Automotive Wiring Harness Connectors And Terminals
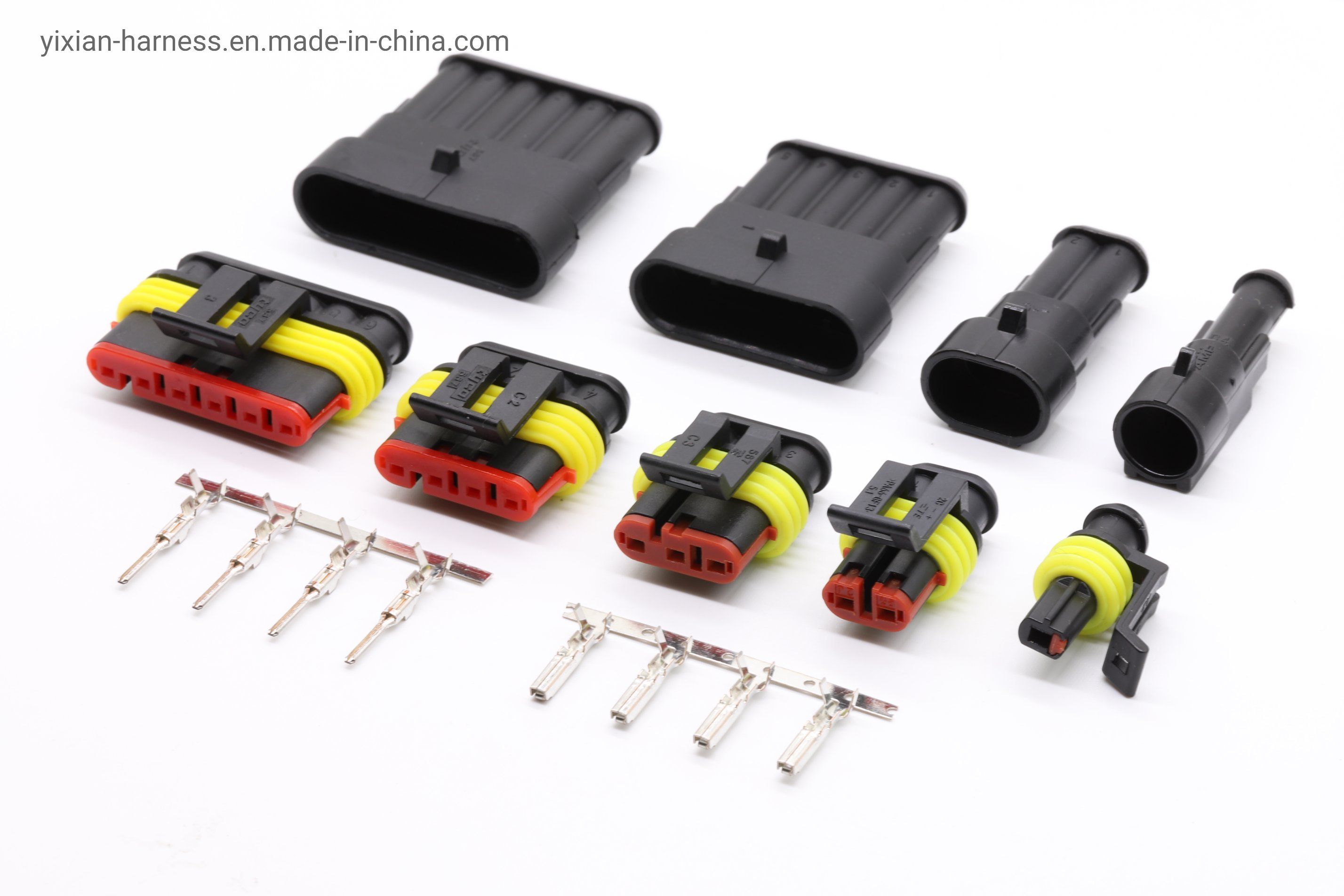
Alright folks, let's dive into the world of automotive wiring harness connectors and terminals. Understanding these components is crucial for anyone who works on cars, whether you're tackling simple repairs, adding aftermarket accessories, or even performing more complex modifications. This article will give you a solid grounding in the anatomy of these vital parts, helping you troubleshoot electrical issues with confidence.
Why This Knowledge Matters
Why bother learning about wiring harness connectors and terminals? Simply put, they're the foundation of your car's electrical system. Without them, electricity wouldn't flow, and nothing would work. Understanding these components is essential for:
- Repairing Faulty Connections: Corrosion, loose connections, and broken wires are common issues. Knowing how to identify and fix these problems can save you a trip to the mechanic.
- Adding Aftermarket Accessories: Installing new stereos, lights, or other electrical devices often requires tapping into existing wiring. Understanding connectors allows you to do this safely and effectively.
- Troubleshooting Electrical Problems: A faulty connector can cause a wide range of symptoms, from a flickering headlight to a completely dead engine. Knowing how to diagnose connector issues is key to pinpointing the problem.
