Valve Cover Gasket Material Properties And Torque Specs
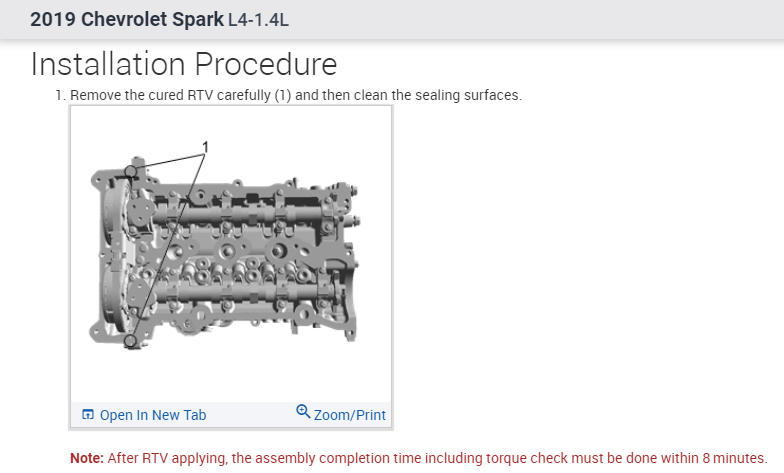
The humble valve cover gasket, often an afterthought in engine maintenance, plays a crucial role in keeping an engine running smoothly and efficiently. It's the unsung hero preventing oil leaks, maintaining proper crankcase pressure, and keeping contaminants out of the valve train. This article dives deep into the material properties and torque specifications of valve cover gaskets, exploring the engineering principles that dictate their design and proper installation.
Material Properties: A Balancing Act
Valve cover gaskets aren't just pieces of rubber or cork; they are carefully engineered components designed to withstand a challenging environment. They are constantly subjected to high temperatures, oil exposure, and the clamping force of the valve cover itself. Therefore, the material selection is paramount. Several materials are commonly used, each with its own strengths and weaknesses:
Cork
Cork gaskets were once ubiquitous. They offer good initial compressibility, meaning they conform well to uneven surfaces and create a tight seal with relatively low clamping force. However, cork's susceptibility to degradation from oil and heat is a significant drawback. Over time, cork gaskets can shrink, harden, and lose their sealing ability, leading to leaks.
Cork is also prone to splitting during installation if over-tightened.Its use is now largely limited to older vehicles and applications where the operating temperatures and oil exposure are minimal.
Rubber (NBR, EPDM, Silicone)
Rubber gaskets, in their various forms, have largely replaced cork in modern applications. Nitrile Butadiene Rubber (NBR) is a common choice due to its excellent resistance to oil and fuels. NBR offers good durability and is cost-effective, making it a suitable general-purpose material. Ethylene Propylene Diene Monomer (EPDM) rubber boasts superior resistance to heat, ozone, and weathering. It's often used in applications with higher operating temperatures. Silicone rubber represents the premium option, offering exceptional heat resistance, flexibility, and longevity. Silicone gaskets maintain their sealing properties over a wider temperature range and are less prone to hardening or cracking compared to other rubber compounds. Silicone is also resistant to a broader range of chemicals, making it suitable for demanding applications.
Rubber-Cork Composites
To combine the advantages of both materials, some valve cover gaskets utilize a composite construction of cork and rubber. These gaskets aim to provide the initial compressibility of cork with the improved durability and oil resistance of rubber. However, the overall performance typically falls short of a solid rubber or silicone gasket.
Metal (with Rubber Coating)
In certain high-performance or specialized applications, valve cover gaskets may feature a metal core, typically steel or aluminum, coated with a layer of rubber or silicone. The metal core provides dimensional stability and prevents the gasket from being crushed or over-compressed. The rubber coating ensures a tight seal against the cylinder head and valve cover. These types of gaskets are designed for high clamping forces and repeated use.
The metal core helps to distribute the clamping force evenly across the sealing surface.
The specific material used in a valve cover gasket significantly impacts its performance and lifespan. Factors such as operating temperature, oil composition, and clamping force should be considered when selecting a replacement gasket.
Torque Specifications: The Key to a Leak-Free Seal
Even the highest quality valve cover gasket will fail if not installed correctly. Torque specifications are critical for achieving a proper seal without damaging the gasket or the valve cover. These specifications are typically provided by the vehicle manufacturer and should be strictly adhered to. Under-torquing can lead to leaks, while over-torquing can crush the gasket, distort the valve cover, or even strip the threads in the cylinder head.
Understanding Torque
Torque is a measure of rotational force. It is expressed in units of pound-feet (lb-ft) or Newton-meters (Nm). Torque is determined by the force applied and the distance from the axis of rotation (e.g., the length of the wrench). Applying the correct torque ensures that the clamping force is evenly distributed across the gasket surface.
Torque Patterns
Equally important as the torque value is the tightening sequence, often referred to as the torque pattern. A proper torque pattern ensures that the clamping force is applied evenly, preventing distortion of the valve cover and ensuring a consistent seal. Typically, a crisscross or spiral pattern is recommended, starting from the center bolts and working outwards. This helps to draw the valve cover down evenly onto the cylinder head.
Always consult the vehicle's service manual for the specific torque pattern.
Torque Stages
Many modern valve cover gasket installations call for a multi-stage torque process. This involves tightening the bolts in several passes, gradually increasing the torque value with each pass. For example, the first pass might involve tightening all bolts to 5 lb-ft, the second pass to 10 lb-ft, and the final pass to the specified torque of 15 lb-ft. This staged approach allows the gasket to compress gradually and evenly, minimizing the risk of distortion or damage.
Torque-to-Yield Bolts
Some engines, particularly those with aluminum cylinder heads, utilize torque-to-yield (TTY) bolts for the valve cover. These bolts are designed to stretch elastically when tightened, providing a very precise clamping force. TTY bolts are typically single-use and must be replaced after removal. Attempting to reuse a TTY bolt can result in inaccurate torque and a compromised seal.
Lubrication
The threads of the valve cover bolts should be clean and lightly lubricated with a suitable lubricant, such as engine oil or anti-seize compound. Lubrication reduces friction and ensures that the applied torque translates accurately into clamping force. Dry threads can lead to inconsistent torque readings and potential under-tightening.
Using a Torque Wrench
A torque wrench is an indispensable tool for installing valve cover gaskets correctly. Using a properly calibrated torque wrench ensures that the bolts are tightened to the specified torque value. There are two main types of torque wrenches: click-type and beam-type. Click-type wrenches emit an audible click when the desired torque is reached, while beam-type wrenches use a needle and scale to indicate the torque value. Regardless of the type, it's crucial to use a torque wrench with an appropriate torque range for the application.
Post-Installation Inspection
After installing the valve cover gasket, it's important to inspect for any signs of leaks. Run the engine for a short period and check around the perimeter of the valve cover for oil seepage. If leaks are detected, carefully re-torque the bolts to the specified value, following the correct torque pattern. If the leaks persist, the gasket may be damaged or improperly installed, requiring further inspection and potential replacement.
Conclusion
The valve cover gasket, though seemingly simple, is a critical component in maintaining engine health and performance. Understanding the material properties and adhering to proper torque specifications are essential for a leak-free and reliable seal. By carefully selecting the correct gasket material, following the recommended torque pattern and torque value, and using a properly calibrated torque wrench, you can ensure that your valve cover gasket provides years of trouble-free service. Neglecting these details can lead to oil leaks, engine damage, and costly repairs. Therefore, take the time to understand the science behind valve cover gaskets and install them correctly.