How Do You Check Fuel Injectors
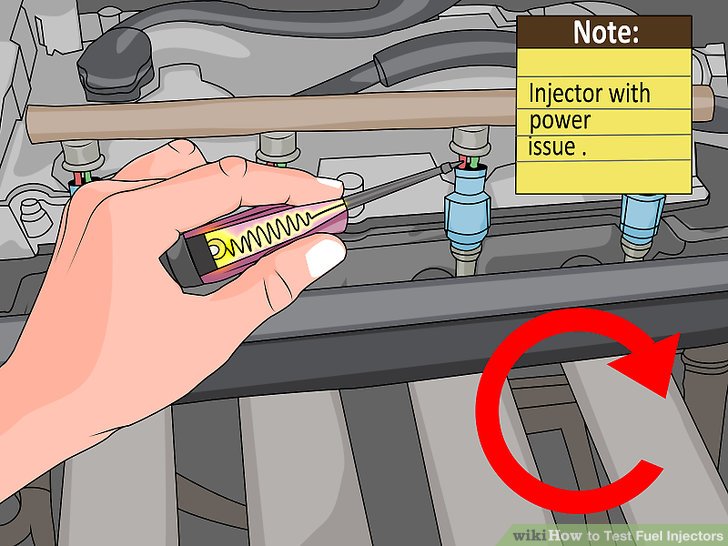
So, you think you've got a fuel injector problem? Maybe your engine's running rough, fuel economy's gone south, or you're throwing a lean code. Whatever the reason, knowing how to diagnose and check your fuel injectors is a crucial skill for any serious DIYer. This article will walk you through the process, covering everything from basic theory to practical troubleshooting. We'll assume you're comfortable with basic automotive tools and safety procedures.
Purpose of Checking Fuel Injectors
Why bother with all this diagnostic work? Simple: accurate diagnosis saves time and money. Replacing fuel injectors is an investment. Knowing for sure that they're the culprit prevents unnecessary replacements and the frustration that comes with chasing phantom issues. Plus, understanding how your fuel injectors work gives you a deeper insight into your engine's overall performance, allowing for more effective tuning and modifications. More specifically, checking fuel injectors allows you to:
- Pinpoint the source of engine misfires.
- Determine if injectors are clogged, leaking, or malfunctioning electrically.
- Evaluate the overall health and performance of your fuel system.
- Make informed decisions about repair or replacement.
Key Specs and Main Parts of a Fuel Injector
Let's get familiar with the hardware. A fuel injector is essentially a solenoid-operated valve that precisely meters fuel into the engine. Here's a breakdown of the key components:
- Injector Body: The main housing that contains all the internal components.
- Solenoid: An electromagnetic coil that, when energized, lifts the needle valve.
- Needle Valve: A precisely machined valve that controls the flow of fuel.
- Nozzle: The outlet through which fuel is sprayed into the intake manifold or combustion chamber.
- Filter Basket: A small filter at the inlet of the injector that prevents debris from entering.
- Electrical Connector: Connects the injector to the engine's wiring harness.
- O-Rings: Seals that prevent fuel leaks between the injector and the fuel rail and intake manifold.
Important specs to consider when dealing with injectors include:
- Flow Rate: Measured in lbs/hr (pounds per hour) or cc/min (cubic centimeters per minute), this indicates how much fuel the injector can deliver at a specific pressure.
- Impedance: Measured in Ohms (Ω), this indicates the electrical resistance of the solenoid coil. Injectors are typically either high-impedance (12-16 Ohms) or low-impedance (2-3 Ohms). Using the wrong type can damage your ECU.
- Spray Pattern: The shape and distribution of the fuel spray. A poor spray pattern can lead to incomplete combustion.
- Static Flow: The flow rate when the injector is held open continuously.
- Dynamic Flow: The flow rate under pulsed operation, which is closer to real-world conditions.
