How To Test Leaking Fuel Injectors
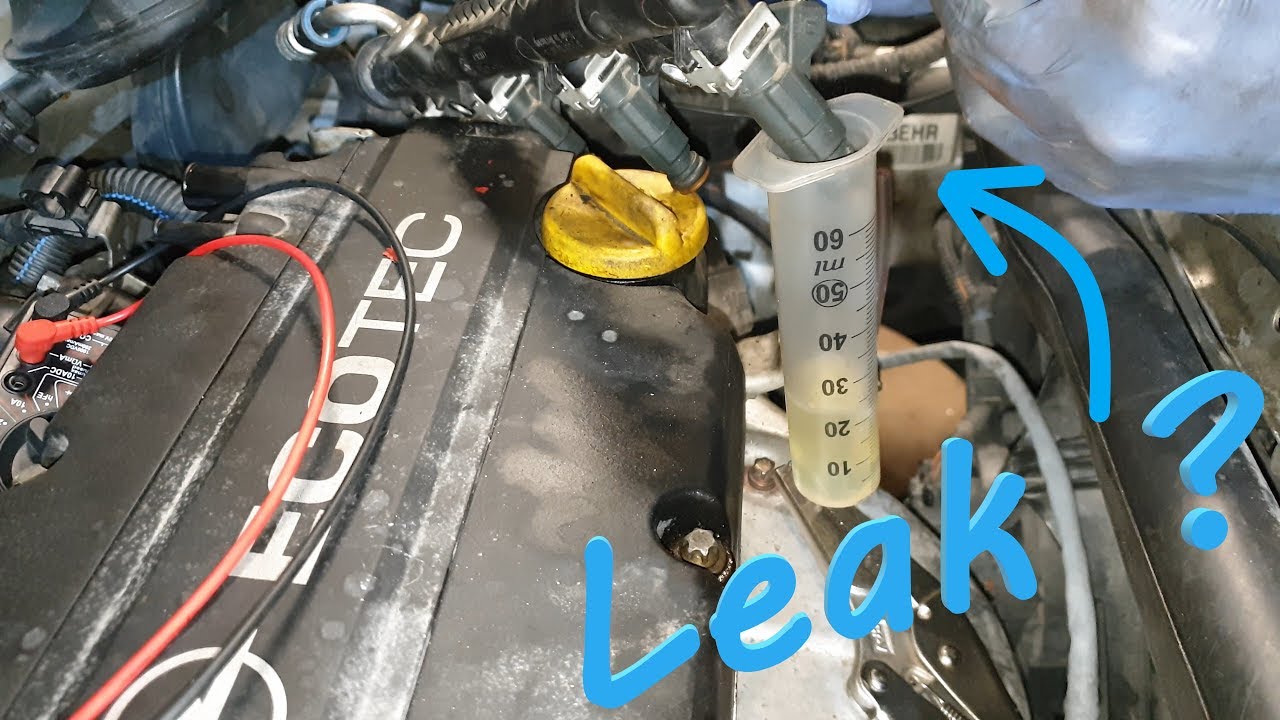
The dreaded misfire. The stumbling idle. The inexplicable drop in fuel economy. These are the harbingers of automotive woes, and all too often, the culprit lurks within the unassuming fuel injector. But how do you pinpoint a leaking injector amidst the labyrinth of your engine? This guide delves into the science and art of testing for leaking fuel injectors, equipping you with the knowledge to diagnose and potentially resolve this common automotive ailment.
The Silent Drip: Understanding the Problem
Imagine a faucet. When you turn it off, you expect the flow to cease completely. Now, picture that faucet perpetually dripping, even when shut. That's essentially what a leaking fuel injector does. Instead of delivering a precise, atomized spray of fuel when commanded, it bleeds fuel into the cylinder even when it shouldn't. This leads to a rich air-fuel mixture, particularly at idle and low speeds, causing a host of problems.
Symptoms of a leaking fuel injector often include:
- Rough idle
- Poor fuel economy
- Black smoke from the exhaust
- Difficulty starting
- Fuel smell
- Engine misfires (especially at low RPM)
- Failed emissions test
It's important to differentiate these symptoms from other potential causes like vacuum leaks, faulty spark plugs, or a malfunctioning oxygen sensor. A systematic approach to diagnosis is crucial.
How Fuel Injectors Work: A Quick Primer
Before diving into testing, let's recap how fuel injectors function. These are essentially electronically controlled valves that spray fuel directly into the engine's intake manifold (in port fuel injection systems) or directly into the combustion chamber (in direct injection systems). When the engine control unit (ECU) determines that fuel is needed, it sends an electrical signal to the injector. This signal energizes a solenoid, which lifts a needle valve off its seat, allowing fuel to spray through a precisely engineered nozzle. The duration of the signal (pulse width) determines the amount of fuel delivered.
A leaking injector, however, fails to fully seal when the solenoid is de-energized. This can be due to several factors, including:
- Contamination: Debris in the fuel system can lodge in the injector, preventing a proper seal.
