Air Compressor Switch Wiring Diagram
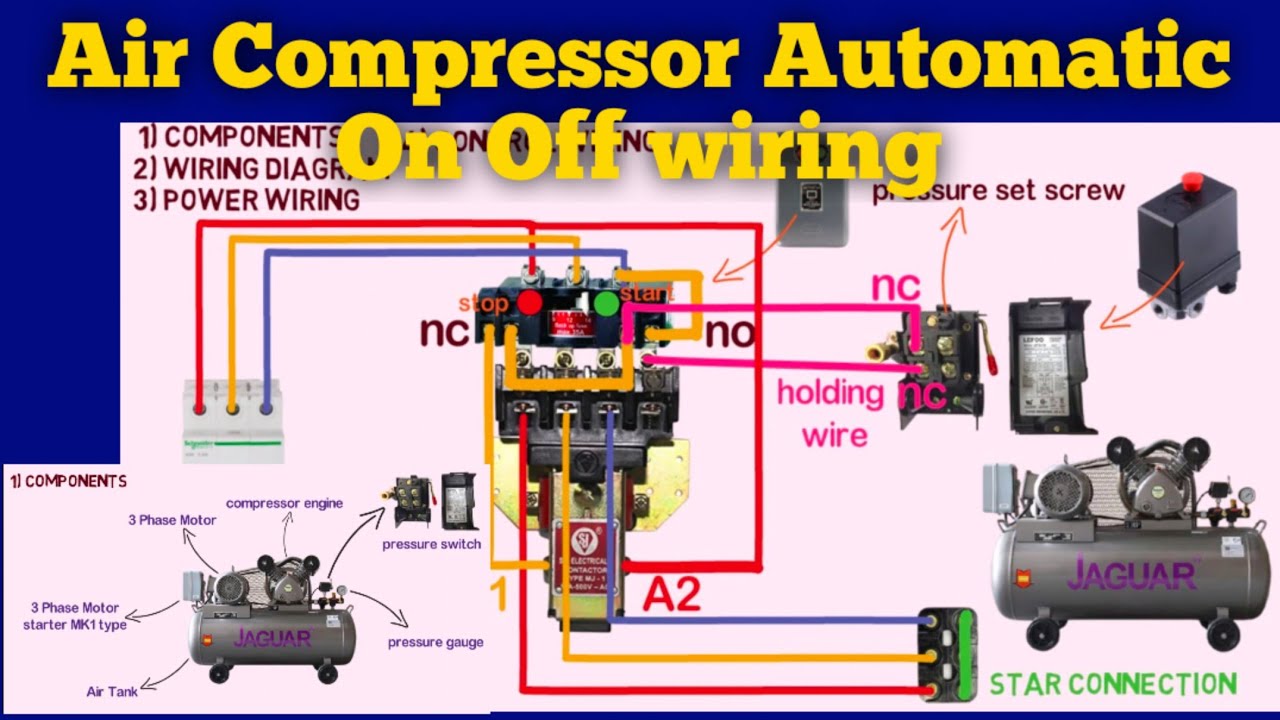
So, you're looking to understand the wiring diagram of an air compressor switch? Excellent! Whether you're troubleshooting a faulty compressor, planning a modification, or simply expanding your DIY knowledge, understanding this diagram is crucial. Think of it as the roadmap to the electrical heart of your compressor. We're going to break down the ins and outs of this diagram, from the basic components to real-world troubleshooting, presented in a way that even an experienced DIYer can easily grasp.
Why This Diagram Matters
A wiring diagram isn't just a pretty picture; it's the key to several critical tasks:
- Repairs: Diagnosing and fixing electrical problems becomes significantly easier when you know exactly how each component is connected. Trying to guess can lead to further damage and frustration.
- Modifications: Adding features like a pressure gauge, upgrading the pressure switch, or integrating the compressor into a larger system requires understanding the existing wiring.
- Safety: Electricity is dangerous. A wiring diagram helps you identify potential hazards and ensures you're working safely by verifying proper grounding and circuit protection.
- Learning: By understanding the wiring of a simple device like an air compressor, you gain a deeper understanding of electrical circuits in general. This knowledge can be applied to other automotive or household projects.
Key Specs and Main Parts of the Compressor Switch
Before diving into the diagram, let's get familiar with the key specifications and components that make up the air compressor switch and its surrounding circuit.
Key Specs:
- Voltage: Most common air compressors operate on 120V or 240V AC. Always verify the voltage rating of your compressor before working on it!
- Amperage: The amperage rating indicates the maximum current the compressor motor draws. This is crucial for selecting appropriately sized wires and circuit breakers.
- Pressure Rating: The pressure switch has a set pressure range (e.g., 90-120 PSI). This determines when the compressor turns on and off.
Main Parts:
- Power Cord: Brings AC power to the compressor. Typically, it contains three wires: Hot (black), Neutral (white), and Ground (green).
- Pressure Switch: The brain of the operation. It senses the air pressure in the tank and opens or closes the circuit to the motor, depending on the pressure.
- Motor Starter (if applicable): Larger compressors often use a motor starter to handle the high inrush current when the motor starts. The pressure switch controls the starter, which then controls the motor.
