Automotive Wiring Harness Connectors
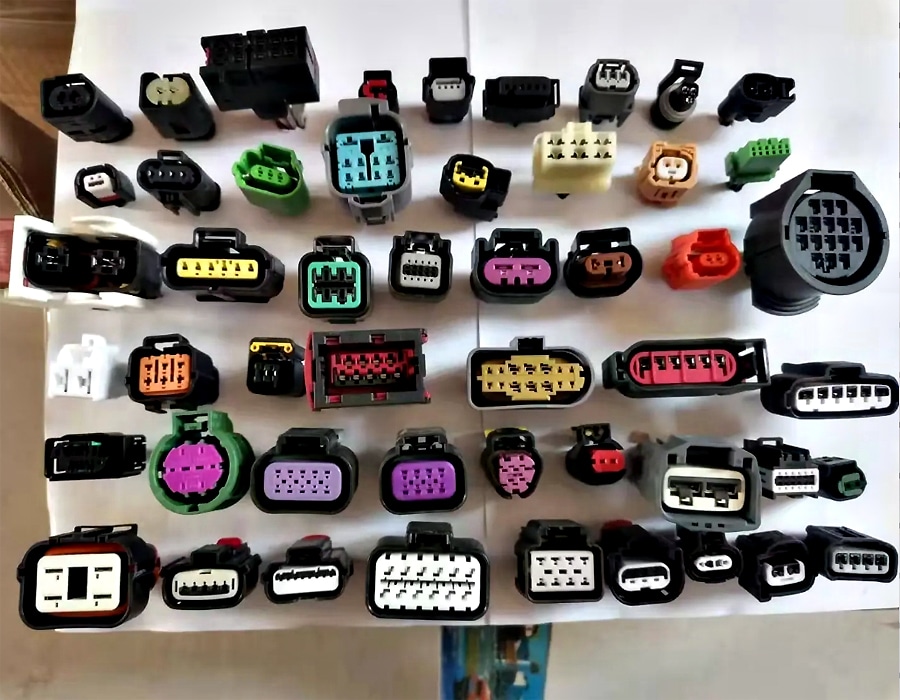
Alright, let's dive into the world of automotive wiring harness connectors. These unassuming plastic bits are absolutely crucial for the proper function of your vehicle. Understanding them is essential for anything from basic repairs to complex modifications. We're going to break down everything you need to know, from the types of connectors to how to troubleshoot them, all in a way that's practical and easy to understand.
Purpose and Importance
Think of your car's electrical system like a nervous system, and the wiring harness connectors as the synapses – the critical junctions where signals (electricity) are passed between components. Without these connectors, nothing works. The wiring harness is a bundle of wires organized and secured together, and the connectors provide a standardized and reliable way to plug these wires into various components like sensors, actuators, lights, and modules. This approach greatly simplifies manufacturing and makes repair easier. If a sensor needs replacing, you don't have to cut and splice wires – you just unplug the connector and plug in a new one.
Why does understanding this matter to you? Here's a few scenarios:
- Repairs: You can diagnose and fix electrical problems more effectively. A loose or corroded connector can cause all sorts of issues, from intermittent problems to complete failures.
- Modifications: Adding aftermarket accessories (lights, audio systems, etc.) often involves tapping into the existing wiring harness. Understanding connectors allows you to do this safely and correctly.
- Diagnostics: Many diagnostic tools rely on reading signals from sensors and actuators. Knowing where these sensors are connected and how to access them is vital for accurate troubleshooting.
- Learning: Gaining a solid grasp of electrical principles empowers you to work on your car with confidence and save money on expensive repairs.
Key Specs and Main Parts of a Connector
Automotive connectors come in various shapes, sizes, and configurations, but they all share common features:
- Housing: The plastic body of the connector, providing insulation and mechanical protection. The housing often includes features like locking tabs, alignment keys, and seals.
- Terminals: The metal contacts inside the housing that make the electrical connection. Terminals are typically made of copper or brass and are plated with tin or gold to prevent corrosion.
- Seals: Connectors used in exposed locations often have rubber seals to prevent water and contaminants from entering the connection and causing corrosion.
- Locking Mechanisms: These mechanisms (clips, latches, or friction fits) ensure the connector remains securely attached, even in the presence of vibration and temperature changes. Common types include push-to-release, slide-to-release, and bayonet locks.
- Wire Seals (Grommets): These are small rubber or plastic seals that surround the wire as it enters the connector housing, providing an extra layer of protection against moisture and debris.
Key specifications to consider when dealing with connectors:
- Number of Pins (or Contacts): The number of individual connections within the connector.
