How Can You Check An Alternator
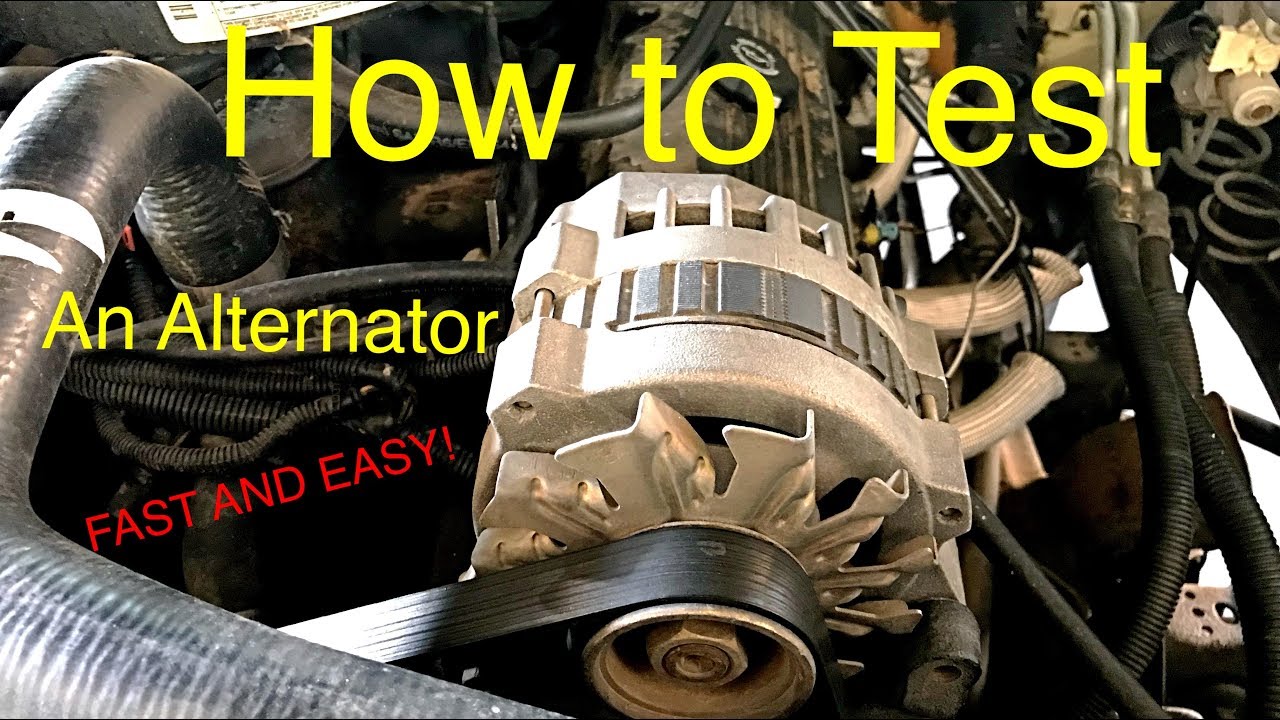
So, you're looking to check your alternator? Good move. Knowing how to diagnose alternator issues can save you a ton of money and prevent getting stranded. This guide is designed for the intermediate DIYer – someone who's comfortable working on their car but maybe hasn't delved too deep into the electrical system. We'll break down the key specs, main parts, and troubleshooting steps you need to confidently assess your alternator's health.
Purpose: Why Understanding Your Alternator Matters
Let's be clear: the alternator is the heart of your car's electrical system. It's responsible for charging your battery while the engine is running and providing power to all the electrical components, from headlights to the infotainment system. A faulty alternator can lead to a dead battery, dim headlights, and eventually, a complete breakdown. Understanding how to test and troubleshoot it is essential for preventative maintenance, DIY repairs, and even performance modifications that might strain the electrical system. Catching problems early can prevent more serious (and expensive) damage down the line.
Key Specs and Main Parts: Understanding the Anatomy
Before we dive into troubleshooting, let's review the critical components and their specs. The alternator's primary function is to convert mechanical energy from the engine into electrical energy. The key specs you'll want to be aware of include:
- Voltage Output: Typically 13.5-14.5 volts when the engine is running. This is the target voltage the alternator aims to maintain. Lower voltage indicates a potential issue.