How Fuel Injectors Work
The Engine Control Unit (ECU) sends a signal to the fuel injector, energizing the solenoid. This creates a magnetic field that pulls the needle valve off its seat, allowing pressurized fuel to flow through the nozzle and into the intake manifold (or directly into the combustion chamber in direct injection systems). The amount of time the injector is held open, known as the pulse width, determines the amount of fuel delivered. A longer pulse width means more fuel, and vice versa. The fuel pump provides constant pressure to the fuel rail, ensuring a consistent supply of fuel to the injectors.
Real-World Use and Troubleshooting
Here's where things get practical. Let's look at some common problems and how to diagnose them:
Visual Inspection
Start with the basics. Check for:
- Fuel Leaks: Look for signs of fuel around the injectors, fuel rail, and fuel lines. Leaks are a fire hazard and indicate a faulty injector or O-ring.
- Damaged Connectors: Inspect the electrical connectors for corrosion, broken wires, or loose connections.
- Physical Damage: Look for cracks or other damage to the injector body.
Electrical Testing
Use a multimeter to check:
- Resistance: Measure the resistance of the injector's solenoid coil. Compare the reading to the manufacturer's specifications. An open circuit (infinite resistance) indicates a faulty coil. A significantly lower or higher resistance suggests a problem as well.
- Voltage: With the engine running (or cranking), check for voltage at the injector connector. You should see battery voltage when the ECU is commanding the injector to fire. No voltage indicates a wiring problem or a faulty ECU output.
- Continuity: Check the continuity of the wiring harness between the injector connector and the ECU.
Stethoscope Test
Using a mechanic's stethoscope, listen to each injector while the engine is running. You should hear a distinct clicking sound as the injector opens and closes. If an injector is silent, it may be clogged or electrically dead.
Injector Cleaning and Flow Testing
For clogged injectors, professional cleaning services use specialized equipment to clean and flow-test injectors. These machines typically use ultrasonic cleaning and back-flushing to remove deposits. Flow testing measures the actual flow rate of each injector and compares it to the manufacturer's specifications. This is the most accurate way to determine if an injector is performing correctly.
Fuel Pressure Testing
While not directly testing the injector, fuel pressure is crucial. Low fuel pressure can mimic the symptoms of faulty injectors. Use a fuel pressure gauge to check the pressure at the fuel rail. Compare the reading to the manufacturer's specifications.
OBDII Codes
Pay attention to any OBDII codes related to fuel injectors, such as P0201-P0208 (Injector Circuit Malfunction), P0300-P0308 (Misfire Detected), or P0171/P0174 (System Too Lean). These codes can provide valuable clues about the location and nature of the problem.
Safety Considerations
Working with fuel systems can be dangerous. Always take the following precautions:
- Disconnect the battery: Before working on the fuel system, disconnect the negative battery cable to prevent accidental sparks.
- Work in a well-ventilated area: Fuel vapors are flammable and toxic. Work in a well-ventilated area, away from open flames or sources of ignition.
- Wear safety glasses and gloves: Protect your eyes and skin from fuel.
- Use caution when handling fuel lines: Fuel lines are under pressure. Relieve the pressure before disconnecting any lines. A fuel pressure release tool is highly recommended.
- Be aware of static electricity: Static electricity can ignite fuel vapors. Ground yourself before working on the fuel system.
- Dispose of fuel properly: Dispose of used fuel in a proper container and according to local regulations.
Accessing Fuel Injector Diagrams
Having a detailed wiring diagram specific to your vehicle is invaluable for troubleshooting fuel injector issues. It shows the wiring layout, pin assignments, and relevant circuits. While we can't embed a specific diagram here due to file size and copyright restrictions, we have a repository of common fuel system diagrams. Contact us with your vehicle's year, make, and model, and we'll provide you with a link to download the relevant diagram.
Remember, tackling fuel injector problems requires a methodical approach. Start with the basics, follow the troubleshooting steps, and don't hesitate to seek professional help if you're unsure about any procedure. With a bit of knowledge and the right tools, you can keep your fuel injectors firing on all cylinders!