- Wire Gauge (AWG): The size of the wire that the connector is designed to accommodate. Using the wrong gauge can lead to poor connections or damage to the connector.
- Current Rating (Amps): The maximum amount of current that the connector can safely handle.
- Voltage Rating (Volts): The maximum voltage that the connector can safely handle.
- Operating Temperature Range: The range of temperatures within which the connector will function reliably.
- IP Rating (Ingress Protection): A rating that indicates the connector's resistance to dust and water. Higher numbers indicate greater protection.
Symbols – Lines, Colors, and Icons
Understanding wiring diagrams is crucial for working with automotive connectors. Here's a breakdown of common symbols and conventions:
- Lines: Represent wires. The thickness of the line may indicate the wire gauge.
- Colors: Each wire is typically identified by a color code (e.g., Red, Blue, Green). Color codes help you trace wires through the harness. Standard abbreviations are used (e.g., RD for Red, BL for Blue, GN for Green). Sometimes you'll see a wire with a primary color and a stripe (e.g., Red/White).
- Connectors: Represented by squares, circles, or other shapes, often with pins numbered inside. The shape can sometimes indicate the type of connector.
- Ground Symbols: Indicate a connection to the vehicle's chassis ground. Common symbols include a series of horizontal lines or a downward-pointing arrow.
- Components: Each component (sensor, actuator, relay, etc.) is represented by a unique symbol. Refer to a legend specific to your vehicle's wiring diagram for details.
Wire color codes are especially important. They are almost universally standardized, though specific color usage can vary between manufacturers and even models. Knowing that "BK" typically means Black (ground) and "RD" means Red (power) will save you a lot of time.
How It Works: The Electrical Connection
The basic principle is simple: the connector mechanically and electrically joins two or more wires together. The terminals inside the connector provide a low-resistance path for current to flow. A good connection requires:
- Proper Contact: The terminals must make firm, reliable contact with the wires they are connected to. This is achieved through crimping or soldering the wire to the terminal.
- Cleanliness: Corrosion or dirt on the terminals can impede current flow.
- Secure Connection: The connector must be securely locked in place to prevent it from coming loose due to vibration or movement.
When a connector fails, it's often due to one or more of these factors. Corrosion is a common culprit, especially in exposed locations. Vibration can also cause terminals to loosen or break, leading to intermittent or complete failures.
Real-World Use: Basic Troubleshooting Tips
Here's a few practical troubleshooting tips when dealing with automotive wiring harness connectors:
- Visual Inspection: Look for signs of damage, corrosion, or loose connections. Check for cracked housings, bent terminals, or discolored wires.
- Connector Cleaning: Use a contact cleaner specifically designed for electronics to clean corroded terminals. Disconnect the battery first.
- Terminal Tension Test: Check the tension of the terminals to ensure they are making good contact. You can use a small pick or specialized terminal testing tools to gently probe the terminals. If they feel loose, they may need to be replaced.
- Continuity Testing: Use a multimeter to check for continuity between the terminals on each side of the connector. This will verify that the wires are properly connected and that there are no breaks in the circuit.
- Voltage Testing: Use a multimeter to check for voltage at the connector. This will verify that power is being supplied to the component.
Example Scenario: Your headlights aren't working. Start by checking the headlight connectors. Look for corrosion or loose connections. Use a multimeter to check for voltage at the connector when the headlights are switched on. If there's no voltage, trace the wiring back to the switch or fuse box, checking connectors along the way.
Safety – Highlight Risky Components
Working with automotive electrical systems can be dangerous. Always disconnect the battery before working on any electrical components. Pay special attention to these potentially risky areas:
- Airbag Connectors: These connectors are typically bright yellow and contain a high-voltage charge. Mishandling them can trigger the airbag deployment, causing serious injury. Never probe or tamper with airbag connectors unless you are specifically trained to do so and have followed the proper deactivation procedures.
- High-Voltage Systems (Hybrids and EVs): These vehicles have high-voltage batteries and electrical systems that can be lethal. Do not attempt to work on these systems unless you are specifically trained and certified.
- Fuel Injection Connectors: While generally low voltage, tampering with these connectors while the engine is running can cause serious engine damage or even a fire.
Remember, when in doubt, consult a qualified mechanic!
Understanding automotive wiring harness connectors is a valuable skill for any DIYer. By understanding their purpose, construction, and how to troubleshoot them, you can tackle a wide range of electrical repairs and modifications with confidence. Electrical problems can seem intimidating, but with a methodical approach and the right tools, you can often diagnose and fix them yourself.
To help you even further, we've prepared a detailed wiring diagram reference guide. Contact us if you'd like to download it for free!