- Wear and Tear: Over time, the needle valve and seat can wear down, leading to leakage.
- Corrosion: Exposure to moisture and contaminants can corrode the injector components.
- Damage: Physical damage to the injector can also cause leaks.
Methods for Testing Leaking Fuel Injectors
Several methods can be employed to diagnose a leaking fuel injector, ranging from simple visual inspections to more sophisticated techniques.
1. The Visual Inspection
While not always conclusive, a visual inspection is the first step. Look for any signs of fuel leakage around the injector body or fuel rail connections. A strong fuel smell emanating from the engine bay can also be a clue. However, be extremely cautious when working around fuel systems, as fuel is highly flammable.
Pros: Simple, quick, and requires no special tools.
Cons: Not always accurate, can be difficult to spot subtle leaks, and may not be safe if a major leak is present.
2. The Fuel Rail Pressure Drop Test
This method involves monitoring the fuel pressure after the engine is shut off. The fuel system should maintain pressure for a reasonable amount of time. A rapid pressure drop indicates a potential leak, which could be a leaking injector, a faulty fuel pump check valve, or a leak in the fuel line.
How to perform a fuel rail pressure drop test:
- Connect a fuel pressure gauge to the Schrader valve on the fuel rail.
- Start the engine and allow it to reach operating temperature.
- Note the fuel pressure reading.
- Turn off the engine.
- Monitor the fuel pressure gauge for any significant drop in pressure over a period of 15-30 minutes.
A pressure drop of more than a few PSI within that time frame suggests a leak. Further investigation is needed to pinpoint the source.
Pros: Relatively simple, provides a good indication of overall fuel system integrity.
Cons: Doesn't isolate the leak to a specific injector, requires a fuel pressure gauge.
3. The Cylinder Balance Test (Power Balance Test)
This test helps identify which cylinder is misfiring due to a leaking injector. By temporarily disabling each injector one at a time, you can observe the engine's response. If disabling a particular injector *improves* the engine's performance, it's a strong indication that the injector was leaking and causing a rich condition in that cylinder.
How to perform a cylinder balance test:
- Start the engine and allow it to idle.
- One at a time, disconnect each fuel injector connector (be careful not to damage the connectors).
- Observe the engine's RPM or smoothness of operation when each injector is disconnected.
- If disconnecting an injector causes the engine to run smoother or the RPM to increase, that injector is likely the culprit.
Important Note: This test should be performed carefully, as disconnecting fuel injectors can potentially damage catalytic converters. It's best to perform this test for short durations and avoid prolonged running with injectors disconnected.
Pros: Helps pinpoint the leaking injector to a specific cylinder.
Cons: Can be risky if not performed carefully, requires access to injector connectors, and doesn't quantify the leak rate.
4. The Injector Leak-Down Test (Professional Method)
This is the most accurate method for testing leaking fuel injectors. It requires specialized equipment: a fuel injector testing machine. The machine allows you to pressurize the injector and observe the leak rate over a specific period. This test can also assess the injector's spray pattern and flow rate, providing a comprehensive evaluation of its performance.
How it works: The injector is connected to the testing machine, pressurized to a specific pressure, and the amount of fuel that leaks past the nozzle is measured over a defined time. Acceptable leak rates vary depending on the injector type and manufacturer specifications.
Pros: Highly accurate, provides quantitative data on leak rate, can assess spray pattern and flow rate.
Cons: Requires specialized equipment, typically performed by professional mechanics.
Manufacturer Examples & Considerations
Fuel injector designs and tolerance levels vary across manufacturers. For instance, Bosch injectors are commonly found in European vehicles, while Denso injectors are prevalent in Japanese cars. Each manufacturer has specific leak-down test specifications. Always consult the vehicle's service manual or the injector manufacturer's data sheet for the correct testing procedures and acceptable leak rates.
For direct injection systems, the pressure is significantly higher than port injection systems (often exceeding 1000 PSI). Testing direct injectors requires specialized equipment designed to handle these extreme pressures, making DIY testing challenging and potentially dangerous.
Real-World Insights and Recommendations
In the real world, a combination of testing methods often provides the most reliable diagnosis. Start with a visual inspection and a fuel rail pressure drop test. If those tests suggest a leak, perform a cylinder balance test to pinpoint the affected cylinder. If the problem persists or you want a definitive answer, consider having the injectors tested by a professional using a leak-down testing machine.
If you confirm a leaking fuel injector, replacement is usually the best course of action. While injector cleaning services exist, they are not always effective in resolving leaks caused by wear or damage. Replacing the entire set of injectors is often recommended to ensure balanced fuel delivery and prevent future problems, especially on older vehicles.
Prevention is key. Using high-quality fuel with detergents and regularly replacing the fuel filter can help prevent contamination and extend the lifespan of your fuel injectors. A well-maintained fuel system is a happy fuel system, and a happy fuel system means a happy engine – and a happy driver!