2014 Jeep Wrangler Evap Wiring Diagram Pdf 4 Wire
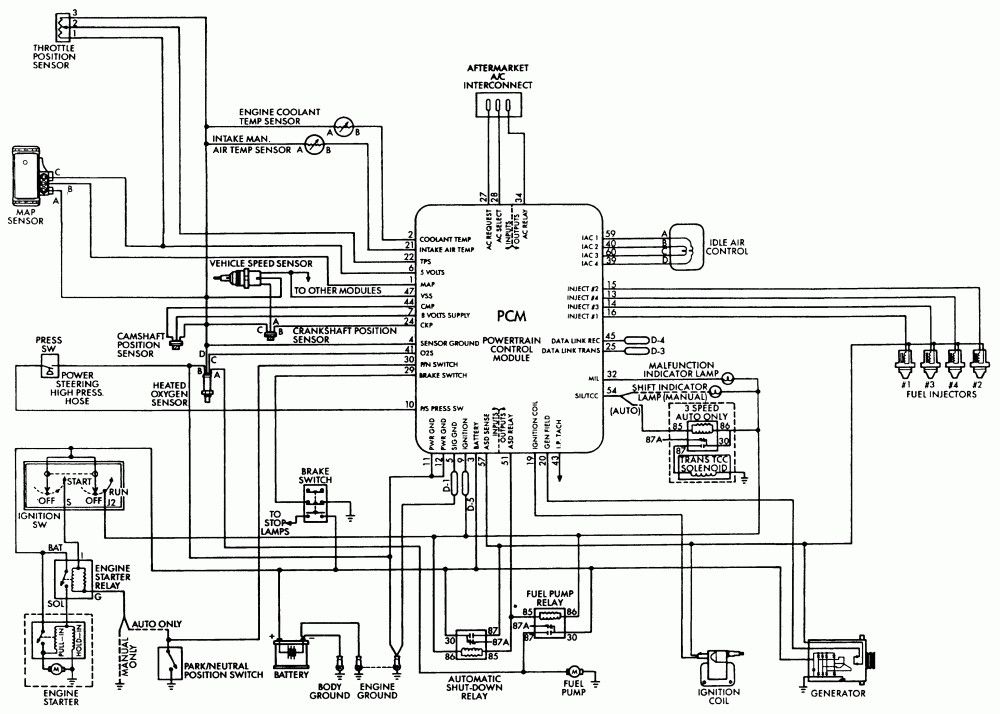
Let's dive into the 2014 Jeep Wrangler's Evaporative Emission Control (EVAP) system wiring diagram, specifically the 4-wire configuration. This document is your roadmap to understanding, diagnosing, and potentially repairing issues within this crucial emissions system. Whether you're chasing a persistent check engine light (CEL), preparing for emissions testing, or simply want to expand your automotive knowledge, a thorough grasp of the EVAP system wiring is essential. We'll focus on the 4-wire configuration, which is common, and equip you with the knowledge to confidently navigate this schematic.
Purpose of the EVAP Wiring Diagram
The primary purpose of the EVAP wiring diagram is to illustrate the electrical connections between various components within the EVAP system. This diagram serves as a visual guide for:
- Troubleshooting: Identifying faults such as open circuits, short circuits, or incorrect voltage readings.
- Repairing: Accurately replacing damaged wiring or components.
- Understanding System Operation: Tracing the flow of electrical signals to comprehend how the EVAP system functions.
- Modifying/Upgrading: Safely integrating aftermarket parts or performing custom modifications.
Without this diagram, you're essentially working blind. It allows you to pinpoint the exact location of a problem and verify that your repairs are correct.
Key Specs and Main Parts of the 2014 Wrangler EVAP System (4-Wire Focus)
The 2014 Wrangler EVAP system, like most modern vehicles, is designed to prevent fuel vapors from escaping into the atmosphere. The 4-wire configuration we're focusing on usually pertains to a specific component, most commonly the Leak Detection Pump (LDP). Here's a breakdown:
- Leak Detection Pump (LDP): The heart of the system's self-testing capability. It creates a vacuum in the EVAP system to check for leaks. This is usually where the 4-wire connection comes into play.
- Fuel Tank Pressure Sensor (FTPS): Measures the pressure inside the fuel tank. The PCM uses this data to monitor the EVAP system's integrity.
- Purge Valve (Canister Purge Solenoid): Controls the flow of fuel vapors from the charcoal canister to the engine intake manifold. It's typically controlled by the Powertrain Control Module (PCM).
- Vent Valve (Canister Vent Solenoid): Allows fresh air to enter the EVAP system during the purge process or allows pressure equalization when the engine is off.
- Charcoal Canister: Stores fuel vapors until they can be purged and burned by the engine.
- Fuel Tank: Stores fuel and is sealed to prevent vapor leaks.