- Amperage Output: This specifies the alternator's maximum current output capacity. Different vehicles have different amperage requirements depending on their electrical load (e.g., a car with a high-powered sound system will need a higher amperage alternator).
The main parts of an alternator are:
- Rotor (Armature): A rotating electromagnet inside the stator. It's driven by the engine via a belt and pulley.
- Stator: A set of stationary coils surrounding the rotor. As the rotor spins, it induces an alternating current (AC) in the stator windings.
- Rectifier (Diode Bridge): Converts the AC current generated in the stator to direct current (DC) needed to charge the battery and power the vehicle's electrical system. It uses diodes, which allow current to flow in only one direction.
- Voltage Regulator: Controls the amount of current supplied to the rotor, thereby regulating the alternator's output voltage. This prevents overcharging the battery and damaging electrical components.
- Brushes: Conduct electricity to the rotor, allowing it to create the magnetic field. These wear down over time and are a common source of alternator failure.
- Pulley: Connects the alternator to the engine via a belt. Sometimes this includes an overrunning alternator decoupler (OAD) or one-way clutch, which allows the alternator to spin freely in one direction, reducing belt wear and noise.
How It Works: The Magic Behind the Charge
The alternator's operation is based on electromagnetic induction. Here's a simplified explanation:
- The engine turns the alternator's pulley, which spins the rotor inside the stator.
- The rotor, an electromagnet, creates a magnetic field that rotates within the stator coils.
- This rotating magnetic field induces an alternating current (AC) in the stator windings. Faraday's Law in action!
- The AC current from the stator is then fed into the rectifier (diode bridge).
- The rectifier converts the AC current into DC current, which is suitable for charging the battery and powering the vehicle's electrical system.
- The voltage regulator monitors the battery voltage and adjusts the current supplied to the rotor to maintain the correct output voltage (typically around 13.5-14.5 volts).
Real-World Use: Basic Troubleshooting Tips
Now, let's get to the practical part. Here are some common symptoms of a failing alternator and how to diagnose them:
- Dim Headlights/Flickering Lights: This is a classic sign. The alternator isn't providing enough power to meet the electrical demand.
- Dead Battery: If your battery keeps dying, even after charging it, the alternator may not be charging it properly.
- Warning Light: The battery or charging system warning light on your dashboard is a big clue.
- Strange Noises: Whining or grinding noises from the alternator can indicate worn bearings or a failing pulley.
- Difficulty Starting: Though often attributed to the battery, a weak alternator can contribute to starting problems.
Here's a basic troubleshooting process using a multimeter:
- Visual Inspection: Check the alternator's wiring for loose connections, corrosion, or damage. Inspect the belt for wear, cracks, or proper tension.
- Voltage Test (Engine Off): With the engine off, use a multimeter to check the battery voltage. It should be around 12.6 volts.
- Voltage Test (Engine Running): Start the engine and let it idle. With the multimeter still connected to the battery terminals, check the voltage again. It should now be between 13.5 and 14.5 volts. A reading significantly below 13.5 volts suggests a problem with the alternator.
- Load Test: Turn on several electrical accessories (headlights, AC, radio) and check the voltage again. If the voltage drops significantly (below 13 volts), the alternator may not be able to handle the electrical load.
Important Note: When performing voltage tests, make sure your multimeter is set to DC voltage and the range is appropriate (e.g., 0-20 volts). Always connect the red lead to the positive terminal (+) and the black lead to the negative terminal (-). Reversing the polarity can damage the multimeter.
Safety: Respecting the Electrical System
Working on your car's electrical system can be dangerous. Here are some crucial safety precautions:
- Disconnect the Battery: Always disconnect the negative (-) battery terminal before working on any electrical components. This prevents accidental shorts and electrical shocks.
- Avoid Contact with Moving Parts: Keep your hands and tools away from the alternator pulley and belt while the engine is running.
- Use Proper Tools: Use insulated tools to prevent short circuits.
- Be Aware of High Voltage: While the alternator output is relatively low voltage, a short circuit can still generate significant heat and sparks.
- Work in a Well-Ventilated Area: Batteries can produce hydrogen gas, which is flammable.
Final Thoughts
Checking your alternator is a manageable task with the right knowledge and tools. By understanding the components, how they work, and the troubleshooting steps outlined above, you can diagnose and potentially fix alternator issues yourself. Remember to prioritize safety and consult a professional mechanic if you're unsure about any aspect of the process.