- Customizing Your Vehicle: If you're involved in custom builds or restorations, you'll need to understand how to create and modify wiring harnesses.
Key Specs and Main Parts
Let's break down the key components of automotive wiring harness connectors and terminals:
Connectors
Connectors are the housings that hold the terminals and provide a secure, weatherproof connection between two or more wires or components. They come in a huge variety of shapes, sizes, and pin counts. Here's a breakdown:
- Housing: The plastic or metal body that holds the terminals. It's often designed with locking mechanisms to prevent accidental disconnection.
- Seals: Rubber or silicone gaskets that protect the terminals from moisture and corrosion.
- Locking Mechanisms: These can be levers, clips, or other devices that secure the connector halves together. Properly engaging the locking mechanism ensures a reliable connection.
Terminals
Terminals are the metal contacts that make the electrical connection between wires. They're crimped or soldered onto the ends of wires and then inserted into the connector housing.
- Crimp Terminals: The most common type. They're attached to wires using a crimping tool, which mechanically deforms the terminal to create a secure connection.
- Solder Terminals: Less common in modern cars but still used in some applications. They're attached to wires using solder, creating a permanent connection.
- Blade Terminals: Flat, rectangular terminals that mate with corresponding female terminals.
- Pin Terminals: Cylindrical terminals that mate with corresponding female terminals.
- Socket Terminals: Female counterparts to blade or pin terminals, designed to receive the male terminal.
Wire Gauges and Colors
Wires come in different gauges (thicknesses) depending on the amount of current they need to carry. Wire gauge is typically expressed in AWG (American Wire Gauge). Smaller numbers indicate thicker wires. Also, wires are color-coded to help identify their function. While color codes can vary between manufacturers, there are some common conventions.
How It Works
The basic principle is simple: connectors and terminals provide a reliable and organized way to connect wires and electrical components. Here's the process:
- A wire is stripped to expose the bare conductor.
- A terminal is crimped or soldered onto the end of the wire. Using the correct crimping tool and technique is crucial for a reliable connection. A poor crimp can lead to resistance, heat buildup, and ultimately, failure.
- The terminated wire is inserted into the appropriate cavity in the connector housing.
- The connector halves are joined together, and the locking mechanism is engaged. This ensures that the terminals make solid contact and that the connection is protected from the environment.
Real-World Use – Basic Troubleshooting Tips
When troubleshooting electrical problems, always check the connectors first. Here are some common issues and how to address them:
- Corrosion: Look for green or white deposits on the terminals. Clean them with a wire brush or electrical contact cleaner. In severe cases, you may need to replace the terminal or connector.
- Loose Connections: Check that the connector is fully seated and that the locking mechanism is engaged. If the terminals are loose, you may need to re-crimp them or replace the connector.
- Broken Wires: Inspect the wires near the connector for breaks or damage. Repair or replace the damaged wire. Sometimes, the wire will break *inside* the insulation near the terminal. Give the wire a gentle tug to check for this.
- Terminal Backout: A terminal can sometimes become dislodged from its cavity in the connector housing. This prevents proper contact. Use a terminal release tool (or a small pick) to reseat the terminal.
Testing for Continuity: Use a multimeter to check for continuity (a complete electrical path) through the connector. Disconnect the connector and place the multimeter probes on either side. A reading of zero ohms (or close to it) indicates continuity.
Safety – Highlight Risky Components
Working with automotive electrical systems can be dangerous. Here are some important safety precautions:
- Disconnect the Battery: Always disconnect the negative battery cable before working on any electrical components. This will prevent accidental shorts and shocks.
- Use the Right Tools: Use appropriate crimping tools, wire strippers, and multimeters. Using the wrong tools can damage the wiring or create unsafe conditions.
- Be Aware of Airbags: Airbag systems contain high-voltage capacitors that can store energy even after the battery is disconnected. Consult your vehicle's service manual for instructions on how to safely disable the airbag system before working near it. Generally, it is best practice to avoid directly working on or around airbag connectors unless absolutely necessary.
- Handle Connectors Carefully: Avoid pulling on wires to disconnect connectors. Use the proper release mechanisms to avoid damaging the connector or wires.
High-Current Circuits: Be especially careful when working with high-current circuits, such as those for the starter motor, alternator, and headlights. These circuits can carry a significant amount of current, which can cause burns or even death. Make sure to properly size your wiring and connectors for the intended current load. Always double-check your work before reconnecting the battery.
Diagram Availability
To further assist you in your automotive wiring endeavors, we have a detailed diagram available for download. This diagram provides a visual representation of common connector types, terminal styles, and wiring configurations. This is a valuable resource for identifying components and understanding how they fit together. Download this diagram to have a handy reference guide whenever you're working on your car's electrical system.
Armed with this knowledge and the downloadable diagram, you'll be well-equipped to tackle a wide range of automotive wiring projects. Remember to always prioritize safety and take your time to ensure that your connections are secure and reliable. Happy wrenching!