- Capacitor(s): Start and run capacitors provide the extra boost needed to start and efficiently run the motor.
- Motor: The electric motor that drives the compressor pump.
- Check Valve: A one-way valve that prevents compressed air from flowing back into the pump when the motor is off. This isn't typically part of the electrical diagram, but its failure can mimic electrical problems.
- Overload Protection: Typically a thermal overload switch built into the motor or a separate circuit breaker. It protects the motor from overheating and damage due to excessive current.
- Unloader Valve: Connected to the pressure switch. Relieves pressure from the cylinder head so the motor can start easily.
Understanding Wiring Diagram Symbols
Wiring diagrams use standardized symbols to represent electrical components and connections. Here's a breakdown of the most common symbols you'll encounter in an air compressor switch wiring diagram:
- Lines: Solid lines represent wires. Dotted lines might indicate a physical connection or a shielded cable.
- Circles: Can represent various components, often with a letter or symbol inside to specify the type of component (e.g., 'M' for motor, 'SW' for switch).
- Resistors: Zigzag lines represent resistors, which limit current flow.
- Capacitors: Two parallel lines represent capacitors, which store electrical energy.
- Switches: A line with a pivoting arm represents a switch. The position of the arm indicates whether the switch is open (circuit broken) or closed (circuit complete). SPST(Single Pole, Single Throw), SPDT(Single Pole, Double Throw), DPST(Double Pole, Single Throw) and DPDT(Double Pole, Double Throw) are common configurations.
- Ground: A series of lines decreasing in length connected to a single point, indicating the ground connection.
- Colors: Wire colors are typically indicated by abbreviations (e.g., BLK for black, WHT for white, GRN for green, RED for red). Always verify wire colors with a multimeter before disconnecting or reconnecting wires.
- Numerical Designations: Numbers often indicate terminals or connection points on components. Refer to the component's datasheet or markings for clarification.
Important: While colors are generally standard, there may be variations. Always confirm with testing, don't assume!
How It Works: A Step-by-Step Explanation
Let's trace the electrical path in a typical air compressor circuit:
- Power Input: AC power enters the compressor through the power cord. The Hot wire carries the electrical current, the Neutral wire provides the return path, and the Ground wire provides a safety path in case of a short circuit.
- Pressure Switch Activation: When the air pressure in the tank drops below the set "cut-in" pressure (e.g., 90 PSI), the pressure switch closes its contacts, completing the circuit to the motor.
- Motor Starter Activation (if applicable): For larger compressors, the pressure switch signals the motor starter to engage. The motor starter then provides the high current needed to start the motor.
- Motor Operation: The motor receives power and starts running, driving the compressor pump to fill the air tank.
- Pressure Switch Deactivation: As the air pressure in the tank rises, the pressure switch senses the increasing pressure. When the pressure reaches the set "cut-out" pressure (e.g., 120 PSI), the pressure switch opens its contacts, breaking the circuit to the motor (or motor starter).
- Motor Shutdown: The motor stops running, and the compressor remains idle until the air pressure drops below the cut-in pressure again.
- Safety Systems: The overload protection device monitors the motor's current draw. If the current exceeds a safe level, the overload protector trips, interrupting the circuit and preventing motor damage.
Real-World Use: Basic Troubleshooting Tips
Here are some common problems you might encounter and how to troubleshoot them using the wiring diagram:
- Compressor won't turn on:
- Check the power cord and outlet.
- Verify the circuit breaker hasn't tripped.
- Use a multimeter to check for voltage at the pressure switch. If there's no voltage, the problem is upstream.
- If there's voltage at the pressure switch, check if the switch is closing its contacts when the tank pressure is low. If not, the pressure switch may be faulty.
- Compressor runs but doesn't build pressure:
- This is often a mechanical issue, but check the wiring to the motor and the motor's capacitors. A failing capacitor can prevent the motor from running at full speed, reducing its pumping capacity.
- Listen for air leaks.
- Compressor runs continuously:
- The pressure switch may be stuck in the closed position. Replace the switch.
- There may be a leak in the system that is so large the compressor can't keep up.
Safety First!
Working with electricity is inherently dangerous. Always take the following precautions:
- Disconnect Power: Always disconnect the compressor from the power outlet before working on any electrical components.
- Verify Dead Circuits: Use a multimeter to verify that the circuit is de-energized before touching any wires or components.
- Grounding: Ensure that the compressor is properly grounded to prevent electric shock.
- Capacitors: Capacitors can store a dangerous electrical charge even after the power is disconnected. Discharge capacitors before handling them. Use a resistor to safely discharge capacitors. Never short them directly with a screwdriver, as this can cause a dangerous explosion.
- Qualified Personnel: If you are not comfortable working with electricity, consult a qualified electrician.
Warning: The capacitors and main power lines carry high voltage and current. They pose a significant electrical shock hazard!
Understanding your air compressor's wiring diagram empowers you to diagnose and fix problems safely and effectively. It is crucial for ensuring safe and efficient compressor operation. To enhance your troubleshooting efforts, we have a comprehensive wiring diagram file ready for you to download. This diagram includes detailed schematics and component layouts tailored for common air compressor models, providing a visual reference to complement the knowledge you've gained in this article.