and why it's used. These kits typically replace the factory front suspension components with a fabricated structure made of tubular steel. Benefits can include:
- Weight Reduction: Tubular construction can often be lighter than factory stamped steel components.
- Improved Handling: Allows for optimized suspension geometry and increased strength.
- Increased Clearance: Provides better clearance for larger tires and obstacles, especially in off-road vehicles.
- Customization: Offers a platform for custom suspension setups and components.
However, these benefits come with a responsibility to ensure the kit is properly designed, manufactured, and installed. A compromised tubed front end kit can lead to catastrophic failure, resulting in loss of control and potential accidents.
Key Areas for Structural Integrity Assessment
Assessing the structural integrity of a tubed front end kit involves examining several critical areas. Here's a breakdown:
1. Material Selection
The type and grade of steel used in the kit's construction are crucial. Common materials include:
- Mild Steel (A36): A common and affordable option, but may not be suitable for high-stress applications.
- DOM (Drawn Over Mandrel) Steel: Offers superior strength and weldability compared to mild steel. A popular choice for many kits.
- Chromoly Steel (4130): The strongest option, offering exceptional strength-to-weight ratio. Typically used in high-performance and racing applications.
The manufacturer should clearly specify the type and grade of steel used. Inquire about certifications or testing data to verify the material's properties. Using the incorrect material can drastically reduce the kit's lifespan and safety.
2. Welding Quality
Welds are the weakest points in any fabricated structure. Thoroughly inspect all welds for the following:
- Penetration: The weld must penetrate deeply into the base metal for a strong bond. Lack of penetration is a major red flag.
- Porosity: Air pockets within the weld weaken its structure. Look for smooth, consistent welds without visible holes or imperfections.
- Undercut: A groove or depression along the edge of the weld. Undercut concentrates stress and can lead to cracking.
- Cracking: Any visible cracks in the weld or surrounding metal are unacceptable.
- Proper Bead Profile: The weld bead should be consistently shaped and properly sized for the joint.
If you're not experienced in welding inspection, consider having a certified welder or experienced fabricator assess the welds.
3. Design and Geometry
The design of the tubed front end kit plays a vital role in its strength and stability. Consider these factors:
- Triangulation: Triangles are inherently strong shapes. A well-designed kit will incorporate triangulation to distribute loads effectively.
- Tube Diameter and Wall Thickness: The diameter and wall thickness of the tubing must be appropriate for the expected loads. Larger diameter and thicker walls generally provide greater strength.
- Joint Design: The way tubes are joined together significantly impacts the overall strength. Gussets and reinforcing plates should be used in high-stress areas.
- Suspension Geometry: Ensure the kit maintains proper suspension geometry and alignment. Poor geometry can lead to handling issues and increased stress on the components.
Look for kits that have been designed and engineered by experienced professionals. Consider requesting engineering drawings or simulations to verify the design's structural integrity.
4. Mounting Points and Hardware
The mounting points where the tubed front end kit attaches to the vehicle's chassis are critical areas. Ensure the following:
- Reinforcement: The chassis should be adequately reinforced at the mounting points to prevent tearing or deformation.
- Hardware Quality: Use high-grade bolts, nuts, and washers that are properly sized for the application. Avoid using cheap or generic hardware.
- Proper Torque: Tighten all hardware to the manufacturer's specified torque values. Over-tightening can damage the hardware or chassis.
- Compatibility: Ensure the kit is compatible with your specific vehicle model and any other modifications you've made.
Pay close attention to the quality and fitment of the mounting hardware. Consider using thread locker on critical bolts to prevent them from loosening over time.
5. Installation Quality
Even the best tubed front end kit can fail if it's not installed correctly. Proper installation is crucial for ensuring structural integrity. Consider these steps:
- Professional Installation: Unless you have extensive experience in vehicle modification, it's highly recommended to have the kit installed by a qualified professional.
- Follow Instructions: Carefully follow the manufacturer's installation instructions. Do not deviate from the recommended procedures.
- Proper Alignment: Ensure the front end is properly aligned after installation. Misalignment can cause uneven tire wear and increased stress on the components.
- Regular Inspection: Periodically inspect the kit for any signs of damage, wear, or loosening hardware. Address any issues promptly.
Warning: Improper installation can void the manufacturer's warranty and compromise the safety of your vehicle.
6. Visual Inspection for Damage or Wear
Regular visual inspections are essential for maintaining the structural integrity of your tubed front end kit. Look for:
- Cracks: Any cracks in the tubing, welds, or mounting points are a serious concern and should be addressed immediately.
- Deformation: Bent or deformed tubing indicates that the kit has been subjected to excessive stress.
- Corrosion: Rust can weaken the steel over time. Protect the kit from corrosion with paint or powder coating.
- Loose Hardware: Check all bolts and nuts regularly to ensure they are properly tightened.
Address any signs of damage or wear promptly. Ignoring these issues can lead to more serious problems and potential failure.
Seeking Professional Advice
Assessing the structural integrity of a tubed front end kit can be complex. If you're unsure about any aspect of the inspection, seek professional advice from a qualified mechanic, fabricator, or engineer.
Here are some professionals who can help:
- Certified Welders: Can inspect welds and perform repairs if necessary.
- Experienced Fabricators: Can assess the overall design and construction of the kit.
- Mechanical Engineers: Can perform structural analysis to verify the kit's strength and stability.
- Suspension Specialists: Can ensure proper suspension geometry and alignment.
Investing in professional advice can save you time, money, and potentially prevent accidents. Remember, your safety and the safety of others depend on the structural integrity of your vehicle.
Conclusion
The structural integrity of a tubed front end kit is paramount for safety and performance. By carefully assessing the material selection, welding quality, design, mounting points, installation, and regularly inspecting for damage or wear, you can ensure that your kit is safe and reliable. When in doubt, seek professional advice to ensure the longevity and safety of your vehicle modification. Prioritizing safety and meticulous attention to detail will allow you to enjoy the benefits of a tubed front end kit with confidence.