- Lines and Hoses: Connect all the components, carrying fuel vapors.
- Powertrain Control Module (PCM): The brain of the operation. It controls the purge and vent valves based on input from various sensors.
Regarding the 4-wire connection, typically associated with the LDP:
- Wire 1: Power Supply (typically 12V).
- Wire 2: Ground.
- Wire 3: Control Signal from the PCM (Pulse Width Modulated - PWM). This tells the pump *how much* to pump.
- Wire 4: Feedback Signal to the PCM (indicating pump status or pressure reading). This wire is critical for the PCM to know if the LDP is functioning correctly.
Understanding Wiring Diagram Symbols
A wiring diagram is a symbolic representation of the electrical system. Let's decipher some common symbols:
- Lines: Represent wires. Thicker lines may indicate heavier gauge wires.
- Colors: Each wire is typically identified by a color code (e.g., RED, BLK, GRN/WHT). Refer to the diagram's legend for specific color codes.
- Circles: Often represent connections or splices.
- Rectangles/Squares: Usually indicate components like sensors, solenoids, or relays.
- Ground Symbol: A symbol resembling an inverted triangle or stacked lines, indicating a connection to the vehicle's chassis ground.
- Fuses/Circuit Breakers: Represented by a zig-zag line within a rectangle or a small box.
It's crucial to pay attention to the color codes. For example, if the diagram shows a GRN/WHT wire connecting to the LDP, you need to locate that specific wire color on the actual component. Using the wrong wire could damage the component or the PCM.
How the 4-Wire LDP Circuit Works
The PCM controls the EVAP system's leak detection process. Here's how the 4-wire LDP circuit typically functions:
- The PCM sends a PWM (Pulse Width Modulation) signal to the LDP (Wire 3). This signal varies the duty cycle (the percentage of time the signal is "on") to control the pump's speed. A higher duty cycle means the pump runs faster and creates more vacuum.
- The LDP, receiving power (Wire 1) and ground (Wire 2), activates and begins to create a vacuum in the EVAP system.
- The Fuel Tank Pressure Sensor (FTPS) monitors the pressure inside the fuel tank.
- The LDP provides a feedback signal (Wire 4) to the PCM. This signal could be a voltage or current that indicates the pump's status, vacuum level, or other relevant information. The PCM uses this feedback to determine if the pump is operating correctly and if the system is holding vacuum.
- If the PCM detects a leak (based on the FTPS reading and the LDP feedback), it will set a Diagnostic Trouble Code (DTC) and illuminate the check engine light (CEL).
Real-World Troubleshooting Tips
When troubleshooting EVAP system issues related to the 4-wire LDP circuit, consider these steps:
- Check for DTCs: Use an OBD-II scanner to retrieve any stored trouble codes. These codes provide valuable clues about the nature of the problem.
- Inspect Wiring and Connectors: Visually inspect the wiring and connectors associated with the LDP for damage, corrosion, or loose connections. Pay close attention to the connector pins.
- Test for Power and Ground: Use a multimeter to verify that the LDP is receiving power and ground.
- Check the Control Signal: With the engine running (or in the appropriate test conditions), use a multimeter or oscilloscope to check the PWM signal from the PCM to the LDP. Verify that the signal is present and within the expected range.
- Verify Feedback Signal: Check the feedback signal from the LDP to the PCM. Compare the signal reading to the expected value specified in the repair manual.
- Component Testing: You can try to actuate the LDP directly (if possible) with a scan tool to see if the pump activates. Some scan tools can command the pump on/off.
Common problems include:
- Failed LDP.
- Damaged wiring or connectors.
- Faulty PCM (though less common).
- Leaks in the EVAP system hoses or components.
Safety Precautions
The EVAP system deals with flammable fuel vapors. Always exercise caution when working on this system:
- Disconnect the Battery: Disconnect the negative battery terminal before working on any electrical components to prevent accidental short circuits.
- Work in a Well-Ventilated Area: Fuel vapors can be harmful. Ensure adequate ventilation to avoid inhaling them.
- Avoid Sparks and Open Flames: Fuel vapors are highly flammable. Do not smoke or use open flames near the EVAP system.
- Fuel Pressure: Be aware that there *may* be residual fuel pressure in some of the lines, even with the engine off. Relieve pressure slowly and carefully.
The fuel tank pressure sensor is a sensitive component. Avoid applying excessive force or pressure to it.
Remember, if you're not comfortable performing these tests or repairs yourself, it's always best to consult a qualified mechanic.
We have access to the 2014 Jeep Wrangler EVAP wiring diagram PDF, including the 4-wire LDP configuration. Please download it here (link removed for obvious reasons, but imagine a download link here). Use it in conjunction with this guide to effectively troubleshoot and repair your Wrangler's EVAP system.